Introduction
La conception des empreintes de moules est la clé de voûte d'un moulage par compression réussi, car elle a le pouvoir de façonner l'avenir de nombreuses industries. Cette facette critique de la fabrication ne doit pas être sous-estimée, car elle permet d'obtenir des résultats cohérents et de haute qualité, ce qui témoigne de son importance.
Dans un monde où l'innovation et la précision règnent en maître, le moulage par compression apparaît comme un processus de fabrication polyvalent et indispensable. Avec des applications couvrant une multitude d'industries, dont l'automobile, l'électronique et les biens de consommation, il joue un rôle essentiel dans la conception des produits dont nous dépendons quotidiennement. Des composants automobiles conçus pour être performants et durables aux matériaux d'isolation électrique garantissant notre sécurité, le moulage par compression touche presque tous les aspects de notre vie.
Au fur et à mesure que nous nous enfonçons dans le domaine des conception des empreintes de moules pour le moulage par compressionDans ce numéro, nous nous embarquons pour un voyage qui dévoile la tapisserie complexe de ce processus. En explorant ses nuances, nous découvrirons comment la bonne conception des empreintes de moules peut ouvrir un monde de possibilités, en créant des produits qui non seulement répondent à nos attentes, mais les dépassent souvent. Rejoignez-nous dans cette exploration de l'art et de la science du moulage par compression, où la conception des empreintes de moules est la boussole qui nous guide vers le summum de l'excellence en matière de fabrication.
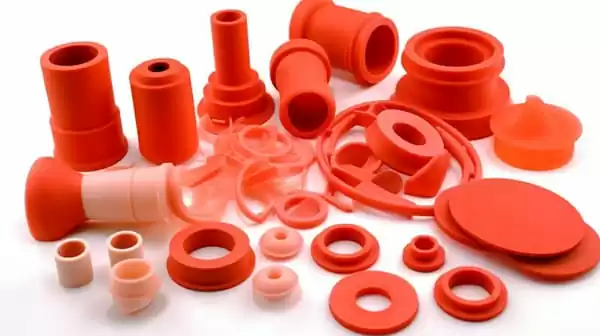
Comprendre les processus de moulage par compression
Le moulage par compression est un procédé de fabrication polyvalent et largement utilisé dans de nombreux secteurs d'activité. Pour saisir l'essence de cette technique, il est essentiel de la décomposer en ses principaux éléments.
1. Le processus de moulage par compression :
En son cœur, moulage par compression est un processus qui consiste à façonner des matériaux à l'aide de la chaleur et de la pression. Les étapes sont les suivantes :
Préparation des matériaux : Le processus commence par la préparation des matières premières, généralement sous forme de granulés, de pastilles ou de composés de moulage en feuilles (SMC).
Chauffage : Le moule, souvent composé de deux moitiés, est fermé autour du matériau. La chaleur est ensuite appliquée pour ramollir ou faire fondre le matériau, ce qui le rend souple.
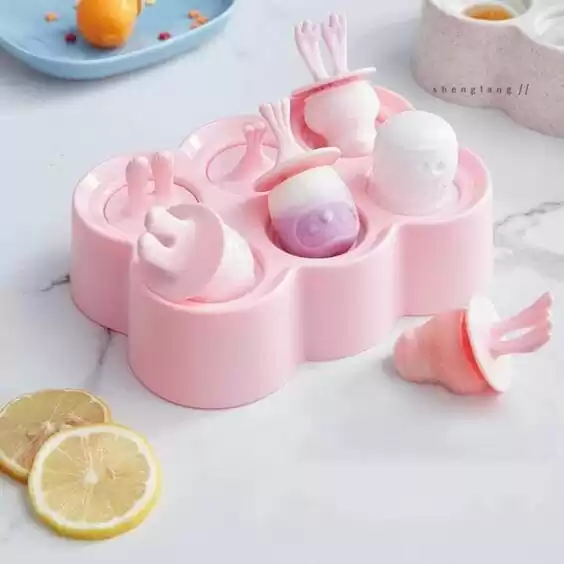
Compression : Une pression est appliquée à la cavité du moule, comprimant le matériau et lui donnant la forme souhaitée pour le produit final.
Refroidissement : Une fois que le matériau a pris la forme du moule, il est refroidi pour se solidifier et le moule chauffé durcit, ce qui permet de conserver la forme souhaitée.
