Giriş:
Silikon kauçuk sıkıştırma kalıplama, sıvı silikon kauçuğun bir kalıp boşluğunda şekillendirilmesini ve kürlenmesini içeren yaygın olarak kullanılan bir üretim sürecidir. Bu çok yönlü yöntem, dayanıklı ve ısıya dirençli ürünler üretme kabiliyetiyle bilinir. Bununla birlikte, yüksek hacimli üretim söz konusu olduğunda, dikkatli bir değerlendirme ve stratejik çözümler gerektiren bazı zorluklar ortaya çıkabilir.
Yüksek hacimli üretim, silikon kauçuk sıkıştırma kalıplamada benzersiz zorlukları beraberinde getirir. Üretimin ölçeği ve hızı, kalıp dolum tutarlılığı, döngü süresi verimliliği ve parlama gibi kusurların ortaya çıkması gibi faktörleri etkileyebilir. Bu zorluklar uygun şekilde ele alınmazsa üretkenliği engelleyebilir, ürün kalitesini etkileyebilir ve üretim maliyetlerini artırabilir.
Bu zorlukların ele alınması başarılı bir üretim için büyük önem taşımaktadır. Üreticiler etkili stratejileri anlayarak ve uygulayarak sıkıştırmalı kalıplama sürecini optimize edebilir, üretim sorunlarını en aza indirebilir ve yüksek hacimli üretimde tutarlı kalite elde edebilir. Bu da ürünlerin pazar taleplerini karşılamasını, katı spesifikasyonlara uymasını ve güvenilir performans sunmasını sağlar.
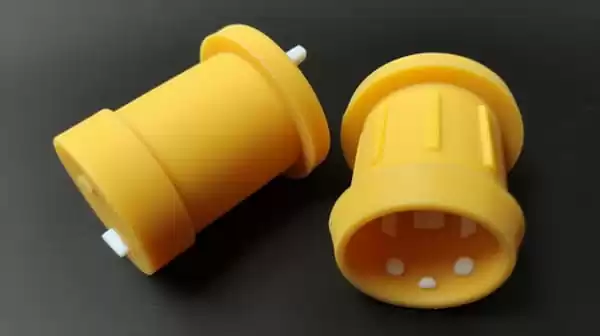
İlerleyen bölümlerde, aşağıdaki konularda karşılaşılan belirli zorlukları daha derinlemesine inceleyeceğiz yüksek hacimli silikon kauçuk sıkıştırma kalıplama ve bunların etkili bir şekilde nasıl üstesinden gelineceğine dair değerli içgörüleri keşfedin. Üreticiler bu zorlukların üstesinden gelerek yüksek hacimli üretimin tüm potansiyelini ortaya çıkarabilir ve çeşitli sektörlere olağanüstü silikon kauçuk ürünler sunabilir.
Sıkıştırmalı Kalıplama ile İlgili Sorunlar:
Sıkıştırmalı kalıplama, yaygın olarak kullanılan bir üretim süreci olmakla birlikte, zorlukları da yok değildir. Üreticiler genellikle üretim verimliliğini ve ürün kalitesini etkileyebilecek birkaç yaygın sorunla karşılaşırlar. İşte sıkıştırma kalıplama ile ilgili bazı temel sorunlar:
1. Tutarsız Kalıp Dolgusu:
Tutarlı kalıp dolumu elde etmek, eşit şekilde kalıplanmış ürünler elde etmek için çok önemlidir. Yüksek hacimli üretimde, malzeme akışı ve dağılımında farklılıklar meydana gelebilir ve bu da kalıp boşluklarının tutarsız bir şekilde doldurulmasına neden olur. Bu da parça boyutlarında farklılıklara, yüzey kusurlarına ve ürün kalitesinde düşüşe yol açabilir.
2. Daha Uzun Çevrim Süreleri:
Enjeksiyon kalıplama işlemi gibi diğer kalıplama teknikleriyle karşılaştırıldığında, sıkıştırmalı kalıplama genellikle daha uzun döngü sürelerine sahiptir. Süreç, silikon kauçuğun kalıp içinde sıkıştırılmasını ve kürlenmesini içerir ve bu da daha fazla zaman alabilir. Yüksek hacimli üretimdeuzun döngü süreleri toplam çıktıyı sınırlayabilir ve üretim sürecini yavaşlatabilir.
