Структура литьевых форм для термореактивных жидких силиконовых резин (LSR) в целом похожа на структуру литьевых форм для термопластичных компаундов, но есть и несколько существенных отличий.
Например, компаунды LSR обычно имеют низкую вязкость и, следовательно, очень короткое время заполнения, даже при очень низком давлении впрыска. Чтобы избежать задержки воздуха, необходимо иметь в пресс-форме хорошее устройство для выпуска воздуха.
Кроме того, компаунды LSR не сжимаются в форме так сильно, как термопластичные компаунды; они имеют тенденцию расширяться в горячем состоянии и немного сжиматься в холодном. В результате изделие не всегда остается на выпуклой стороне формы, как ожидалось, а удерживается в полости с большей площадью поверхности.
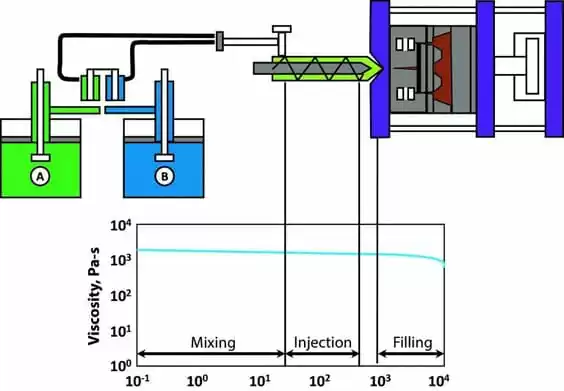
1. Усадка
Хотя LSR не дает усадки в форме, после распалубки и охлаждения они часто дают усадку от 2,5% до 3%. Точная величина усадки в определенной степени зависит от рецептуры компаунда.
Однако с точки зрения пресс-формы на усадку может влиять несколько факторов, включая температуру пресс-формы, температуру компаунда при его распаковке, а также давление в полости пресс-формы и последующее сжатие компаунда.
Также стоит обратить внимание на расположение точки впрыска, так как усадка в направлении потока клея обычно больше, чем усадка в направлении, перпендикулярном потоку клея.
Размер изделия также влияет на его усадку, причем толстые изделия обычно имеют меньшую усадку, чем тонкие. Если требуется вторичная вулканизация, усадка может составлять дополнительно 0,5%-0,7%.
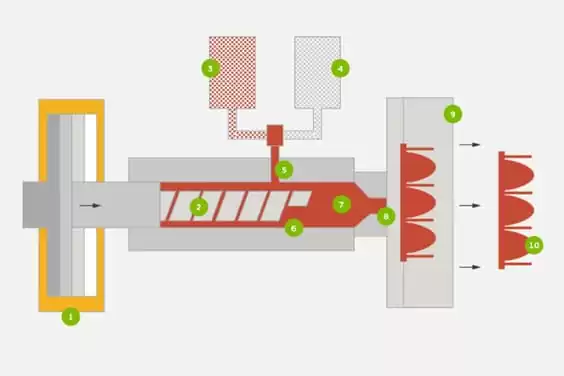
2. Линия разделения
Определение местоположения линии раздела - один из первых шагов при проектировании пресс-форма для литья под давлением силиконовой резины. Вентиляция достигается в основном с помощью канавок, расположенных на линии разделения, которая должна находиться в области, где инъекционный состав будет находиться дольше всего. Это помогает избежать образования внутренних пузырьков воздуха и снизить потерю прочности клеевого шва.
Из-за низкой вязкости LSR линия раздела должна быть точной, чтобы избежать пролива. Несмотря на это, линии разделения часто видны на фасонных изделиях. На выделение формы влияет геометрия детали и положение поверхности раздела. Проектирование детали с небольшой фаской поможет обеспечить постоянное сцепление с желаемой второй половинкой литьевая форма полость.
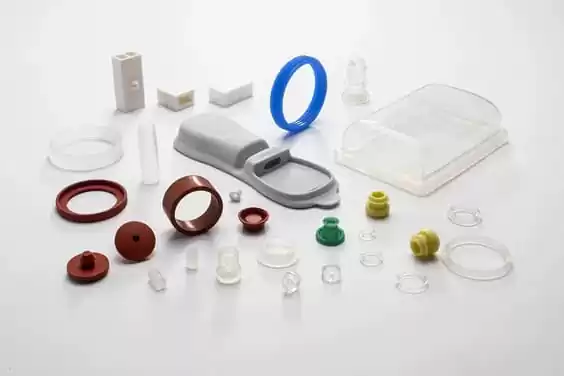
3. Вентиляция
При впрыскивании LSR воздух, находящийся в полости, сжимается при закрытии формы, а затем выводится через вентиляционные канавки при заполнении формы.
Если воздух выводится не полностью, он задерживается в клее (что часто приводит к тому, что на части изделия появляются белые края). Вентиляционные канавки обычно имеют ширину мм-3 мм и глубину 0,004 мм-0,005 мм.
Наилучший эффект вентиляции может быть достигнут путем вакуумирования внутри пресс-формы. Это достигается путем создания прокладки на линии разъема и быстрого удаления воздуха из всех полостей до вакуума с помощью вакуумного насоса. Как только вакуум достигнет номинального уровня, пресс-форма полностью закрывается и начинается прессование.
