1. Caraterísticas do material de silicone
A. As matérias-primas de silicone são geralmente gelatinosas, algo semelhantes à plasticina, incolores, translúcidas e inodoras.
B. As suas principais caraterísticas são a resistência a altas temperaturas (até 300°C) e a resistência a baixas temperaturas (mínimo -100°C), que é atualmente a melhor borracha resistente ao frio e a altas temperaturas; ao mesmo tempo, possui um excelente isolamento elétrico e uma elevada estabilidade à oxidação térmica e ao ozono, quimicamente inerte.
A desvantagem é que a resistência mecânica é baixa, a resistência ao óleo, a resistência ao solvente e a resistência a ácidos e álcalis são fracas, é difícil de vulcanizar e o preço é mais caro. Temperatura de operação: -60 ℃ ~ + 200 ℃. O acima é a descrição de borracha de silicone no manual.
C. Temperatura de utilização: Como mencionado acima, é geralmente definida para -40°C a 200°C, e pode atingir 230°C num curto espaço de tempo.
D. Problema de envelhecimento: a resistência ao óleo, aos ácidos e aos álcalis é fraca, e tem pouco a ver com o stress.
E. Problema de aderência: Antes do tratamento de superfície, para além de utilizar produtos de silicone como adesivos para ligação a peças de silicone, a adesão a outras peças deve ser activada à superfície e a superfície da cola pode ser curada por vulcanização.
Todas as substâncias que podem reagir com a borracha ou provocar a sua reticulação são coletivamente designadas por agentes de vulcanização, também conhecidos como agentes de reticulação. Existem muitos tipos de agentes de vulcanização, e estes continuam a aumentar.
Os agentes de vulcanização que têm sido utilizados incluem enxofre, selénio, telúrio, compostos contendo enxofre, óxidos metálicos, peróxidos, resinas, quinonas e aminas.
F. Dureza do material: De acordo com a dureza Shore, as peças de plástico podem, teoricamente, ser selecionadas entre 10 graus e 80 graus no mercado nacional.
Os que podem ser facilmente encontrados são geralmente de 20 a 70 graus, e os mais utilizados são de 40 a 50 graus.
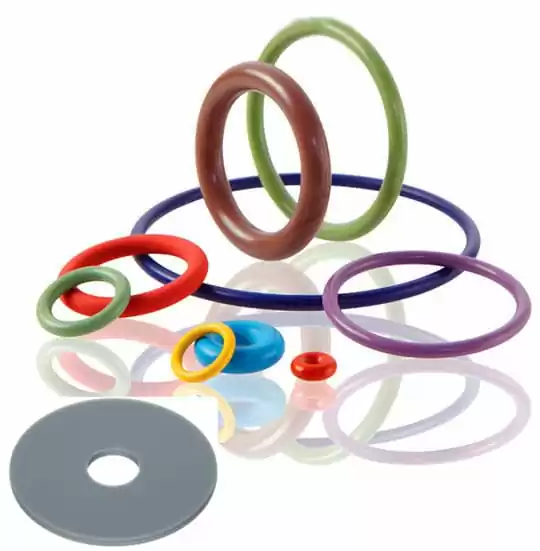
2. O processo de produção de produtos de silicone
A: Forma e cor das matérias-primas
B: Após a combinação de cores e a amassadura, os flocos de várias cores são transformados em gel de sílica branco leitoso
C: Depois de amassadas e moldadas, as matérias-primas são prensadas em tiras e cortadas em tiras
D: Moldagem por vulcanização
E: Corte, remoção de arestas, inspeção, embalagem
F: Concluído produtos de silicone
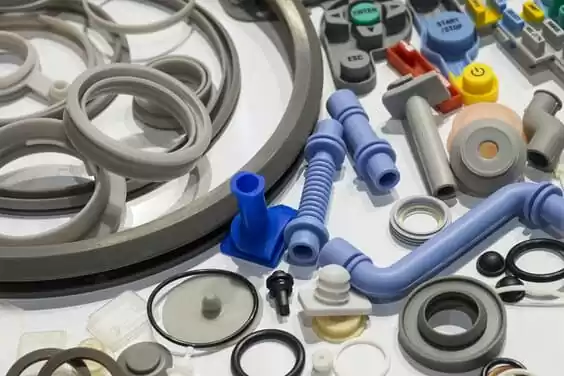
3. Dimensão e caraterísticas do produto
A. Limite de tamanho: A parte mais grossa pode ser de 15~20MM, se for uma esfera, o diâmetro pode ser de 30MM. Geralmente, a espessura recomendada não é superior a 3MM.
Se for superior a 3MM, demorará mais tempo a vulcanizar e aumentará o custo. A parte mais fina pode teoricamente atingir os 0,2MM, mas os 0,3MM mais finos são geralmente utilizados no projeto e recomenda-se 0,4MM.
