Silikon kauçuk kokusuzdur ve toksik değildir, yüksek sıcaklıklardan ve soğuk özelliklerden korkmaz, 300 santigrat derecede ve eksi 90 santigrat derecede "sakin", "yüz renk değiştirmez" ve hala iyi bir mukavemete ve esnekliğe sahiptir.
Silikon kauçuk ayrıca iyi elektrik yalıtımı, oksijen direnci ve yaşlanma direnci, ışık direnci ve yaşlanma direncinin yanı sıra kalıp direnci, kimyasal stabilite vb.
Yüksek sıcaklıkta vulkanize dimetil silikon kauçuğun piyasaya sürülmesinden bu yana, silikon kauçuğun hızlı gelişimi, silikon kauçuk yapımı yaygın olarak kullanılır.
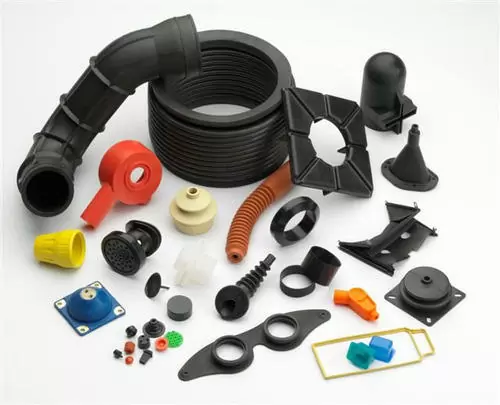
Silikon kauçuğun yapısal özellikleri ve mükemmel performansı
1. Yüksek moleküler bağ enerjisi
C-C bağ enerjisi 348 KJ/mol; Si-O bağ enerjisi 444 KJ/mol kadar yüksektir; ultraviyole (300 nm) enerjisi ise sadece 400 KJ/mol'dür. Moleküler zincir sarmaldır, silikonun bağ açısı daha büyüktür (130°- 160°) ve moleküller arası kuvvet küçüktür.
2. Silikon kauçuğun benzersiz özellikleri
Mükemmel hava koşullarına dayanıklılık performansı, UV, O2, O3, tuz spreyi vb.
Düşük yüzey enerjisi, mükemmel su iticilik ve su itici migrasyon.
Mükemmel yalıtım performansı ve geniş bir sıcaklık ve frekans aralığında kararlı dielektrik özellikler. Çok iyi ark direnci ve kaçak direnci.
Yüksek sıcaklıklara karşı iyi direnç 180-200°C'de sürekli olarak kullanılabilir. Silikon kauçuğun oda sıcaklığındaki mukavemeti, doğal kauçuğun veya bazı sentetik kauçuğun sadece yarısı olmasına rağmen, 200 ° C'nin üzerindeki yüksek sıcaklıklı bir ortamda, silikon kauçuk hala belirli bir esneklik, esneklik ve yüzey sertliğini koruyabilir ve mekanik özelliklerde önemli bir değişiklik olmaz.
İyi elastikiyet ve düşük sıcaklık esnekliği, -50 ℃'de kullanılabilir. Silikon kauçuğun camsı geçiş sıcaklığı genellikle -70~-50℃'dir ve özel formülasyon -100℃'ye ulaşabilir, bu da mükemmel düşük sıcaklık performansını gösterir. Bu, havacılık ve uzay sanayi hatları için önemlidir.
İyi alev geciktirici performans, yanarken neredeyse hiç toksik ve zararlı gaz açığa çıkmaz. Şeffaf ürünler haline getirilebilir ve kabarcıklar veya safsızlıklar gibi kusurlar görsel inceleme ile kolayca tespit edilebilir.
Genel amaçlı kauçukla karşılaştırıldığında, her üç ana silikon kauçuk türü de nispeten basit birleşme bileşenlerine sahiptir ve sıcak vulkanize tipler de öyle.
Ham kauçuğa ek olarak, eşleştirme maddesi esas olarak bir takviye maddesi, vulkanize edici madde ve bazı özel katkı maddeleri içerir, genellikle pratik bir formül oluşturmak için sadece 5 ila 6 bileşen içerir.
