De structuur van thermohardende spuitgietmatrijzen voor vloeibaar siliconenrubber (LSR) is over het algemeen gelijk aan die van matrijzen voor thermoplastische compounds, maar er zijn een aantal significante verschillen.
Zo hebben LSR-compounds over het algemeen een lage viscositeit en daardoor zeer korte vultijden, zelfs bij een zeer lage injectiedruk. Om luchtinsluiting te voorkomen, is een goede ontluchting in de matrijs essentieel.
Bovendien krimpen LSR-compounds niet zoveel als thermoplastische compounds in de matrijs; ze hebben de neiging om uit te zetten als ze warm zijn en iets te krimpen als ze koud zijn. Daardoor blijft het product niet altijd zoals verwacht aan de bolle kant van de mal liggen, maar wordt het in de holte met een groter oppervlak vastgehouden.
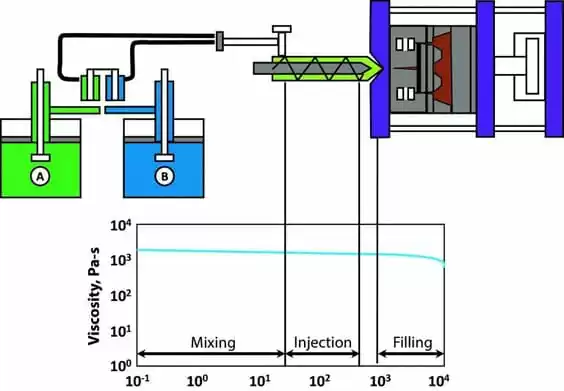
1. Krimp
Hoewel LSR niet krimpen in de mal, krimpen ze vaak 2,5% tot 3% na het ontvormen en afkoelen. De exacte hoeveelheid krimp hangt tot op zekere hoogte af van de formulering van die samenstelling.
Vanuit het perspectief van de matrijs kan krimp echter door verschillende factoren worden beïnvloed, waaronder de temperatuur van de matrijs, de temperatuur van de samenstelling bij het ontvormen, de druk in de matrijsholte en de daaropvolgende compressie van de samenstelling.
De locatie van het injectiepunt is ook het overwegen waard, omdat de krimp in de richting van de lijmvloei meestal groter is dan de krimp in de richting loodrecht op de lijmvloei.
De grootte van het product beïnvloedt ook de krimp, waarbij dikkere producten over het algemeen minder krimpen dan dunnere. Als secundaire vulkanisatie nodig is, kan de krimp nog eens 0,5%-0,7% bedragen.
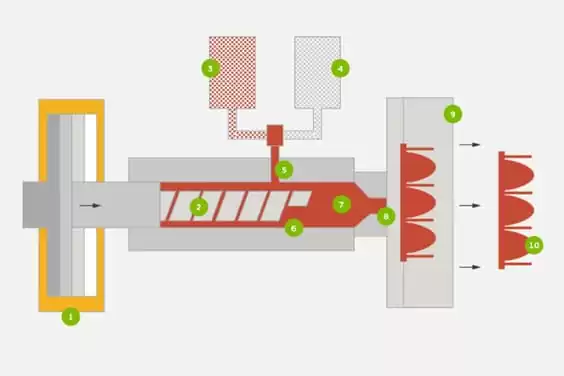
2. Deellijn
Het bepalen van de locatie van de deellijn is een van de eerste stappen bij het ontwerpen van een siliconenrubber spuitgietmatrijs. Ontluchting wordt voornamelijk bereikt met behulp van groeven op de scheidingslijn, die zich in het gebied moet bevinden waar de injectiepasta blijft zitten. Dit helpt om interne luchtbellen te voorkomen en het verlies van sterkte bij de lijmverbinding te verminderen.
Door de lage viscositeit van LSR moet de scheidingslijn precies zijn om morsen te voorkomen. Toch zijn deellijnen vaak zichtbaar op gevormde producten. Het vrijkomen van de gietvorm wordt beïnvloed door de geometrie van het onderdeel en de positie van het deellijnoppervlak. Als je het onderdeel met een lichte afschuining ontwerpt, zorg je voor een consistente affiniteit met de gewenste andere helft van de matrijs. spuitgietvorm holte.