Éjection : Enfin, la pièce moulée est éjectée de la cavité du moule, prête à être transformée ou utilisée.
2. Conception de moules de compression :
La base d'une opération de moulage par compression réussie réside dans la conception de la cavité du moule. Conception du moule de compression englobe plusieurs éléments cruciaux :
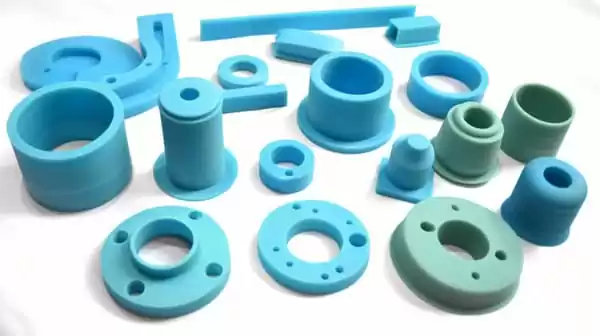
Géométrie : La géométrie de l'empreinte doit correspondre précisément à la forme prévue du produit final. Cela inclut des considérations telles que l'épaisseur de la pièce, les angles de dépouille et les contre-dépouilles, afin d'assurer une éjection en douceur.
Ventilation : Une ventilation efficace est essentielle pour permettre à l'air et aux gaz piégés de s'échapper pendant le moulage. Une bonne ventilation permet d'éviter les défauts tels que les poches d'air ou les vides dans le produit final.
Ligne de séparation : Le plan de joint désigne l'endroit où le moule se sépare pour libérer la pièce moulée. Il doit être bien défini et ne pas nuire à l'esthétique et à la fonctionnalité du produit.
Conception de l'opercule : L'opercule est le point par lequel la matière en fusion pénètre dans la cavité du moule. Une conception minutieuse de l'opercule garantit un remplissage uniforme et minimise les défauts. Les types de portillons comprennent les portillons de bord, les portillons à broches et les portillons à tunnel.
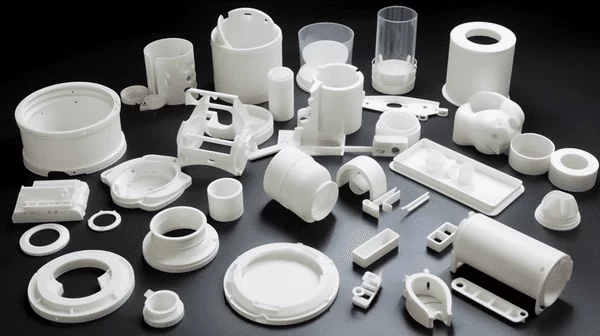
Système de refroidissement : Des canaux de refroidissement efficaces à l'intérieur du moule permettent de solidifier rapidement la pièce moulée, d'éviter les déformations et d'améliorer les temps de cycle.
Finition de la surface : En fonction des exigences du produit, la surface de l'empreinte peut être polie, texturée ou revêtue pour améliorer l'esthétique du produit final.
3. Matériaux utilisés dans le moulage par compression :
Le moulage par compression est compatible avec une large gamme de matériaux, y compris les matériaux thermodurcis tels que la résine époxy, le caoutchouc silicone et les résines polymères. Il excelle particulièrement avec les matériaux en résine renforcés de fibres, tels que les composites à base de fibres de verre ou de carbone. Ces matériaux offrent d'excellentes performances mécaniques, une résistance à la température et une résistance chimique.
4. Avantages et inconvénients du moulage par compression :
Avantages :
Rentable : Le moulage par compression utilise souvent des matériaux thermoplastiques recyclés et des matériaux dont le point de fusion est relativement bas, ce qui réduit les coûts de production.
Large gamme de températures : Il peut créer des moules pour des pièces présentant de larges plages de température et des exigences élevées en matière de résistance chimique.
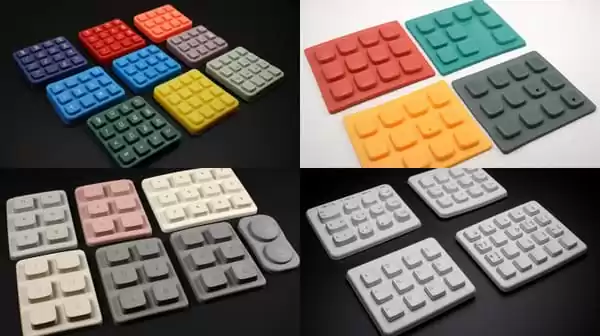
Matériaux composites : Idéal pour travailler avec des matériaux composites tels que les fibres de verre et les fibres de carbone, ce qui permet de produire des composants légers et très résistants.