3.Flaş Oluşumu:
Flaş, sıkıştırmalı kalıplama sırasında kalıp boşluğundan kaçan fazla malzemeyi ifade eder. Yanlış kalıp tasarımı, aşırı malzeme miktarı veya yetersiz sıkıştırma kuvveti gibi faktörler nedeniyle oluşur. Flaş oluşumu sadece malzemeyi israf etmekle kalmaz, aynı zamanda fazla malzemeyi çıkarmak veya kırpmak için ek işlem sonrası gerektirir. Bu da üretim maliyetlerinin artmasına ve potansiyel kalite sorunlarına yol açar.
Bu sorunlar, yüksek hacimli sıkıştırmalı kalıplamada üretim verimliliğini ve ürün kalitesini önemli ölçüde etkileyebilir. Tutarsız kalıp dolumu, farklı boyutlara ve yüzey kusurlarına sahip parçalara yol açarak ürünlerin reddedilmesine ve israfın artmasına neden olabilir. Daha uzun döngü süreleri genel üretim çıktısını azaltarak pazar taleplerini karşılama kabiliyetini etkiler. Flaş oluşumu sadece malzeme israfını artırmakla kalmaz, aynı zamanda işlem sonrası için ek zaman ve kaynak gerektirir, bu da üretim sürecinin genel verimliliğini ve maliyet etkinliğini etkiler.
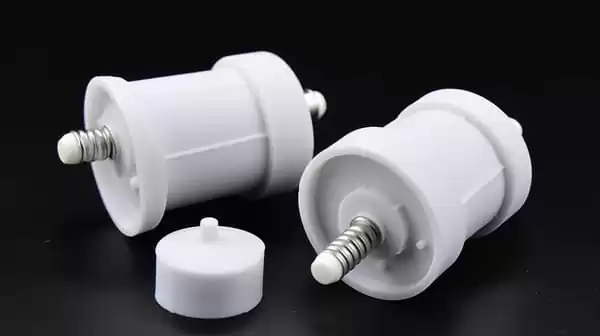
Bu sorunların ele alınması, verimli ve yüksek kaliteli üretimin sağlanması için çok önemlidir. Aşağıdaki bölümlerde, bu zorlukların üstesinden gelmek için etkili stratejileri inceleyeceğiz yüksek hacimli silikon kauçuk sıkıştırma ve enjeksiyon kalıplama uygulamaları. Üreticiler bu stratejileri uygulayarak süreci optimize edebilir, üretkenliği artırabilir ve pazar taleplerini karşılamak için üstün ürünler sunabilir.
Sıkıştırmalı Kalıplamanın Başlıca Dezavantajı:
Özellikle yüksek hacimli üretim senaryolarında sıkıştırma kalıplamanın en büyük dezavantajı, diğer kalıplama tekniklerine kıyasla daha yavaş üretim hızıdır. Enjeksiyon kalıplama gibi daha hızlı süreçlerin aksine, sıkıştırma kalıplama malzeme hazırlama, kalıbın manuel veya otomatik olarak yüklenmesi ve silikon kauçuğun sıkıştırılması ve kürlenmesi gibi ek adımlar içerir. Bu adımlar daha uzun döngü sürelerine katkıda bulunur, bu da genel üretim çıktısını sınırlayabilir ve yüksek hacimli üretimin verimliliğini etkileyebilir.
Yüksek hacimli sıkıştırmalı kalıplamada daha yavaş üretim hızının etkileri önemlidir. İlk olarak, sıkı üretim teslim tarihlerini karşılama ve pazar taleplerine ayak uydurma becerisini engelleyebilir. Sıkıştırmalı kalıplama ile ilişkili daha uzun döngü süreleri, büyük siparişleri kısa bir zaman dilimi içinde yerine getirmek için gereken istenen üretim hızlarıyla uyumlu olmayabilir. Bu durum ürün teslimatında gecikmelere yol açabilir ve potansiyel olarak müşteri memnuniyetini etkileyebilir.
Dahası, daha yavaş üretim hızının mali sonuçları olabilir. Yüksek hacimli üretim genellikle daha yüksek üretim miktarlarının birim başına maliyetleri düşürmeye yardımcı olduğu ölçek ekonomilerine ulaşmayı amaçlar. Ancak, sıkıştırmalı kalıplamanın daha yavaş hızı toplam çıktıyı azaltarak birim başına daha yüksek üretim maliyetlerine yol açabilir. Bu da karlılığı ve pazardaki rekabet gücünü etkileyebilir.
