EPDM (каучук EPDM), как синтетический каучук, обладающий хорошей эластичностью, износостойкостью, теплостойкостью, атмосферостойкостью, озоностойкостью, стойкостью к пресной и морской воде, широко используется в производстве автомобильных резиновых изделий, таких как уплотнители дверей и окон, шланги и уплотнения гидравлических тормозов, вентиляционные каналы кондиционеров, уплотнения в системах охлаждения двигателя и холодильных системах кондиционеров, шланги для транспортировки охлаждающей жидкости и т.д.
EPDM резина представляет собой неполярную, насыщенную структуру. Так называемые "неполярные", то есть входящие в состав полимера молекулы не содержат внутри полярных групп.
Так называемые "насыщенные", то есть входящие в состав полимера, не содержат двойных связей внутри молекулы. В целом, каучуки и термоэластопласты можно разделить на "полярные" и "неполярные", а также "насыщенные" и "ненасыщенные" по нескольким структурам.
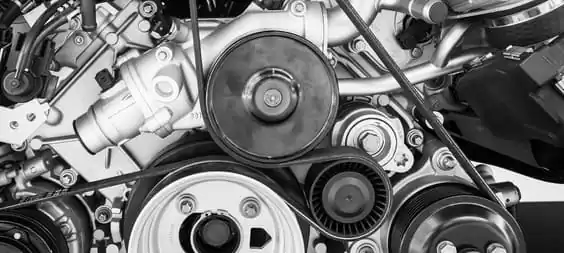
Материалы, молекулы которых сами содержат полярные группы, обычно являются "полярными" материалами. Полярная" структура определяет устойчивость полимеров к растворителям, как правило, по принципу сходной растворимости, то есть полярные растворители растворяют или набухают полярные полимеры, и наоборот.
С "насыщенной" структурой связана устойчивость полимеров к атмосферному старению (окислению). Если молекула полимера содержит двойную связь, то двойная связь легко окисляется, поэтому полимер нестабилен и легко разрушается.
Так же как и "неполярный" EPDM, устойчив к полярным средам, таким как горячая вода и пар, моющие средства, органические и неорганические кислоты, полярные растворители (такие как этанол, ацетон, эфиры и т.д.), тормозная жидкость на основе гликоля и т.д.
И не устойчив к неполярным средам, таким как минеральное масло, бензин, животные и растительные жиры и масла, силиконовое масло и т.д., и широко используется в системах тормозной жидкости на основе гликоля (SL-DOT4), системах охлаждения двигателя, содержащих антифриз; как "насыщенный" EPDM, с отличной устойчивостью к озону и выветриванию, широко используется в производстве воздуха, воды и т.д.
Температура использования EPDM в автомобильной промышленности обычно составляет от -40 ℃ до 120 ℃. Ниже приводится конкретное введение в использование Изделия из EPDM в автомобилях, соответствующие требования к характеристикам материалов и анализ распространенных ситуаций отказа.
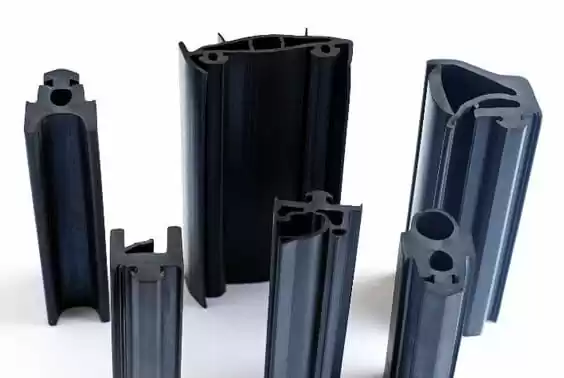
Применение в автомобильных уплотнительных изделиях
Подавляющее большинство автомобильных уплотнений производится на экструзионном оборудовании с постоянным сечением и бесконечной длиной (при использовании перехвата в соответствии с требуемой длиной), в то время как небольшое количество нестандартных изделий производится на вулканизационных фильерах.
