EPDM (EPDM rubber), als synthetisch rubber met een goede elasticiteit, slijtvastheid, hittebestendigheid, weerbestendigheid, ozonbestendigheid, zoetwaterbestendigheid en zeewaterbestendigheid, wordt veel gebruikt in rubberproducten voor de auto-industrie, zoals deur- en raamafdichtingen, hydraulische remslangen en afdichtingen, ventilatiekanalen voor airconditioning, afdichtingen in motorkoelsystemen en koelsystemen voor airconditioning, slangen voor het transport van koelvloeistof, enz.
EPDM-rubber is een apolaire, verzadigde structuur. De zogenaamde "apolaire", d.w.z. de moleculen waaruit het polymeer is opgebouwd, bevatten geen polaire groepen binnenin.
De zogenaamde "verzadigde", dat wil zeggen, de samenstelling van het polymeer bevat geen dubbele bindingen in het molecuul. In het algemeen kunnen rubber en thermoplastische elastomeren worden onderverdeeld in "polaire" en "apolaire", en "verzadigde" en "onverzadigde" verschillende structuren.
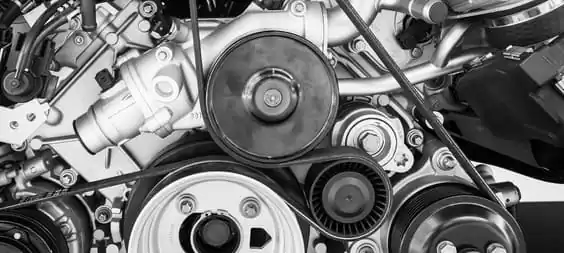
Materialen waarvan de moleculen zelf polaire groepen bevatten, zijn over het algemeen "polaire" materialen. De "polaire" structuur bepaalt de weerstand van polymeren tegen oplosmiddelen, over het algemeen volgens het principe van vergelijkbare oplosbaarheid, dat wil zeggen, polaire oplosmiddelen lossen polaire polymeren op of zwellen ze op, en omgekeerd.
De "verzadigde" structuur heeft te maken met de weerstand van polymeren tegen atmosferische veroudering (oxidatie). Als de polymeermolecule een dubbele binding bevat, wordt de dubbele binding gemakkelijk geoxideerd, waardoor het polymeer instabiel is en gemakkelijk wordt afgebroken.
Dus als "apolair" EPDM, bestand tegen polaire media, zoals heet water en stoom, detergenten, organische en anorganische zuren, polaire oplosmiddelen (zoals ethanol, aceton, esters, enz.), remvloeistof op basis van glycol, enz.
En niet bestand tegen niet-polaire media, zoals minerale olie, benzine, dierlijke en plantaardige vetten, en oliën, siliconenolie, enz., en wordt veel gebruikt in remvloeistof op basis van glycol (SL-DOT4) systemen, motorkoelsystemen met antivries; als "verzadigde" EPDM, met een uitstekende weerstand tegen ozon en verwering, op grote schaal gebruikt in de productie van lucht, water, enz.
EPDM in de auto-gebruikstemperatuur is over het algemeen -40 ℃ tot 120 ℃. Het volgende is een specifieke inleiding tot het gebruik van EPDM producten in auto's, de bijbehorende materiaalprestatievereisten en een analyse van veelvoorkomende storingssituaties.
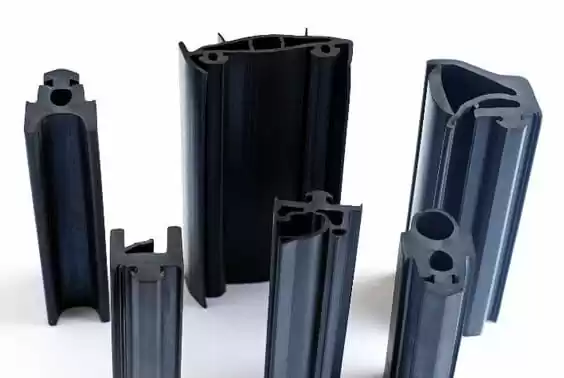
Toepassing in afdichtingsproducten voor de auto-industrie
De overgrote meerderheid van de afdichtingen voor auto's wordt geproduceerd door extrusieapparatuur met een consistente dwarsdoorsnede en oneindige lengte (indien gebruikt, onderschept volgens de vereiste lengte), terwijl een klein aantal onregelmatige producten wordt geproduceerd door vulkanisatiematrijzen.