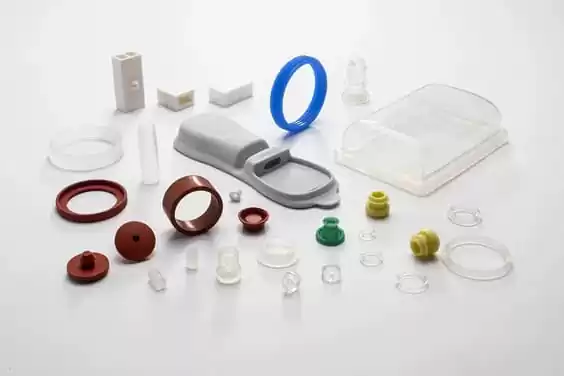
3. Ontluchting
Als de LSR wordt geïnjecteerd, wordt de lucht in de holte samengeperst als de mal sluit en vervolgens door de ontluchtingsgroeven uitgestoten als de mal zich vult.
Als de lucht niet volledig wordt afgevoerd, zal deze worden ingesloten in de lijm (wat er vaak toe leidt dat een deel van het product witte randen vertoont). De ontluchtingsgroeven zijn over het algemeen mm-3 mm breed en 0,004 mm-0,005 mm diep.
Het beste ontluchtingseffect creëer je door binnenin de mal te vacumeren. Dit wordt bereikt door een pakking te maken op de scheidingslijn en alle holtes snel vacuüm te pompen met een vacuümpomp. Zodra het vacuüm het nominale niveau heeft bereikt, wordt de matrijs volledig gesloten en begint de injectiepers.
Sommige spuitgietmachines kunnen werken met variabele sluitkrachten, waardoor de verwerker de matrijs kan sluiten met lage druk totdat 90-95% van de holte gevuld is met LSR (waardoor lucht gemakkelijker kan ontsnappen), en dan overschakelen naar een hogere sluitkracht om te voorkomen dat de matrijs wordt gesloten. siliconenrubber expansie en overloop.
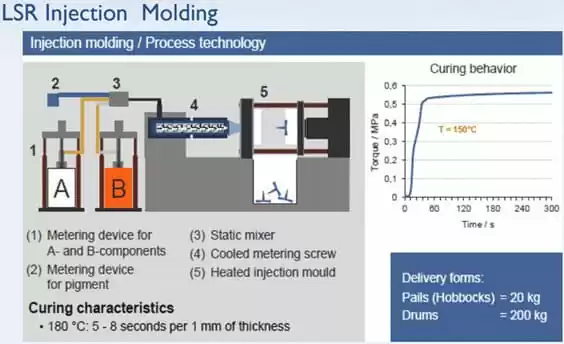
4. Injectiepunt
Bij het gieten van LSR wordt een koud runnersysteem gebruikt. De voordelen van dit siliconenrubber kan worden gemaximaliseerd en de productie-efficiëntie kan maximaal worden verhoogd.
Door producten op een dergelijke manier te verwerken, is het niet nodig om het injectiekanaal te verwijderen, waardoor meer arbeid voor de bewerking en soms een grote hoeveelheid materiaalafval wordt vermeden. In veel gevallen vermindert de rijstrookloze constructie ook de bedieningstijd.
De spuitmond wordt bestuurd door een naaldklep voor positieve stroming en veel fabrikanten bieden nu standaard spuitmonden met pneumatische schakelaars die in verschillende delen van de matrijs kunnen worden geplaatst.
Sommige spuitgietvorm makers hebben een open cold runnersysteem ontwikkeld dat zo klein is dat meerdere injectiepunten (en dus de hele caviteit) moeten worden ingesteld in een zeer beperkte matrijsruimte.
Deze technologie maakt het mogelijk om grote hoeveelheden van hoge kwaliteit te produceren. siliconenrubber producten zonder de injectiepoorten te hoeven scheiden.
Als er een koud runnersysteem wordt gebruikt, is het belangrijk om een effectieve temperatuurscheiding te creëren tussen de hete caviteit en de koude runner. Als de runner te heet is, kan het rubber gaan vulkaniseren voordat het wordt geïnjecteerd. Maar als het te snel afkoelt, zal het te veel warmte absorberen van het spruegebied van de spuitgietvormwat resulteert in onvolledige vulkanisatie.