Некоторое оборудование для литья под давлением позволяет работать с переменным усилием смыкания, что позволяет переработчику закрывать пресс-форму при низком давлении до тех пор, пока 90-95% полости не будут заполнены ЛСР (что облегчает выход воздуха), а затем переключиться на более высокое усилие смыкания, чтобы избежать силиконовая резина расширение и переполнение.
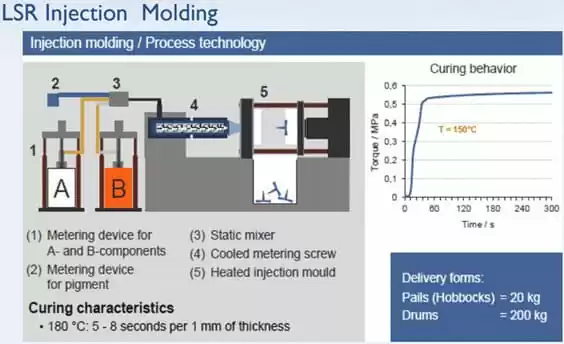
4. Место инъекции
При формовании LSR используется система холодной обкатки. Преимущества этой системы силиконовая резина и эффективность производства может быть увеличена до максимума.
При обработке изделий таким способом нет необходимости удалять канал впрыска, что позволяет избежать увеличения трудозатрат на выполнение операции, а иногда и большого количества отходов материала. Во многих случаях бесканальная конструкция также сокращает время работы.
Сопло для впрыска управляется игольчатым клапаном, обеспечивающим положительный поток, и многие производители теперь предлагают сопла с пневматическими переключателями в качестве стандартного оборудования, которые могут быть установлены в различных частях пресс-формы.
Некоторые литьевая форма Производители разработали открытую систему холодной обкатки, которая настолько мала, что несколько точек впрыска (а значит, и вся полость) должны быть установлены в очень ограниченном пространстве пресс-формы.
Эта технология позволяет производить большое количество высококачественных изделия из силиконовой резины без необходимости разделять порты впрыска.
Если используется система холодной обкатки, важно создать эффективное температурное разделение между горячей полостью и холодной обкаткой. Если бегунок слишком горячий, резина может начать вулканизироваться еще до впрыска. Если же она охлаждается слишком быстро, то поглощает слишком много тепла из области литника. литьевая формачто приводит к неполной вулканизации.
Для изделий, инжектируемых с помощью обычного литника (например, погружного литника и конического литника), целесообразно использовать инжекционный порт небольшого диаметра (обычно 0,2-0,5 мм).
При использовании низковязких LSR-компаундов, как и при использовании термопластичных компаундов, важно сбалансировать систему бегунков таким образом, чтобы все полости равномерно заполнялись компаундом. Программное обеспечение для моделирования системы бегунков может значительно упростить разработку формы и доказать ее эффективность с помощью испытаний на заполнение формы.
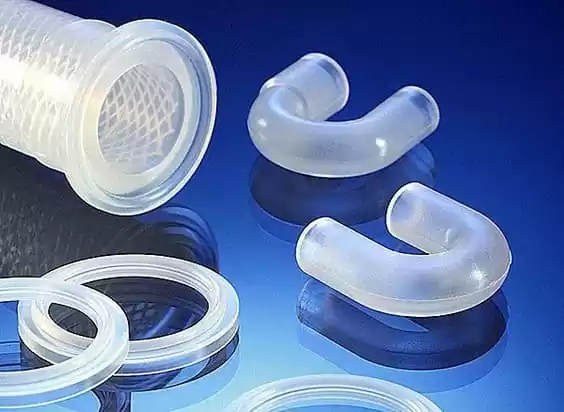
5. Распаковка
Жидкий силикон при вулканизации прилипает к поверхности металла, а гибкость изделия может затруднить его освобождение. Прочность LSR на разрыв при высоких температурах позволяет высвобождать его при нормальных условиях без повреждения даже крупных изделий.
К наиболее распространенным методам разделения относятся разделение пластин, разделение штифтов и пневматическое разделение. Другими распространенными методами являются шабрение роликами, выпуск экспортных пластин и автоматический выпуск пресс-форм.
При использовании системы выпуска важно соблюдать высокую степень точности. Если между верхним нажимным штифтом и втулкой направляющего штифта слишком большой зазор или если зазор между деталями становится большим из-за износа с течением времени, может произойти утечка клея.
Перевернутый конический или грибовидный верхний штифт очень эффективен, так как позволяет прикладывать большее контактное давление и способствует улучшению герметизации.
