Introducción
Estos intrincados aparatos abarcan desde los manuales hasta los totalmente automatizados, cada uno meticulosamente diseñado para cumplir con precisión y eficacia distintos requisitos industriales. La evolución de tecnología de procesos de dispensación ha introducido avances como los sistemas de control digitalizados, la dosificación meticulosa y los sofisticados circuitos de retroalimentación, que garantizan una aplicación uniforme y precisa de la silicona. Este progreso tecnológico ha aumentado las capacidades de los sistemas de dosificación, permitiéndoles gestionar diversos materiales y atender a una amplia gama de aplicaciones, desde la aplicación de capas de silicona diáfanas en aparatos electrónicos hasta la asignación de cantidades más sustanciales para el sellado de componentes de automoción.

Al profundizar en el ámbito de la asignación de silicona, es imperativo reconocer su papel fundamental no sólo en el ámbito del procedimiento, sino también en su influencia expansiva en el paisaje de la fabricación moderna. La capacidad de asignar silicona con eficacia y precisión va más allá de un mero paso en la fabricación; representa un elemento fundamental en la concepción y fabricación de productos duraderos de alto calibre que se ajustan a los estrictos criterios de las esferas industriales contemporáneas.
Proceso de dispensación de productos de silicona:
La dosificación de cola de silicona es tecnología de transformación de la silicona. De la fábrica de silicona Bezhit técnicos de silicona , nos enteramos de que el pegamento de silicona y el sistema de dispensación se divide ahora en dos métodos de dispensación de pegamento , uno es manual y el otro es automático de la máquina . La materia prima utilizada en el pegamento epoxi es material de silicona líquida, y su aplicación es algo similar a la pintura. Se trata de una tecnología de procesamiento de silicona muy interesante. La dispensación de silicona puede realizarse mediante máquina dispensadora o a mano.
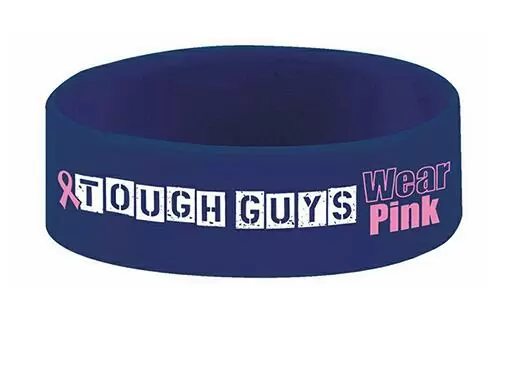
La materia prima de silicona está en estado líquido. La materia prima se coloca en la jeringa. La materia prima se deja caer sobre el molde mediante operación neumática y manual, y se calienta y vulcaniza para darle forma. Este proceso es manual y requiere mucha mano de obra, por lo que la capacidad de producción no es alta. Tiene la característica de que un producto puede ser goteado con múltiples colores según se requiera, por lo que este proceso se utiliza principalmente para hacer productos de silicona de alta gama. Por ejemplo: pulseras de silicona multicolor, fundas de silicona para botellas, bolsas de silicona de dibujos animados, fundas para carcasas,
regalos de silicona de alta gama, etc.
Introducción detallada al proceso de dosificación de cola para productos de silicona
El material utilizado en los procesos de dispensación de cola de los productos de silicona consiste en mezclar resina epoxi y agente de curado y, a continuación, dejarlo gotear sobre la superficie del botón de silicona. Después de dejarlo durante un periodo de tiempo, la resina epoxi y el agente de curado se secarán formando un efecto cristalino. De este modo, los productos de silicona no sólo adquieren belleza, sino que también se protege su superficie de posibles daños.
El proceso de fabricación de proceso de goteo de la cola de los productos de silicona es generalmente preparar primero resina epoxi de alta pureza y agente de curado en una cierta proporción, y luego ponerlos en un tanque de goteo de pegamento. Puede utilizar el tanque de goteo de pegamento para gotear una cierta cantidad de pegamento sobre la superficie del botón de silicona. ¡resina epoxi, y luego colocar el producto de silicona pegado durante unas 12 horas hasta que esté completamente fijado (se puede colocar en el horno para fijarlo completamente, lo que puede acortar el tiempo, y la temperatura del horno es de 60-70 grados), y esperar a que el producto de silicona Después de la fijación es completa, el proceso de dispensación de pegamento se ha completado!