Het proces van geëxtrudeerde producten is als volgt: ingrediënten → rubber mengen → meerdere materialen (kan bestaan uit: hard rubber, zacht rubber, sponsrubber, gekleurd rubber, metalen skelet, versterkingsdraad, enz.)
Samengestelde extrusie → verwarmende vulkanisatie (misschien: heteluchtvulkanisatie, vulkanisatie tankvulkanisatie, microgolfvulkanisatie, glasparel kookbedvulkanisatie, zoutbadvulkanisatie, enz. → nabewerking (snijden, vulkanisatievoeg, elektrostatisch flocken, oppervlakte flood coating, lijmen, enz.
Het wordt veel gebruikt in de voor-en achterruiten, deuren, ramen, motorruimte, kofferbak en andere delen van de auto, gebruikt om de kloof tussen de carrosseriedelen op te vullen, met schokabsorptie, waterdicht, stofdicht, geluidsisolatie, decoratie, bescherming van bestuurders en passagiers en andere functies.
Zulke siliconenrubber producten zijn voornamelijk in contact met zonlicht, water en ozon, het gebruik van temperaturen in -40 ℃ ~ 100 ℃, de korte-termijn hittebestendige temperatuur kan oplopen tot 125 ℃.
EPDM materiaal gebruikt voor rubber afdichtstrip algemene hardheid (Shore A) in 40 ~ 90 tussen de keuze; de treksterkte moet meer dan 7MPa; rek bij breuk over het algemeen in 150% ~ 500%; compressie vervorming (85 ℃, 22h) moet minder dan 45%.
De scheursterkte zou groter dan 5N/m moeten zijn; ozon het verouderen (50pphm, rek 20%, 72h) zou geen barsten moeten zijn; xenonlamp het Verouderen (gebruikend xenonlamp 1200 materiaal, relatieve vochtigheid 80% ~ 95%, zwarte plaattemperatuur 55 ℃ ~ 60 ℃, 1000h) zijn treksterkte en verlenging van de daling kunnen 15% niet overschrijden.
Zijn temperatuur van de glasovergang (TR) maximum -50 ℃; thermische het verouderen test (100 ℃, 70 h), zijn hardheidsverandering zou ± 5 moeten zijn, de verandering van de treksterkte zou ± 15% moeten zijn, en de verlenging van de daling zou 30% niet moeten overschrijden.
Over het algemeen is de levensduur van afdichtingen voor auto's gemaakt van EPDM-rubber kan oplopen tot meer dan tien jaar. In de feitelijke productie en toepassing hebben we echter ook te maken gehad met oppervlaktescheuren, verlies van afdichtingsprestaties, oppervlaktebevriezing en andere storingsverschijnselen van de deur- en raamafdichtingen na één jaar installatie.
Het oppervlak kraken van het product testen, de ozonbestendigheid test na 20 uur dat scheuren, niet aan de standaard eisen. Na het onderzoek van deze batch van substandaard producten, de formulering fout (EPDM-rubber gehalte lager is) werd veroorzaakt door; rubber afdichtingsoppervlak vorst (bloei).
Analyse van de oorzaak:
(1) Onjuist ontworpen formuleringen. Zwavelgeel, versneller, activator, antioxidant, enz. in de ingrediënten, door verzadigingsoverstroming; anorganisch calciumcarbonaat vulmiddel stressoverstroming.
(2) Onjuiste werking van het mengproces, te korte tijd, wat resulteert in ongelijkmatige dispersie van vulstof, lokaal meer dan verzadiging. Door de formule te wijzigen, de mengtijd te verlengen en uiteindelijk het overstromingsprobleem op te lossen.
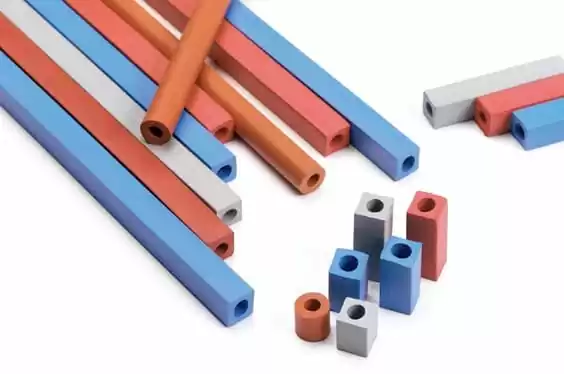
Toepassing van EPDM in hydraulische remslangen en ronde afdichtingen
EPDM remvloeistofbestendig (DOT3, DOT4, DOT5 (op basis van siliconenolie), gebruikt bij de productie van de binnenste rubberlaag van hydraulische remslangen en rempompafdichtingen.