Ayrıca, daha yavaş üretim hızı, pazardaki değişikliklere hızla uyum sağlama veya yeni ürün tasarımları sunma becerisini etkileyebilir. Hızlı tempolu sektörlerde, pazar taleplerine veya tasarım değişikliklerine hızla yanıt verebilmek çok önemlidir. Sıkıştırmalı kalıplamanın zaman alan doğası, üretimde çevikliği ve esnekliği kısıtlayabilir.
Bu dezavantaja rağmen, sıkıştırma kalıplama çok yönlülük, malzeme seçenekleri ve karmaşık parça geometrilerini işleme yeteneği açısından avantajlar sunar. Genellikle benzersiz özellikler veya karmaşık tasarımlar gerektiren belirli uygulamalar için tercih edilir. Üreticiler, süreci optimize etmek ve döngü sürelerini en aza indirmek için stratejiler uygulayarak daha düşük üretim hızının etkisini azaltabilir ve yüksek hacimli üretim senaryolarında sıkıştırma kalıplamanın faydalarını en üst düzeye çıkarabilir.
Sıkıştırmalı Kalıplama Sürecini Etkileyen Faktörler:
Kalıp doldurma, sıkıştırma, kalıptan çıkarma ve genel ürün kalitesinde kritik bir rol oynayan birkaç temel faktör, sıkıştırmalı kalıplama sürecini etkiler. Bu faktörleri anlamak ve etkili bir şekilde yönetmek, tutarlı ve yüksek kaliteli sonuçlar elde etmek için çok önemlidir. Şimdi temel faktörleri inceleyelim:
1. Kalıp Tasarımı:
Kalıp tasarımı, sıkıştırmalı kalıplamada hayati bir rol oynar. Kalıp boşlukları, yolluk sistemleri ve ayırma hatları gibi faktörler malzeme akışını, kalıp dolumunu ve parça sıkıştırmayı etkiler. İyi tasarlanmış kalıplar, düzgün malzeme dağılımını kolaylaştırarak tutarlı parça boyutları sağlar ve kusur oluşumunu azaltır.
2.Kalıp Sıcaklığı:
Sıkıştırmalı kalıplamada kalıp sıcaklığını kontrol etmek çok önemlidir. Kalıp sıcaklığı malzeme akışını, vulkanizasyon sürecini ve parça özelliklerini etkiler. Uygun kalıp sıcaklığı yönetimi, kalıp boşluklarına optimum malzeme akışını sağlar, homojen kürlenmeyi destekler ve nihai ürünün mekanik özelliklerini geliştirir.
3. Sıkıştırma Kuvveti:
Uygun sıkıştırma kuvveti, uygun sıkıştırma ve parça konsolidasyonu elde etmek için gereklidir. Yetersiz sıkıştırma kuvveti eksik dolum ve düşük parça kalitesiyle sonuçlanabilirken, aşırı kuvvet parlama oluşumuna neden olabilir. Sıkıştırma kuvvetinin dikkatli bir şekilde kontrol edilmesi, kalıp boşlukları boyunca eşit sıkıştırma sağlayarak tutarlı parça boyutları ve yüzey kalitesi sağlar.
4. Malzeme Özellikleri:
Sıkıştırmalı kalıplamada kullanılan silikon kauçuk malzemenin özellikleri, süreci ve ürün kalitesini büyük ölçüde etkiler. Viskozite, kürlenme süresi, yüksek kıvamlı kauçuk ve malzemenin mekanik özellikleri kalıp dolumunu, akışı ve nihai parça performansını etkiler. Uygulama için uygun özelliklere sahip doğru malzemenin seçilmesi, istenen sonuçların elde edilmesi için çok önemlidir.
5.Kalıp Ayırıcılar:
Kalıp ayırıcılar, kürlenmiş parçaların kalıptan çıkarılmasını kolaylaştırmak için kullanılır. Kalıp ayırıcıların doğru uygulanması yapışmayı en aza indirir ve parçaların sorunsuz bir şekilde çıkarılmasını sağlayarak kalıptan çıkarma sırasında hasar veya kusur riskini azaltır.
