Giriş
Kalıp tasarımı, yüksek kaliteli silikon kauçuk ürünlerin üretilmesinde hayati bir rol oynar. Silikon kauçuğu şekillendirmek ve biçimlendirmek için kullanılan kalıplar, nihai kalitesini, işlevselliğini ve verimliliğini doğrudan etkiler; silikon kauçuk ürünler çok sayıda sektörde popülerlik kazanmaya devam ettikçe bu kalıp tasarımını optimize etmek daha da önemli hale gelmiştir.
Silikon kauçuk ürünler ısı direnci, esneklik ve dayanıklılık gibi olağanüstü özellikleri nedeniyle oldukça rağbet görmektedir. Silikon kauçuk, otomotiv, elektronik, tıbbi cihazlar ve tüketim malları üretimi gibi çok sayıda sektörde uygulama alanı bulmuştur - çok yönlülüğü ve güvenilirliği, onu yenilikçi ancak yüksek performanslı ürünler geliştirmek isteyen üreticiler için tercih edilen malzeme haline getirmektedir.
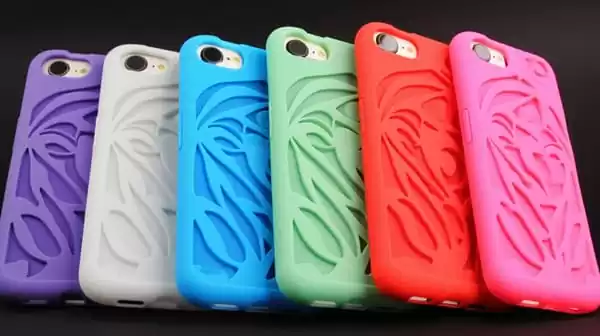
Optimize edilmiş kalıp tasarımları, verimli malzeme akışı sağladıkları, kusurları azalttıkları ve tutarlı parça kalitesi sağladıkları için üreticilerin silikon kauçuğun tüm potansiyelini ortaya çıkarmasına ve kaliteli ürünlere yönelik artan tüketici taleplerini karşılamasına yardımcı olabilir. Kalıp tasarımının optimize edilmesi yalnızca daha yüksek üretkenlik sağlamakla kalmaz, aynı zamanda pazardaki başarısına ve rekabet gücüne de katkıda bulunur.
II. Sıvı Silikon Kauçuk (LSR) Kalıplama Süreçlerini Anlamak
A. Silikon kauçuk ürünler için bir enjeksiyon kalıplama işlemi olarak LSR kalıplamanın tanımı
LSR kalıplama (veya sıvı silikon kauçuk kalıplama), aşağıdakiler için kullanılan bir sıvı enjeksiyon kalıplama işlemi tekniğidir silikon kauçuk ürünler üretmek. Bu teknik, istenen şekil ve özellikleri elde etmek için sıvı silikon kauçuğun yüksek basınç ve sıcaklık altında kalıp boşluklarına enjekte edilmesini içerir. LSR kalıplama, geleneksel enjeksiyon kalıplamaya göre yüksek hassasiyet, mükemmel parça kalitesi ve karmaşık geometriler üretme kabiliyeti gibi çeşitli avantajlar sunar.
Sürecin başlangıcı, tipik olarak iki bileşenden oluşan sıvı silikon kauçuk malzeme oluşturmayı içerir - baz silikon polimer ve katalizör / çapraz bağlayıcı - istenen malzeme özelliklerini ve kürleme özelliklerini elde etmek için hassas oranlarda karıştırılır.
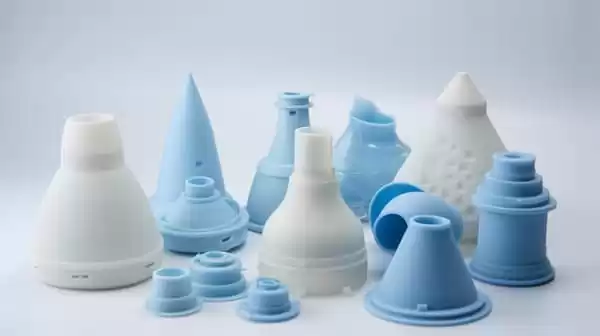
Sıvı silikon kauçuk, ısıtılmış bir varil, malzeme dağıtımı için vida veya piston mekanizması ve kalıp boşluğundan oluşan bir enjeksiyon kalıplama makinesine beslenir. Burada malzeme, yüksek basınç altında istenen kalıp şekline ve boşluğuna zorlanmadan önce ısıtılır.