Inconvénients :
Géométries complexes : Peut ne pas convenir à la production de composants présentant des géométries extrêmement complexes ou des tolérances serrées.
Processus plus lent : Le moulage par compression peut être plus lent que d'autres procédés de moulage tels que le moulage par injection, ce qui peut avoir un impact sur les taux de production.
Essentiellement, comprendre le processus de moulage par compression, le rôle de la conception des moules de compression, la polyvalence des matériaux utilisés, ainsi que les avantages et les inconvénients de cette méthode, c'est poser les bases de l'exploitation de son potentiel dans diverses industries. Il s'agit d'un processus qui allie précision, créativité et ingénierie pour transformer des matières premières en produits qui font fonctionner notre monde.
Section 2 : Types de moulage par compression
Dans le domaine du moulage par compression, les types de moules jouent un rôle essentiel dans la détermination du résultat du processus. Le choix du moule peut avoir un impact significatif sur la qualité, la complexité et l'efficacité de la production. Examinons les trois principaux types de moules pour le moulage par compression et découvrons leurs caractéristiques et leurs applications :
1. Moule à ciel ouvert :
Caractéristiques :
Gestion des flashs : La caractéristique principale des moules à flasque ouvert est qu'ils permettent à l'excédent de matière, appelé "flash", de s'échapper au cours du processus de moulage par compression. Cette bavure est ensuite éliminée, laissant derrière elle le produit désiré.
Applications :
Pièces de faible précision : Les moules à fente ouverte sont couramment utilisés lorsque la précision n'est pas une exigence critique. Ils conviennent parfaitement à la production de pièces pour lesquelles une grande précision dimensionnelle n'est pas nécessaire.
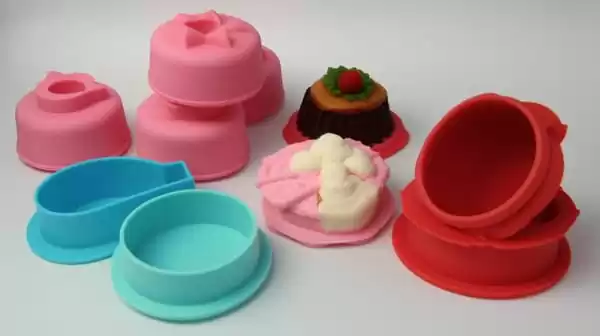
2. Moule fermé :
Caractéristiques :
Précision : Les moules fermés sont conçus pour maintenir un haut degré de précision tout au long du processus de moulage par compression. Ils sont conçus pour minimiser les bavures et garantir des tolérances serrées dans le produit final.
Applications :
Précision critique : Les moules fermés trouvent leur place dans les applications où la précision est primordiale. Ils sont utilisés dans des scénarios où la cohérence du produit et le respect de tolérances serrées ne sont pas négociables.
3. Moule semi-fermé :
Caractéristiques :
Approche hybride : Les moules semi-fermés combinent des éléments des moules ouverts et fermés. S'ils permettent à la vapeur de s'échapper, ils permettent également de contrôler les dimensions des pièces.
Applications :
Exigences équilibrées : Les moules semi-fermés sont choisis lorsqu'une précision modérée est nécessaire et que la gestion du flash est essentielle, mais pas aussi critique que dans les moules fermés. Ils offrent une approche équilibrée qui répond à un large éventail d'exigences en matière de produits.
En fait, le choix entre les moules ouverts, fermés et semi-fermés dans le domaine du moulage par compression dépend des exigences spécifiques du produit fabriqué. Les moules à fente ouverte conviennent lorsque la précision n'est pas la priorité absolue, les moules fermés excellent dans les applications exigeant une précision extrême, et les moules semi-fermés atteignent un équilibre entre ces deux extrêmes. En choisissant le type de moule approprié, les fabricants peuvent optimiser leurs processus de moulage par compression pour répondre aux besoins uniques de leurs produits et de leurs industries.