Voor producten die geïnjecteerd worden met conventionele sprue (bijv. ondergedompelde sprue en conische sprue), is het handig om een injectiepoort met een kleine diameter (meestal 0,2-0,5 mm) te gebruiken voor injectie.
Bij LSR-compounds met een lage viscositeit is het, net als bij thermoplastische compounds, belangrijk om het runnersysteem zo te balanceren dat alle holtes gelijkmatig worden gevuld met het compound. Simulatiesoftware voor het ontwerpen van het runnersysteem kan de ontwikkeling van de matrijs sterk vereenvoudigen en de effectiviteit bewijzen met matrijsvultests.
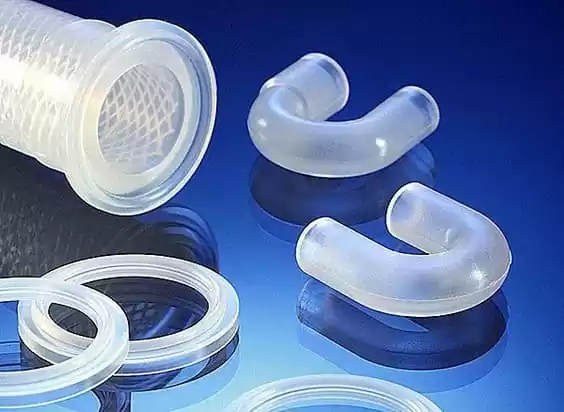
5. Ontvouwen
Vloeibaar siliconen gieten heeft door vulkanisatie de neiging om zich aan het metaaloppervlak te hechten en de flexibiliteit van het product kan het moeilijk maken om het los te maken. Dankzij de scheursterkte van LSR bij hoge temperaturen kan het onder normale omstandigheden worden losgemaakt zonder zelfs grotere producten te beschadigen.
De meest voorkomende release technieken zijn stripper plate release, stripper pin release en pneumatische release. Andere veelgebruikte technieken zijn rollenschrapen, uitvoerplaatvrijgave en automatische vormvrijgave.
Als je een lossysteem gebruikt, is het belangrijk om het binnen een hoge mate van nauwkeurigheid te houden. Als er te veel speling is tussen de bovenste drukpen en de geleidebouthuls, of als de ruimte tussen de onderdelen groot wordt door slijtage na verloop van tijd, kan er lijm gemorst worden.
De omgekeerde kegel- of paddestoelvormige topdrukstift is zeer effectief omdat hierdoor een grotere contactdruk kan worden uitgeoefend en het afdichtingsdoel kan worden verbeterd.
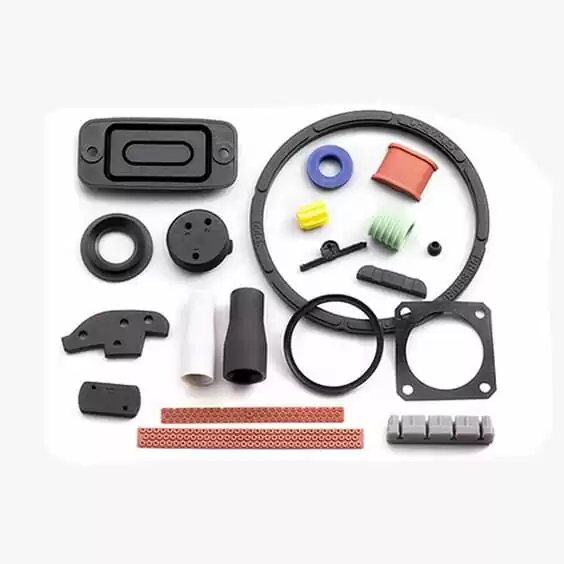
6. Materiaal matrijs
Matrijspallets worden vaak gemaakt van ongelegeerd gereedschapsstaal (nr. 1.1730, DIN-code C45W). Voor matrijspallets die bestand moeten zijn tegen de hoge temperatuur van 170℃-210℃, moeten ze met het oog op de slagvastheid worden gemaakt van voorgetemperd staal (nr. 1.2312, DIN-code 40 CrMn-M oS 8 6).
Matrijspallets met matrijsholten moeten worden gemaakt van genitreerd of gehard hittebehandeld ethylgereedschapsstaal om bestand te zijn tegen hoge temperaturen.