Sıvı silikon kauçuk bir kalıba enjekte edildikten sonra, malzemesinin uygun şekilde kürlenmesini ve katılaşmasını teşvik etmek için ısıtma veya soğutmanın kullanılabileceği bir kürleme işleminden geçmelidir. Tamamlandığında, kalıp açılabilir ve katılaşmış silikon kauçuk kısmı ondan çıkarılabilir.
B. Enjeksiyon kalıplama makinesine genel bakış ve süreçteki rolü
Enjeksiyon kalıplama makinesi, üretimde çok önemli bir bileşendir. LSR kalıplama süreci. Sıvı silikon kauçuğun istenen ürüne enjeksiyonunu ve şekillendirilmesini kolaylaştıran birkaç temel unsurdan oluşur. İşte ana bileşenlere ve işlevlerine genel bir bakış:
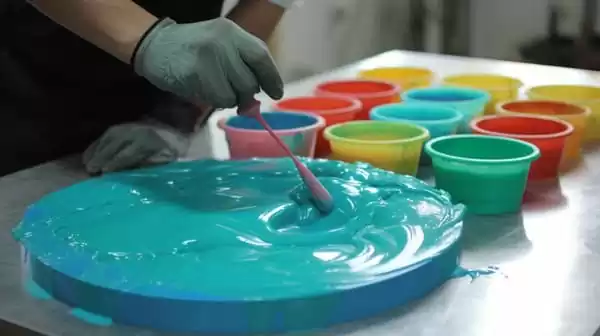
1. Namlu ve Vida/Piston Mekanizması:
Varil, sıvı silikon kauçuk malzemeyi barındırır ve kontrollü bir sıcaklığa kadar ısıtır. Vida veya piston mekanizması daha sonra malzemeyi kalıp boşluğuna enjekte etmek için ileri doğru hareket eder.
2.Kalıp Boşluğu:
Kalıp boşluğu, silikon kauçuk ürünün nihai şeklini tanımlayan kalıptaki içi boş alandır. Parçanın istenen geometrisini, özelliklerini ve boyutlarını barındıracak şekilde tasarlanmıştır.
3. Isıtma ve Soğutma Sistemleri:
Enjeksiyon kalıplama makinesi, kalıbın sıcaklığını düzenleyen ısıtma ve soğutma sistemlerini içerir. Isıtma, malzeme akışını ve kürlenmeyi kolaylaştırmak için gereklidir; soğutma ise silikon kauçuk parçanın dışarı atılmak üzere katılaşmasına yardımcı olur.
4. Sıkıştırma Ünitesi:
Sıkıştırma ünitesi, enjeksiyon işlemi sırasında kalıp yarımlarını bir arada tutarak düzgün hizalamayı sağlar ve malzeme sızıntısını önler. Enjeksiyon sırasında kalıbı kapalı tutmak ve parça çıkarma için açmak için gerekli kuvveti uygular.
Enjeksiyon kalıplama makinesi, enjeksiyon hızı, basınç, sıcaklık ve diğer proses parametreleri üzerinde hassas kontrol sağlayarak tutarlı üretim ve yüksek kaliteli silikon kauçuk ürünler.
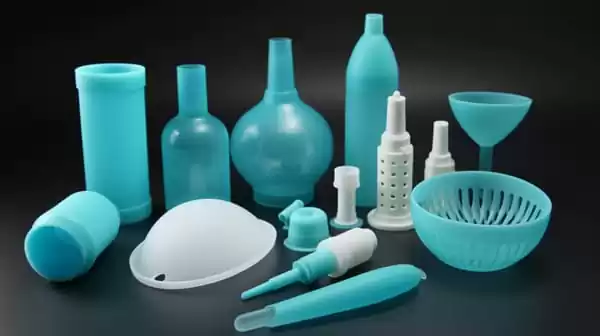
III. Kalıp Tasarımı Optimizasyonu için Temel Hususlar
A. Başarılı kalıp tasarımı için ürün gereksinimlerini anlamanın önemi
Silikon kauçuk ürünlere yönelik kalıp tasarımını optimize etmek için ürün gereksinimlerinin kapsamlı bir şekilde anlaşılması çok önemlidir. Bu, boyutlar, karmaşıklık, yüzey kalitesi ve işlevsel özellikler gibi faktörleri içerir. Üreticiler bu gereksinimleri anlayarak kalıp tasarımını özel ihtiyaçları karşılayacak şekilde uyarlayabilir ve müşteri beklentilerine uygun yüksek kaliteli silikon kauçuk ürünlerin üretilmesini sağlayabilir.