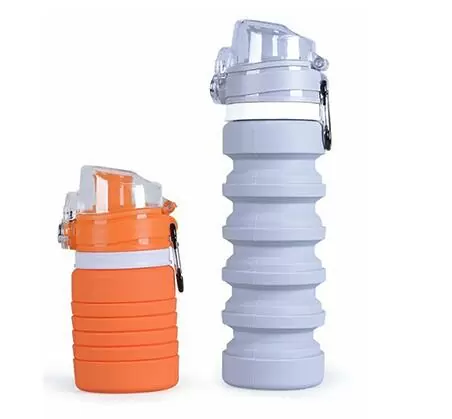
En resumen, el proceso de dosificación de cola para productos de silicona es una parte importante de la producción de productos de silicona. Puede lograr productos de silicona cristalina manteniendo un buen tacto y brillo. Sin embargo, no debe poner demasiada resina epoxi durante el proceso de aplicación de cola a los productos de silicona, y la temperatura del horno no debe ser demasiado alta. Para evitar que los productos de silicona salgan defectuosos y causar pérdidas a los fábrica de productos de silicona.
Aspectos que hay que tener en cuenta al utilizar productos de silicona con proceso de dosificación de cola
Las ventajas que aporta el proceso de aplicación de cola a los productos de silicona no son sólo la protección de la superficie del producto frente al desgaste, sino también la búsqueda de una alta calidad y un aspecto exquisito. No es difícil conseguir que un producto adquiera un aspecto dorado y translúcido. Haga lo siguiente Sólo unas pocas en punto.
1. Asegúrese de que todo el equipo esté limpio durante el proceso de dispensación de cola para evitar impurezas, ondulaciones, picaduras y otros defectos en la superficie después de que se cure la cola dispensada.
2. La proporción de cola debe pesarse con precisión y la cola debe agitarse uniformemente, ya que de lo contrario el curado de la cola será incompleto y tardará mucho tiempo en curarse.
3. La humedad del ambiente de trabajo de dispensación de cola se controla dentro de 68%. No se recomienda realizar trabajos de dispensado de cola en días lluviosos, porque cuando la humedad del aire es demasiado alta, la niebla en el aire causará directamente la oxidación de la superficie de la cola. Se recomienda utilizar la deshumidificación del aire en tareas de producción ajustadas. dispositivo.
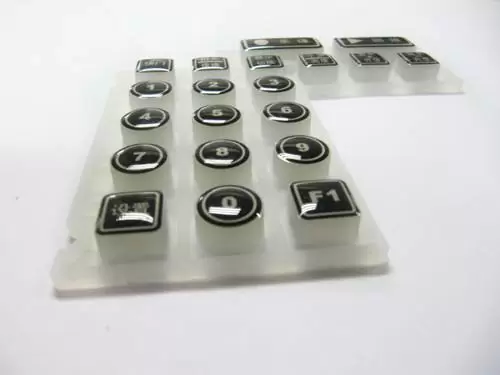
4. Los productos de silicona con estricto efecto dispensador de cola deben concentrarse en la zona a secar, y la temperatura debe controlarse entre 28-40°.
Mecánica del proceso de dispensación de silicona
Principios básicos de la dispensación:
El proceso de dosificación de silicona es un procedimiento meticuloso que exige precisión y control. En esencia, el método consiste en aplicar silicona con precisión en lugares o superficies específicos. Este proceso se rige por mecanismos de control precisos para garantizar que se dispense la cantidad correcta de silicona, respetando los patrones, el grosor y el volumen designados. La precisión de este proceso es primordial, ya que influye directamente en la calidad y el rendimiento del producto final.
Precisión en dosificación de silicona no se trata sólo de la cantidad, sino también de la colocación y la consistencia del material de silicona. Esto es especialmente crucial en aplicaciones en las que la silicona actúa como sellador o adhesivo, donde una capa uniforme e ininterrumpida es esencial para un rendimiento óptimo. En sectores de fabricación como el electrónico o el aeroespacial, donde los componentes son muy sensibles, la precisión de dosificación de silicona puede ser la diferencia entre un producto exitoso y otro defectuoso.
