Giriş
Silikon kauçuk kalıplama, modern üretimde çok önemli bir rol oynar ve her gün karşılaştığımız çok çeşitli ürünlerin üretilmesinde temel oluşturur. Bu çok yönlü süreç, esnekliği, ısı direnci ve dayanıklılığı da dahil olmak üzere silikon kauçuğun benzersiz özelliklerinden yararlanma konusunda olağanüstü bir yeteneğe sahiptir. Bununla birlikte, her üretim yöntemi gibi silikon kauçuk kalıplamanın da zorlukları ve kusurları yok değildir. Bu makalede, silikon kauçuk kalıplamanın üretim ortamındaki önemini inceleyecek ve bu karmaşık süreç sırasında ortaya çıkabilecek yaygın zorluklara ve kusurlara ışık tutacağız.
Çeşitli sektörlerdeki üreticiler aşağıdakilere güveniyor silikon kauçuk kalıplama Kritik otomotiv parçalarından hayat kurtaran tıbbi cihazlara ve hatta günlük tüketim mallarına kadar çeşitli bileşenler oluşturmak için. Önemi, olağanüstü performans özelliklerine sahip yüksek kaliteli, hassas mühendislik ürünü parçalar üretme kabiliyetinde yatmaktadır. Silikon kauçuğun aşırı sıcaklıklara, kimyasallara ve yaşlanmaya karşı doğal direnci, onu dayanıklılık ve güvenilirlik gerektiren uygulamalar için birincil seçim haline getirir.
Takip eden bölümlerde, bu yaygın zorlukları derinlemesine inceleyecek ve bunları hafifletmek veya ortadan kaldırmak için uygulanabilir çözümler sunacağız. Üreticiler, silikon kauçuk kalıplamanın inceliklerini ve buna bağlı kusurların nasıl üstesinden gelineceğini daha iyi anlayarak ürünlerinin kendi sektörlerinin katı standartlarını karşılamasını veya aşmasını sağlayabilir. Silikon kauçuk kalıplamada mükemmelliğe ulaşmanın sırlarını çözmek için bu yolculuğa çıkalım.
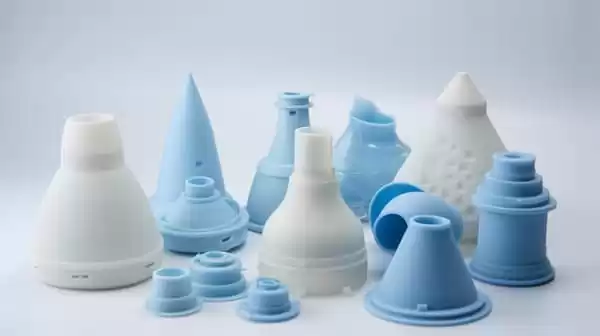
II. Kalıp Malzemesi Kusurları
Nihai Ürün Üzerindeki Etki
Kalıp malzemesi kusurları tüm üretim sürecine uzun bir gölge düşürebilir. Bu kusurlar, kalıp malzemesinin kendisindeki kusurları, safsızlıkları veya tutarsızlıkları içerebilir. Mevcut olduğunda, bu kusurlar nihai silikon kauçuk ürünün kalitesini ve bütünlüğünü doğrudan etkileyen bir dizi soruna yol açabilir. İşte kalıp malzemesi kusurlarının nihai ürünü etkileyebileceği yollardan bazıları:
Yüzey Kusurları: Kalıp malzemesi kusurları, kalıplanan parçanın yüzeyine aktarılarak düzensizliklere, pürüzlü dokulara ve hatta çukur izlerine neden olabilir. Bu kusurlar sadece estetiği etkilemekle kalmaz, aynı zamanda bileşenin işlevselliğini de tehlikeye atabilir.
Azaltılmış Kalıp Ömrü: Kusurlu kalıp malzemeleri daha hızlı aşınabilir veya bozulabilir, bu da kalıp ömrünün kısalmasına neden olur. Bu durum, sık kalıp değişimleri nedeniyle üretim maliyetlerini ve duruş sürelerini artırabilir.
