Inleiding
Het ontwerp van de matrijsholte is de spil van succesvol persgieten en kan de toekomst van veel industrieën vormgeven. Dit kritische facet van de productie mag niet onderschat worden, omdat het in staat is om consistente resultaten van hoge kwaliteit te leveren - een waar bewijs van het belang ervan.
In een wereld waar innovatie en precisie de boventoon voeren, komt het persgieten naar voren als een veelzijdig en onmisbaar productieproces. Met toepassingen in een groot aantal industrieën, waaronder de auto-industrie, elektronica en consumptiegoederen, speelt het een centrale rol bij het vormgeven van de producten waar we dagelijks op vertrouwen. Van auto-onderdelen die zijn ontworpen voor prestaties en duurzaamheid tot elektrische isolatiematerialen die onze veiligheid garanderen, compressievormen raakt bijna elk facet van ons leven.
Als we dieper ingaan op het rijk van ontwerp van de matrijsholte voor persgietenbeginnen we aan een reis die het ingewikkelde tapijt van dit proces ontrafelt. Door de nuances te verkennen, zullen we onthullen hoe het juiste ontwerp van de matrijsholte een wereld van mogelijkheden kan openen en producten kan maken die niet alleen aan onze verwachtingen voldoen, maar deze vaak zelfs overtreffen. Ga met ons mee op verkenning naar de kunst en wetenschap achter compressievormen, waarbij het ontwerp van de matrijsholte het kompas is dat ons naar het toppunt van uitmuntende productie leidt.
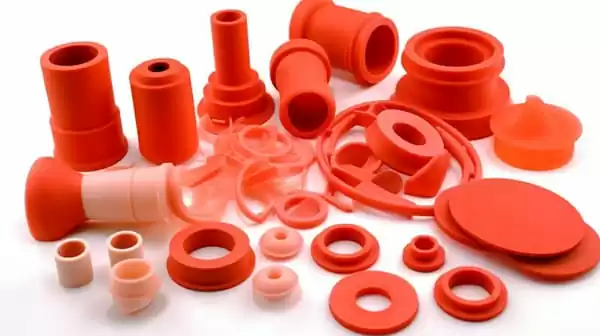
Inzicht in spuitgietprocessen
Persgieten is een veelzijdig en veelgebruikt productieproces met toepassingen in verschillende industrieën. Om de essentie van deze techniek te begrijpen, is het cruciaal om het op te splitsen in zijn kerncomponenten.
1. Het persgietproces:
De kern, persgieten is een proces waarbij materialen worden gevormd met behulp van hitte en druk. De betrokken stappen zijn als volgt:
Materiaalvoorbereiding: Het proces begint met de voorbereiding van grondstoffen, meestal in de vorm van korrels, pellets of sheet molding compounds (SMC).
Verwarmen: De mal, die vaak uit twee helften bestaat, wordt rond het materiaal gesloten. Vervolgens wordt warmte toegepast om het materiaal zacht te maken of te smelten, waardoor het buigzaam wordt.
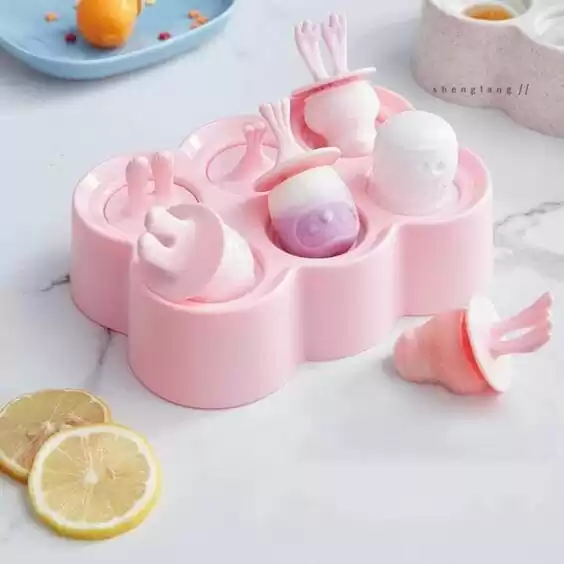
Samenpersen: Er wordt druk uitgeoefend op de vormholte, waardoor het materiaal wordt samengeperst en de gewenste vorm van het eindproduct krijgt.
