La structure des moules d'injection de caoutchouc silicone liquide (LSR) thermodurcissable est généralement similaire à celle des moules utilisés pour les composés thermoplastiques, mais il existe plusieurs différences significatives.
Par exemple, les composés LSR ont généralement une faible viscosité et donc des temps de remplissage très courts, même à des pressions d'injection très faibles. Pour éviter l'emprisonnement de l'air, il est essentiel de disposer d'un bon dispositif d'évacuation de l'air dans le moule.
En outre, les composés LSR ne se rétractent pas autant que les composés thermoplastiques dans le moule ; ils ont tendance à se dilater à chaud et à se rétracter légèrement à froid. Par conséquent, le produit ne reste pas toujours sur le côté convexe du moule comme prévu, mais il est retenu dans la cavité avec une plus grande surface.
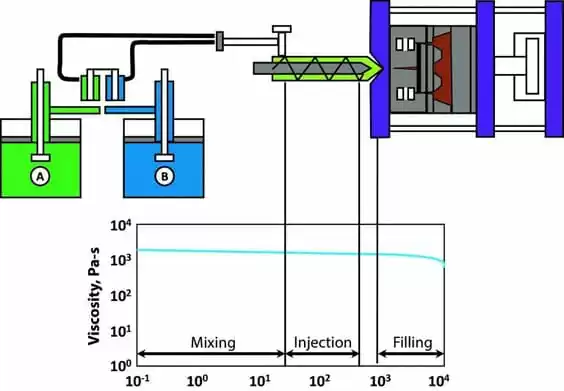
1. Rétrécissement
Bien que les LSR ne se rétractent pas dans le moule, ils se rétractent souvent de 2,51 TTP3T à 31 TTP3T après le démoulage et le refroidissement. L'ampleur exacte du retrait dépend dans une certaine mesure de la formulation de ce composé.
Toutefois, du point de vue du moule, le retrait peut être influencé par plusieurs facteurs, notamment la température du moule, la température du composé lorsqu'il est démoulé, ainsi que la pression dans la cavité du moule et la compression ultérieure du composé.
L'emplacement du point d'injection mérite également d'être pris en compte, car le retrait dans la direction du flux de colle est généralement plus important que le retrait dans la direction perpendiculaire au flux de colle.
La taille du produit influe également sur son retrait, les produits plus épais ayant généralement un retrait moins important que les produits plus fins. Si une vulcanisation secondaire est nécessaire, le retrait peut être de 0,5%-0,7% supplémentaires.
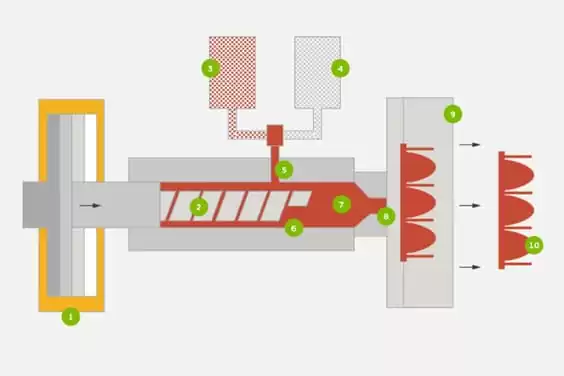
2. Ligne de séparation
La détermination de l'emplacement du plan de joint est l'une des premières étapes de la conception d'un produit. moule d'injection en caoutchouc de silicone. L'aération est réalisée principalement à l'aide de rainures situées sur le plan de joint, qui doit se trouver dans la zone où le composé d'injection va durer. Cela permet d'éviter les bulles d'air internes et de réduire la perte de résistance au niveau du joint de colle.
En raison de la faible viscosité des LSR, le plan de joint doit être précis pour éviter les débordements. Malgré cela, les plans de joint sont souvent visibles sur les produits façonnés. Le démoulage est influencé par la géométrie de la pièce et la position du plan de joint. Concevoir la pièce avec un léger chanfrein permet d'assurer une affinité constante avec l'autre moitié du produit. moule d'injection cavité.