Voor LSR's met een hoge vulcapaciteit, zoals oliebestendige LSR's, wordt aangeraden hardere materialen te gebruiken voor het maken van de mallen, zoals glanzend verchroomd staal of poedervormig metaal dat speciaal voor dit doel is ontwikkeld (nr. 1.2379, DINcode X 155 CrVMo121).
Bij het ontwerpen van spuitgietmatrijzen voor slijtagegevoelige materialen moeten de onderdelen die onderhevig zijn aan hoge wrijving zo worden ontworpen dat ze op een vervangbare manier kunnen worden gevormd, zodat niet de hele matrijs hoeft te worden vervangen.
Het binnenoppervlak van de matrijsholte heeft een grote invloed op de afwerking van het product. Het meest voor de hand liggende is dat het gevormde product perfect aansluit op het oppervlak van de holte. Spuitgietmatrijzen voor transparante producten moeten worden gemaakt van gepolijst staal. Het oppervlaktebehandelde Chin/Nikkel-staal is extreem slijtvast, terwijl PTFE/Nikkel ervoor zorgt dat de vorm gemakkelijker loslaat.
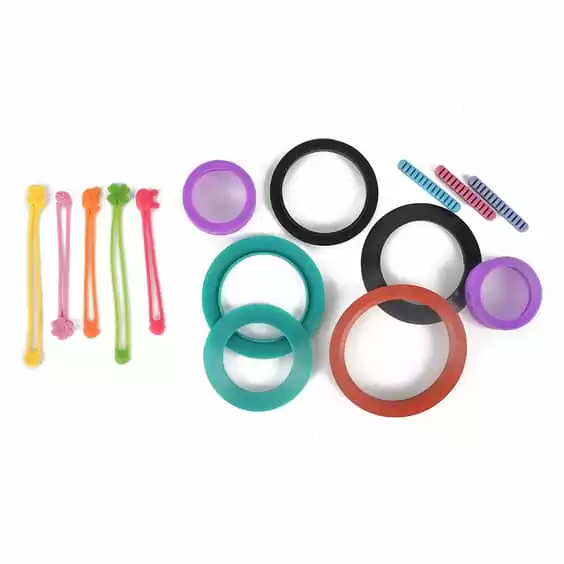
7. Temperatuurregeling
Over het algemeen wordt het gieten van LSR bij voorkeur elektrisch verwarmd, meestal met bandverwarmers, patroonverwarmers of verwarmingsplaten.
De sleutel is om het temperatuurveld gelijkmatig verdeeld over de mal om uniforme uitharding van LSR te bevorderen. Op grote mallen, is een kosteneffectieve verwarming methode bij het duwen olie temperatuurregeling verwarming.
De matrijs omwikkelen met een isolerende plaat helpt om warmteverlies te beperken. Als een deel van de hete matrijs ongeschikt is, kan dit leiden tot grote temperatuurschommelingen tussen de processen door of tot luchtstromingen.
Als de oppervlaktetemperatuur te laag wordt, wordt de uithardingssnelheid van de lijm vertraagd, waardoor het product vaak niet uit de lijm kan komen. spuitgietvorm en veroorzaakt kwaliteitsproblemen.
Er moet een bepaalde afstand worden aangehouden tussen het verwarmingselement en de deellijn om te voorkomen dat de mal buigt en vervormt en een lijmbraam vormt op het eindproduct. Als de mal ontworpen is met een koud runnersysteem, moeten het hete uiteinde en het koude uiteinde volledig van elkaar gescheiden zijn.
Speciale Chin-legeringen (bijv. 3.7165 [TiA16V4]) kunnen worden gebruikt vanwege hun veel lagere warmtegeleidingsvermogen in vergelijking met andere staalsoorten. Bij een integraal verwarmingssysteem voor spuitgietmatrijzen moet het hitteschild tussen de matrijs en de matrijspallet worden geplaatst om warmteverlies te minimaliseren. Een goed ontwerp en concept kunnen zorgen voor LSR spuitgieten, waarbij de matrijs erg belangrijk is.
De bovenstaande matrijsontwerpprincipes zijn gericht op het vullen van de matrijsholte met rubber, het verkorten van de uithardingstijd en het bereiken van een superieure kwaliteit en een hoge opbrengst van het eindproduct. gieten van siliconenrubber processor met goede economische voordelen.