6. Yolluk Burç Tasarımı:
Kalıbı enjeksiyon ünitesine bağlayan yolluk burcunun tasarımı, malzeme akışını ve kalıp boşluklarının doldurulmasını etkileyebilir. Etkili bir yolluk burcu tasarımı, akış hızlarını kontrol etmeye, hava sıkışmasını önlemeye ve kalıp içinde eşit malzeme dağılımı sağlamaya yardımcı olur.
Bu faktörler toplu olarak kalıp doldurma, sıkıştırma, kalıptan çıkarma ve sıkıştırmalı kalıplamada genel ürün kalitesini etkiler. Optimum kalıp tasarımı, uygun kalıp sıcaklığı kontrolü, hassas sıkıştırma kuvveti yönetimi, uygun malzeme seçimi, kalıp ayırıcı maddelerin etkili kullanımı ve özenli yolluk burcu tasarımı tutarlı parça boyutlarına, daha az hataya ve gelişmiş nihai ürün kalitesine katkıda bulunur.
Üreticiler bu faktörleri anlayarak ve optimize ederek süreç verimliliğini artırabilir, istenen parça özelliklerini elde edebilir ve başarılı yüksek kaliteli silikon kauçuk ürünlerin üretimi sıkıştırma kalıplama yoluyla.
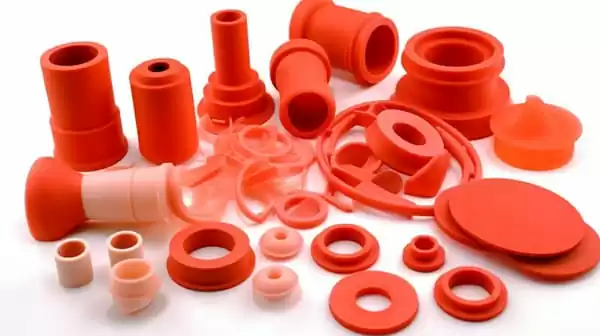
Kauçuk Kalıplama Kusurları:
Kauçuk sıkıştırma kalıplama işlemi de dahil olmak üzere kauçuk kalıplama, nihai ürünün işlevselliğini ve görünümünü etkileyebilecek çeşitli kusurlara karşı hassas olabilir. Bu kusurların ele alınması ve en aza indirilmesi, yüksek kaliteli sonuçlar elde etmek için çok önemlidir. Kauçuk kalıplama ile ilişkili bazı yaygın kusurları inceleyelim:
1.Flash:
Parlama, kalıplama işlemi sırasında kalıp boşluğundan kaçan fazla malzemeyi ifade eder. Genellikle ayırma çizgilerinde veya kalıbın boşluklu veya yanlış hizalamalı alanlarında meydana gelir. Parlama, ürünün boyutsal doğruluğunu tehlikeye atabilir ve nihai parça üzerinde fazla malzeme veya istenmeyen çıkıntılara neden olabilir. Parlamayı gidermek için kırpma veya ikincil işlemler gibi ek son işlemler gerekebilir, bu da üretim süresini ve maliyetleri artırır.
2. Hava Hapsi:
Hava sıkışması, kalıplama işlemi sırasında hava veya gazın kalıplanmış parça içinde sıkışmasıyla meydana gelir. Yanlış havalandırma, yetersiz kalıp tasarımı veya yetersiz kalıp dolgusundan kaynaklanabilir. Hava sıkışması eksik doluma, yapısal zayıflıklara ve parça içinde boşlukların oluşmasına yol açabilir. Bu boşluklar nihai ürünün mukavemet veya dayanıklılık gibi mekanik özelliklerini etkileyerek işlevselliğini tehlikeye atabilir.
3. Yüzey Kusurları:
Yüzey kusurları, kalıplanmış ürünün yüzeyinde çizikler, lekeler, pürüzler veya diğer tutarsızlıklar olarak ortaya çıkabilir. Bu kusurlar kalıp yüzeyi kusurları, zayıf malzeme akışı veya yetersiz kalıp sıcaklığı kontrolü gibi faktörlerden kaynaklanabilir. Yüzey kusurları sadece ürünün estetik görünümünü etkilemekle kalmaz, aynı zamanda özellikle sızdırmazlık veya temas yüzeyleri gibi pürüzsüz bir yüzeyin kritik olduğu uygulamalarda işlevselliğini de etkileyebilir.