Afkoelen: Zodra het materiaal de vorm van de mal heeft aangenomen, wordt het afgekoeld om te stollen en wordt de verwarmde mal hard, waardoor de gewenste vorm behouden blijft.
Uitwerpen: Tot slot wordt het spuitgietproduct uit de matrijsholte uitgeworpen, klaar voor verdere verwerking of gebruik.
2. Ontwerp van compressiemallen:
De basis van succesvol persen ligt in het ontwerp van de vormholte. Ontwerp van compressiematrijzen omvat verschillende cruciale elementen:
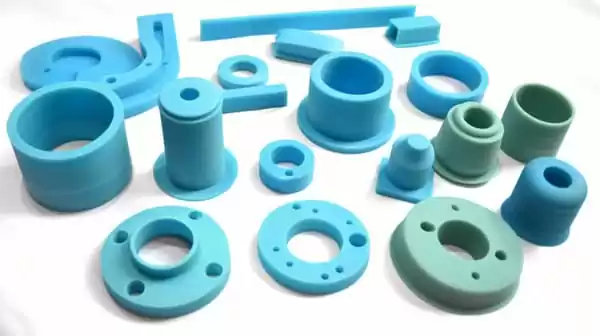
Geometrie: De geometrie van de matrijsholte moet precies overeenkomen met de vorm van het eindproduct. Dit omvat overwegingen zoals productdikte, ontwerphoeken en ondersnijdingen, om een soepele uitwerping te garanderen.
Ontluchting: Effectief ontluchten is essentieel om ingesloten lucht en gassen te laten ontsnappen tijdens het gieten. Een goede ontluchting voorkomt defecten zoals luchtzakken of holtes in het eindproduct.
Deellijn: De deellijn geeft aan waar de matrijs zich splitst om het gevormde onderdeel vrij te geven. Het moet goed gedefinieerd zijn en onopvallend voor de esthetiek en functionaliteit van het product.
Poortontwerp: De poort is het punt waardoor het gesmolten materiaal de matrijsholte binnenkomt. Een zorgvuldig poortontwerp zorgt voor een gelijkmatige vulling en minimaliseert defecten. Poorttypes zijn onder andere randpoorten, pinpoorten en tunnelpoorten.
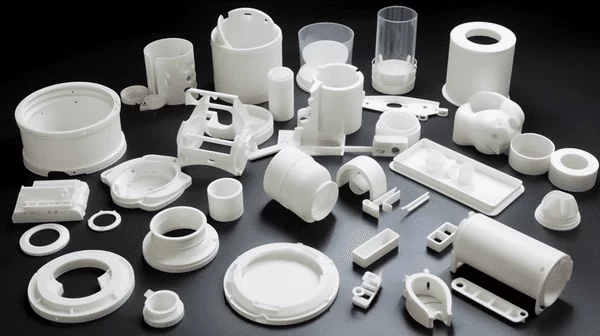
Koelsysteem: Efficiënte koelkanalen in de matrijs helpen om het gevormde onderdeel snel te laten stollen, voorkomen kromtrekken of vervormen en verbeteren de cyclustijden.
Afwerking oppervlak: Afhankelijk van de vereisten van het product kan de oppervlakteafwerking van de matrijsholte gepolijst, getextureerd of gecoat worden om de esthetiek van het eindproduct te verbeteren.
3. Materialen die gebruikt worden bij het persen:
Persgieten is compatibel met een groot aantal materialen, waaronder thermohardende materialen zoals epoxyhars, siliconenrubber en polymeerharsen. Het blinkt vooral uit met vezelversterkte harsmaterialen, zoals glasvezel- of koolstofvezelcomposieten. Deze materialen bieden uitstekende mechanische prestaties, temperatuurbestendigheid en chemische weerstand.