Deze EPDM producten zijn in contact met het belangrijkste medium remvloeistof, het gebruik van temperaturen tussen -40 ℃ ~ 120 ℃, en op korte termijn hittebestendige temperaturen tot 135 ℃.
Dergelijke gebruikte delen EPDM, hardheid (Shore A) is 80; zijn treksterkte zou meer dan 10.5MPa moeten zijn; verlenging bij breuk is over het algemeen boven 175%; in het verlengingstarief van 50% van de vaste uitbreidingsspanning van 2.5 ~ 4MPa; in het verlengingstarief van 100% van de vaste uitbreidingsspanning van 8MPa of meer.
De compressievervorming (100 ℃, 22 h) zou minder dan 40% moeten zijn; zijn temperatuur van de glasovergang (TR) maximum -50 ℃; het ozon verouderen (50pphm, 20% verlenging, 72h) zou geen barsten moeten zijn; de test van de remvloeistof (zet het specimen in de remvloeistof, 150 ℃, 70h) zijn hardheidsverandering zou 5 moeten zijn.
De treksterkteverandering zou ± 20% moeten zijn, zou de verlengingverandering -15% ~ 20% moeten zijn, zou de volumeverandering binnen ± 20% moeten zijn. 20%, zou de volumeverandering ± 5% moeten zijn; thermische test (125 ℃, 70h), zou de hardheidsverandering ± 5 moeten zijn, zou de treksterkteverandering ± 15% moeten zijn, en de verlenging van de daling kan 15% niet overschrijden.
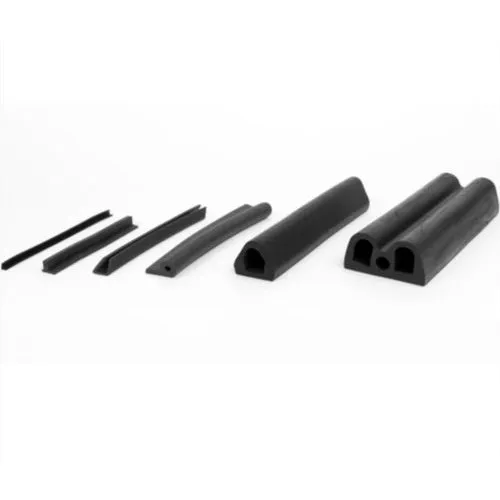
EPDM in toepassingen voor verwarmings-, ventilatie- en aircoslangen
De rubberslang bestaat meestal uit drie lagen, namelijk de binnenlaag, de middelste versterkingslaag (chemische vezelstof of staaldraad) en de buitenlaag. De materialen die voor de drie lagen worden gebruikt, moeten worden gekozen op basis van de werkelijke vereisten.
De binnenlaag moet bestand zijn tegen corrosie van het geleverde medium, terwijl de buitenlaag mechanische sterkte moet hebben en aangepast moet zijn aan de externe omgeving.
Daarom is het binnenste en buitenste rubber vaak geen rubber. EPDM wordt veel gebruikt in verwarmings- en ventilatieslangen binnen en buiten de rubberlaag en aircoslangen in de buitenste rubberlaag omdat het materiaal goed bestand is tegen lucht, water, ozon, veroudering door zonlicht en flexibiliteit bij lage temperaturen.
Dergelijke onderdelen die EPDM gebruiken, hardheid (Shore A) voor 70; de treksterkte moet meer zijn dan 10,5MPa; breukrek is over het algemeen meer dan 300%; compressie restvervorming (100 ℃, 22 h) moet minder zijn dan 40%;
Zijn temperatuur van de glasovergang (TR) maximum -45 ℃; ozon het verouderen (50pphm, die 20%, 72h uitrekken) zou geen barst moeten zijn; IRM902-olietest (zet het specimen in IRM902-olie, 100 ℃, 70h) zijn hardheidsverminderingsmaximum van 15, de vermindering van de treksterkte maximum van 30%.
De scheursterktevermindering maximum van 30%, volumeverandering zou binnen 80% moeten zijn; thermische het verouderen test (125 ℃, 70 h), zijn hardheidsverandering zou ± 5 moeten zijn, de treksterkteverandering zou ± 15% moeten zijn, kan de verlengingvermindering 40% niet overschrijden.