4. Boyutsal Tutarsızlıklar:
Boyutsal tutarsızlıklar, kalıplanan parçanın boyut, şekil veya kalınlığındaki farklılıkları ifade eder. Bu varyasyonlar, uygunsuz kalıplama gibi sorunlar nedeniyle ortaya çıkabilir. kalıp tasarımıyetersiz kalıp dolumu veya eşit olmayan sıkıştırma. Boyutsal tutarsızlıklar nihai ürünün uyumunu, montajını veya performansını etkileyerek hassas toleransların elde edilmesini veya belirli işlevsel gereksinimlerin karşılanmasını zorlaştırabilir.
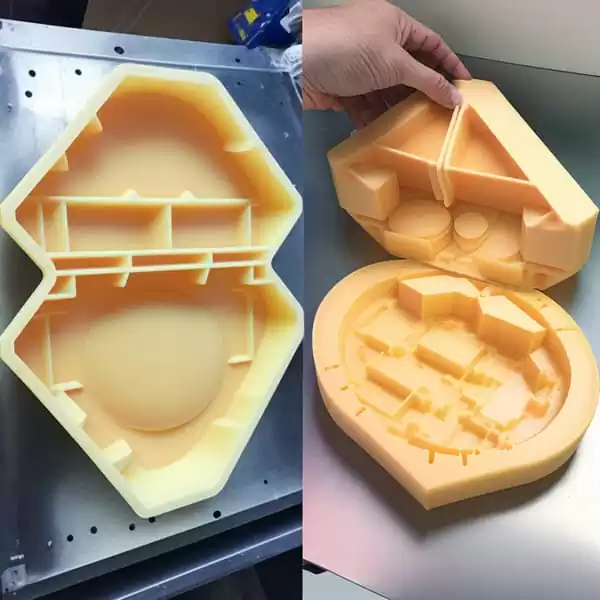
Bu kusurlar nihai ürünün işlevselliği ve görünümü üzerinde önemli etkilere sahip olabilir. Fazla parlama kötü estetiğe yol açabilir, ürünün işlevselliğini engelleyebilir veya montaj sırasında zorluklara neden olabilir. Hava sıkışması ve boşluklar parçanın yapısal bütünlüğünü zayıflatarak mukavemetini veya dayanıklılığını etkileyebilir. Yüzey kusurları sadece görsel çekiciliği tehlikeye atmakla kalmaz, aynı zamanda sürtünme, sızdırmazlık kabiliyeti veya temas özellikleri gibi işlevsel özellikleri de etkileyebilir. Boyutsal tutarsızlıklar düzgün oturmayı engelleyebilir, eşleşen parçalara müdahale edebilir veya ürünün genel performansını veya işlevselliğini etkileyen yanlış hizalamalara neden olabilir.
Üreticiler, etkili transfer kalıplama süreci tasarımı uygulayarak, süreç parametrelerini optimize ederek ve sıkı kalite kontrol önlemleri alarak kauçuk kalıplamadaki bu kusurları en aza indirebilir ve istenen işlevsel ve estetik gereksinimleri karşılayan yüksek kaliteli ürünler sağlayabilir.
Yüksek Hacimli Silikon Kauçuk Sıkıştırmalı Kalıplamada Zorlukların Üstesinden Gelme Stratejileri:
Zorlukların üstesinden gelmek yüksek hacimli silikon kauçuk sıkıştırma kalıplama sistematik bir yaklaşım ve etkili stratejilerin uygulanmasını gerektirir. İşte bu zorlukların üstesinden gelmek için bazı temel stratejiler:
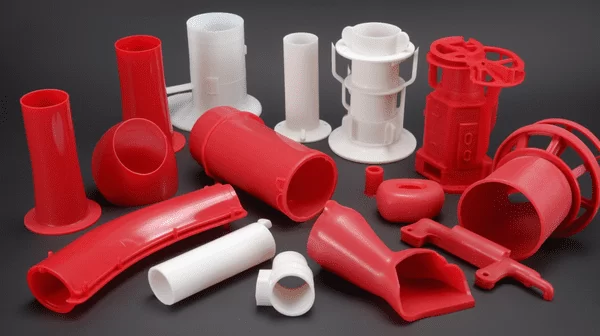
1. Tutarlı Kalıp Dolgusu:
Düzgün malzeme akışı için uygun yolluk ve yolluk sistemi tasarımını sağlamak üzere kalıp tasarımını optimize edin.