Tipos de sistemas de dispensación:
En la industria se emplean varios sistemas de dosificación para satisfacer distintas necesidades. Los sistemas de presión neumática son de los más comunes. Estos sistemas utilizan aire comprimido para ejercer presión sobre la silicona, empujándola a través de una boquilla dispensadora. Son muy populares por su sencillez, fiabilidad y facilidad de control, lo que los hace adecuados para una amplia gama de aplicaciones.
Sin embargo, el espectro de los sistemas de dispensación va mucho más allá de las soluciones neumáticas. Los sistemas avanzados pueden incluir dispensadores robotizados, que ofrecen alta precisión mediante controles automatizados. Estos sistemas robóticos son programables y pueden ejecutar patrones de dispensación complejos con alta repetibilidad, lo que los hace ideales para la producción a gran escala o aplicaciones que requieren diseños de dispensación intrincados.
El papel de la tecnología en estos sistemas de dispensación es integral. Los avances modernos han permitido desarrollar mecanismos de control más sofisticados. Por ejemplo, algunos sistemas incorporan ahora sensores y circuitos de retroalimentación que permiten realizar ajustes en tiempo real en el proceso de dispensación, adaptándose a factores como los cambios de viscosidad o las variaciones de temperatura. Esta integración tecnológica no sólo mejora la precisión del proceso de dosificación, sino que también aumenta su eficacia y adaptabilidad, satisfaciendo las demandas cambiantes de diversas industrias.
En conclusión, la mecánica del proceso de dosificación de silicona, respaldada por un control metódico y sistemas avanzados, es crucial para mantener los elevados estándares exigidos en la fabricación moderna. Las continuas mejoras tecnológicas de estos sistemas no solo agilizan el proceso, sino que también amplían las posibilidades de lo que puede conseguirse con la dispensación de silicona.
Componentes y materiales clave en la dispensación de silicona
Componentes sensibles y su protección:
La dosificación de silicona desempeña un papel fundamental en la protección de componentes sensibles, especialmente en la industria electrónica y en la fabricación de otros dispositivos de alta precisión. Estos componentes, a menudo susceptibles de sufrir daños por factores ambientales como la humedad, el polvo y las fluctuaciones térmicas, requieren una protección sólida para garantizar su longevidad y funcionalidad. La silicona, con sus excepcionales propiedades aislantes de sellado y revestimiento conformado, es un material ideal para este fin.
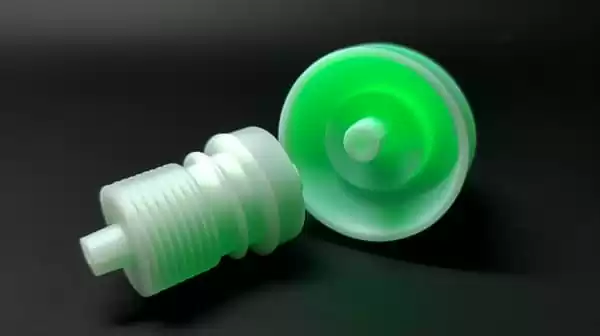
El proceso de dosificación permite aplicar silicona en patrones y grosores precisos, formando una capa protectora sobre componentes sensibles. En electrónica, por ejemplo, se utiliza una fina capa de silicona para encapsular placas de circuitos, protegiéndolas de la humedad y las interferencias eléctricas. Este encapsulado no sólo protege los componentes, sino que también mantiene su rendimiento al proporcionar estabilidad térmica y reducir el riesgo de sobrecalentamiento.
En otros dispositivos, como sensores o equipos médicos, la dosificación de silicona se utiliza para crear barreras contra contaminantes externos, garantizando al mismo tiempo que los componentes sigan siendo funcionales y receptivos. La capacidad de aplicar silicona con precisión y uniformidad es crucial en estas aplicaciones, ya que influye directamente en la eficacia y fiabilidad de la capa protectora.