4. Voor- en nadelen van persen:
Voordelen:
Kosteneffectief: Bij persen worden vaak gerecyclede thermoplastische materialen en materialen met een relatief laag smeltpunt gebruikt, waardoor de productiekosten lager zijn.
Breed temperatuurbereik: Het kan mallen maken voor onderdelen met een groot temperatuurbereik en hoge eisen aan chemische bestendigheid.
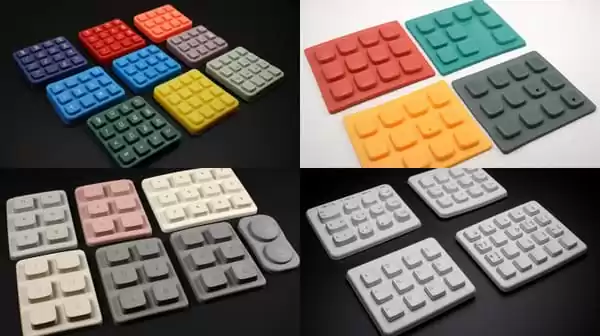
Composietmaterialen: Ideaal voor het werken met composietmaterialen zoals glasvezels en koolstofvezels, waardoor de productie van lichtgewicht componenten met hoge sterkte mogelijk wordt.
Nadelen:
Complexe geometrieën: Mogelijk niet geschikt voor het produceren van onderdelen met extreem complexe geometrieën of nauwe toleranties.
Langzamer proces: Compressievormen kan langzamer zijn dan andere vormprocessen zoals spuitgieten, wat invloed kan hebben op de productiesnelheid.
In essentie legt inzicht in het compressievormproces, de rol van het ontwerp van compressievormen, de veelzijdigheid van de gebruikte materialen en de voor- en nadelen van deze methode de basis voor het benutten van het potentieel ervan in verschillende industrieën. Het is een proces dat precisie, creativiteit en techniek combineert om grondstoffen te vormen tot de producten die onze wereld doen functioneren.
Sectie 2: Soorten persen
Op het gebied van persen spelen matrijstypen een cruciale rol bij het bepalen van het resultaat van het proces. De keuze van de matrijs kan de productkwaliteit, complexiteit en productie-efficiëntie aanzienlijk beïnvloeden. Laten we ons eens verdiepen in de drie primaire matrijstypes voor persgieten en hun kenmerken en toepassingen ontrafelen:
1. Open-flash mal:
Kenmerken:
Flashbeheer: Het kenmerk van open-flash mallen is de mogelijkheid voor overtollig materiaal, bekend als "flash", om te ontsnappen tijdens het persen. Deze "flash" wordt later weggesneden en laat het gewenste product achter.
Toepassingen:
Onderdelen met lage precisie: Open-flash mallen worden vaak gebruikt als precisie geen kritische vereiste is. Ze zijn ideaal voor het maken van onderdelen waarbij een hoge mate van maatnauwkeurigheid niet nodig is.
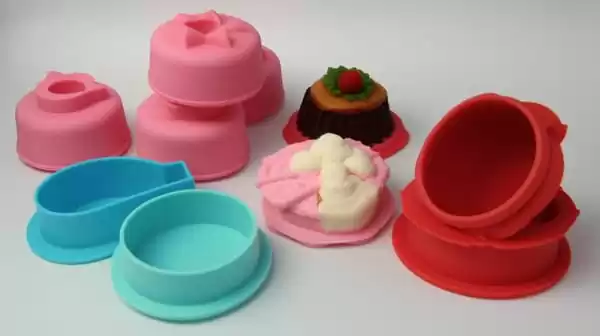
2. Gesloten mal:
Kenmerken:
Nauwkeurig: Gesloten matrijzen zijn ontworpen om een hoge mate van precisie te behouden tijdens het compressievormproces. Ze zijn ontworpen om uitvloeiing te minimaliseren en strakke toleranties in het eindproduct te garanderen.