Varyasyonları belirlemek ve gerekli ayarlamaları yapmak için gerçek zamanlı basınç ve sıcaklık algılama gibi gelişmiş süreç izleme tekniklerini kullanın.
Optimize etmek için kalıp akış analizi yapın kalıp tasarımı ve tutarlı kalıp dolumu sağlar.
2. Verimli Çevrim Süreleri:
Potansiyel darboğazları belirlemek ve daha hızlı döngü süreleri için kalıp tasarımını optimize etmek için gelişmiş kalıp tasarım yazılımı ve simülasyon araçlarını kullanın.
Yüksek performanslı seçin silikon kauçuk bileşikleri Genel döngü sürelerini azaltmak için hızlı kürlenme için özel olarak formüle edilmiştir.
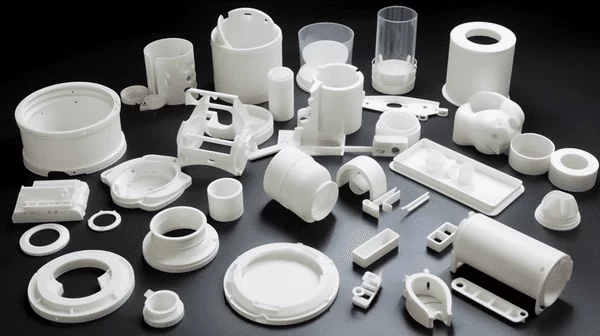
Kürlenme süresini en aza indirmek ve üretim verimliliğini artırmak için sıcaklık, basınç ve zaman gibi proses parametrelerini optimize edin.
3. Flaş Kontrolü:
Parlama oluşumunu en aza indirmek için uygun kalıp tasarımına ve sıkma kuvvetinin hassas kontrolüne odaklanın.
Uygun malzeme akışını sağlamak ve aşırı parlamayı önlemek için kalıp sıcaklığı kontrolünü uygulayın.
Parlama ile ilgili kusurları derhal tespit etmek ve ele almak için düzenli denetim ve izleme de dahil olmak üzere sıkı kalite kontrol önlemleri uygulayın.
4.Kalıp Bakımı:
Kalıpların uzun ömürlü olmasını ve tutarlı performans göstermesini sağlamak için önleyici bir bakım programı oluşturun.
Kalıpları düzenli olarak temizleyin ve yapışmayı önlemek ve kalıptan çıkarmayı iyileştirmek için uygun kalıp ayırıcı maddeler kullanın.
Hasarı önlemek ve kalıpların verimli üretime hazır olmasını sağlamak için uygun kalıp depolama tekniklerini uygulayın.
5. Malzeme Kalitesi:
Saygın malzeme tedarikçileri ile yakın çalışarak tutarlı ve yüksek kaliteli silikon kauçuk bileşikleri.
Malzeme özellikleri için açık spesifikasyonlar ve standartlar oluşturun ve uygunluğu doğrulamak için düzenli testler yapın.
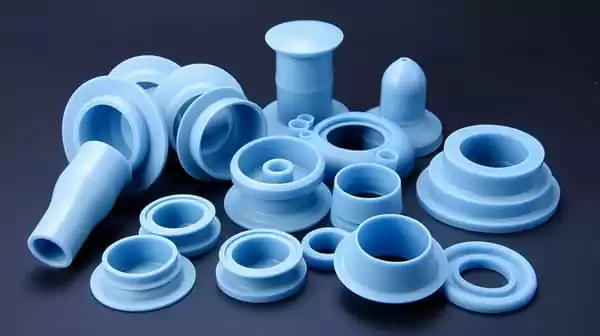
Kauçuk malzemenin amaçlanan uygulamaya uygunluğunu sağlamak ve kusurları en aza indirmek için titiz malzeme testleri gerçekleştirin.
6. Kalıp Tasarım Optimizasyonu:
Verimli üretim ve minimum atık için kalıp boşluklarını, yolluk sistemlerini ve ayırma hatlarını optimize etmek için gelişmiş kalıp tasarım yazılımı ve simülasyon araçlarını kullanın.
Tasarım kalıpları Hava sıkışmasını en aza indirmek ve düzgün malzeme akışı sağlamak için uygun havalandırma ve geçit sistemleri ile.