Materiales y productos químicos utilizados:
El proceso de dosificación de silicona utiliza una serie de materiales, cada uno seleccionado por sus propiedades y aplicaciones específicas. Las siliconas son el material principal, valorado por su versatilidad, durabilidad y resistencia a condiciones extremas. Sin embargo, el proceso a menudo implica algo más que silicona pura. Dependiendo de la aplicación, pueden añadirse otros materiales, como resinas y cargas, para modificar las propiedades de la silicona.
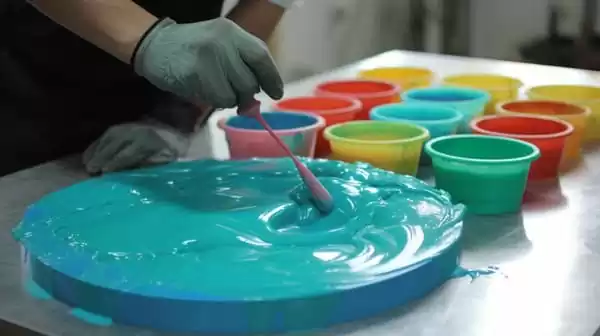
Las resinas, por ejemplo, pueden mezclarse con la silicona para mejorar sus propiedades adhesivas o alterar su viscosidad para facilitar su aplicación. Los rellenos, por su parte, se utilizan para reforzar la silicona, mejorando su resistencia y conductividad térmica. Estos aditivos desempeñan un papel importante en la adaptación de la silicona a los requisitos específicos de las distintas aplicaciones.
El proceso de curado de estos materiales es otro aspecto crítico de la dispensación de silicona. El curado se refiere al proceso químico mediante el cual la mezcla de silicona se endurece y alcanza sus propiedades finales. Este proceso puede iniciarse o acelerarse por diversos medios, como la aplicación de calor, la exposición al aire o a la humedad, o mediante catalizadores químicos. La elección del método de curado depende de factores como la velocidad deseada del proceso, las propiedades de la mezcla de silicona y las características específicas de la aplicación.
En resumen, los materiales y productos químicos utilizados en el proceso de dosificación de silicona son tan importantes como el propio proceso. La combinación adecuada de siliconas, resinas, rellenos y métodos de curado puede mejorar significativamente el rendimiento y la durabilidad del producto final, garantizando que los componentes sensibles estén adecuadamente protegidos y sean funcionales a lo largo de su vida útil.
Técnicas avanzadas y desafíos
Avances tecnológicos:
En los últimos años se han producido notables avances en la tecnología de dosificación de silicona, que han transformado la eficacia y las capacidades de este proceso. Uno de los avances clave es el perfeccionamiento de los sistemas de control. Estos sofisticados sistemas ofrecen ahora una mayor precisión en el proceso de dosificación, lo que permite patrones más intrincados y una aplicación uniforme. Esta precisión es crucial en sectores en los que incluso una pequeña desviación puede provocar fallos en el producto.
Otro avance significativo es la aparición de la tecnología de dispensación por vacío. La dosificación al vacío es especialmente eficaz para eliminar las burbujas de aire durante el proceso de dosificación, lo que resulta esencial para aplicaciones que requieren una gran pureza y uniformidad. Este método es especialmente beneficioso en la industria electrónica, donde las burbujas de aire en la silicona pueden comprometer el aislamiento y la protección de componentes sensibles.
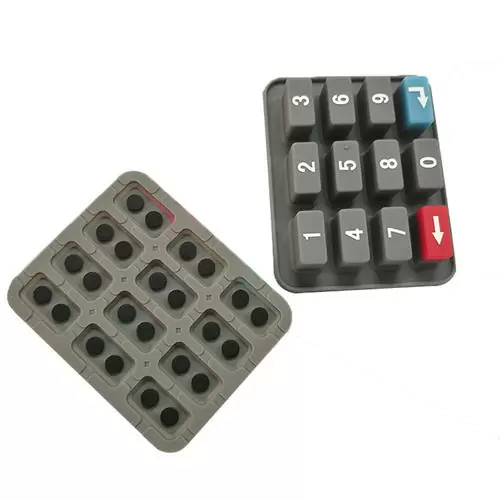
La automatización también ha desempeñado un papel importante en el avance de la tecnología de dispensación. Los sistemas automatizados de dispensación pueden integrarse ahora en las líneas de producción, lo que aumenta el rendimiento y la uniformidad, al tiempo que reduce los costes de mano de obra y los errores humanos. Estos sistemas suelen estar equipados con sensores y mecanismos de retroalimentación, lo que permite realizar ajustes en tiempo real y garantizar un alto nivel de precisión en todo el proceso de dispensación.