Процесс производства экструдированных изделий выглядит следующим образом: ингредиенты → смешивание резины → множество материалов (могут быть: твердая резина, мягкая резина, губчатая резина, цветная резина, металлический каркас, армирующая проволока и т.д.).
Экструзия компаундов → вулканизация нагревом (может быть: вулканизация горячим воздухом, вулканизация в резервуаре, микроволновая вулканизация, вулканизация в кипящем слое стеклянных шариков, вулканизация в соляной ванне и т.д.) → последующая обработка (резка, вулканизация шва, электростатическое флокирование, покрытие поверхности наливом, склеивание и т.д.).
Он широко используется в передних и задних лобовых стеклах, дверях, окнах, моторном отсеке, багажнике и других частях автомобиля, используется для заполнения зазора между частями кузова, с амортизацией, водонепроницаемостью, пылезащитой, звукоизоляцией, украшением, защитой водителя и пассажиров и другими функциями.
Такие изделия из силиконовой резины В основном в контакте с солнечным светом, водой и озоном, использование температур в -40 ℃ ~ 100 ℃, кратковременная жаропрочная температура может достигать 125 ℃.
EPDM материал, используемый для резиновых уплотнительных лент общей твердостью (Shore A) в 40 ~ 90 между выбором; его прочность на разрыв должна быть более 7MPa; удлинение при разрыве обычно в 150% ~ 500%; деформация сжатия (85 ℃, 22h) должна быть меньше, чем 45%.
Прочность на разрыв должна быть более 5N / м; озон старения (50pphm, растяжение 20%, 72h) не должно быть трещин; ксеноновая лампа Старение (с использованием ксеноновой лампы 1200 оборудования, относительная влажность 80% ~ 95%, температура черной пластины 55 ℃ ~ 60 ℃, 1000h) его прочность на разрыв и удлинение спада не может превышать 15%.
Температура стеклования (TR) не более -50 ℃; испытание на термическое старение (100 ℃, 70 ч), изменение твердости должно быть ± 5, изменение прочности на разрыв должно быть ± 15%, а удлинение падения не должно превышать 30%.
В целом, срок службы автомобильных уплотнений, изготовленных из EPDM резина может достигать более десяти лет. Однако в процессе производства и применения мы сталкиваемся с растрескиванием поверхности, потерей герметичности, образованием инея на поверхности и другими явлениями разрушения дверных и оконных уплотнителей после одного года установки.
Поверхностное растрескивание при тестировании продукта, его тест на озоностойкость через 20 часов, что трескается, не соответствует требованиям стандарта. После расследования этой партии некачественных продуктов, ошибка в рецептуре (EPDM резина содержание меньше) вызвано; замерзанием (распусканием) поверхности резинового уплотнения.
Анализ причин:
(1) Неправильно разработанные составы. Сернистый желтый, ускоритель, активатор, антиоксидант и т.д. в составе ингредиентов, из-за насыщенного наводнения; неорганический наполнитель карбонат кальция стрессовое наводнение.
(2) Неправильная работа процесса смешивания, слишком короткое время, что приводит к неравномерному диспергированию наполнителя, локальному более чем насыщению. Изменив формулу, увеличив время смешивания, можно решить проблему наводнения.
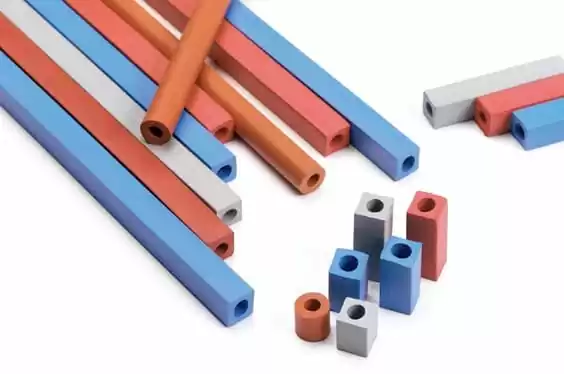
Применение EPDM в гидравлических тормозных шлангах и круглых уплотнениях
EPDM, устойчивый к тормозной жидкости (характеристики DOT3, DOT4, DOT5 (на основе силиконового масла), используется в производстве внутреннего резинового слоя гидравлических тормозных шлангов и уплотнений тормозных насосов.