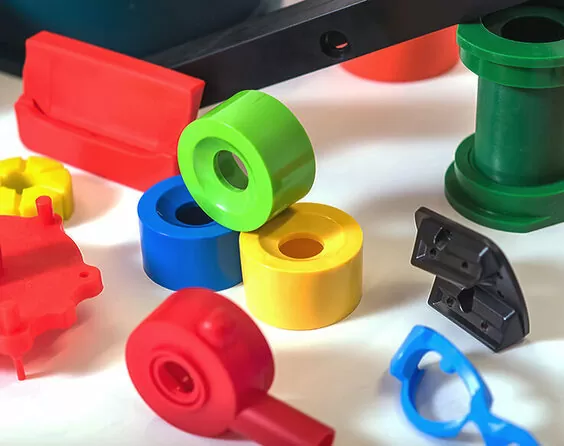
Silikon kauçuk formülasyon tasarımı aşağıdaki noktaları dikkate almalıdır:
(1) Ham kauçuğun yüksek doygunluğu için silikon kauçuk, genellikle sülfür sarı vulkanizasyon ve sıcak vulkanizasyon kullanımı kullanamaz.
Sıcak vulkanizasyon, vulkanize edici bir ajan olarak organik peroksittir, bu nedenle kauçuk, peroksitin ayrışma ürünleri ile etkileşime girebilecek aktif maddeler içermemelidir, aksi takdirde vulkanizasyonu etkileyecektir.
(2) Silikon kauçuk ürünler genellikle yüksek sıcaklıklarda kullanılır, bileşiğin yüksek sıcaklıklarda stabil kalması gerekir, bu nedenle takviye maddesi olarak genellikle inorganik oksitler kullanılır.
(3) Eser miktarda asit veya alkali ve diğer polar kimyasal reaktifler içindeki silikon kauçuğun silikon bağının bölünmesine ve yeniden düzenlenmesine neden olması kolaydır, bu da silikon kauçuğun ısı direncinin azalmasına neden olur.
Bu nedenle, eşleştirme maddelerinin seçimi asitlik ve alkaliliklerini dikkate almalı ve ayrıca vulkanize kauçuğun performansını etkilememek için peroksit ayrışma ürünlerinin asitliğini de hesaba katmalıdır.
Ham kauçuk seçimi
Formül tasarlanırken, ürünün performansına ve kullanım koşullarına göre farklı özelliklere sahip ham kauçuk seçilmelidir.
Genel olarak silikon kauçuk ürünler 70 ℃ ~ 250 ℃ aralığında sıcaklık kullanımı gerektirdiğinde, vinil silikon kauçuk kullanabilir; ürünlerin kullanımı daha yüksek sıcaklık gerektirdiğinde (-90 ~ 300 ℃), düşük fenil silikon kauçuk kullanabilir; ürünler yüksek ve düşük sıcaklık direnci gerektirdiğinde ve yakıt veya çözücüye direnmesi gerektiğinde, florosilikon kauçuk kullanmalıdır.
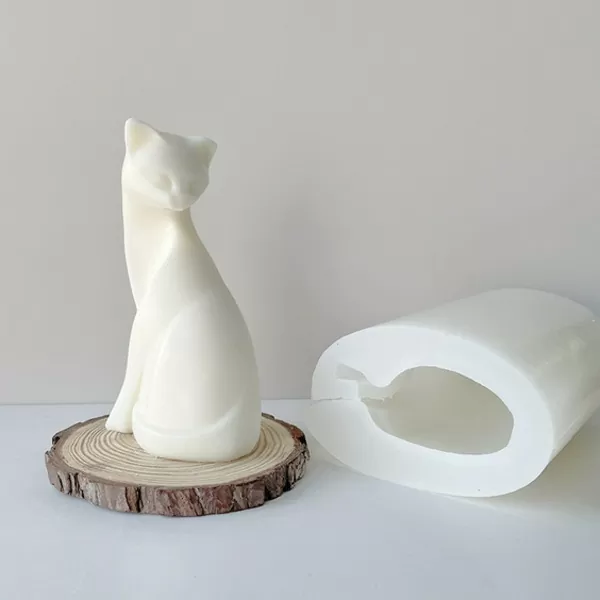
Vulkanize edici madde
Sıcak vulkanize silikon kauçuk için kullanılan vulkanizasyon maddesi esas olarak organik peroksit, alifatik azo bileşikleri, inorganik bileşikler, yüksek enerjili ışınlar vb. olup, bunlardan en yaygın kullanılanı organik peroksittir.