B. Kalıplanabilirlik için tasarım: karmaşık geometrilerden, keskin köşelerden ve alt kesimlerden kaçınma
Silikon kauçuk ürünlerin kalıplanabilirlik göz önünde bulundurularak tasarlanması, başarılı kalıp tasarımı optimizasyonu için esastır. Kalıptan çıkarma sırasında zorluk yaratabilecekleri ve parça kalitesini etkileyebilecekleri için karmaşık geometrilerden, keskin köşelerden ve alt kesimlerden kaçınılması tavsiye edilir. Bunun yerine, düzgün kalıptan çıkarmayı kolaylaştırmak ve kalıp boşluğu içinde uygun malzeme akışını sağlamak için yumuşak eğriler ve taslak açılar ekleyin.
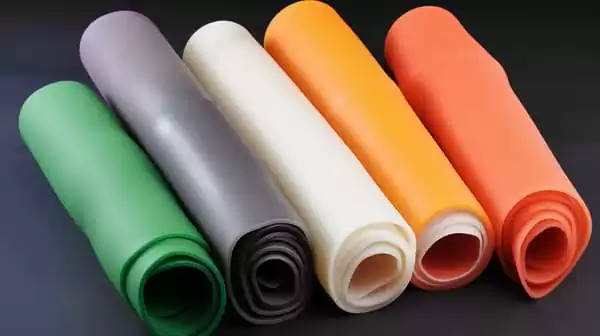
C. Duvar kalınlığı ile ilgili hususlar ve parça kalitesi ve malzeme akışı üzerindeki etkisi
Uygun et kalınlığı, optimum kalıp tasarımı elde etmek için kritik öneme sahiptir. Silikon kauçuk ürün boyunca tutarlı ve uygun bir et kalınlığının korunması, tutarlı bir kürlenme sağlar ve hava tuzakları veya malzeme akışı kısıtlamaları gibi sorunları önler. Et kalınlığındaki sapmalar, eğilme veya çökme izleri gibi kusurlar da dahil olmak üzere parça kalitesinde değişikliklere yol açabilir. Tasarım sürecinde et kalınlığının dikkatlice değerlendirilmesi, eşit parça kalitesi ve malzeme akışı elde etmek için çok önemlidir.
D. Kürleme sırasında etkili hava ve gaz tahliyesi için havalandırma ve gaz giderme teknikleri
Etkili havalandırma ve gaz giderme, silikon kauçuk ürünler için kalıp tasarımı optimizasyonunda çok önemlidir. Kalıba havalandırma delikleri eklemek, kürleme işlemi sırasında sıkışan hava veya gazların dışarı çıkmasını sağlar. Doğru havalandırma, ürünün bütünlüğünü tehlikeye atabilecek hava kabarcıkları veya boşluklar gibi kusurların oluşmasını önler. Havalandırma deliklerinin hava veya gaz sıkışmasının muhtemel olduğu alanlara dikkatlice yerleştirilmesi, verimli hava tahliyesi ve optimum kürlenme sağlar.
E. Soğutma sistemi tasarımı ve bunun çevrim süreleri ve boyutsal kararlılık üzerindeki etkisi
Etkili soğutma sistemi tasarımı, kalıp tasarımını optimize etmek ve silikon kauçuk ürün imalatında daha kısa döngü süreleri ve boyutsal stabilite elde etmek için gereklidir. Doğru soğutma, kürleme sürecini kontrol etmeye, parça büzülmesini azaltmaya ve boyutsal doğruluğu korumaya yardımcı olur. Soğutma kanallarının kalıp içine stratejik olarak yerleştirilmesi ve uygun soğutma ortamı, homojen soğutma ve verimli ısı dağılımı sağlar. İyi tasarlanmış soğutma sistemleri üretkenliği artırır, kürleme süresini en aza indirir ve tutarlı parça kalitesine katkıda bulunur.