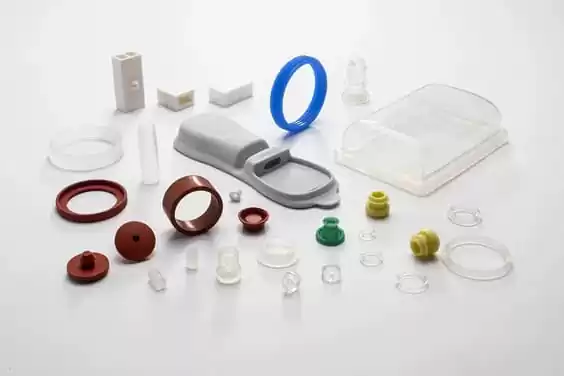
3. Mise à l'air libre
Lorsque le LSR est injecté, l'air emprisonné dans la cavité est comprimé lors de la fermeture du moule, puis expulsé par les rainures d'aération lors du remplissage du moule.
Si l'air n'est pas complètement évacué, il sera piégé dans l'adhésif (ce qui se traduit souvent par des bords blancs sur une partie du produit). Les rainures d'aération ont généralement une largeur de mm à 3 mm et une profondeur de 0,004 mm à 0,005 mm.
Le meilleur effet de mise à l'air libre peut être créé par la mise sous vide à l'intérieur du moule. Pour ce faire, on conçoit un joint sur le plan de joint et on vide rapidement toutes les cavités à l'aide d'une pompe à vide. Une fois que le vide a atteint le niveau nominal, le moule est complètement fermé et la presse à injection commence.
Certains équipements de moulage par injection permettent de travailler avec des forces de fermeture variables, ce qui permet au transformateur de fermer le moule à basse pression jusqu'à ce que 90-95% de la cavité soit remplie de LSR (ce qui facilite l'évacuation de l'air), puis de passer à une force de fermeture plus élevée afin d'éviter que les LSR ne s'infiltrent dans la cavité. caoutchouc de silicone l'expansion et le débordement.
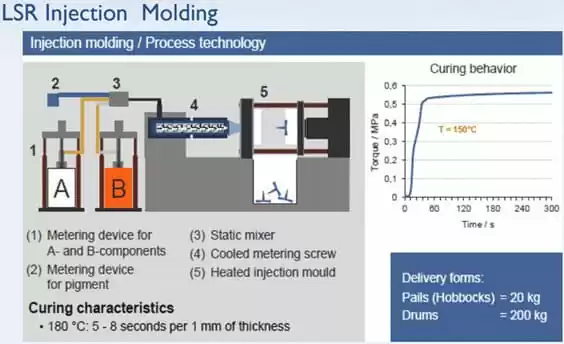
4. Point d'injection
Un système de canaux froids est utilisé pour le moulage des LSR. Les avantages de ce système sont les suivants caoutchouc de silicone peut être maximisée et l'efficacité de la production peut être augmentée au maximum.
En traitant les produits de cette manière, il n'est pas nécessaire d'enlever le canal d'injection, ce qui évite une augmentation de la main-d'œuvre pour l'opération et parfois une grande quantité de déchets de matériaux. Dans de nombreux cas, la construction sans couloir permet également de réduire le temps d'exploitation.
La buse d'injection est contrôlée par une vanne à pointeau pour un débit positif, et de nombreux fabricants proposent désormais des buses avec des interrupteurs pneumatiques en tant qu'équipement standard, qui peuvent être installés dans différentes parties du moule.
Certains moule d'injection makers ont mis au point un système ouvert de canaux froids si petit que plusieurs points d'injection (et donc la totalité de la cavité) doivent être placés dans un espace de moule très limité.
Cette technologie permet de produire de grandes quantités de produits de haute qualité. produits en caoutchouc de silicone sans devoir séparer les orifices d'injection.
Si un système de canaux froids est utilisé, il est important de créer une séparation de température efficace entre la cavité chaude et le canal froid. Si le canal est trop chaud, le caoutchouc peut commencer à se vulcaniser avant d'être injecté. Mais s'il refroidit trop rapidement, il absorbera trop de chaleur provenant de la zone de la carotte de l'injecteur. moule d'injectionce qui entraîne une vulcanisation incomplète.