B. Tamanho relativo: Em termos de diferença de espessura, recomenda-se que a parte mais fina e a parte mais grossa não excedam 3 vezes. Tais problemas dependem principalmente dos requisitos de temperatura e pressão quando o material é vulcanizado.
C. Taxa de contração: A taxa de contração do material de silicone está relacionado com a dureza do material. A maioria dos materiais secundários fornecidos pelo fabricante situa-se entre 1,022 e 1,042.
Para materiais com um grau de 40 a 50 graus, a taxa de retração é geralmente de 1,03. Em comparação com o plástico, os produtos de silicone não sofrem de defeitos de superfície aparentes semelhantes devido à contração.
D. Precisão dimensional: Porque a maioria dos produtos de borracha de silicone são um molde com múltiplas cavidades, o número de cavidades é muito grande em comparação com os produtos de plástico. Por conseguinte, o controlo do tamanho dos produtos de plástico não é tão prático como o dos produtos de plástico.
A precisão geral é de mais ou menos 0,1, e o produto de alta precisão é de mais ou menos 0,05. Quando é utilizado para fazer corresponder o orifício da peça de plástico e o botão, a folga mínima é de 0,1 por lado e o valor recomendado é de 0,2 por lado.
E. Desenho da forma: Para peças de manga de borracha, geralmente é suficiente fornecer o desenho original à fábrica de moldes de acordo com o desenho da forma do produto e explicar o problema de correspondência, que é decidido pela fábrica de moldes.
Em circunstâncias normais, dependendo do tamanho do produto, a coordenação entre a manga de borracha e o produto é geralmente um desvio negativo de 0,2~0,5 pequeno de um lado.
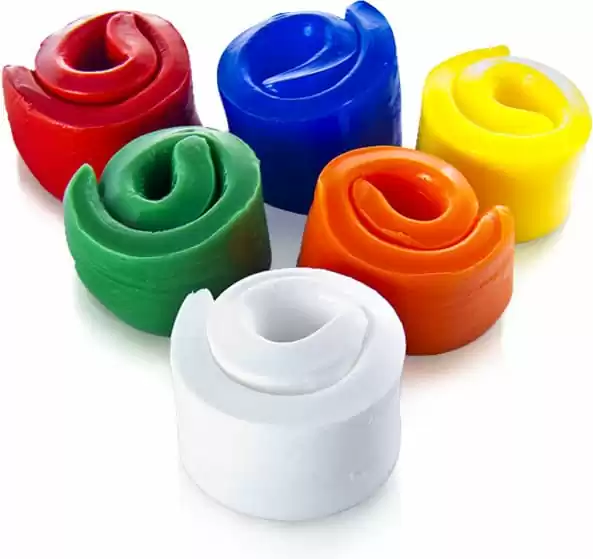
4. Estrutura do molde
A. Limite superior da espessura do molde:
Tentativamente 250mm, o tamanho pode chegar a 500X500, e o produto pode ser de até 400X400 na área do molde. A estrutura do molde é geralmente dividida em molde superior, molde inferior, placa inferior, placa superior, pino ejetor, núcleo do molde, dobradiça e outras peças auxiliares. Ao projetar produtos de siliconeA Comissão deve prestar atenção às caraterísticas dos seus moldes e processos de produção:
B. Desmoldagem:
A libertação dos produtos de silicone pode ser feita de forma direta e forçada. Para produtos sem defeitos de conceção, o requisito de tamanho para a libertação forçada reside principalmente na relação entre a circunferência da maior parte do núcleo do molde e a menor parte de fecho durante a desmoldagem. Para produtos abaixo de 55°, pode ser feito 2-3 vezes. Pode haver fendas e cantos afiados na abertura.
Uma vez que é necessária uma temperatura de 180 graus Celsius durante a vulcanização, o trabalho de desmoldagem é quase todo manual, exceto a separação superior e inferior do próprio molde. Por isso, a conveniência e a rapidez da remoção devem ser consideradas no projeto das peças.
Para não afetar a qualidade da vulcanização e a eficiência da produção em massa das peças devido ao longo tempo de desmoldagem. Uma vez que o método de libertação do silicone é principalmente manual e o curso de ação da placa superior também é pequeno, o molde de silicone não tem uma parte superior inclinada em comparação com o molde de silicone de molde de plástico. Geralmente, não é fornecida nenhuma tração ao núcleo.