Üreticiler, kalıp tasarımı optimizasyonu sürecinde bu temel faktörleri göz önünde bulundurarak, yüksek kaliteli silikon kauçuk ürünlerle sonuçlanan optimum kalıp tasarımları elde edebilirler. Ürün gereksinimleri, kalıplanabilirlik, duvar kalınlığı, havalandırma ve soğutma dahil olmak üzere bu hususlar, parça kalitesini, üretim verimliliğini ve müşteri memnuniyetini artırmada kritik bir rol oynar.
IV. Kalıp Tasarım Optimizasyonu için İleri Teknikler
A. Ekleme kalıplama ve ek bileşenlerin veya eklerin dahil edilmesine yönelik faydaları
Ekleme kalıplama, silikon kauçuk ürünler için kalıp tasarımı optimizasyonunda kullanılan gelişmiş bir tekniktir. Sıvı silikon kauçuğu enjekte etmeden önce kalıp boşluğuna ek bileşenler veya ekler yerleştirmeyi içerir. Ek kalıplamanın faydaları şunları içerir:
Geliştirilmiş parça işlevselliği: Ekleme kalıplama, metal ekler veya elektrik konektörleri gibi işlevsel bileşenlerin doğrudan parçaya entegre edilmesine olanak tanır silikon kauçuk ürün. Bu, ürünün performansını ve işlevselliğini artırır.
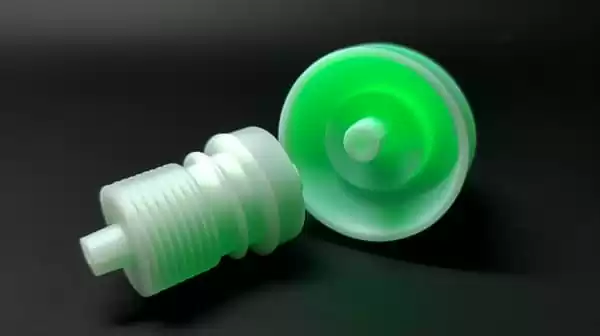
Geliştirilmiş parça mukavemeti ve stabilitesi: Ek parçaların silikon kauçuk ile güvenli bir şekilde bağlanması sayesinde, ek parça kalıplama nihai ürünün yapısal bütünlüğünü ve stabilitesini artırır. İkincil montaj işlemlerine olan ihtiyacı ortadan kaldırarak maliyetleri ve potansiyel arıza noktalarını azaltır.
Tasarım esnekliği: Ekleme kalıplama, karmaşık geometrilerin ve çok malzemeli ürünlerin oluşturulmasını sağlayan tasarım esnekliği sunar. Farklı özelliklere sahip farklı malzemelerin kombinasyonuna olanak tanıyarak silikon kauçuk ürünler için uygulama yelpazesini genişletir.
B. Gelişmiş tasarım doğruluğu için simülasyon araçlarından ve sonlu eleman analizinden (FEA) yararlanma
Simülasyon araçları ve sonlu elemanlar analizi (FEA), kalıp tasarımı optimizasyonu için güçlü araçlardır. Tasarım doğruluğunu artırmaya, malzeme akışını tahmin etmeye, potansiyel kusurları belirlemeye ve proses parametrelerini optimize etmeye yardımcı olurlar. Simülasyon araçlarını ve FEA'yı kullanarak üreticiler şunları yapabilir
Dolum modelini görselleştirin ve analiz edin: Simülasyon araçları, sıvı silikon kauçuğun kalıp boşluğu içinde nasıl aktığının görsel bir temsilini sağlar. Bu sayede hava tuzakları, yetersiz dolum veya aşırı malzeme kayması gibi akışla ilgili potansiyel sorunlar tespit edilebilir.
Geçit konumlarını ve boyutlarını optimize edin: Simülasyon araçları, enjeksiyon noktaları için en uygun kapı konumlarının ve boyutlarının belirlenmesine yardımcı olur. Bu, düzgün malzeme akışını sağlar, akışla ilgili hataları en aza indirir ve parça kalitesini artırır.
Parça büzülmesini ve çarpılmasını tahmin edin: FEA, parça büzülmesini ve çarpılmasını tahmin edebilir ve bu sorunları en aza indirmek için tasarım ayarlamalarına izin verir. Boyutsal doğruluk sağlar ve kalıplama sonrası bozulma olasılığını azaltır.