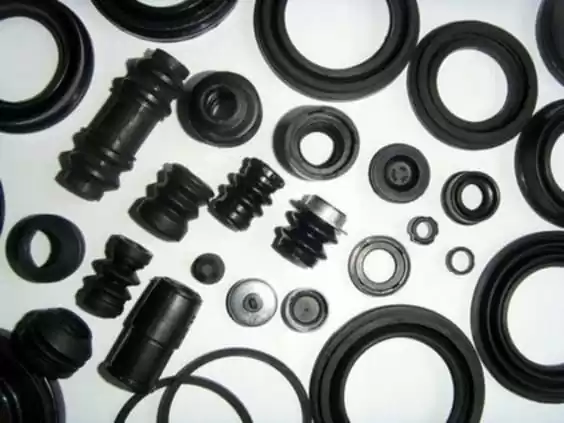
EPDM in de toepassing van het trekken van de riem
Dit soort onderdeel, voornamelijk gebruikt voor de verbinding tussen de wieldop, accubox deksel bevestiging, enz., is bestand tegen de hoge dynamische en mechanische belasting, in het gebruik van het proces en is altijd in de spanning staat.
Deze siliconenrubber producten worden voornamelijk blootgesteld aan zonlicht, water en ozon, het gebruik van temperaturen in -40 ℃ ~ 85 ℃, de korte-termijn hittebestendige temperatuur kan oplopen tot 100 ℃.
EPDM-materiaal dat wordt gebruikt om dergelijke onderdelen te maken, de hardheid (Shore A) is over het algemeen 60 ~ 80; de treksterkte moet meer dan 14MPa zijn; breukrek is over het algemeen 200% ~ 400%; de scheursterkte moet groter zijn dan 7N/m;
Compressie restvervorming (85 ℃, 22h) moet minder zijn dan 45%; compressie restvervorming (-20 ℃, 22h) moet minder zijn dan 45%; weerstand tegen ozon veroudering (50pphm, 20% uitrekken, 72h) moet geen scheuren; xenonlamp het verouderen (gebruikend xenonlamp 1200 materiaal, relatieve vochtigheid 80% ~ 95%, zwarte plaattemperatuur 55 ℃ ~ 60 ℃, 1000h) de treksterkte en de verlenging van de daling zouden 15% niet moeten overschrijden;
Zijn temperatuur van de glasovergang (TR) van -50 ℃ maximum; hitte het verouderen test (100℃, 70h), zou zijn hardheidsverandering ±75 moeten zijn, zou de treksterkteverandering ±15% moeten zijn, zou de verlenging daling 40% niet moeten overschrijden.
De breuk van de band van de batterijklep en de scheuren op het oppervlak van de band van de wielbeschermer ontstonden na een half jaar belasting. Na het mislukken van de treksterkte-, scheursterkte- en ozonverouderingstest van het product waren de behaalde resultaten 8,5MPa treksterkte, scheursterkte 5N/m en ozonveroudering 42 uur scheurvorming, die niet voldoen aan de standaardvereisten.
Individuele fabrikanten van het trekken van tape op het belang van de rubberen formule zijn niet genoeg begrip, dat zolang de EPDM rubber is gemaakt van rubber trekkende tape kan worden, in feite, vanwege de verschillende formuleringen, kunnen de prestaties van het product sterk variëren.
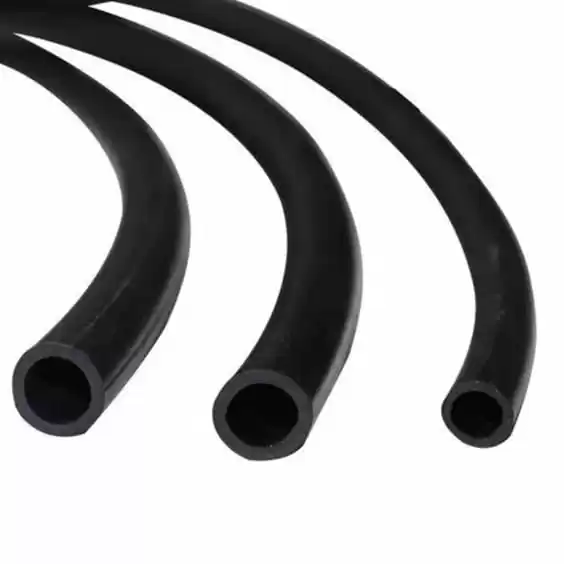
Toepassing van EPDM in motorkoelsystemen en afdichtingen van airconditionings- en koelsystemen
EPDM wordt gebruikt om afdichtingen te maken in motorkoelsystemen. Deze producten zijn in contact met het medium is antivriesmiddel, zonlicht, water, ozon, het gebruik van temperatuur in -40 ℃ ~ 125 ℃, en op korte termijn hittebestendige temperaturen tot 135 ℃.