Malzeme Kirlenmesi: Kalıplama malzemesindeki safsızlıklar, kalıplama işlemi sırasında kullanılan sıvı silikon kauçuk parçalarla karışarak malzeme kontaminasyonuna neden olabilir. Bu kirlenme yapısal zayıflıklara, malzeme bütünlüğünün azalmasına ve nihai üründe daha yüksek kusur olasılığına neden olabilir.
Tutarsız Kalıplama: Kalıp malzemesi kusurları, boyutlarda ve et kalınlığında farklılıklar ile tutarsız kalıplamaya yol açarak hassas spesifikasyonların ve toleransların karşılanmasını zorlaştırabilir.
Kalıp Malzemesi Kusurlarını Önlemek için Önleyici Tedbirler
Herhangi bir kalıplama kusurunun ve malzeme hatasının önlenmesi, silikon kauçuk kalıplamanın güvenilirliğini ve tutarlılığını sağlamak için çok önemlidir. İşte dikkate alınması gereken temel önleyici tedbirler:
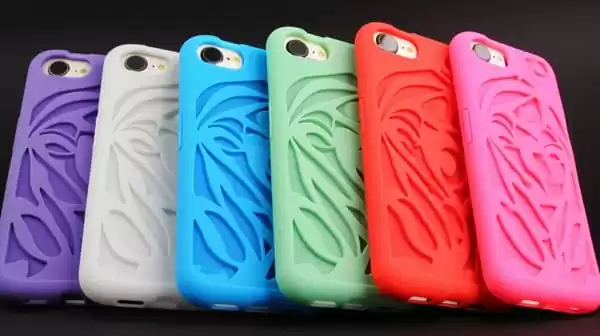
Yüksek Kaliteli Kalıp Malzemeleri Seçin: Kalite ve güvenilirlikleriyle bilinen kalıp malzemelerini seçerek işe başlayın. Birinci sınıf malzemelere yatırım yapmak kusur riskini önemli ölçüde azaltabilir.
Düzenli Muayene ve Bakım: Kalıplarınız için titiz bir denetim ve bakım programı uygulayın. Kalıp yüzeylerini aşınma, hasar veya kusur belirtileri açısından düzenli olarak inceleyin ve sorunları derhal ele alın.
Uygun Depolama: Kalıp malzemelerini neme, kirleticilere ve sıcaklık dalgalanmalarına maruz kalmayı en aza indiren kontrollü bir ortamda saklayın. Doğru depolama, malzemelerin bütünlüğünün korunmasına yardımcı olabilir.
Kalite Kontrol: Üretim döngüsü boyunca sıkı kalite kontrol süreçleri oluşturun. Bu, gelen kalıp malzemelerinin kusurlara karşı incelenmesini ve spesifikasyonlara uygunluğunun sağlanmasını içerir.
Tedarikçilerle İstişare: Malzeme seçimi, kullanımı ve depolanması ile ilgili en iyi uygulamalar konusunda rehberlik sağlayabilecek kalıp malzemesi tedarikçileriyle yakın işbirliği içinde olun.
III. Sıkıştırmalı Kalıplama Kusurları için Çözümler
Sıkıştırmalı Kalıplamada Sık Karşılaşılan Kusurlar
Eksik Doldurma: Sıkıştırma kalıplamadaki başlıca zorluklardan biri, kalıp boşluğunun sıcaklığı içinde tam malzeme dolumu sağlamaktır. Bu, eksik bölümleri veya boşlukları olan parçalarla sonuçlanabilir.
Yüzey Düzensizlikleri: Pürüzlü dokular veya tutarsızlıklar gibi yüzey kusurları oluşabilir ve nihai ürünün estetiğini ve işlevselliğini etkileyebilir.
Çarpıtma ve Bozulma: Sıkıştırma kalıplı parçalar bazen eşit olmayan soğutma veya fırlatma sorunları nedeniyle eğrilme veya bozulma yaşayabilir.
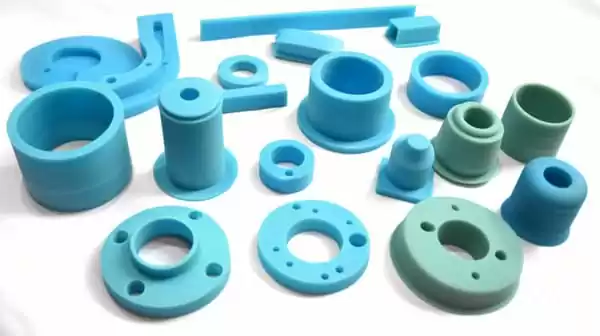
Malzeme Kirlenmesi: Silikon malzemedeki kirleticiler veya safsızlıklar, kalıplanmış parçada yapısal zayıflıklara ve kusurlara yol açabilir.