C. Alt kesimler, ayırma çizgileri ve ayırma yüzeyleri için dikkat edilecek hususlar
Silikon kauçuk ürünler için kalıp tasarımını optimize ederken, alt kesimler, ayırma çizgileri ve ayırma yüzeyleri ile ilgili hususları ele almak çok önemlidir. Bu faktörler şunları içerir:
- Alt kesimler: Alt kesimler, ürün geometrisindeki parça çıkarmayı zorlaştıran özellikler veya girintilerdir. Alt kesimleri yerleştirmek ve başarılı bir kalıptan çıkarmayı sağlamak için katlanabilir maçalar veya mekanik kızaklar gibi yenilikçi kalıp tasarım teknikleri kullanılabilir.
- Ayırma çizgileri: Ayırma çizgileri, kalıp yarılarının birleştiği ve bitmiş ürün üzerinde görünür bir çizgiyle sonuçlanan alanlardır. Ürünün kozmetik görünümü ve işlevselliği üzerindeki etkilerini en aza indirmek için ayırma çizgisi yerleşimine dikkat edilmelidir.
- Ayırma yüzeyleri: Ayırma yüzeyleri, kalıp yarımlarını ayıran kalıp yüzeylerini ifade eder. Pürüzsüz ve hassas ayırma yüzeylerinin sağlanması, uygun hizalamanın elde edilmesine yardımcı olur ve silikon kalıplama işlemi sırasında parlama oluşumunu önler.
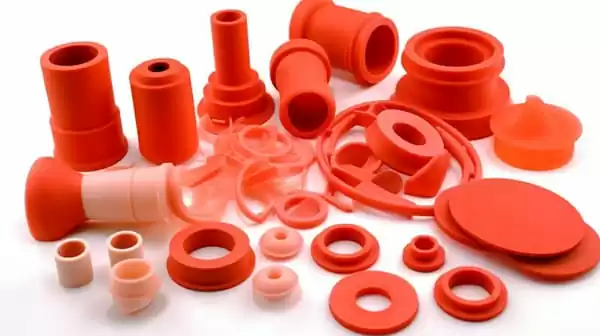
D. Tutarlı kalite için kalıp sıcaklığını, enjeksiyon basıncını ve boşluk basıncını optimize etme
Kalıp sıcaklığı, enjeksiyon basıncı ve boşluk basıncının optimize edilmesi, silikon kauçuk ürünlerde tutarlı bir kalite elde etmek için çok önemlidir. Önemli hususlar şunları içerir:
- Kalıp sıcaklığı: Kalıp sıcaklığının uygun şekilde kontrol edilmesi malzeme akışını, kürlenme süresini ve boyutsal kararlılığı etkiler. Kalıp sıcaklığının optimize edilmesi tutarlı parça kalitesi sağlar ve mekanik özelliklerdeki varyasyonları en aza indirir.
- Enjeksiyon basıncı: Enjeksiyon basıncı malzeme akışını, dolum davranışını ve kalıp özelliklerinin çoğaltılmasını etkiler. Enjeksiyon basıncının optimize edilmesi, kalıp veya parça üzerinde aşırı stres olmadan kalıp boşluğunun tamamen doldurulmasını sağlar.
- Boşluk basıncı: Kalıplama işlemi sırasında boşluk basıncının izlenmesi, tutarlı parça kalitesi ve boyutsal doğruluk sağlanmasına yardımcı olur. Enjeksiyon parametrelerinde gerçek zamanlı ayarlamalar yapılmasına olanak tanıyarak üretim sürecini optimize eder.
Üreticiler, kalıp tasarımı optimizasyonunda bu gelişmiş teknikleri uygulayarak silikon kauçuk ürünlerinin işlevselliğini, kalitesini ve verimliliğini artırabilir. Ekleme
V. Silikon Kauçuk Ürünler için LSR Kalıplamanın Avantajları
A. Geniş bir mekanik özellik yelpazesi de dahil olmak üzere LSR malzemelerinin faydaları
LSR kalıplama, öncelikle sıvı silikon kauçuk malzemelerin benzersiz özellikleri nedeniyle silikon kauçuk ürünler için çeşitli avantajlar sunar. Bu avantajlar şunları içerir:
- Geniş mekanik özellik yelpazesi: LSR malzemeleri, farklı sertlik, esneklik ve elastikiyet seviyeleri de dahil olmak üzere çok çeşitli mekanik özellikler sergileyecek şekilde formüle edilebilir. Bu, üreticilerin malzemeyi farklı endüstrilerdeki belirli ürün gereksinimlerini karşılayacak şekilde uyarlamasına olanak tanır.