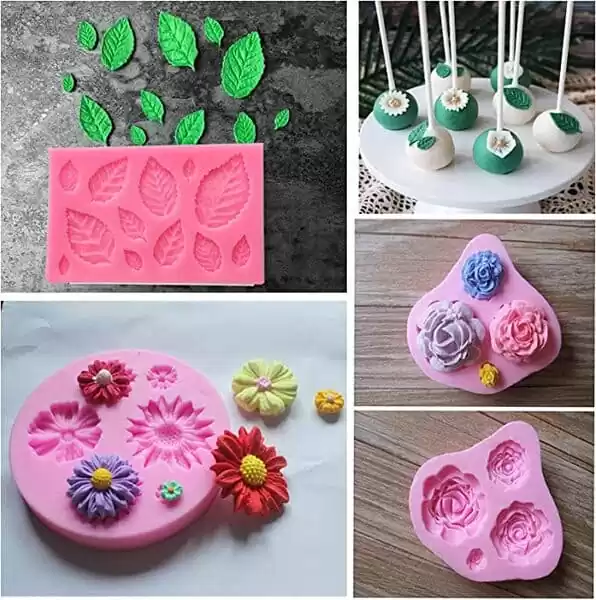
C. Fixação do núcleo:
Ao contrário dos moldes de plástico, os núcleos dos moldes de silicone são geralmente removidos juntamente com as peças do produto quando o molde de injeção é aberto e as peças são retiradas. Por isso, a fixação e o posicionamento exato do núcleo do molde são mais difíceis de manusear do que o molde de plástico, e a rigidez do núcleo do molde é maior.
Os núcleos são geralmente feitos em conjunto e todos os núcleos são fixados de uma só vez. Ou passar o núcleo do molde através de ferramentas auxiliares para permitir o seu posicionamento rápido. Uma vez que existe muita pressão no processo de fixação do molde, é necessário evitar rigorosamente que o núcleo do molde se mova.
D. Puxar pelo núcleo:
Geralmente, não pode ser movido automaticamente, mas pode ser forçado a sair, e a extração do núcleo só é utilizada para estruturas de pequena dimensão. A configuração de tração do núcleo é semelhante à do molde de plásticomas é retirada manualmente quando o molde é aberto.
Além disso, a extração do núcleo ocupa um grande espaço no molde, o que não só é complicado de processar no excesso molde de silicone num molde, mas também tem uma baixa utilização do espaço do molde. Por isso, não puxe o núcleo tanto quanto possível.
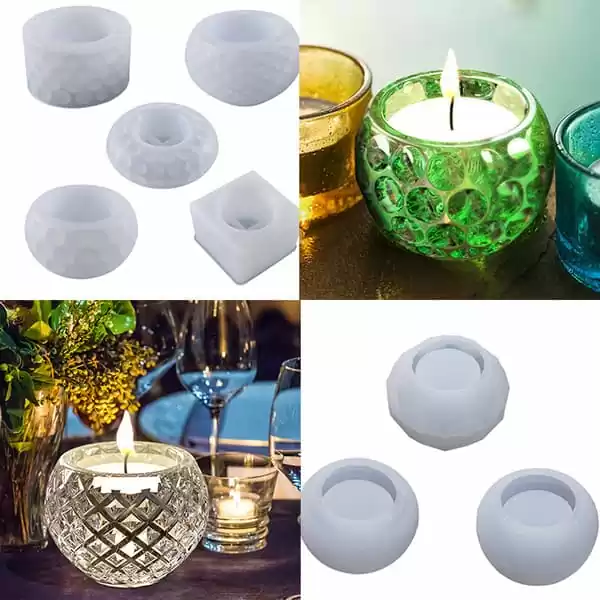
E. Forma:
Os produtos de silicone têm uma grande resistência quando a superfície está intacta, mas quando há fissuras, estas expandem-se rapidamente sob a ação de forças externas. Assim sendo, produtos de silicone são muito sensíveis às fissuras.
Tendo em conta estes problemas, deve prestar-se atenção à conceção correta do molde das peças de silicone: não deve haver cantos afiados em todas as posições, para evitar a concentração de tensões e fissuras. O ângulo R na abertura não deve ser inferior a 0,5.
F. Aresta de auto-remoção:
A principal função da borda auto-retirável: é acomodar o excesso de borracha; facilitar a exaustão do molde; fácil de aparar o flash.
A aresta de auto-remoção é geralmente composta por uma aresta fina na superfície de separação da peça e uma aresta de rasgo relativamente forte correspondente. A espessura da borda fina é geralmente 0,1 ~ 0,2, a espessura da borda de rasgo é geralmente 0,8, e a largura é geralmente 1 ~ 2MM.
G. Inserir:
Podem ser colocados vários tipos de inserções em produtos de silicone, mas é necessário prestar atenção a várias questões Em primeiro lugar, a superfície das peças embutidas deve ser pré-tratada, principalmente a vulcanização da superfície ou a ativação da superfície.
Caso contrário, será difícil ligar firmemente o inserto e a cola. O segundo é o posicionamento fixo do inserto, que pode ser fixado numa direção na direção vertical, mas deve ser totalmente fixado noutras direcções. Para evitar o movimento do inserto durante todo o processo do molde.