Çözümler ve Ayarlamalar
Bu yaygın kusurları gidermek için sıkıştırma kalıplamaaşağıdaki çözümleri ve ayarlamaları göz önünde bulundurun:
Sıcaklık ve Basıncı Optimize Edin: Uygun malzeme akışını sağlamak ve kalıp boşluğunu tamamen doldurmak için sıcaklık ve basınç ayarlarını yapın. Özel malzemeniz ve kalıp tasarımınız için ideal kombinasyonu bulmak için farklı ayarlarla denemeler yapın.
Tek Tip Malzeme Dağıtımı: Sıkıştırma işlemi boyunca tutarlı basınç uygulayarak kalıp boşluğu içinde eşit malzeme dağılımı sağlayın. Bu, eksik dolumu ve yüzey düzensizliklerini önlemeye yardımcı olur.
Doğru Havalandırma: Sıkıştırma işlemi sırasında sıkışan havanın dışarı çıkmasını sağlamak için kalıp içinde etkili havalandırma sistemleri uygulayın. Uygun havalandırma boşluk riskini azaltır ve yüzey kalitesini artırır.
Kaliteli Kalıp Ayırıcılar Kullanın: Parça salınımını artırmak ve yüzey kusurlarını en aza indirmek için kalıp yüzeylerine yüksek kaliteli kalıp ayırıcı maddeler uygulayın.
Soğutma Oranlarını Kontrol Edin: Eşit soğutma elde etmek ve bükülme veya bozulmayı önlemek için soğutma sürecini dikkatli bir şekilde yönetin. Doğru soğutma parça bütünlüğünün korunmasına yardımcı olur.
Malzeme Kalite Kontrolü: Kullanarak önceliklendirin yüksek kaliteli silikon malzemekirletici veya yabancı madde içermez. Malzeme partilerini tutarlılık ve saflık açısından düzenli olarak inceleyin.
Bakım ve Temizlik: Kalıplarınız için rutin bir bakım programı oluşturun. Kalıp yüzeylerini düzenli olarak temizleyin ve aşınma, hasar veya kirlenme açısından inceleyin. Herhangi bir sorunu derhal ele alın.
Uygun Sıkıştırma Kuvveti: Malzeme sızıntısını önlemek ve tutarlı parça kalınlığı elde etmek için kalıbın uygun şekilde kelepçelendiğinden emin olun.
IV. Plastik Kusurların Önlenmesi
Yüksek Kaliteli Plastik Malzemelerin Önemi
Silikon kauçuk kalıplamada kullanılan plastik malzemeler nihai ürünün genel kalitesini, dayanıklılığını ve performansını önemli ölçüde etkiler. İşte bu yüzden yüksek kaliteli plastik malzemeler tercih etmek çok önemlidir:
Malzeme Bütünlüğü: Yüksek kaliteli plastik malzemelerin safsızlık, kirletici madde veya tutarsızlık içerme olasılığı daha düşüktür. Bu, malzemenin kalıplama süreci boyunca yapısal bütünlüğünü korumasını sağlar ve böylece kusur riskini azaltır.
Tutarlılık: Üstün kaliteli plastik malzemeler tutarlı özellikler ve davranış sergiler. Tutarlılık, düzgün malzeme akışı, tam kalıp boşluğu dolumu ve kontrollü soğutma elde etmek için gereklidir ve bunların tümü hataların önlenmesine katkıda bulunur.
Boyutsal Kararlılık: Kaliteli plastikler, soğutma sırasında büzülme veya eğrilme gibi boyutsal değişikliklere daha az eğilimlidir. Bu kararlılık, nihai ürünün boyutlarının doğruluğunun korunmasına yardımcı olur.