Bunun nedeni, organik peroksitlerin oda sıcaklığında genellikle daha kararlı olması, ancak daha yüksek vulkanizasyon sıcaklıklarında serbest radikaller üretmek için hızla ayrışabilmesi ve böylece silikon kauçuğun çapraz bağlı hale gelmesidir.
Peroksitler aktivite seviyelerine göre iki kategoriye ayrılabilir. Bir tür genel amaçlı, yani her türlü malzeme için vulkanize edilebilen yüksek aktiviteli silikon kauçukDiğer tip ise vinil-spesifik, yani düşük aktiviteli olup sadece vinil içeren silikon kauçuk için vulkanize edilebilir.
İki peroksit türü arasındaki yukarıdaki genel farklılıklara ek olarak, her peroksitin kendine has özellikleri vardır. Vulkanize edici ajan BP, hızlı vulkanizasyon hızı ve yüksek üretim verimliliği ile kalıplanmış ürünler için en yaygın kullanılan vulkanize edici ajandır, ancak kalın ürünlerin üretimi için uygun değildir.
Vulkanize edici ajan DCBP, ürünlerinin uçması kolay olmadığından, basınçsız vulkanizasyon da kabarcıklar üretecektir, özellikle sıcak hava sürekli vulkanizasyonun preslenmiş ürünleri için uygundur, ancak ayrışma sıcaklığı düşüktür, kavurmaya neden olması kolaydır, kauçuk depolama süresi kısadır.
Vulkanize edici ajan BP ve DCBP kristal tozdur, patlayıcıdır, güvenli çalışma için ve dispersiyon için uygundur, genellikle silikon yağında veya silikon kauçuk Geçmişte, 50%'nin genel bir içeriği. Vulkanize edici maddenin kaynama noktası 110℃ olup çok uçucudur.
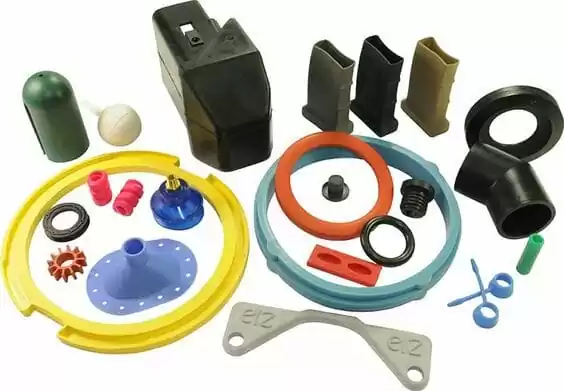
Kauçuk oda sıcaklığında depolandığında vulkanize edici madde buharlaşır ve en iyi taşıyıcı olarak moleküler elek şeklinde kullanılır. Vulkanize edici madde DTBP hava veya karbon siyahı ile reaksiyona girmez ve iletken kauçuk ve zor kalıplama işlemlerine sahip ürünlerin üretiminde kullanılabilir.
Vulkanize edici ajan DBPMH, DTBP'ye benzer, ancak oda sıcaklığında uçucu değildir ve ayrışma ürünleri uçucudur, bu da ikinci aşama vulkanizasyon süresini kısaltabilir.
Vulkanize edici ajan DCP, oda sıcaklığında uçucu hale gelmez, vinil özel bir tipin özellikleri olarak ele alınırken, ayrışma ürünü uçuculuğu da düşüktür ve küçük dış basınç durumlarının vulkanizasyonu için kullanılabilir. Vulkanize edici madde TBPB, sünger ürünlerin imalatında kullanılır.
Peroksit miktarı çeşitli faktörlerden etkilenir. Örneğin, ham kauçuk türleri, dolgu maddesi türü ve miktarı, işleme teknolojisi vb. Genel olarak, vulkanize edici madde, istenen çapraz bağlanma elde edilebildiği sürece mümkün olduğunca az olmalıdır.
Ancak gerçek miktar teorik miktardan çok daha yüksektir, çünkü düzensiz karıştırma, kauçuğun depolanmasında peroksit kaybı, havanın vulkanizasyonu ve diğer bileşik maddelerin bloke edilmesi gibi çeşitli işleme faktörleri dikkate alınmalıdır.
Vinil için silikon kauçuk kalıplı ürünler kauçuk ile, çeşitli peroksit ortak ağırlık parçaları aralığı aşağıdaki gibidir.