Toepassingen:
Kritische precisie: Gesloten matrijzen vinden hun niche in toepassingen waar precisie van het grootste belang is. Ze worden gebruikt in scenario's waar productconsistentie en naleving van nauwe toleranties ononderhandelbaar zijn.
3. Half gesloten mal:
Kenmerken:
Hybride aanpak: Semi-gesloten mallen combineren elementen van zowel open als gesloten mallen. Hoewel ze enige uitvloeiing toelaten, bieden ze ook controle over de afmetingen van het product.
Toepassingen:
Evenwichtige vereisten: Semi-gesloten mallen worden gekozen als er een gematigde precisie nodig is en als vlampolthuishouding essentieel is, maar niet zo kritisch als bij gesloten mallen. Ze bieden een gebalanceerde benadering die past bij een breed scala aan productvereisten.
In essentie hangt de keuze tussen open-flash, gesloten en semi-gesloten mallen bij persen af van de specifieke eisen van het product dat gemaakt wordt. Open-flash mallen zijn geschikt als precisie niet de hoogste prioriteit heeft, gesloten mallen blinken uit in toepassingen die uiterste precisie vereisen en semi-gesloten mallen vormen een balans tussen deze twee uitersten. Door het juiste matrijstype te kiezen, kunnen fabrikanten hun compressievormprocessen optimaliseren om te voldoen aan de unieke behoeften van hun producten en industrieën.
Sectie 3: Soorten materialen voor persen
In de wereld van het persgieten is de materiaalkeuze voor persgietproducten cruciaal voor het bepalen van de eigenschappen en kenmerken van het eindproduct. Twee veelgebruikte materialen in dit proces zijn Sheet Molding Compound (SMC) en Bulk Molding Compound (BMC). Laten we ons eens verdiepen in deze materialen en de voordelen van het gebruik van thermohardende materialen bij persgieten belichten:
1. Sheet Molding Compound (SMC):
Kenmerken:
Vezelversterkt: SMC is een vezelversterkt materiaal dat thermohardende harsen combineert met gehakte glasvezels. Deze versterking geeft het materiaal een uitstekende sterkte en stijfheid.
Bladvorm: SMC wordt meestal geleverd in de vorm van vlakke platen of rollen. Deze platen zijn vooraf geïmpregneerd met hars en kunnen gemakkelijk worden gesneden en gelaagd in de vormholte.
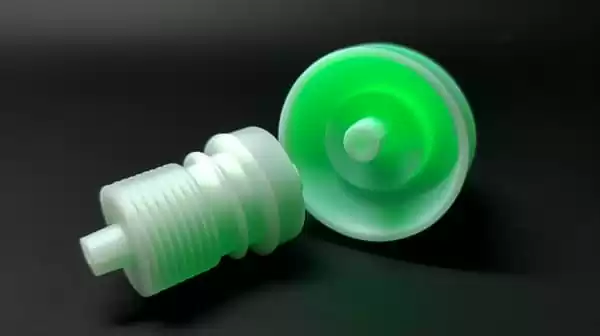
Toepassingen:
Auto-onderdelen: SMC wordt veel gebruikt in de auto-industrie om onderdelen te maken zoals carrosseriedelen, motorkappen en buitenbekleding vanwege de hoge sterkte, slagvastheid en corrosiebestendigheid.
Elektrische behuizingen: Dankzij de elektrische isolatie-eigenschappen is SMC de keuze bij uitstek voor elektrische behuizingen en panelen.
2. Bulk Molding Compound (BMC):
Kenmerken:
Thermohardend materiaal: BMC is ook een thermohardend materiaal dat bestaat uit een mengsel van thermohardende hars, vulmateriaal en versterkingsvezels (meestal glas).
Korrelvorm: In tegenstelling tot SMC wordt BMC geleverd in korrelvorm. Deze korrelige consistentie maakt nauwkeurig gieten van complexe vormen mogelijk.