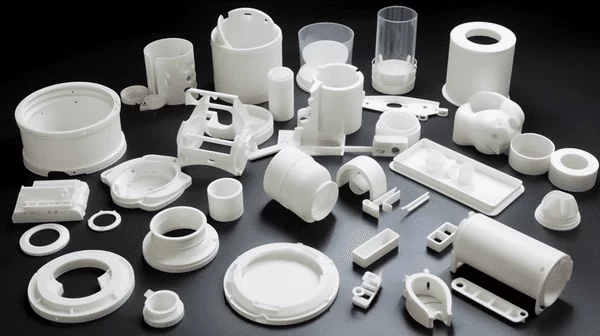
Azaltılmış Malzeme Kontaminasyonu: Yüksek kaliteli plastik malzemelerin sıvı silikon kauçuk filme kirletici madde katma olasılığı daha düşüktür, böylece kalıplanan parçada malzeme kontaminasyonu ve yapısal kusur riski azalır.
Tutarlı İşleme Koşulları
Silikon kauçuk kalıplamada plastik kusurlarının önlenmesinde tutarlı işleme koşullarının sürdürülmesi de aynı derecede hayati önem taşır. İşte tutarlı koşulların hataların önlenmesine nasıl katkıda bulunabileceği:
Sıcaklık Kontrolü: Kalıplama işlemi sırasında malzeme sıcaklık ayarlarının hassas kontrolü kritik öneme sahiptir. Tutarlı sıcaklıklar düzgün malzeme akışı sağlar, çarpılma riskini azaltır ve parça boyutlarının korunmasına yardımcı olur.
Basınç Regülasyonu: Enjeksiyon basıncı ve tutma basıncı dahil olmak üzere uygun basınç kontrolü, tutarlı parça yoğunluğu elde etmek ve kusur olasılığını azaltmak için gereklidir.
Enjeksiyon Hızı: Tutarlı enjeksiyon hızı, kalıp boşluğu içinde düzgün malzeme dağılımının korunmasına yardımcı olarak boşlukları, yüzey kusurlarını ve eksik dolumu önler.
Soğutma Oranları: Soğutma hızlarının yönetilmesi, malzemenin eşit şekilde soğumasını sağlayarak eğrilme, yüzey kusurları ve malzeme dengesizliği riskini en aza indirir.
Malzeme Taşıma: Plastik malzemelerin uygun şekilde taşınması ve depolanması, kontaminasyonu önlemek ve malzeme bütünlüğünü korumak için çok önemlidir. Neme, kirletici maddelere ve sıcaklık dalgalanmalarına maruz kalmasını önleyin.
Kalite Kontrol ve İzleme
Kullanmaya ek olarak yüksek kaliteli plastik malzemeler ve tutarlı işleme koşullarının sürdürülmesi için kapsamlı kalite kontrol ve izleme şarttır. Gelen malzeme partilerini düzenli olarak inceleyin, sıcaklık ve basınç ayarlarını izleyin ve herhangi bir sapma veya anormalliği tespit etmek için kalıplama sürecinin görsel denetimlerini yapın.
V. Enjeksiyon Kalıplamadaki Kusurların Nedenleri
Yaygın Kusur Nedenleri
Yanlış Kalıp Tasarımı: Kalıbın tasarımı enjeksiyon kalıplamada kritik bir faktördür. Kalıp tasarımı hassasiyetten yoksun olduğunda, yetersiz havalandırmaya sahip olduğunda veya uygun olmayan kalıp kapıları konumlarında kusurlar meydana gelebilir, bu da kalıp boşluğunun yanıp sönmesi veya eksik doldurma kaynak hatları gibi sorunlara yol açar.
Yetersiz Sıcaklık Kontrolü: Enjeksiyon kalıplamada sıcaklık kontrolü çok önemlidir. Kalıp ve malzeme sıcaklıklarındaki değişimler eğilme, yüzey kusurları ve boyutsal dengesizlik gibi kusurlara neden olabilir.
Kötü Malzeme Kalitesi: Enjeksiyon kalıplamada kullanılan silikon kauçuk malzemenin kalitesi nihai ürünü doğrudan etkiler. Malzeme kusurları veya tutarsızlıkları, malzeme kontaminasyonu, boşluklar ve parça bütünlüğünün azalması gibi sorunlara yol açabilir.