- Isı direnci ve dayanıklılık: LSR malzemeleri mükemmel ısı direnci ve dayanıklılık sunarak onları yüksek sıcaklıklara, zorlu ortamlara veya sık kullanıma maruz kalmayı içeren uygulamalar için uygun hale getirir. Bütünlüklerinden ödün vermeden aşırı sıcaklıklara dayanabilirler.
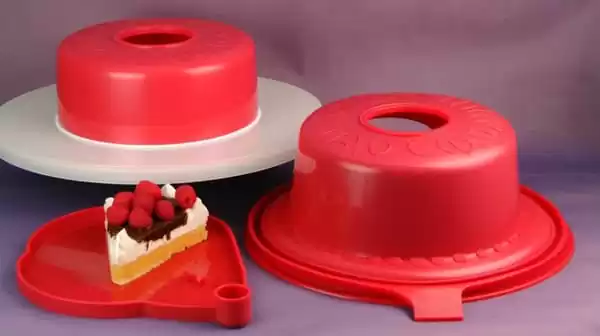
B. Geleneksel kalıplamaya kıyasla gelişmiş kozmetik görünüm ve daha pürüzsüz yüzeyler
LSR kalıplama, geleneksel kalıplama yöntemlerine kıyasla üstün kozmetik görünüm ve daha pürüzsüz yüzeyler sağlar. Bu durum, sıvı silikon kauçuğun düşük viskozitesi ve kendiliğinden yayılma özellikleri gibi benzersiz özelliklerine bağlanmaktadır. Avantajlar şunları içerir:
- Yüzey kusurlarının ortadan kaldırılması: LSR malzemeleri kalıp boşluğuna kolayca akarak homojen dağılım sağlar ve çökme izleri, akış çizgileri veya yüzey kusurları gibi yüzey kusurlarının oluşumunu en aza indirir.
- Geliştirilmiş parça estetiği: LSR kalıplama, karmaşık detayların ve ince özelliklerin yüksek hassasiyetle çoğaltılmasına olanak tanıyarak görsel olarak çekici ürünler elde edilmesini sağlar. LSR kalıplama ile elde edilen pürüzsüz yüzeyler, silikon kauçuk parçaların genel kozmetik mükemmelliğine katkıda bulunur.
C. Seri üretim kabiliyetleri ve çeşitli endüstriler için uygunluk
LSR kalıplama kitle kalıplama için son derece uygundur si̇li̇kon kauçuk ürünleri̇ üreti̇mi̇. Avantajlar şunları içerir:
- Daha kısa döngü süreleri: LSR malzemeleri hızla sertleşerek diğer kauçuk kalıplama proseslerine kıyasla daha kısa kalıplama döngü süreleri sağlar. Bu da daha fazla üretim verimliliği ve daha yüksek çıktı anlamına gelir.
- Tutarlılık ve tekrarlanabilirlik: LSR kalıplama, silikon kauçuk ürünlerin tutarlı ve tekrarlanabilir üretimini sağlayarak parça boyutlarında, özelliklerinde ve kalitesinde tekdüzelik sağlar. Bu, minimum varyasyonla yüksek hacimli üretim gerektiren endüstriler için çok önemlidir.
- Geniş uygulanabilirlik: LSR kalıplama, otomotiv, elektronik, sağlık ve tüketim malları dahil olmak üzere çeşitli sektörlerde uygulanabilir. Tıbbi bileşenlerden endüstriyel contalara, contalara ve tüketici elektroniğine kadar çeşitli ürün gereksinimlerini karşılar.
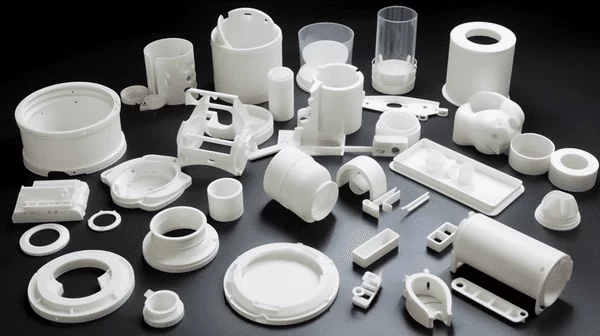
D. Uygun et kalınlığının parça bütünlüğü ve kozmetik kusurlar üzerindeki etkisi
LSR kalıplamada duvar kalınlığının optimize edilmesi, parça bütünlüğü ve kozmetik kusurlar üzerinde önemli bir etkiye sahiptir. Önemli hususlar şunları içerir:
- Yapısal bütünlük: Uygun duvar kalınlığı silikon kauçuk ürünlerin yapısal bütünlüğünü ve mukavemetini sağlar. Yetersiz malzeme dağılımı veya eşit olmayan kürlenme nedeniyle çarpılma, bozulma veya parça arızası gibi sorunları önler.