Toepassingen:
Auto-industrie: BMC vindt zijn plaats in de auto-industrie voor de productie van complexe onderdelen zoals kleppendeksels, inlaatspruitstukken en onderdelen onder de motorkap. De maatvastheid en bestendigheid tegen chemicaliën en hitte maken het een ideale keuze.
Elektriciteit en elektronica: BMC wordt gebruikt in elektrische en elektronicatoepassingen vanwege de uitstekende elektrische isolatie-eigenschappen en vlambestendigheid.
Voordelen van het gebruik van thermohardende materialen bij persen:
De keuze voor thermohardende materialen, zoals die gebruikt worden in SMC en BMC, biedt verschillende voordelen in het compressievormproces:
Temperatuurbestendigheid: Thermohardende materialen blinken uit in omgevingen met hoge temperaturen. Ze zijn bestand tegen hoge temperaturen zonder te vervormen, waardoor ze geschikt zijn voor toepassingen die bestand moeten zijn tegen hitte en thermische cycli.
Chemische weerstand: Deze materialen hebben een uitstekende chemische weerstand, waardoor ze ideaal zijn voor toepassingen waarbij blootstelling aan verschillende chemicaliën wordt verwacht.
Dimensionale stabiliteit: Thermohardende materialen behouden hun vorm en afmetingen onder druk en hoge temperaturen, wat zorgt voor consistentie en precisie in het eindproduct.
Elektrische isolatie: Zowel SMC als BMC hebben uitstekende elektrische isolerende eigenschappen, waardoor ze onmisbaar zijn in elektrische en elektronicatoepassingen.
Complexe vormen: De korrelige vorm van BMC en de mogelijkheid tot gelaagdheid van SMC maken het mogelijk om complexe en ingewikkelde vormen te gieten, wat zorgt voor veelzijdigheid in het ontwerp.
Samengevat zijn Sheet Molding Compound (SMC) en Bulk Molding Compound (BMC) voorbeelden van thermohardende materialen die gebruikt worden bij het persen. Door hun inherente voordelen, zoals temperatuur- en chemische weerstand, dimensionale stabiliteit en elektrische isolatie-eigenschappen, zijn ze een waardevolle keuze bij de productie van diverse producten in verschillende industrieën. Het gebruik van deze materialen, in combinatie met de precisie van persgietenDit resulteert in hoogwaardige componenten met op maat gemaakte eigenschappen en prestaties.
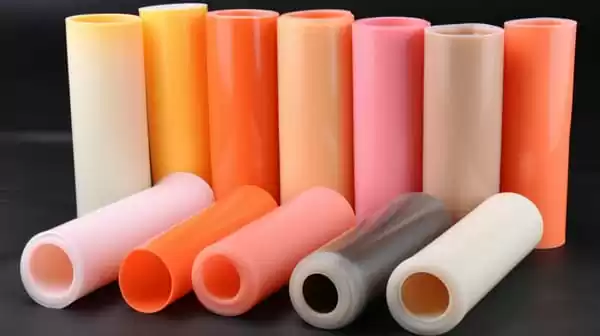
Deel 4: Het spuitgietproces zelf
Om de fijne kneepjes van het persgieten echt te begrijpen, is het essentieel om in de kern van het proces zelf te duiken. In dit deel verkennen we de essentiële onderdelen van de persmatrijs, begrijpen we de betekenis van de hoge druk en ontrafelen we het hardingsproces dat verantwoordelijk is voor het stollen van het spuitgietproduct:
1. Onderdelen van de compressiematrijs:
De persmatrijs is het hart van het persgietproces. Hij bestaat uit verschillende cruciale onderdelen:
Vormholte: Dit is waar de magie gebeurt. De vormholte bepaalt de vorm en afmetingen van het eindproduct. Hij moet nauwkeurig worden ontworpen voor de gewenste geometrie, inclusief factoren als productdikte, ontwerphoeken en oppervlakteafwerking.