Uygun malzeme akışı, kalıptan çıkarma ve yüzey kalitesini desteklemek için kalıp sıcaklığı, yolluk burcu tasarımı ve kalıp ayırıcı maddeler gibi faktörleri göz önünde bulundurun.
7. Süreç İzleme ve Denetleme:
Üretim sırasındaki varyasyonları ve potansiyel sorunları belirlemek için gerçek zamanlı süreç izleme tekniklerini uygulayın.
Kalite standartlarına uyulmasını sağlamak ve herhangi bir sapma veya kusuru tespit etmek için sıkıştırmalı kalıplama sürecini düzenli olarak inceleyin ve izleyin.
Proaktif ayarlamalar ve sürekli iyileştirme sağlamak üzere süreç verilerini izlemek ve analiz etmek için istatistiksel süreç kontrol (SPC) yöntemlerini kullanmak.
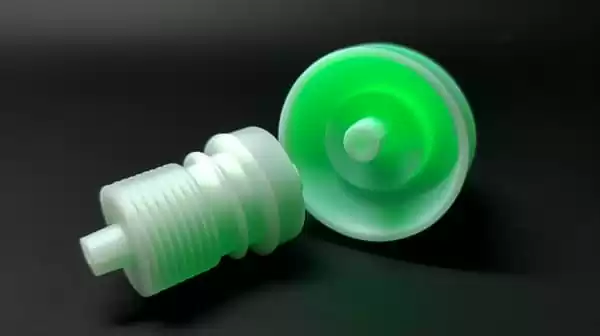
Üreticiler bu stratejileri uygulayarak aşağıdaki zorlukların üstesinden gelebilirler yüksek hacimli silikon kauçuk sıkıştırma kalıplama. Tutarlı kalıp dolumu, verimli döngü süreleri, flaş kontrolü, kalıp bakımı ve malzeme kalitesi, başarılı üretim sonuçlarına ulaşmada hayati rol oynar. Kalıp tasarımının optimize edilmesi, sürecin izlenmesi ve saygın malzeme tedarikçileriyle çalışılması, üretkenliğin artmasına, ürün kalitesinin yükselmesine ve uygun maliyetli üretime katkıda bulunur.
Sonuç:
Sonuç olarak, yüksek hacimli silikon kauçuk sıkıştırma kalıplama, başarılı bir üretim için ele alınması gereken kendine özgü bir dizi zorluk sunar. Bu makale boyunca bu zorlukları inceledik ve bunların etkili bir şekilde nasıl üstesinden gelineceğine dair değerli bilgiler sunduk.
Tutarlı kalıp dolumu, verimli döngü süreleri, flaş kontrolü, kalıp bakımı ve malzeme kalitesi dikkat edilmesi gereken kilit alanlar olarak vurgulanmıştır. Üreticiler bu hususları dikkatlice planlayıp optimize ederek üretkenliği önemli ölçüde artırabilir ve nihai ürünlerin kalitesini yükseltebilirler.
Yüksek hacimli silikon kauçuk sıkıştırma kalıplamanın zorluklarının üstesinden gelmek, sistematik bir yaklaşım ve etkili stratejilerin uygulanmasını gerektirir. Bu, sıvı enjeksiyon kalıplamanın tasarımla optimize edilmesini, gelişmiş süreç izleme tekniklerinin kullanılmasını, düzenli denetimlerin yapılmasını ve saygın malzeme tedarikçileriyle çalışılmasını içerir.
Üreticiler bu zorlukların üstesinden gelerek daha iyi üretkenlik, daha iyi ürün kalitesi elde edebilir ve pazar taleplerini etkin bir şekilde karşılayabilir. Bu da daha fazla müşteri memnuniyeti, daha yüksek kârlılık ve sektörde rekabet avantajı sağlayabilir.
Sonuç olarak, bu stratejilerin dikkatli bir şekilde planlanması, optimizasyonu ve uygulanması, üreticilerin yüksek hacimli silikon kauçuk sıkıştırma kalıplamada başarılı olması için çok önemlidir. Üreticiler, süreçlerini sürekli iyileştirerek ve geliştirerek bu üretim yönteminin tüm potansiyelini ortaya çıkarabilir ve pazarın çeşitli ihtiyaçlarını karşılamak için olağanüstü silikon kauçuk ürünler sunabilirler.