Dergelijke delen die EPDM gebruiken, hardheid (Shore A) voor 60 ~ 80 (75 voor de toepassing van ronde verbindingen in het koelsysteem); zijn treksterkte zou meer dan 10 moeten zijn.5MPa; breukrek is over het algemeen meer dan 175%; in de rek van 50% van de vaste uitbreidingsspanning van 1 ~ 2MPa; in de rek van 100% van de vaste uitbreidingsspanning van 2 ~ 5MPa hierboven; krimpvervorming (150 ℃, 22 h) moet minder zijn dan 20%;
De hittebestendige temperatuur tot 135 ℃. (22 uur) moet lager zijn dan 20%; de glasovergangstemperatuur (TR) is maximaal -50 ℃; de weerstand tegen ozonveroudering (50pphm, uitrekken van 20%, 72 uur) mag geen barsten vertonen;
Voor afdichtingen die in motorkoelsystemen worden gebruikt, moet een koelmiddeltest worden uitgevoerd (testmonster geplaatst in antivries, 150°C, 166u, testdruk ongeveer 0,4 MPa) en de verandering in hardheid moet ±5 zijn, de verandering in treksterkte moet ±20% zijn, de verandering in breukrek moet -15% tot 20% zijn en de volumeverandering moet ±5% zijn;
Voor verbindingen die in airconditioningssystemen worden gebruikt, moet een koelmiddeltest worden uitgevoerd (het specimen dat in P-test wordt geplaatst (zet het specimen in PAG, ND8 koelmiddel, 100 ℃, 70h) de hardheidsverandering van tot ± 5, treksterkteverandering van tot ± 20%, verlenging bij onderbrekingsverandering van tot -15% ~ 20%, volumeverandering zou binnen ± 5% moeten zijn; thermische het verouderen test (150 ℃, 70h), zou de hardheidsverandering ± 5 moeten zijn, zou de treksterktedaling minder dan 10% moeten zijn, kan de elongatiedaling 10% niet overschrijden.
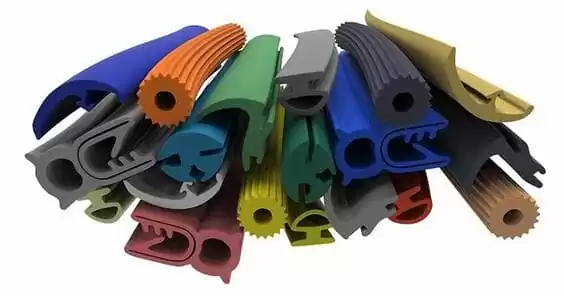
EPDM in de toepassing van koelvloeistofslang
EPDM wordt gebruikt om een motorwaterslang te maken. De binnenste en buitenste rubberen lagen zijn gemaakt van EPDM-materiaal. Zo'n EPDM producten in contact met het medium zijn antivriesmiddel, zonlicht, water, ozon, het gebruik van temperatuur in -40 ℃ ~ 125 ℃, de korte-termijn hittebestendige temperatuur kan oplopen tot 150 ℃.
Dergelijke gebruikte delen EPDM, hardheid (Shore A) voor 65; zijn treksterkte zou boven 10.5MPa moeten zijn; verlenging bij breuk in meer dan 300%; in het verlengingstarief van 50% van de vaste uitrekspanning van 1 ~ 2MPa; verlengingstarief van 100% van de vaste uitrekspanning van 2 ~ 4.5MPa hierboven; compressie overblijvende vervorming (100 ℃, 22 h) zou minder dan 20% moeten zijn;
Zijn glasovergangstemperatuur (TR) maximum van -50 ℃; ozon het verouderen (50pphm, die 20%, 72h uitrekken) zou geen barsten moeten zijn; koelmiddeltest (het specimen dat in antivriesmiddel, 150 ℃, 166h, testdruk van ongeveer 0.4MPa wordt geplaatst).
De hardheidsverandering moet ± 5 zijn, de treksterkteverandering moet ± 20% zijn, de breukrekverandering moet -15% ~ 20% zijn, de volumeverandering moet ± 5% zijn. Hitte het verouderen test (150 ℃, 70 h), de hardheidsverandering zou ± 5 moeten zijn, treksterkte zou minder dan 10% moeten zijn, en de verlenging van de daling zou 10% niet moeten overschrijden.