Pour les produits injectés avec une carotte conventionnelle (par exemple, carotte immergée et carotte conique), il convient d'utiliser un orifice d'injection de petit diamètre (généralement 0,2 mm-0,5 mm) pour l'injection.
Avec les composés LSR à faible viscosité, comme avec les composés thermoplastiques, il est important d'équilibrer le système de canaux de manière à ce que toutes les cavités soient uniformément remplies par le composé. Un logiciel de simulation pour la conception du système de canaux peut grandement simplifier le développement du moule et prouver son efficacité à l'aide d'essais de remplissage du moule.
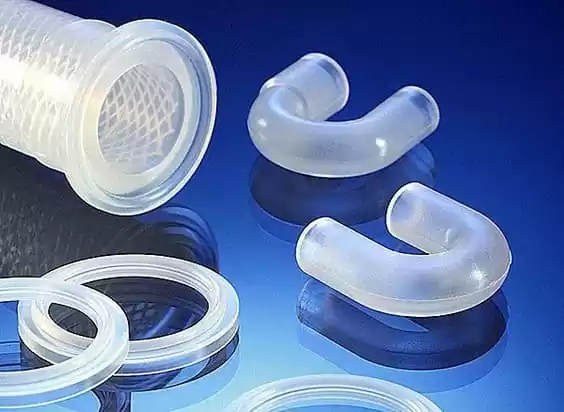
5. Démoulage
Le moulage en silicone liquide, par vulcanisation, a tendance à adhérer à la surface du métal, et la flexibilité du produit peut rendre son démoulage difficile. La résistance à la déchirure à haute température du LSR permet de le démouler dans des conditions normales sans endommager les produits, même les plus grands.
Les techniques de démoulage les plus courantes sont le démoulage à l'aide d'une plaque de démoulage, le démoulage à l'aide d'une goupille de démoulage et le démoulage pneumatique. D'autres techniques courantes sont le raclage au rouleau, le démoulage par plaque d'exportation et le démoulage automatique.
Lors de l'utilisation d'un système de démoulage, il est important de le maintenir à un niveau de précision élevé. S'il y a trop d'espace entre la tige de poussée supérieure et le manchon de la tige de guidage, ou si l'espace entre les pièces devient important en raison de l'usure au fil du temps, il peut en résulter une fuite de colle.
La tige de poussée supérieure en forme de cône inversé ou de champignon est très efficace car elle permet d'appliquer une pression de contact plus importante et facilite l'amélioration de l'étanchéité.
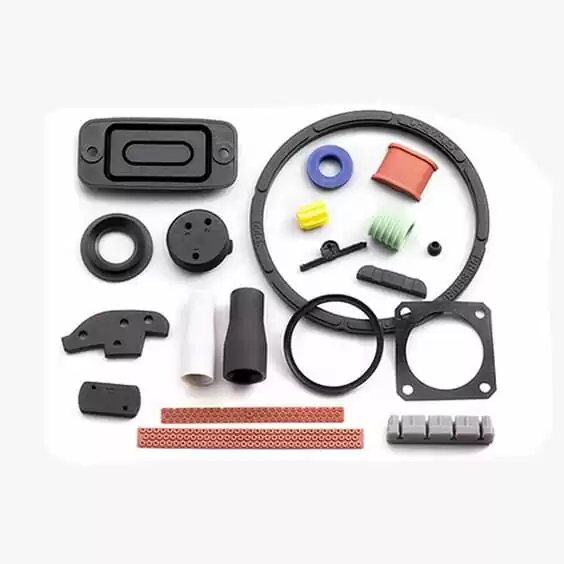
6. Matériau du moule
Les palettes pour moules sont souvent fabriquées en acier à outils non allié (n° 1.1730, code DIN C45W). Pour les palettes de moules qui doivent résister à une température élevée de 170℃-210℃, elles doivent être fabriquées en acier pré-trempé (no.1.2312, code DIN 40 CrMn-M oS 8 6) pour des raisons de résistance aux chocs.
Pour les palettes de moules comportant des cavités, elles doivent être fabriquées en acier à outils éthylique nitruré ou trempé, traité thermiquement, afin de garantir leur résistance aux températures élevées.
