A estrutura dos moldes de injeção de borracha de silicone líquido termoendurecível (LSR) é geralmente semelhante à dos moldes utilizados para compostos termoplásticos, mas existem várias diferenças significativas.
Por exemplo, os compostos LSR têm geralmente uma baixa viscosidade e, por conseguinte, tempos de enchimento muito curtos, mesmo a pressões de injeção muito baixas. Para evitar o aprisionamento de ar, é essencial ter um bom dispositivo de ventilação no molde.
Para além disso, os compostos de LSR não encolhem tanto como os compostos termoplásticos no molde; tendem a expandir-se quando estão quentes e a encolher ligeiramente quando estão frios. Como resultado, o produto nem sempre permanece no lado convexo do molde como esperado, mas é retido na cavidade com uma área de superfície maior.
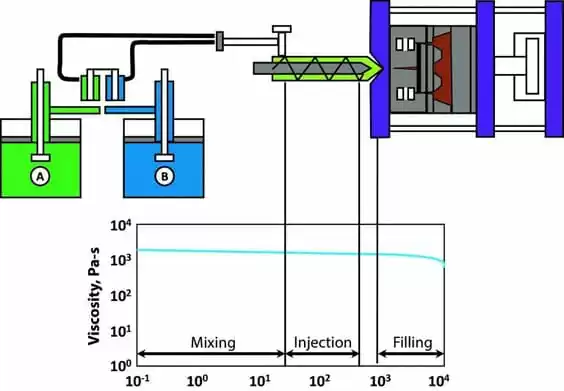
1. Retração
Apesar de os LSR não encolherem no molde, encolhem frequentemente entre 2,5% e 3% após a desmoldagem e o arrefecimento. A quantidade exacta de retração depende, em certa medida, da formulação desse composto.
No entanto, do ponto de vista do molde, a retração pode ser influenciada por vários factores, incluindo a temperatura do molde, a temperatura do composto quando é desmoldado, bem como a pressão na cavidade do molde e a subsequente compressão do composto.
Também vale a pena considerar a localização do ponto de injeção, uma vez que a retração na direção do fluxo da cola é normalmente maior do que a retração na direção perpendicular ao fluxo da cola.
O tamanho do produto também afecta o seu encolhimento, sendo que os produtos mais espessos têm geralmente menos encolhimento do que os mais finos. Se for necessária uma vulcanização secundária, o encolhimento pode ser de mais 0,5%-0,7%.
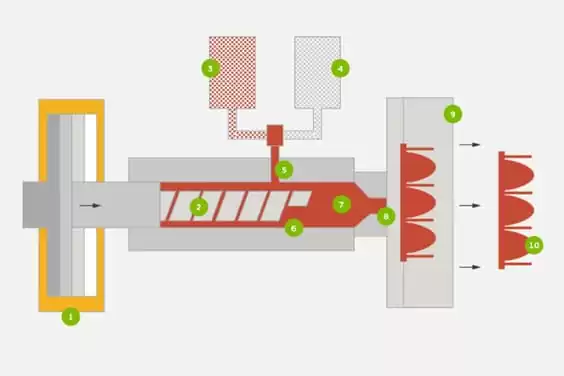
2. Linha de separação
A determinação da localização da linha de partição é um dos primeiros passos na conceção de um molde de injeção de borracha de silicone. A ventilação é conseguida principalmente através de ranhuras localizadas na linha de separação, que deve estar na área onde o composto de injeção irá durar. Isto ajuda a evitar bolhas de ar internas e a reduzir a perda de resistência na junta de colagem.
Devido à baixa viscosidade do LSR, a linha de separação deve ser exacta para evitar derrames. Mesmo assim, as linhas de partição podem ser frequentemente vistas em produtos moldados. A libertação do molde é influenciada pela geometria da peça e pela posição da superfície de separação. A conceção da peça com um ligeiro chanfro ajudará a garantir uma afinidade consistente com a outra metade da peça desejada. molde de injeção cavidade.