Bileşen Ağırlığı
Tiksotropik ajan BP 0,5 ~ 1
Tiksotropik ajan DCBP 1~2
Tiksotropik ajan DTBP 1~2
Tiksotropik ajan DCP 0,5~1
Sülfürleme maddesi DBPMH 0,5~1
Tiksotropik ajan TBPB 0,5~1
Vinil içeriğindeki artışla birlikte peroksit miktarı azaltılmalıdır. Yapıştırıcı macun preslenmiş ürün yapıştırıcı ve yapıştırıcıdaki peroksit miktarı kalıplanmış yapıştırıcıdakinden daha yüksek olmalıdır.
Bazı durumlarda, iki peroksit kullanımı vulkanize edici madde miktarını azaltabilir ve vulkanizasyon sıcaklığını uygun şekilde düşürerek vulkanizasyonun etkisini artırabilir.
Güçlendirici madde
Takviyesiz silikon kauçuk vulkanize kauçuğun mukavemeti çok düşüktür, sadece yaklaşık 0.3MPa'dır ve pratik kullanım değeri yoktur. Uygun bir takviye maddesinin kullanılması, silikon kauçuk vulkanizasyon kauçuğunun mukavemetini 3.9-9.8MPa'ya çıkarabilir, bu da silikon kauçuğun performansını artırmak ve ürünlerin hizmet ömrünü uzatmak için son derece önemlidir.
Silikon kauçuk takviye dolgu seçimi, silikon kauçuğun yüksek sıcaklıkta kullanımını ve peroksit ile vulkanizasyonu, özellikle asidik ve alkali maddelerin silikon kauçuk üzerindeki olumsuz etkilerini dikkate almalıdır.
İlki 10-50nm çapa ve 70-400m²/g özgül yüzey alanına sahip olup daha iyi bir takviye etkisine sahiptir; ikincisi ise 300-10000nm olup 30m²/g veya daha az özgül yüzey alanına sahip olup daha zayıf bir takviye etkisine sahiptir.
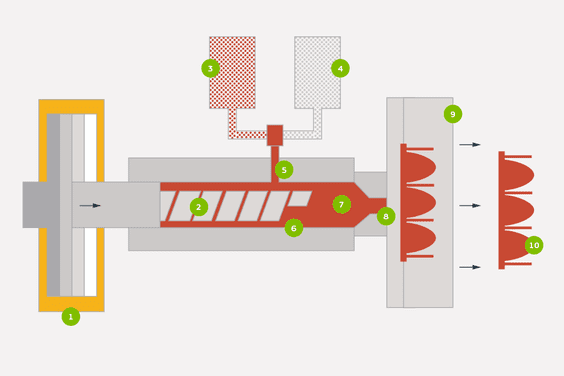
Takviye için dolgu maddesi
(1) Silika, silikon kauçuk takviye dolgusunun türü ve özellikleri esas olarak silika olarak da bilinen sentetik silikayı ifade eder. Silika, füme silika ve çökeltilmiş silika olarak ikiye ayrılır.
a. Füme silika partiküllerinin boyutu, spesifik yüzey alanı, yüzey özellikleri ve yapısı hammadde gaz oranı, yanma hızı, SiO2 çekirdeklerinin yanma odasında kalma süresi ve diğer faktörlerle ilişkilidir.
Füme silika partikülleri ne kadar ince olursa, spesifik yüzey alanı o kadar büyük olur ve takviye etkisi o kadar iyi olur, ancak operasyonel performans o kadar kötü olur. Aksine, partikülleri daha iri ve spesifik yüzey alanı daha küçüktür, takviye etkisi zayıftır, ancak çalışabilirlik daha iyidir.
Füme silika, aşağıdakiler için en yaygın kullanılan takviye maddelerinden biridir silikon kauçukve bununla güçlendirilmiş kauçuk, yüksek mekanik mukavemete ve vulkanize kauçuğun iyi elektriksel özelliklerine sahiptir. Füme silika, kauçuk kullanımı için farklı gereksinimler üretmek üzere diğer takviye maddeleri veya zayıf takviye maddeleri ile birlikte de kullanılabilir.