Section 3 : Types de matériaux pour le moulage par compression
Dans le monde du moulage par compression, le choix des matériaux pour les produits moulés par compression est essentiel pour déterminer les propriétés et les caractéristiques du produit final. Deux matériaux couramment utilisés dans ce processus sont le composé de moulage en feuille (SMC) et le composé de moulage en vrac (BMC). Examinons ces matériaux et mettons en lumière les avantages de l'utilisation de matériaux thermodurcissables dans le moulage par compression :
1. Composé de moulage en feuille (SMC) :
Caractéristiques :
Renforcé par des fibres : Le SMC est un matériau renforcé par des fibres qui combine des résines thermodurcissables avec des fibres de verre hachées. Ce renforcement confère au matériau une résistance et une rigidité excellentes.
Forme de la feuille : Le SMC est généralement fourni sous forme de feuilles plates ou de rouleaux. Ces feuilles sont pré-imprégnées de résine et peuvent être facilement découpées et superposées dans la cavité du moule.
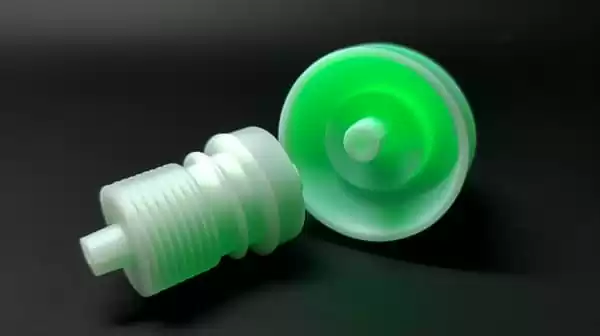
Applications :
Composants automobiles : Le SMC est largement utilisé dans l'industrie automobile pour fabriquer des composants tels que des panneaux de carrosserie, des capots et des garnitures extérieures en raison de sa grande solidité, de sa résistance aux chocs et de sa résistance à la corrosion.
Enveloppes électriques : Ses propriétés d'isolation électrique font du SMC un choix privilégié pour les boîtiers et les panneaux électriques.
2. Composé de moulage en vrac (BMC) :
Caractéristiques :
Matériau thermodurcissable : Le BMC est également un matériau thermodurcissable, composé d'un mélange de résine thermodurcissable, de matériaux de remplissage et de fibres de renforcement (généralement du verre).
Forme granulaire : Contrairement au SMC, le BMC est fourni sous forme de granulés. Cette consistance granulaire permet de mouler avec précision des formes complexes.
Applications :
Industrie automobile : Le BMC trouve sa place dans l'industrie automobile pour la production de composants complexes tels que les couvercles de soupapes, les collecteurs d'admission et les pièces sous le capot. Sa stabilité dimensionnelle et sa résistance aux produits chimiques et à la chaleur en font un choix idéal.
Électricité et électronique : Le BMC est utilisé dans les applications électriques et électroniques en raison de ses excellentes propriétés d'isolation électrique et de résistance à la flamme.
Avantages de l'utilisation de matériaux thermodurcissables dans le moulage par compression :
Le choix de matériaux thermodurcissables, tels que ceux utilisés dans le SMC et le BMC, offre plusieurs avantages dans le processus de moulage par compression :
Résistance à la température : Les matériaux thermodurcissables excellent dans les environnements à haute température. Ils peuvent supporter des températures élevées sans se déformer, ce qui les rend adaptés aux applications qui nécessitent une résistance à la chaleur et aux cycles thermiques.
Résistance chimique : Ces matériaux présentent une excellente résistance aux produits chimiques, ce qui les rend idéaux pour les applications où l'on s'attend à une exposition à divers produits chimiques.
Stabilité dimensionnelle : Les matériaux thermodurcissables conservent leur forme et leurs dimensions sous pression et à haute température, ce qui garantit l'uniformité et la précision du produit final.
Isolation électrique : Le SMC et le BMC possèdent tous deux d'excellentes propriétés d'isolation électrique, ce qui les rend indispensables dans les applications électriques et électroniques.
Formes complexes : La forme granulaire du BMC et la capacité de stratification du SMC permettent de mouler des formes complexes, offrant ainsi une grande souplesse de conception.