Verwarmingssysteem: Compressiematrijzen zijn uitgerust met een verwarmingssysteem dat de temperatuur in de matrijsholte verhoogt. Deze verwarming is essentieel om het ruwe materiaal zacht te maken of te smelten zodat het plooibaar en vormbaar wordt.
Koelsysteem: Efficiënte koelkanalen of -systemen lopen door de matrijs om het gevormde onderdeel snel af te koelen en te laten stollen zodra het zijn vorm heeft aangenomen. Een goede koeling zorgt ervoor dat de gewenste vorm behouden blijft en voorkomt kromtrekken of vervorming.
Drukmechanisme: Compression molding staat bekend om zijn hoge druk. De matrijs bevat een mechanisme om aanzienlijke druk uit te oefenen op de matrijsholte. Deze druk is verantwoordelijk voor het verdichten van het materiaal, zorgt ervoor dat het alle hoeken en gaten van de matrijs vult en bepaalt uiteindelijk de dichtheid en structurele integriteit van het onderdeel.
2. Het hogedrukkarakter van persen:
Persgieten wordt gekenmerkt door de inherente hoge druk die een cruciale rol speelt bij het vormen van het eindproduct. Het belang van deze hogedrukomgeving ligt in verschillende aspecten:
Materiaalcompressie: De hoge druk tijdens het persen comprimeert het materiaal in de matrijsholte. Deze compressie zorgt ervoor dat het materiaal precies voldoet aan de geometrie van de matrijs, wat resulteert in uitstekende onderdeelreproductie en maatnauwkeurigheid.
Dichtheidscontrole: De druk bepaalt de dichtheid van het eindproduct. Door de druk zorgvuldig te regelen, kunnen fabrikanten specifieke materiaaldichtheden bereiken die de mechanische eigenschappen en prestaties van het onderdeel beïnvloeden.
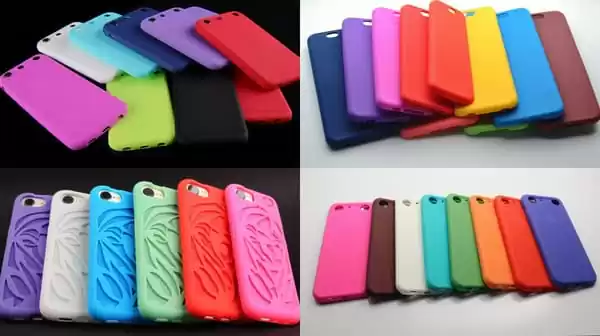
Uniforme vulling: Hoge druk helpt bij het gelijkmatig vullen van de vormholte. Dit minimaliseert het risico op holtes, luchtzakken of andere defecten in het eindproduct, wat bijdraagt aan de kwaliteit.
3. Het uithardingsproces:
Nadat het materiaal de gewenste vorm heeft aangenomen in de matrijsholte, komt het uithardingsproces om de hoek kijken. Uitharden is de stap die verantwoordelijk is voor het stollen van het gevormde onderdeel en het zijn uiteindelijke structurele integriteit geeft. Zo werkt het:
Hitte en druk: De verhoogde temperatuur in de mal, in combinatie met de toegepaste druk, veroorzaakt een chemische reactie in het thermohardende materiaal. Deze reactie zorgt ervoor dat het materiaal hard wordt en zijn vorm aanneemt.
Koeling: Zodra het uithardingsproces is voltooid, wordt het koelsysteem van de mal geactiveerd om de temperatuur snel te verlagen. Deze koelfase helpt bij het stollen van het onderdeel, waardoor het stijf wordt en klaar is om uit de mal te worden geworpen.
Concluderend kan gesteld worden dat het begrijpen van de onderdelen van de persmatrijs, de betekenis van de hogedrukomgeving en het uithardingsproces waardevolle inzichten verschaft in de mechanica van het persgieten. Dit ingewikkelde samenspel van warmte, druk en precisietechniek maakt de productie mogelijk van hoogwaardige componenten met de gewenste vorm, dichtheid en mechanische eigenschappen. Het is de belichaming van uitmuntende productie en levert producten die voldoen aan de hoogste normen op het gebied van prestaties en betrouwbaarheid.