Çöktürülmüş silika
Çökeltilmiş silikanın performansı, asitlik ve sıcaklık gibi çökeltme koşullarından etkilenir.
ile karşılaştırıldığında silikon kauçuk bileşiği Füme silika ile güçlendirilmiş, çökeltilmiş silika ile güçlendirilmiş bileşiğin mekanik mukavemeti biraz daha düşüktür ve özellikle nemden sonra dielektrik özellikleri daha zayıftır, ancak ısı direnci yaşlanma özellikleri daha iyidir ve bileşiğin maliyeti çok daha düşüktür. Ürünün mekanik mukavemeti yüksek olmadığında, çökeltilmiş silika kullanılabilir veya füme silika ile birlikte kullanılabilir.
Silika, yüzeyi hidrofobik bir madde haline getirmek için uygun bileşiklerle muamele edilebilir. İki ana işlem yöntemi vardır: sıvı faz ve gaz fazı.
Sıvı faz yönteminin koşulları kontrol etmesi kolaydır, ürün kalitesi istikrarlıdır ve arıtma etkisi iyidir, ancak süreç karmaşıktır ve çözücünün geri kazanılması gerekir; gaz fazı yöntemi basittir, ancak ürünün kalitesi yeterince istikrarlı değildir ve arıtma etkisi zayıftır.
Yüzey işleme maddesi olarak kullanılan maddeler, prensip olarak, silika yüzeyindeki hidroksil gruplarıyla etkileşime girebilen aşağıdaki maddelerdir.
- Alkoller
- Klorosilanlar
- Alkoksisilan
- Heksametildisilil eter
- Silazan
(2) Silika takviye mekanizması, silika yüzey kimyası silikon kauçuk. Aşağıdaki gibi iki tür olduğuna inanılmaktadır.
Dolgu partikülleri adsorpsiyon polimeri tarafından kauçuk adsorpsiyonu, böylece kauçuk moleküler zincir segmentleri doğrudan dolgu partiküllerinin yakınına sabitlenir veya dolgu yüzeyi boyunca yönlendirilir veya dolgu agregaları tarafından tutulur.
b. Kauçuk ve dolgu partikülleri ile dolgu partikülleri ve polimer zincir segmentleri, dolgu partiküllerinin etkili çapraz bağlanmasını ve polimer dolanmasını üretmek için birleştirilmiştir.
Yukarıdaki iki etkiye dayanarak, silika silikon kauçuk üzerinde takviye edici bir etkiye sahiptir.
Silikanın asitliği ve alkaliliği üretim yöntemine bağlı olarak değişir. Füme silika asidik, çöktürülmüş silika ise alkalidir.
HCL içermeyen en saf füme silikanın pH değeri 6'dır, bu da silika yüzeyindeki hidroksil gruplarının suda ayrışarak H+ üretmesinden kaynaklanmaktadır. 4,6'nın altındaki pH değeri, yüksek sıcaklıkta hidroliz ile tutulan HCL'den kaynaklanmaktadır.
(3) Silika'nın fiziksel ve kimyasal özelliklerinin ölçüm yöntemi
Silisin fiziksel ve kimyasal özellikleri kaliteyi doğrudan yansıtır, bu nedenle kullanım için farklı gereksinimleri doğru bir şekilde ölçmek çok önemlidir. Şu anda, yabancı üreticilerin göstergeleri aynı değildir, ancak bazı önemli göstergelerin her aile tarafından ölçüldüğü kabul edilmektedir.
En önemli göstergeler, partikül boyutu ve dağılımı, spesifik yüzey alanı gibi birincil yapısını yansıtan göstergeler; yağ emme değeri vb. gibi ikincil yapısını yansıtan göstergeler; yüzeydeki çeşitli hidroksil gruplarının konsantrasyonu vb. gibi yüzey kimyasını yansıtan göstergelerdir.
Üretim koşulları ve partikül büyüme farklılıkları nedeniyle partikül boyutu ve partikül boyutu dağılımı, bu nedenle silika partikül çapı tek tip değildir, normal partikül çapı, sadece istatistiksel ortalama anlamına gelir.
Spesifik yüzey alanının belirlenmesi, toz malzemenin dış yüzey alanının büyüklüğünün bir göstergesidir, gözenekli toz malzeme için spesifik yüzey alanı, yüzey alanı ve gözeneklerin dış yüzey alanının toplamıdır.