Tutarsız enjeksiyon parametreleri işleme: Basınç, hız ve zaman gibi enjeksiyon parametrelerindeki sapmalar kusurlara neden olabilir. Örneğin yetersiz enjeksiyon basıncı veya aşırı yüksek enjeksiyon basıncı veya hızı, eksik doluma veya akış hatlarına yol açabilir.
Uygun Olmayan Küf Havalandırması: Yetersiz kalıp havalandırması, kalıp boşluğu içinde havayı hapsederek kalıplanmış bileşende hava kabarcıklarına veya boşluklara neden olabilir.
Malzeme Kirlenmesi: Silikon malzemedeki kirleticiler veya safsızlıklar nihai ürünün bütünlüğünü tehlikeye atabilir ve yapısal kusurlara yol açabilir.
Kalıp Yüzey Pürüzlülüğü: Kalıp yüzeyi pürüzlülüğü kalıplanan parçaya geçerek yüzey kusurlarına veya hatalara neden olabilir.
Nedenler ve Önleme Konusunda İçgörüler
Enjeksiyon kalıplamadaki hataları azaltmak için aşağıdaki bilgileri göz önünde bulundurun:
Kalıp Tasarımı: Tek tip duvar kalınlığına, uygun havalandırma kanallarına ve stratejik olarak yerleştirilmiş kapılara sahip hassas kalıp tasarımına yatırım yapın. Tasarım kusurlarını derhal giderin.
Sıcaklık Kontrolü: Enjeksiyon işlemi boyunca tutarlı kalıp ve malzeme sıcaklıklarını koruyun. Sıcaklık değişimlerini en aza indirmek için sıcaklık kontrol sistemlerini kullanın.
Malzeme Kalitesi: Güvenilir tedarikçilerden yüksek kaliteli silikon kauçuk malzeme temin edin. Malzeme partilerini tutarlılık ve saflık açısından düzenli olarak inceleyin.
Enjeksiyon Parametreleri: Optimum malzeme akışı elde etmek, kalıp boşluğunu tamamen doldurmak ve boşluklar ve akış çizgileri gibi kusurları önlemek için enjeksiyon parametrelerini dikkatlice izleyin ve ayarlayın.
Kalıp Havalandırma: Enjeksiyon sırasında sıkışan havanın dışarı çıkmasını sağlayarak hava kabarcığı ve boşluk riskini azaltmak için etkili kalıp havalandırması uygulayın.
Malzeme Kirlenmesi: Malzeme kontaminasyonunu önlemek için temiz ve kontrollü bir üretim ortamı sağlayın. Enjeksiyondan önce silikon malzemeyi filtreleyin veya eleyin.
Kalıp Yüzey İşlemi: Nihai üründe pürüzsüz bir yüzey sağlamak için kalıp yüzey kaplamasına dikkat edin. Gerekirse kalıp ayırıcı maddeler kullanın.
V. Enjeksiyon Kalıplamadaki Kusurların Nedenleri
Yaygın Kusur Nedenleri
Yanlış Kalıp Tasarımı:
Kalıbın tasarımı enjeksiyon kalıplamada kritik bir faktördür. Kalıp tasarımında hassasiyet olmadığında, yetersiz havalandırma olduğunda, uygun olmayan yolluk konumları olduğunda veya büzülme hesaba katılmadığında kusurlar meydana gelebilir, bu da yanıp sönme, kısa atışlar veya kalıp boşluğunun eksik doldurulması gibi sorunlara yol açar.
Yetersiz Sıcaklık Kontrolü:
Enjeksiyon kalıplamada sıcaklık kontrolü çok önemlidir. Kalıp ve malzeme sıcaklıklarındaki değişimler eğilme, yüzey kusurları ve boyutsal dengesizlik gibi kusurlara neden olabilir.
Kötü Malzeme Kalitesi:
Kullanılan silikon kauçuk malzemenin kalitesi enjeksiyon kalıplama nihai ürünü doğrudan etkiler. Malzeme kusurları veya tutarsızlıkları malzeme kontaminasyonu, boşluklar ve parça bütünlüğünün azalması gibi sorunlara yol açabilir.