- Kozmetik kusurlar: Ürün boyunca uygun et kalınlığının korunması, yüzey farklılıkları, çukur izleri veya görünür akış çizgileri gibi kozmetik kusurların oluşumunu azaltır. Düzgün et kalınlığı, tutarlı kürleme ve malzeme akışını teşvik ederek görsel olarak çekici parçalar elde edilmesini sağlar.
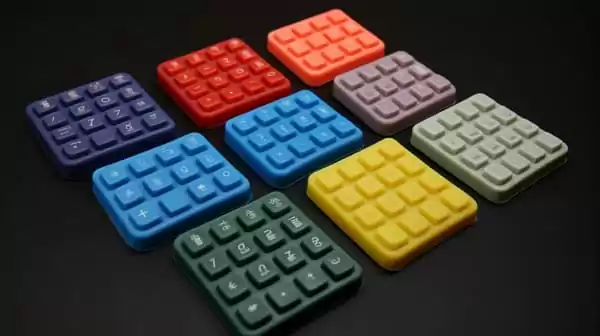
LSR kalıplamanın avantajlarından yararlanarak üreticiler şunları yapabilirler silikon kauçuk ürünler üretmek olağanüstü mekanik özelliklere, gelişmiş kozmetik görünüme ve seri üretim yeteneklerine sahiptir. Uygun duvar kalınlığı elde etme yeteneği, parça bütünlüğünü sağlar ve kozmetik kusurları en aza indirerek silikon kauçuk ürünlerin pazardaki genel başarısına ve rekabet gücüne katkıda bulunur.
Sonuç
Sonuç olarak, lsr enjeksiyon kalıplama sürecini ve tasarımını optimize etmek, yüksek kaliteli silikon kauçuk ürünler elde etmek için çok önemlidir. Üreticiler, temel stratejileri ve hususları uygulayarak sıvı silikon kauçuk (LSR) kalıplama sürecinin potansiyelini en üst düzeye çıkarabilir ve hassas, dayanıklı ve görsel olarak çekici ürünler sunabilir.
Makale boyunca, ürün gereksinimlerini anlamanın, kalıplanabilirlik için tasarım yapmanın, duvar kalınlığını dikkate almanın, havalandırma ve gaz giderme tekniklerini dahil etmenin ve soğutma sistemlerini optimize etmenin önemini tartıştık. Bu faktörler, diğerlerinin yanı sıra, silikon kauçuk ürün üretimi için optimum kalıp tasarımının elde edilmesinde kritik bir rol oynamaktadır.
Titiz kalıp tasarımı, tutarlı parça kalitesi sağlamak, kusurları en aza indirmek ve üretkenliği artırmak için gereklidir. Üreticiler alt kesimleri, ayırma çizgilerini ve ayırma yüzeylerini dikkatle değerlendirerek kalıp tasarımını optimize edebilir ve kozmetik kusurları en aza indirebilir.
LSR malzemelerin sunduğu çok çeşitli mekanik özellikler, gelişmiş kozmetik görünüm ve seri üretime uygunluk dahil olmak üzere LSR kalıplamanın avantajları, kalıp tasarımını optimize etmenin önemini daha da vurgulamaktadır. LSR kalıplama, olağanüstü performans, dayanıklılık ve estetik çekiciliğe sahip silikon kauçuk ürünlerin üretilmesini sağlar.
Özetle, üreticiler kalıp tasarımı optimizasyonuna çok dikkat ederek LSR kalıplama sürecinin tüm potansiyelini ortaya çıkarabilirler. Bu da müşteri beklentilerini karşılayan, endüstri standartlarına uygun ve pazarda rekabet avantajı sağlayan yüksek kaliteli silikon kauçuk ürünlerle sonuçlanır. Titiz kalıp tasarımıyla üreticiler, çeşitli sektörlerde geniş bir uygulama yelpazesine hitap eden hassas, dayanıklı ve görsel olarak çekici silikon kauçuk ürünler sağlayabilir.