En résumé, les composés de moulage en feuilles (SMC) et les composés de moulage en vrac (BMC) sont des exemples de matériaux thermodurcissables utilisés dans le moulage par compression. Leurs avantages inhérents, notamment la résistance à la température et aux produits chimiques, la stabilité dimensionnelle et les propriétés d'isolation électrique, en font des choix précieux pour la fabrication de divers produits dans toutes les industries. L'utilisation de ces matériaux, combinée à la précision du moulage par compression, permet de réduire les coûts de production. moulage par compressionL'utilisation de la technologie de l'information et de la communication (TIC) permet d'obtenir des composants de haute qualité avec des caractéristiques et des performances sur mesure.
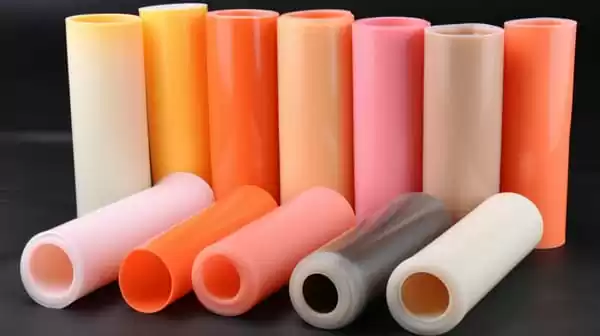
Section 4 : Le processus de moulage par compression lui-même
Pour bien saisir les subtilités du moulage par compression, il est essentiel de se plonger au cœur du processus lui-même. Dans cette section, nous allons explorer les composants essentiels du moule de compression, comprendre la signification de sa nature à haute pression et démêler le processus de durcissement responsable de la solidification de la pièce moulée :
1. Composants du moule de compression :
Le moule de compression est au cœur du processus de moulage par compression. Il se compose de plusieurs éléments essentiels :
Cavité du moule : C'est là que la magie opère. L'empreinte du moule définit la forme et les dimensions du produit final. Elle doit être méticuleusement conçue pour s'adapter à la géométrie souhaitée, en tenant compte de facteurs tels que l'épaisseur de la pièce, les angles de dépouille et la finition de la surface.
Système de chauffage : Les moules à compression sont équipés d'un système de chauffage qui augmente la température à l'intérieur de la cavité du moule. Ce chauffage est essentiel pour ramollir ou faire fondre la matière première afin de la rendre souple et apte au moulage.
Système de refroidissement : Des canaux ou systèmes de refroidissement efficaces traversent le moule pour refroidir et solidifier rapidement la pièce moulée une fois qu'elle a pris forme. Un refroidissement adéquat permet de conserver la forme souhaitée et d'éviter les déformations ou les distorsions.
Mécanisme de pression : Le moulage par compression est connu pour sa nature à haute pression. Le moule intègre un mécanisme permettant d'appliquer une pression importante dans la cavité du moule. Cette pression permet de compacter le matériau, de s'assurer qu'il remplit tous les coins et recoins du moule et, en fin de compte, de définir la densité et l'intégrité structurelle de la pièce.
2. La nature haute pression du moulage par compression :
Le moulage par compression se caractérise par sa haute pression inhérente, qui joue un rôle essentiel dans la formation du produit final. L'importance de cet environnement à haute pression réside dans plusieurs aspects :
Compression du matériau : La pression élevée appliquée pendant le moulage par compression comprime le matériau dans la cavité du moule. Cette compression garantit que le matériau se conforme précisément à la géométrie du moule, ce qui permet d'obtenir une excellente reproduction des pièces et une grande précision dimensionnelle.
Contrôle de la densité : La pression détermine la densité du produit final. En contrôlant soigneusement la pression, les fabricants peuvent obtenir des densités de matériaux spécifiques, qui influencent les propriétés mécaniques et les performances de la pièce.
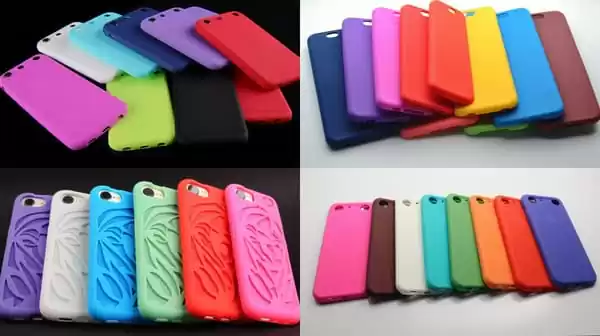
Remplissage uniforme : La haute pression permet de remplir uniformément la cavité du moule. Cela minimise le risque de vides, de poches d'air ou d'autres défauts dans le produit final, contribuant ainsi à sa qualité.