Эти Изделия из EPDM находятся в контакте с основной средой тормозной жидкости, использование температур между -40 ℃ ~ 120 ℃, и краткосрочные термостойкие температуры до 135 ℃.
В таких деталях используется EPDM, твердость (по Шору А) составляет 80; прочность на разрыв должна быть более 10,5 МПа; удлинение при разрыве обычно выше 175%; при удлинении 50% фиксированное напряжение растяжения 2,5 ~ 4 МПа; при удлинении 100% фиксированное напряжение растяжения 8 МПа или более.
Деформация сжатия (100 ℃, 22 ч) должна быть меньше, чем 40%; температура стеклования (TR) максимум -50 ℃; озоновое старение (50pphm, 20% удлинение, 72 ч) не должно быть трещин; испытание тормозной жидкостью (положите образец в тормозной жидкости, 150 ℃, 70 ч) его изменение твердости должно быть 5.
Изменение прочности на разрыв должно быть ± 20%, изменение удлинения должно быть -15% ~ 20%, изменение объема должно быть в пределах ± 20%. 20%, изменение объема должно быть ± 5%; тепловой тест (125 ℃, 70h), изменение твердости должно быть ± 5, изменение прочности на растяжение должно быть ± 15%, и удлинение снижения не может превышать 15%.
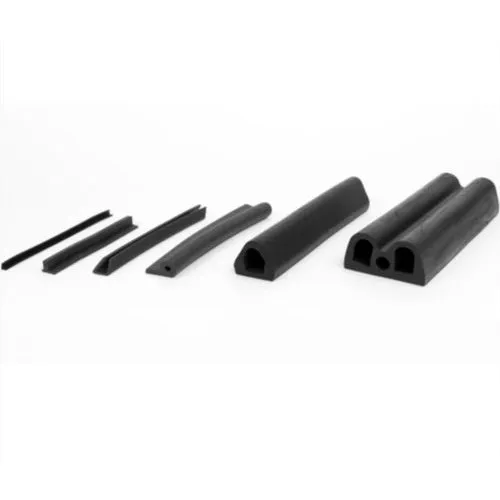
EPDM в шлангах для систем отопления, вентиляции и кондиционирования воздуха
Резиновый шланг обычно состоит из трех слоев: внутреннего, среднего армирующего слоя (ткань из химического волокна или стальная проволока) и внешнего слоя. Материалы, используемые для трех слоев, должны выбираться в соответствии с реальными требованиями.
Внутренний слой должен быть устойчив к коррозии подаваемой среды, а внешний слой должен обладать механической прочностью и быть адаптированным к внешней среде.
Поэтому внутренняя и внешняя резина часто не является резиной. EPDM широко используется в шлангах для отопления и вентиляции внутри и снаружи резинового слоя, а также в шлангах для кондиционеров во внешнем резиновом слое, поскольку этот материал обладает хорошей устойчивостью к воздуху, воде, озону, старению под воздействием солнечных лучей и гибкостью при низких температурах.
Для таких деталей используется EPDM, твердость (по Шору A) 70; прочность на разрыв должна быть более 10,5 МПа; удлинение при разрыве обычно более 300%; остаточная деформация при сжатии (100 ℃, 22 ч) должна быть менее 40%;
Его температура стеклования (TR) максимум -45 ℃; озон старения (50pphm, растяжение 20%, 72h) не должно быть трещин; IRM902 нефти тест (положить образец в IRM902 нефти, 100 ℃, 70h) его твердость снижение максимум 15, прочность на разрыв снижение максимум 30%.
Снижение прочности на разрыв не более 30%, изменение объема должно быть в пределах 80%; испытание на термическое старение (125 ℃, 70 ч), изменение твердости должно быть ± 5, изменение прочности на разрыв должно быть ± 15%, снижение удлинения не может превышать 40%.