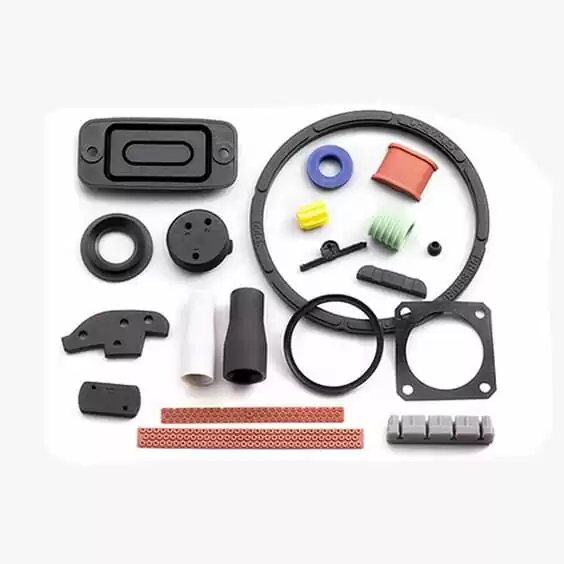
6. Материал пресс-формы
Поддоны пресс-форм часто изготавливаются из нелегированной инструментальной стали (№ 1.1730, код DIN C45W). Для поддонов пресс-форм, которые должны выдерживать высокую температуру 170℃-210℃, они должны быть изготовлены из предварительно закаленной стали (№ 1.2312, DIN код 40 CrMn-M oS 8 6) с учетом ударопрочности.
Для поддонов с полостями пресс-форм они должны быть изготовлены из азотированной или закаленной термообработанной этиловой инструментальной стали для обеспечения их высокотемпературной стойкости.
Для ЛСР с высокой наполняемостью, например, для маслостойких ЛСР, рекомендуется использовать более твердые материалы для изготовления пресс-форм, например, блестящую хромированную сталь или порошкообразный металл, специально разработанный для этих целей (№ 1.2379, DINcode X 155 CrVMo121).
При проектировании литьевые формы для материалов с высоким уровнем износа, те части, которые подвержены высокому трению, должны быть спроектированы таким образом, чтобы их можно было формировать сменным способом, чтобы не требовалась замена всей пресс-формы.
Внутренняя поверхность полости пресс-формы оказывает значительное влияние на отделку изделия. Наиболее очевидным является то, что формованное изделие будет идеально соответствовать поверхности полости. Формы для литья под давлением для прозрачных изделий должны быть изготовлены из полированной стали. Чина/никелевая сталь с поверхностной обработкой обладает высокой износостойкостью, а PTFE/никель облегчает освобождение формы.
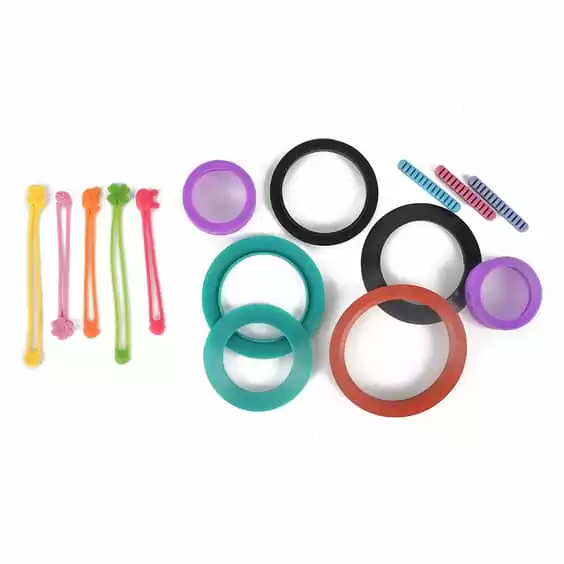
7. Контроль температуры
Вообще говоря, формование LSR предпочтительно осуществлять с помощью электрического нагрева, обычно с помощью ленточных нагревателей, патронных нагревателей или нагревательных пластин.
Главное, чтобы температурное поле было равномерно распределено по всей форме, что способствует равномерному отверждению LSR. На больших пресс-формах это экономически эффективный метод нагрева при контроле температуры масла.
Обертывание формы изоляционной пластиной помогает снизить потери тепла. Непригодность какой-либо части горячей пресс-формы может привести к большим колебаниям температуры между рабочими процессами или вызвать воздушные прогоны.
Если температура поверхности опускается слишком низко, скорость отверждения клея замедляется, что часто препятствует выходу продукта из литьевая форма и вызывает проблемы с качеством.
Между нагревателем и линией раздела должно быть выдержано определенное расстояние, чтобы предотвратить изгиб и деформацию шаблона и образование заусенцев от перелива клея на готовом изделии. Если пресс-форма спроектирована с системой холодного хода, горячий и холодный концы должны быть полностью отделены друг от друга.
Можно использовать специальные сплавы Чина (например, 3.7165 [TiA16V4]), поскольку их теплопроводность значительно ниже по сравнению с другими сталями. При использовании встроенной системы нагрева литьевой формы тепловой экран должен быть установлен между формой и поддоном формы, чтобы свести к минимуму потери тепла. Правильный дизайн и концепция могут обеспечить литье под давлением LSR, где пресс-форма очень важна.
Вышеуказанные принципы проектирования пресс-форм направлены на заполнение полости формы резиной, сокращение времени вулканизации, достижение превосходного качества и высокого выхода готовой продукции, что обеспечивает жидкий формовка силиконовой резины процессор с хорошими экономическими преимуществами.