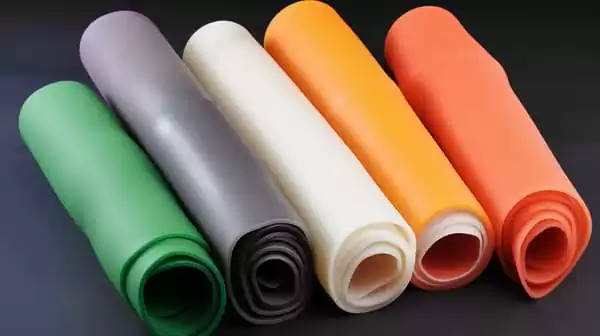
Tutarsız Enjeksiyon Parametreleri: Basınç, hız ve zaman gibi enjeksiyon parametrelerindeki sapmalar kusurlara neden olabilir. Örneğin yetersiz enjeksiyon basıncı veya aşırı yüksek enjeksiyon hızı, eksik doluma veya akış hatlarına yol açabilir.
Uygun Olmayan Küf Havalandırması: Yetersiz kalıp havalandırması, kalıp boşluğu içinde havayı hapsederek kalıplanmış bileşende hava kabarcıklarına veya boşluklara neden olabilir.
Malzeme Kirlenmesi: Silikon malzemedeki kirleticiler veya safsızlıklar nihai ürünün bütünlüğünü tehlikeye atabilir ve yapısal kusurlara yol açabilir.
Kalıp Yüzey Pürüzlülüğü: Kalıp yüzeyi pürüzlülüğü kalıplanan parçaya geçerek yüzey kusurlarına veya hatalara neden olabilir.
Nedenler ve Önleme Konusunda İçgörüler
Enjeksiyon kalıplamadaki hataları azaltmak için aşağıdaki bilgileri göz önünde bulundurun:
Kalıp Tasarımı: Tek tip duvar kalınlığına, uygun havalandırma kanallarına ve stratejik olarak yerleştirilmiş kapılara sahip hassas kalıp tasarımına yatırım yapın. Tasarım kusurlarını derhal giderin.
Sıcaklık Kontrolü: Enjeksiyon işlemi boyunca tutarlı kalıp ve malzeme sıcaklıklarını koruyun. Sıcaklık değişimlerini en aza indirmek için sıcaklık kontrol sistemlerini kullanın.
Malzeme Kalitesi: Güvenilir tedarikçilerden yüksek kaliteli silikon kauçuk malzeme temin edin. Malzeme partilerini tutarlılık ve saflık açısından düzenli olarak inceleyin.
Enjeksiyon Parametreleri: Optimum malzeme akışı elde etmek, kalıp boşluğunu tamamen doldurmak ve boşluklar ve akış çizgileri gibi kusurları önlemek için enjeksiyon parametrelerini dikkatlice izleyin ve ayarlayın.
Kalıp Havalandırma: Enjeksiyon sırasında sıkışan havanın dışarı çıkmasını sağlayarak hava kabarcığı ve boşluk riskini azaltmak için etkili kalıp havalandırması uygulayın.
Malzeme Kirlenmesi: Malzeme kontaminasyonunu önlemek için temiz ve kontrollü bir üretim ortamı sağlayın. Enjeksiyondan önce silikon malzemeyi filtreleyin veya eleyin.
Kalıp Yüzey İşlemi: Nihai üründe pürüzsüz bir yüzey sağlamak için kalıp yüzey kaplamasına dikkat edin. Gerekirse kalıp ayırıcı maddeler kullanın.
VI.Yaygın Kusurlar ve Çözümleri
1. Hava Kabarcıkları:
Kusur: Hava kabarcıkları, kalıplanmış parça içinde sıkışmış hava cepleridir, bu da yapısını zayıflatabilir ve estetiği etkileyebilir.
Çözüm: Hava kabarcıklarını önlemek için uygun kalıp havalandırması sağlayın ve kalıp sıcaklığı ve enjeksiyon basıncı dahil olmak üzere tutarlı enjeksiyon parametreleri kullanın. Havalandırma kanalları ve yeterli kalıp sıcaklığının korunması, enjeksiyon sırasında havanın dışarı çıkmasına yardımcı olur.
2. Yüzey Kusurları:
Kusur: Pürüzlü dokular veya düzensizlikler gibi yüzey kusurları, ürünün görünümünü ve işlevselliğini bozabilir. kalıplanmış parça.