A terceira é a espessura da cola à volta da inserção. Para peças totalmente encapsuladas (em que todas as superfícies estão encapsuladas, pelo que a pastilha não pode ser posicionada), deve ser utilizada uma espessura mínima de 0,5 mm à volta da pastilha. Para inserções com posicionamento, a espessura da camada adesiva periférica deve ser superior a 0,4MM.
H. Outros processos auxiliares:
Processo de injeção de cola (colagem):
Semelhante ao moldagem por injeção No processo de injeção, as peças a serem injectadas são fixadas primeiro e a primeira camada do molde é fechada para controlar que as matérias-primas não contaminem as peças que não foram concebidas para injeção durante a injeção. Em seguida, a segunda camada do molde é fechada e o composto de borracha é prensado para ganhar forma.
Processo de laminagem: primeira mão-preformar a borracha
Moldagem: Este processo de fabrico pode ser utilizado no caso de encapsulamento total.
Mergulhar: A matéria-prima do corpo de borracha (borracha) é fluida, e a peça de trabalho é mergulhada na matéria-prima várias vezes. A camada interior da matéria-prima é vulcanizada e depois mergulhada novamente até se atingir a espessura pretendida.
Epóxi: A matéria-prima tem boa fluidez, semelhante à tinta, e é vulcanizada à temperatura ambiente. O molde é uma operação relativamente simples, geralmente manual, e o revestimento seguinte é aplicado quando a primeira camada é rapidamente curada.
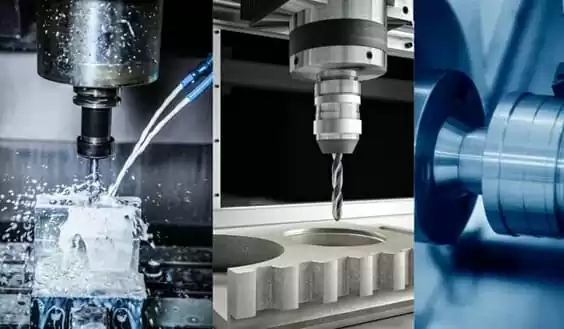
L. Produtos multicoloridos:
A é dividido em 2 conjuntos de moldes de vulcanização, e B é colorido à mão, uma vez vulcanizado, a parte de separação de cores das peças é necessária para ter uma certa altura, para evitar a combinação de adesivo condutor de mistura de cores, silicone de vulcanização secundária e silicone (borracha) pode ser diretamente vulcanizado sem tratamento Ligação 5. Medição da dureza e ferramentas.
O instrumento mais utilizado para medir a dureza da borracha é o chamado durómetro Shore (também conhecido como Shore). Utiliza uma mola para pressionar um indentador metálico na superfície do material e mede a profundidade da sua penetração.
O instrumento mede as profundidades de penetração de zero a 0,100 polegadas. Uma leitura de zero na escala significa que o indentador penetrou na profundidade limite, enquanto uma leitura de 100 significa que a profundidade de penetração é zero. Existem vários aparelhos de teste de dureza shore com diferentes gamas de dureza e graus de automatização.
Uma das escalas mais utilizadas é a escala Shore A. Os durómetros Shore A têm um indentador rombo e uma mola média. Quando as leituras são superiores a 90, o durómetro Shore A torna-se impreciso. Para estes materiais mais duros, é utilizado um durómetro Shore D. Tem um indentador afiado e uma mola forte para uma penetração profunda.
Para medir plásticos mais duros, utilize um durómetro com um indentador mais afiado e mais resistente, como um durómetro Rockwell. No extremo oposto, os durómetros Shore 00 são utilizados para medir géis macios e borrachas de espuma.

A maioria dos materiais múltiplos pode suportar a tensão inicial, mas com o tempo cederá devido à fluência e relaxamento. As leituras do durómetro podem ser efectuadas instantaneamente ou após um determinado tempo de atraso, normalmente 5 a 10 segundos. As leituras imediatas mostrarão sempre leituras mais elevadas (ou mais duras) do que as leituras atrasadas.
As leituras de atraso são mais representativas não só da dureza do material, mas também da sua elasticidade. Um material mais fraco e menos elástico é mais propenso à fluência do que aqueles que são mais fortes e mais elásticos.
Para garantir a validade dos dados, são necessários procedimentos de teste precisos. Para obter uma leitura precisa, é necessário ter uma peça de teste que seja plana e suficientemente espessa para que o indentador não seja afetado pela superfície de suporte.
Normalmente, a espessura necessária é de 0,200 polegadas, mas os materiais rígidos com menos deformação podem ser testados com precisão quando estão presentes espessuras mais finas.