Hoofdstuk 5: De vormholte ontwerpen
De matrijsholte vormt het hart van het compressievormproces. In dit deel verkennen we de kritieke rol van het ontwerp van de matrijsholte, definiëren we het ontwerp van een compressiematrijs en gaan we dieper in op de berekening van tonnage - een cruciale factor bij het persen:
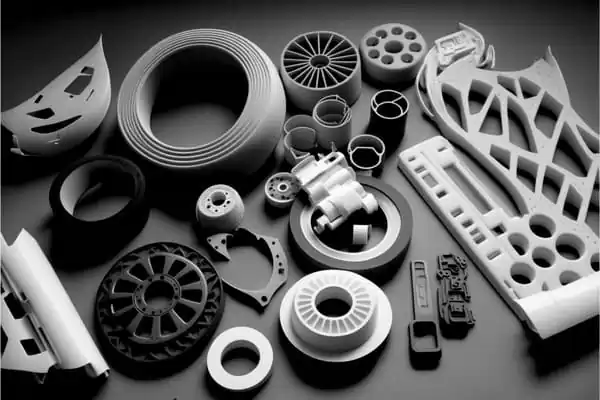
1. Het belang van het ontwerp van de vormholte:
Het ontwerp van de matrijsholte is van het grootste belang voor het succes van het compressievormproces. Dit is waarom het zo belangrijk is:
Precisie en consistentie: De vormholte bepaalt de uiteindelijke vorm en afmetingen van het product. Een goed ontworpen matrijsholte garandeert precisie en consistentie in elk gevormd stuk en voldoet aan de hoogste kwaliteitsnormen.
Materiaalstroom: De geometrie van de matrijsholte bepaalt hoe het materiaal stroomt en de matrijs vult. Een verkeerd ontwerp kan leiden tot een ongelijkmatige verdeling van het materiaal, met defecten of onregelmatigheden in het eindproduct tot gevolg.
Ventilatie en koeling: Effectieve ontluchtingskanalen of groeven in de matrijsholte laten opgesloten lucht en gassen ontsnappen, waardoor defecten zoals luchtzakken worden voorkomen. Het koelsysteem in de holte helpt om het onderdeel snel te laten stollen, waardoor de cyclustijden korter worden.
Afwerking oppervlak: Het ontwerp van de matrijsholte speelt ook een rol bij het verkrijgen van de gewenste oppervlakteafwerking op het spuitgietproduct. Het kan gepolijst, gestructureerd of gecoat worden om aan specifieke esthetische en functionele eisen te voldoen.
2. Wat is een compressiematrijs ontwerpen?
Ontwerp van compressiematrijzen is het proces van het nauwgezet creëren van een matrijsholte die bestand is tegen de hoge druk en temperaturen die inherent zijn aan compressievormen. Het omvat verschillende kritieke aspecten:
Meetkunde: De matrijsholte moet precies overeenkomen met de vorm van het eindproduct. Dit houdt ook in dat rekening moet worden gehouden met de dikte van het product, de ontwerphoeken en ondersnijdingen voor een soepele uitwerping.
Ontluchting: Door de juiste ontluchtingskanalen of groeven kunnen ingesloten lucht en gassen tijdens het gieten ontsnappen, waardoor defecten zoals luchtzakken of holtes in het eindproduct worden voorkomen.
Afscheidszin: De deellijn geeft aan waar de matrijs zich splitst om het gevormde onderdeel vrij te geven. Het moet goed gedefinieerd zijn en onopvallend voor de esthetiek en functionaliteit van het product.