3. Le processus de maturation :
Une fois que le matériau a pris la forme souhaitée dans la cavité du moule, le processus de durcissement entre en jeu. Le durcissement est l'étape qui permet de solidifier la pièce moulée et de lui donner son intégrité structurelle finale. Voici comment cela fonctionne :
Chaleur et pression : La température élevée à l'intérieur du moule, associée à la pression appliquée, déclenche une réaction chimique dans le matériau thermodurcissable. Cette réaction entraîne le durcissement du matériau et sa mise en forme.
Refroidissement : Une fois le processus de durcissement terminé, le système de refroidissement du moule est activé pour réduire rapidement la température. Cette phase de refroidissement permet de solidifier la pièce, la rendant rigide et prête à être éjectée du moule.
En conclusion, la compréhension des composants du moule de compression, de l'importance de l'environnement à haute pression et du processus de durcissement fournit des informations précieuses sur la mécanique du moulage par compression. Cette interaction complexe de la chaleur, de la pression et de la mécanique de précision permet la production de des composants de haute qualité avec la forme, la densité et les propriétés mécaniques souhaitées. C'est l'incarnation de l'excellence en matière de fabrication, avec des produits qui répondent aux normes les plus strictes en matière de performance et de fiabilité.
Section 5 : Conception de l'empreinte du moule
L'empreinte est au cœur même du processus de moulage par compression. Dans cette section, nous explorerons le rôle critique de la conception de l'empreinte, nous définirons la conception du moule de compression et nous nous pencherons sur le calcul du tonnage, un facteur crucial dans le moulage par compression :
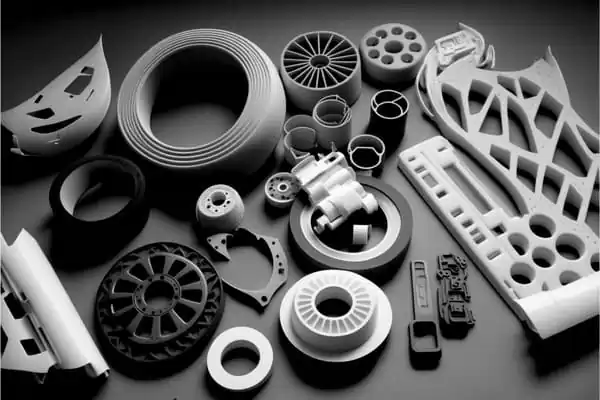
1. L'importance de la conception de l'empreinte du moule :
La conception de la cavité du moule est primordiale pour garantir le succès du processus de moulage par compression. Voici pourquoi elle revêt une telle importance :
Précision et cohérence : La cavité du moule définit la forme et les dimensions finales du produit. Une cavité bien conçue garantit la précision et l'uniformité de chaque pièce moulée, répondant ainsi aux normes de qualité les plus élevées.
Flux de matériaux : La géométrie de l'empreinte détermine la manière dont le matériau s'écoule et remplit le moule. Une mauvaise conception peut entraîner une distribution inégale du matériau, ce qui se traduit par des défauts ou des incohérences dans le produit final.
Ventilation et refroidissement : Des canaux de ventilation efficaces ou des rainures dans la cavité du moule permettent à l'air et aux gaz piégés de s'échapper, évitant ainsi les défauts tels que les poches d'air. Le système de refroidissement à l'intérieur de la cavité permet de solidifier rapidement la pièce, ce qui réduit les temps de cycle.
Finition de la surface : La conception de l'empreinte du moule joue également un rôle dans l'obtention de l'état de surface souhaité pour la pièce moulée. Celle-ci peut être polie, texturée ou revêtue pour répondre à des exigences esthétiques et fonctionnelles spécifiques.
2. Qu'est-ce que la conception d'un moule de compression ?
Conception du moule de compression est le processus de création méticuleuse d'une cavité de moule capable de résister aux pressions et températures élevées inhérentes au moulage par compression. Il englobe plusieurs aspects critiques :
Géométrie : La cavité du moule doit correspondre précisément à la forme prévue du produit final. Il faut donc tenir compte de l'épaisseur de la pièce, des angles de dépouille et des contre-dépouilles pour une éjection en douceur.
Ventilation : Des canaux ou des rainures d'aération appropriés permettent à l'air et aux gaz piégés de s'échapper pendant le moulage, évitant ainsi les défauts tels que les poches d'air ou les vides dans le produit final.