Genel olarak, toz maddenin partikül boyutu spesifik yüzey alanı ile ters orantılıdır, bu nedenle spesifik yüzey alanının belirlenmesi tozun partikül boyutunu niteliksel olarak yansıtabilir. Elektron mikroskobu tüm endüstriyel birimlerde mevcut olmadığından, tozun partikül boyutu mevcut değildir, bu nedenle spesifik yüzey alanının belirlenmesi önemli pratik uygulama değerine sahiptir.
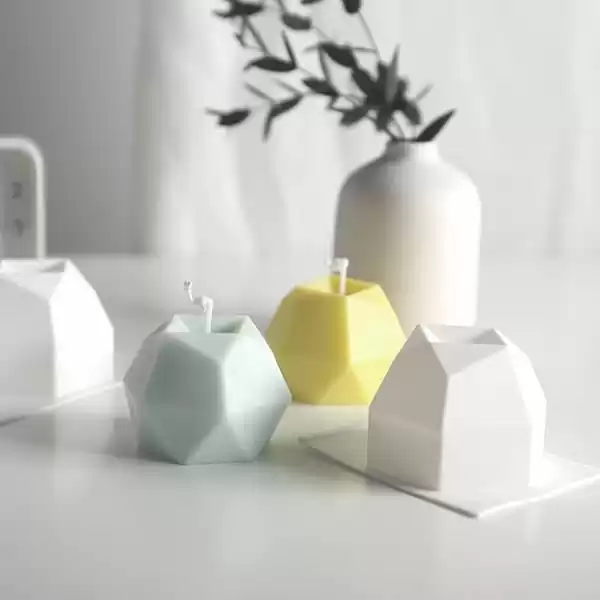
c. Yüzey hidroksil grubunun belirlenmesi Silika yüzeyinde silanol grupları vardır ve silikanın birçok uygulaması doğrudan bu gruplarla ilgilidir, bu nedenle yüzey hidroksil grubunun nicel olarak belirlenmesi çok önemlidir.
Silika yüzey hidroksil grubunun belirlenmesine yönelik veriler genellikle toplam hidroksil grubu, bitişik hidroksil grubu ve izole hidroksil grubunu içerir.
Son ikisi silika yüzeyinde Si-OH şeklinde birleşir ve topluca birleşik hidroksil grubu olarak adlandırılır; toplam hidroksil grubu, birleşik hidroksil grubu ile silika yüzeyine adsorbe edilen su moleküllerindeki hidroksil grubunun toplamıdır ve bu hidroksil grubu verileri sırasıyla farklı koşullar altında belirlenebilir. Ölçüm koşulları şunlardır.
(1) Silika torbasından doğrudan örnekleme yoluyla ölçülen hidroksil grubu toplam hidroksil miktarıdır.
(2) Silika 110°C'de 3 saat kurutularak ölçülen hidroksil grubu bağlı hidroksil grubudur.
(3) Silika 600°C'de 3 saat kurutulduktan sonra ölçülen hidroksil grubu izole edilmiş hidroksil grubudur.
(4) Birleştirilmiş hidroksil grubu ile izole edilmiş grup arasındaki fark, bitişik hidroksil grubudur.
d. Yurtdışında ikincil yapının belirlenmesi genellikle ikincil yapının derecesinin dolgu takviye davranışını doğrudan etkilediğine inanmaktadır, bu nedenle ikincil yapının belirlenmesi de çok önemlidir.
Ancak şu ana kadar iyi bir belirleme yöntemi yoktur, en yaygın kullanılan iki yöntem vardır: biri sıkıştırma altında görünür özgül hacmi belirlemek; ikincisi ise yağ emme değerini belirlemektir.
Zayıf takviye dolgu maddesi
Zayıf takviye dolgu maddesi aynı zamanda inert dolgu maddesi olarak da adlandırılabilir, silikon kauçuk üzerinde sadece küçük bir takviye etkisi vardır, genellikle tek başına kullanılmazlar. silikon kauçukancak silika rolü ile silikon kauçuğun sertliğini ayarlamak, kauçuğun proses performansını ve vulkanizasyon kauçuğunun yağ direncini ve çözünür özelliklerini iyileştirmek, kauçuk maliyetini düşürmek.
Yaygın olarak kullanılan zayıf takviye maddeleri diyatomlu toprak, kuvars tozu, çinko oksit, titanyum dioksit, zirkonyum silikat, kalsiyum karbonat vb.dir.