Afrontar los retos:
A pesar de estos avances tecnológicos, la proceso de dosificación de silicona se enfrenta a varios retos. Uno de los más frecuentes es lidiar con la viscosidad de la silicona. La viscosidad puede variar significativamente en función de la formulación y la temperatura, lo que afecta al flujo y la aplicación del material. La gestión de este problema requiere sistemas de control sofisticados que puedan ajustar los parámetros de dosificación en tiempo real para adaptarse a los cambios de viscosidad.
Las influencias relacionadas con la temperatura también plantean un reto. Las propiedades de la silicona pueden cambiar en respuesta a las variaciones de temperatura, lo que afecta a su tiempo de curado y a su adherencia. Esto es especialmente difícil en entornos con temperaturas fluctuantes o en aplicaciones en las que la silicona debe curarse rápidamente. Los sistemas de dosificación avanzados incluyen ahora mecanismos de control de la temperatura para mitigar estos problemas, garantizando una aplicación y un curado uniformes independientemente de las condiciones de temperatura externas.
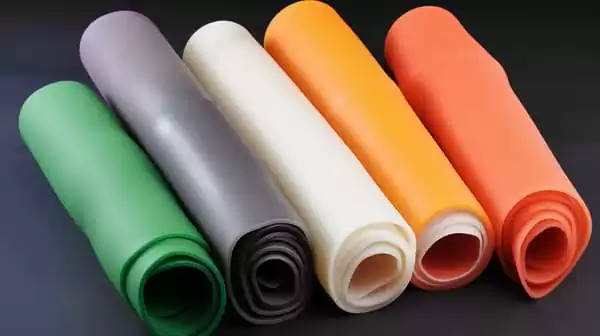
En resumen, aunque los avances en tecnología de dispensación de silicona han racionalizado y mejorado el proceso, sigue siendo crucial abordar los retos inherentes. Superarlos requiere una combinación de innovación tecnológica, control preciso y un profundo conocimiento de las propiedades de los materiales y los factores medioambientales implicados. A medida que la tecnología sigue evolucionando, se abren nuevas posibilidades para la aplicación de la silicona en diversas industrias, consolidando aún más su papel en los procesos de fabricación modernos.
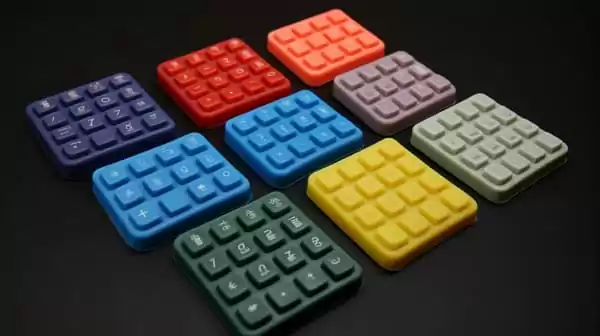
Conclusión
De cara al futuro, la proceso de dosificación de silicona está preparada para seguir evolucionando y ampliando su papel en las aplicaciones industriales. Con las continuas innovaciones tecnológicas, el potencial de los sistemas de dosificación más precisos, eficientes y versátiles es inmenso. Esta evolución abrirá probablemente nuevas aplicaciones y mejorará los procesos de fabricación existentes, reforzando la importancia de la dosificación de silicona en el panorama industrial.
A medida que las industrias sigan avanzando y exigiendo soluciones de fabricación más sofisticadas, el proceso de dosificación de silicona permanecerá sin duda a la vanguardia, adaptándose e innovando para satisfacer las necesidades siempre cambiantes de la fabricación moderna. El futuro de la dosificación de silicona promete logros aún mayores en precisión, eficacia y versatilidad, y seguirá impulsando la innovación industrial.