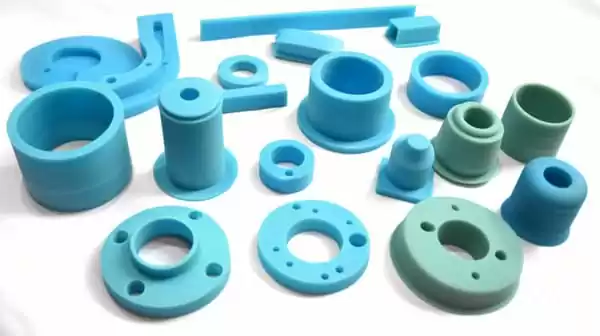
Poortontwerp: De poort dient als het punt waardoor het gesmolten materiaal de matrijsholte binnenkomt. Een zorgvuldig poortontwerp zorgt voor een gelijkmatige vulling en minimaliseert defecten. Poorttypes zijn onder andere randpoorten, pinpoorten en tunnelpoorten.
Koelsysteem: Efficiënte koelkanalen in de matrijs helpen om het gevormde onderdeel snel te laten stollen, voorkomen kromtrekken of vervormen en verbeteren de cyclustijden.
Afwerking oppervlak: Afhankelijk van de vereisten van het product kan de oppervlakteafwerking van de matrijsholte gepolijst, getextureerd of gecoat worden om de esthetiek van het eindproduct te verbeteren.
3. Hoe tonnage berekenen voor persen:
Tonnage in persgieten verwijst naar de kracht die nodig is om het materiaal in de matrijsholte samen te drukken. Het is een cruciale factor bij het bereiken van de juiste materiaalcompressie en onderdeeldichtheid. Om de tonnage te berekenen, kun je de volgende formule gebruiken:
Tonnage = Druk × Oppervlakte
Druk: Druk wordt meestal gemeten in PSI (Pounds per Square Inch).
Gebied: Area vertegenwoordigt de geprojecteerde oppervlakte van het spuitgietproduct.
Door de vereiste tonnage te berekenen, kunnen fabrikanten ervoor zorgen dat de pers die gebruikt wordt in het compressievormproces de nodige kracht uitoefent om de gewenste compressie en dichtheid van het materiaal in de matrijsholte te bereiken.
In wezen is het ontwerp van de matrijsholte de hoeksteen van succesvol persgieten. Het bepaalt de productkwaliteit, precisie en consistentie. Het ontwerp van compressiematrijzen omvat geometrie, ontluchting, deellijnen, poortontwerp, koelsystemen en oppervlakteafwerking - allemaal afgestemd op de specifieke vereisten van het gewenste onderdeel. Het begrijpen en berekenen van tonnage zorgt er verder voor dat het compressievormproces optimaal werkt en hoogwaardige componenten produceert die voldoen aan de industrienormen of deze zelfs overschrijden.
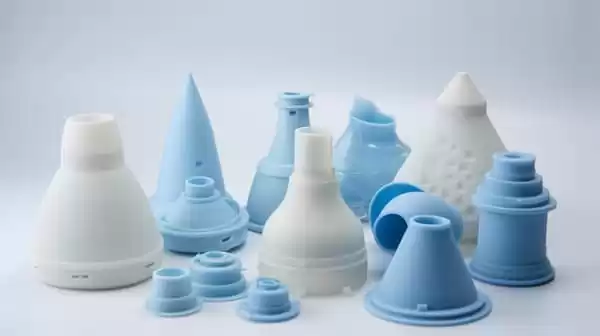
Conclusie
In deze uitgebreide verkenning van compressievormen en het ontwerp van matrijsholtes hebben we de ingewikkelde wereld blootgelegd van een productieproces dat een onuitwisbare stempel drukt op een groot aantal industrieën.
Nu we onze verkenning afsluiten, moedigen we de lezers aan om compressievormen te overwegen voor hun productiebehoeften. De precisie, veelzijdigheid en het vermogen om componenten van hoge kwaliteit te leveren, maken het een proces dat het waard is om te onderzoeken voor een breed scala aan toepassingen. Door compressievormen te omarmen en de kracht van het juiste ontwerp van de vormholte te benutten, kunnen fabrikanten een wereld van mogelijkheden ontsluiten en producten maken die niet alleen voldoen aan de hoogste productienormen, maar deze zelfs overtreffen.