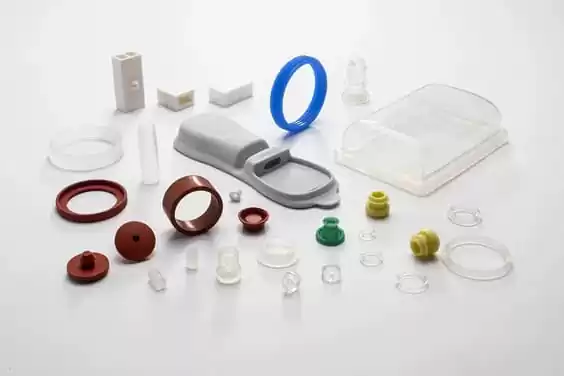
3. Ventilação
À medida que o LSR é injetado, o ar preso na cavidade é comprimido à medida que o molde se fecha e depois expulso através das ranhuras de ventilação à medida que o molde se enche.
Se o ar não for completamente expelido, ficará retido no adesivo (o que resulta frequentemente numa parte do produto com bordos brancos). As ranhuras de ventilação têm geralmente mm-3mm de largura e 0,004mm-0,005mm de profundidade.
O melhor efeito de ventilação pode ser criado através da aspiração no interior do molde. Isto é conseguido concebendo uma junta na linha de separação e evacuando rapidamente todas as cavidades para o vácuo com uma bomba de vácuo. Quando o vácuo atinge o nível nominal, o molde é totalmente fechado e a prensa de injeção começa.
Alguns equipamentos de moldagem por injeção permitem o funcionamento com forças de fecho variáveis, o que permite ao processador fechar o molde a baixa pressão até que 90-95% da cavidade esteja preenchida com LSR (facilitando a saída de ar) e, em seguida, mudar para uma força de fecho mais elevada para evitar borracha de silicone expansão e transbordo.
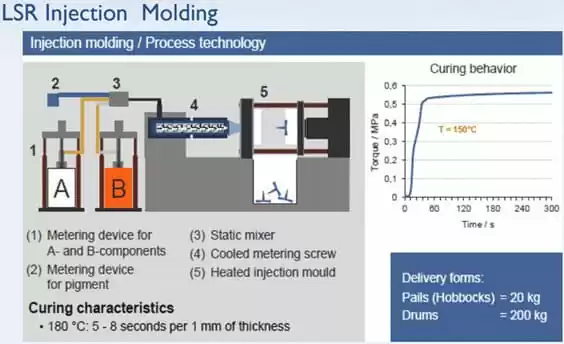
4. Ponto de injeção
Um sistema de canal frio é utilizado na moldagem de LSR. As vantagens deste sistema borracha de silicone pode ser maximizada e a eficiência da produção pode ser aumentada ao máximo.
Ao processar os produtos desta forma, não é necessário remover o canal de injeção, evitando assim o aumento de mão de obra para a operação e, por vezes, uma grande quantidade de desperdício de material. Em muitos casos, a construção sem canal também reduz o tempo de operação.
O bico de injeção é controlado por uma válvula de agulha para um fluxo positivo, e muitos fabricantes oferecem agora bicos com interruptores pneumáticos como equipamento de série e podem ser instalados em várias partes do molde.
Alguns molde de injeção Os fabricantes desenvolveram um sistema aberto de canal frio que é tão pequeno que vários pontos de injeção (e, por conseguinte, toda a cavidade) têm de ser colocados num espaço de molde muito limitado.
Esta tecnologia permite produzir grandes quantidades de produtos de alta qualidade produtos de borracha de silicone sem ter de separar os orifícios de injeção.