Pour les LSR à haute capacité de remplissage, tels que les LSR résistants à l'huile, il est recommandé d'utiliser des matériaux plus durs pour la fabrication des moules, tels que l'acier chromé brillant ou le métal en poudre spécialement conçu à cet effet (n° 1.2379, DINcode X 155 CrVMo121).
Lors de la conception moules d'injection pour les matériaux à forte usure, les pièces soumises à une forte friction doivent être conçues pour être formées de manière à pouvoir être remplacées, de sorte que l'ensemble du moule ne doive pas être remplacé.
La surface intérieure de la cavité du moule a un impact significatif sur la finition du produit. Le plus évident est que le produit formé correspondra parfaitement à la surface de la cavité. Moules d'injection pour les produits transparents doivent être en acier poli. L'acier Chin/Nickel traité en surface est extrêmement résistant à l'usure, tandis que le PTFE/Nickel facilite le démoulage.
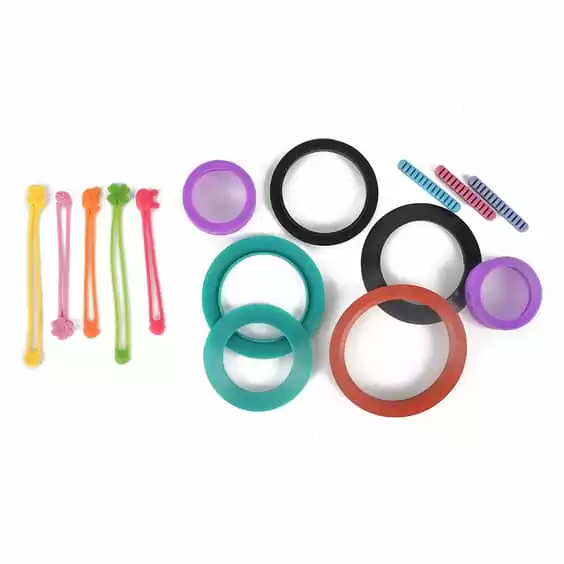
7. Contrôle de la température
D'une manière générale, le moulage des LSR est de préférence chauffé par un chauffage électrique, généralement par des bandes chauffantes, des cartouches chauffantes ou des plaques chauffantes.
L'essentiel est de répartir uniformément le champ de température dans l'ensemble du moule afin de favoriser un durcissement uniforme des LSR. Pour les grands moules, il s'agit d'une méthode de chauffage rentable lorsque l'on pousse le chauffage de contrôle de la température de l'huile.
Le fait d'envelopper le moule d'une plaque isolante permet de réduire les pertes de chaleur. L'inadaptation d'une partie du moule chaud peut entraîner des fluctuations de température importantes entre les processus d'exploitation ou provoquer des courants d'air.
Si la température de la surface est trop basse, la vitesse de durcissement de l'adhésif est ralentie, ce qui empêche souvent le produit de se détacher de l'emballage. moule d'injection et entraîne des problèmes de qualité.
Une certaine distance doit être maintenue entre le dispositif de chauffage et le plan de joint afin d'éviter que le gabarit ne se plie et ne se déforme et ne forme une bavure de colle sur le produit fini. Si le moule est conçu avec un système de canaux froids, l'extrémité chaude et l'extrémité froide doivent être complètement séparées l'une de l'autre.
Des alliages spéciaux de Chin (par exemple 3.7165 [TiA16V4]) peuvent être utilisés en raison de leur conductivité thermique beaucoup plus faible que celle des autres aciers. Dans le cas d'un système de chauffage intégral du moule d'injection, le bouclier thermique doit être placé entre le moule et la palette du moule afin de minimiser les pertes de chaleur. Une conception et un design appropriés peuvent garantir le moulage par injection de LSR, où le moule est très important.
Les principes de conception des moules susmentionnés visent à remplir la cavité du moule avec du caoutchouc, à raccourcir le temps de vulcanisation et à obtenir une qualité supérieure et un rendement élevé du produit fini, ce qui permet de fournir le liquide à l'utilisateur. moulage de caoutchouc de silicone avec de bonnes retombées économiques.