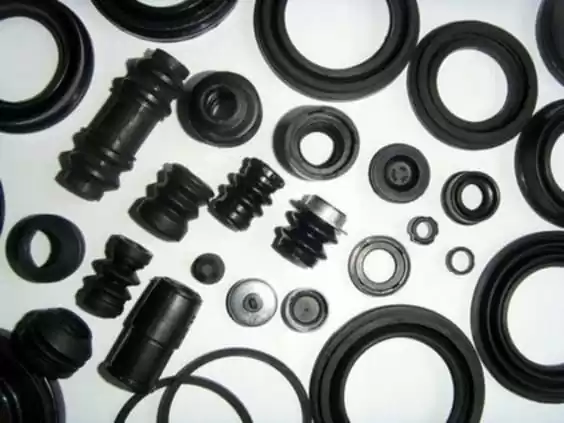
EPDM в применении для натяжения ленты
Этот вид детали, в основном используемый для соединения крышки колеса, крепления крышки аккумуляторного блока и т.д., может выдерживать высокую динамическую и механическую нагрузку, в процессе использования и всегда находится в напряженном состоянии.
Эти изделия из силиконовой резины В основном подвергаются воздействию солнечного света, воды и озона, использование температур в -40 ℃ ~ 85 ℃, кратковременная жаропрочная температура может достигать 100 ℃.
Материал EPDM, используемый для изготовления таких деталей, имеет твердость (по Шору A) обычно 60 ~ 80; его прочность на разрыв должна быть более 14MPa; удлинение при разрыве обычно составляет 200% ~ 400%; прочность на разрыв должна быть более 7N / m;
Остаточная деформация при сжатии (85 ℃, 22 ч) должна быть менее 45%; остаточная деформация при сжатии (-20 ℃, 22 ч) должна быть менее 45%; устойчивость к озоновому старению (50pphm, растяжение 20%, 72 ч) не должно быть трещин; Старение ксеноновой лампы (с использованием ксеноновой лампы 1200 оборудования, относительная влажность 80% ~ 95%, температура черной пластины 55 ℃ ~ 60 ℃, 1000ч) прочность на разрыв и удлинение спада не должны превышать 15%;
Температура стеклования (TR) не выше -50 ℃; испытание на тепловое старение (100℃, 70 часов), изменение твердости должно быть ±75, изменение прочности на разрыв должно быть ±15%, снижение удлинения не должно превышать 40%.
Разлом ремешка крышки аккумуляторного отсека и трещины на поверхности ремешка защитного кожуха колеса появились после полугода нагрузки. После неудачного испытания изделия на прочность на растяжение, разрыв и озоновое старение фактические результаты составили 8,5 МПа на растяжение, прочность на разрыв 5 Н/м и озоновое старение 42 часа, что не соответствует стандартным требованиям.
Отдельные производители тянущейся ленты о важности резиновой формулы не достаточно понимают, что пока EPDM каучук изготовлен из резиновой тянущейся ленты может быть, на самом деле, из-за различных формул, производительность продукта может сильно отличаться.
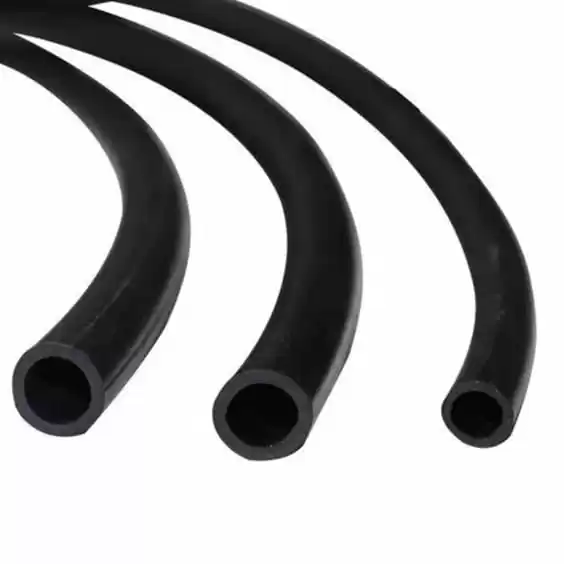
Применение EPDM в системе охлаждения двигателя и уплотнениях систем кондиционирования и охлаждения
EPDM используется для изготовления уплотнений в системах охлаждения двигателей. Эти продукты находятся в контакте со средой антифриз, солнечный свет, вода, озон, использование температуры в -40 ℃ ~ 125 ℃, и краткосрочные термостойкие температуры до 135 ℃.