Ligne d'arrêt : Le plan de joint désigne l'endroit où le moule se sépare pour libérer la pièce moulée. Il doit être bien défini et ne pas nuire à l'esthétique et à la fonctionnalité du produit.
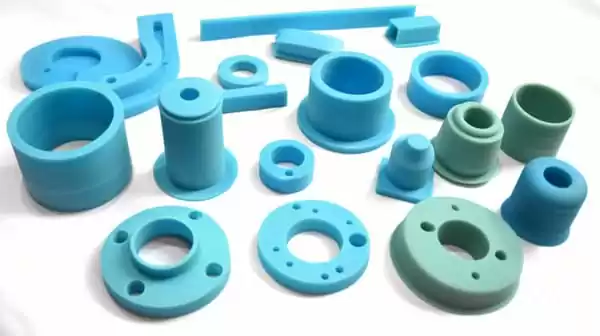
Conception de la porte : L'opercule est le point par lequel la matière en fusion pénètre dans la cavité du moule. Une conception minutieuse de l'opercule garantit un remplissage uniforme et minimise les défauts. Les types de portillons comprennent les portillons de bord, les portillons à broches et les portillons à tunnel.
Système de refroidissement : Des canaux de refroidissement efficaces à l'intérieur du moule permettent de solidifier rapidement la pièce moulée, d'éviter les déformations et d'améliorer les temps de cycle.
Finition de la surface : En fonction des exigences du produit, la surface de l'empreinte peut être polie, texturée ou revêtue pour améliorer l'esthétique du produit final.
3. Comment calculer le tonnage pour le moulage par compression :
Tonnage en moulage par compression désigne la force nécessaire pour comprimer le matériau dans la cavité du moule. Il s'agit d'un facteur crucial pour obtenir une bonne compression du matériau et une bonne densité des pièces. Pour calculer le tonnage, vous pouvez utiliser la formule suivante :
Tonnage = Pression × Surface
Pression : La pression est généralement mesurée en PSI (Pounds per Square Inch).
Zone : La surface représente la surface projetée de la pièce à mouler.
En calculant le tonnage requis, les fabricants peuvent s'assurer que la presse utilisée dans le processus de moulage par compression exerce la force nécessaire pour obtenir la compression et la densité souhaitées du matériau dans la cavité du moule.
Par essence, la conception de l'empreinte du moule est la pierre angulaire d'un moulage par compression réussi. Elle détermine la qualité, la précision et la cohérence du produit. La conception des moules de compression englobe la géométrie, les évents, les plans de joint, la conception des portes, les systèmes de refroidissement et la finition de la surface, tous adaptés pour répondre aux exigences spécifiques de la pièce souhaitée. Comprendre et calculer le tonnage permet de s'assurer que le processus de moulage par compression fonctionne de manière optimale, produisant des composants de haute qualité qui respectent ou dépassent les normes industrielles.
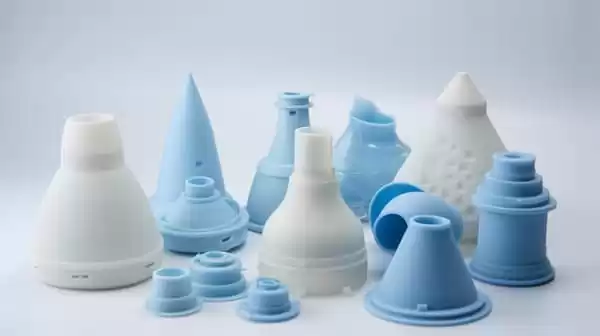
Conclusion
Dans cette exploration complète du moulage par compression et de la conception des empreintes de moules, nous avons découvert le monde complexe d'un processus de fabrication qui laisse une marque indélébile sur une multitude d'industries.
Au terme de notre exploration, nous encourageons les lecteurs à envisager le moulage par compression pour leurs besoins de fabrication. Sa précision, sa polyvalence et sa capacité à produire des composants de haute qualité en font un procédé qui mérite d'être exploré pour un large éventail d'applications. En adoptant le moulage par compression et en exploitant la puissance d'une conception adéquate de l'empreinte du moule, les fabricants peuvent ouvrir un monde de possibilités, en créant des produits qui non seulement répondent aux normes d'excellence les plus élevées en matière de fabrication, mais qui les dépassent.