Çözüm: Hassas kalıp yüzey pürüzlülüğünü koruyarak pürüzsüz bir yüzey finişi elde edin. Uygun kalıp yağı uygulaması da finisajı geliştirebilir.
3. Flaş:
Kusur: Fazla malzeme kalıp boşluğundan kaçtığında, parçanın kenarları boyunca istenmeyen ince çıkıntılar meydana gelir.
Çözüm: Kalıp tasarımını iyileştirin ve yanıp sönmeyi önlemek için uygun kalıp sıkıştırmasını sağlayın. Ayrıca, aşırı dolumu önlemek için enjeksiyon basıncını, sıcaklığını ve enjeksiyon hızını kontrol edin.
4. Eksik Doldurma:
Kusur: Eksik doldurma, eksik bölümleri veya boşlukları olan parçalara yol açar.
Çözüm: Kalıp boşluğunun tamamen dolmasını sağlamak için enjeksiyon hızı ve basıncı dahil olmak üzere enjeksiyon parametrelerini ayarlayın. Uygun kalıp havalandırması da doluma yardımcı olabilir.
5. Çarpıtma:
Kusur: Eşit olmayan soğutma hızları nedeniyle çarpılma veya bozulma meydana gelebilir ve bu da parça deformasyonlarına yol açabilir.
Çözüm: Çarpılmayı önlemek için soğutma hızlarını kontrol edin ve tutarlı kalıp ve malzeme sıcaklıklarını koruyun. Yeterli soğutma ile homojen soğutma elde edin kalıp tasarımı.
6. Malzeme Kirlenmesi:
Kusur: Malzeme kontaminasyonu silikon kauçuğu zayıflatabilir ve yapısal kusurlara neden olabilir.
Çözüm: Yüksek kaliteli silikon malzeme tedarik edin, temiz bir üretim ortamı sağlayın ve kontaminasyonu önlemek için malzemeleri filtreleyin veya eleyin.
7. Akış Hatları:
Kusur: Akış çizgileri, malzeme akışı tutarsızlıklarından kaynaklanan parça yüzeyindeki görünür çizgiler veya izlerdir.
Çözüm: Düzgün malzeme akışını desteklemek için enjeksiyon hızı da dahil olmak üzere enjeksiyon parametrelerini ayarlayın. Uygun kalıp tasarımı ve havalandırma, enjeksiyon hızını artırabilir ve ayrıca akış çizgilerini ortadan kaldırmaya yardımcı olabilir.
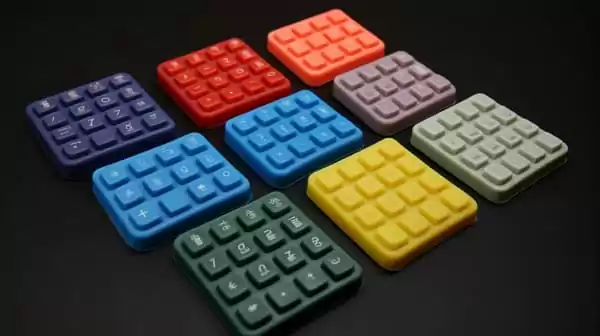
Sonuç
Silikon kauçuk kalıplama son derece etkili bir üretim yöntemidir, ancak zorlukları da yok değildir. Yaygın kusurlar nihai ürünün kalitesini ve bütünlüğünü tehlikeye atabilir. Ancak üreticiler, temel çözümleri ve en iyi uygulamaları uygulayarak bu engellerin üstesinden gelebilir ve yüksek kaliteli silikon kauçuk bileşenler üretebilirler.
Silikon kauçuk kalıplama dünyasında mükemmellik arayışı devam eden bir yolculuktur. Bu çıkarımları benimseyerek ve sürekli izleme ve iyileştirmenin önemini vurgulayarak, üreticiler yalnızca yaygın kusurları çözmekle kalmaz, aynı zamanda silikon kauçuk kalıplama süreçlerinin genel kalitesini ve verimliliğini de artırabilir. Her iyileştirme ile üretim operasyonlarında en yüksek mükemmellik standartlarına ulaşmaya daha da yaklaşırlar.