Такие детали используют EPDM, твердость (Shore A) для 60 ~ 80 (75 для применения круглых уплотнений в холодильной системе); его прочность на разрыв должна быть более 10.5MPa; удлинение при разрыве, как правило, более 175%; в скорости удлинения 50% фиксированного напряжения расширения 1 ~ 2MPa; в скорости удлинения 100% фиксированного напряжения расширения 2 ~ 5MPa выше; деформация усадки (150 ℃, 22 ч) должна быть меньше, чем 20%;
Температура термостойкости до 135 ℃ (22 часа) должна быть ниже, чем у 20%; температура стеклования (TR) -50 ℃ максимум; устойчивость к озонному старению (50pphm, растяжение 20%, 72 часа) должна быть без трещин;
Для уплотнений, используемых в системах охлаждения двигателя, должно быть проведено испытание хладагентом (образец помещается в антифриз, 150°C, 166 ч, испытательное давление около 0,4 МПа), при этом изменение твердости должно составлять ±5, изменение прочности на растяжение - ±20%, изменение удлинения при разрыве -15% - 20%, а изменение объема - ±5%;
Для уплотнений, используемых в системах кондиционирования воздуха, тест хладагента должны быть выполнены (образец помещен в P тест (положить образец в PAG, ND8 хладагента, 100 ℃, 70h) изменение твердости до ± 5, изменение прочности на растяжение до ± 20%, удлинение при разрыве изменения до -15% ~ 20%, изменение объема должно быть в пределах ± 5%; тест на термическое старение (150 ℃, 70 часов), изменение твердости должно быть ± 5, падение прочности на разрыв должно быть менее 10%, падение удлинения не может превышать 10%.
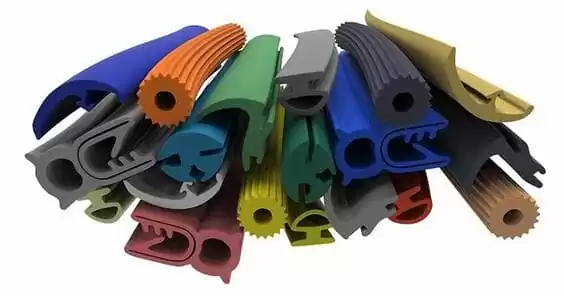
EPDM в применении шлангов для охлаждающей жидкости
EPDM используется для изготовления водяного шланга двигателя, его внутренний и внешний резиновые слои изготовлены из материала EPDM. Такие Изделия из EPDM В контакте со средой являются антифриз, солнечный свет, вода, озон, использование температуры в -40 ℃ ~ 125 ℃, краткосрочные жаропрочные температура может достигать 150 ℃.
Такие детали используются EPDM, твердость (по Шору A) для 65; его прочность на растяжение должна быть выше 10,5 МПа; удлинение при разрыве в более чем 300%; в скорости удлинения 50% фиксированного напряжения растяжения 1 ~ 2 МПа; скорость удлинения 100% фиксированного напряжения растяжения 2 ~ 4,5 МПа выше; сжатия остаточной деформации (100 ℃, 22 ч) должно быть меньше, чем 20%;
Его температура стеклования (TR) максимум -50 ℃; озон старения (50pphm, растяжение 20%, 72h) не должно быть трещин; охлаждающей жидкости тест (образец помещен в антифриз, 150 ℃, 166h, испытательное давление около 0,4MPa).
Изменение твердости должно быть ± 5, изменение прочности на растяжение должно быть ± 20%, изменение удлинения при разрыве должно быть -15% ~ 20%, изменение объема должно быть ± 5%. Испытание на тепловое старение (150 ℃, 70 ч), изменение твердости должно быть ± 5, прочность на разрыв должна быть менее 10%, а удлинение при разрыве не должно превышать 10%.