Se for utilizado um sistema de canal frio, é importante criar uma separação efectiva da temperatura entre a cavidade quente e o canal frio. Se o canal estiver demasiado quente, a borracha pode começar a vulcanizar antes de ser injectada. Mas se arrefecer muito rapidamente, absorverá demasiado calor da área do canal de injeção do molde de injeção, resultando numa vulcanização incompleta.
Para os produtos injectados com um jito convencional (por exemplo, jito submerso e jito cónico), é adequado utilizar um orifício de injeção de pequeno diâmetro (normalmente 0,2 mm-0,5 mm) para a injeção.
Com compostos LSR de baixa viscosidade, tal como com compostos termoplásticos, é importante equilibrar o sistema de canais para que todas as cavidades sejam preenchidas uniformemente com o composto. O software de simulação para a conceção do sistema de canais pode simplificar bastante o desenvolvimento do molde e provar a sua eficácia através de testes de enchimento do molde.
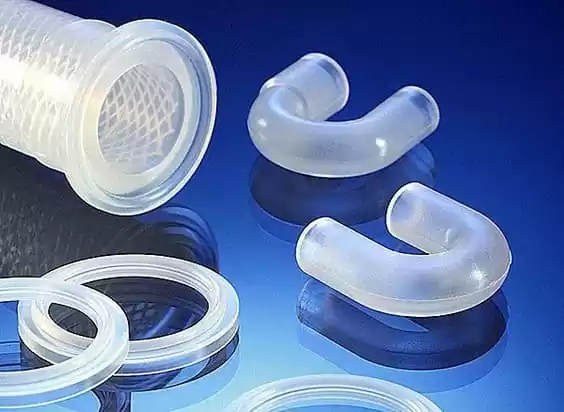
5. Desmoldagem
A moldagem de silicone líquido, através da vulcanização, tende a aderir à superfície do metal, e a flexibilidade do produto pode dificultar a sua libertação. A resistência ao rasgamento a altas temperaturas do LSR permite a sua libertação em condições normais sem danificar mesmo os produtos de maiores dimensões.
As técnicas de libertação mais comuns incluem a libertação da placa de decapagem, a libertação do pino de decapagem e a libertação pneumática. Outras técnicas comuns são a raspagem com rolo, a libertação da placa de exportação e a libertação automática do molde.
Quando se utiliza um sistema de desbloqueio, é importante mantê-lo dentro de um elevado grau de precisão. Se houver uma folga demasiado grande entre o pino de pressão superior e a manga do pino de guia, ou se o espaço entre as peças se tornar grande devido ao desgaste ao longo do tempo, pode ocorrer derrame de cola.
A cavilha superior cónica invertida ou em forma de cogumelo é muito eficaz porque permite a aplicação de uma maior pressão de contacto e facilita a melhoria da finalidade da vedação.
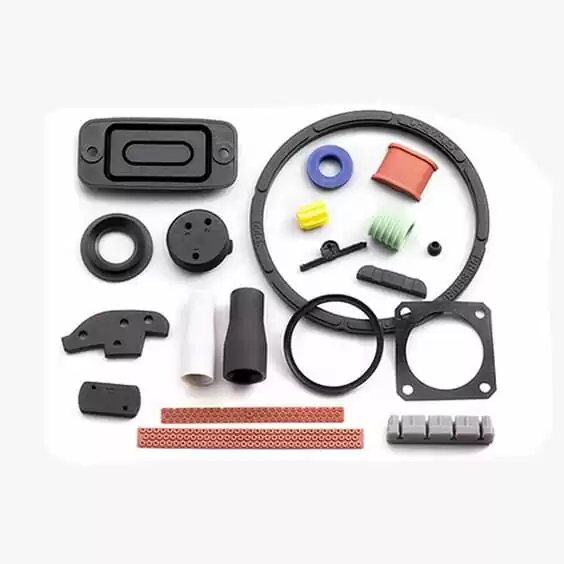
6. Material do molde
Os paletes de molde são frequentemente feitos de aço ferramenta não ligado (no.1.1730, código DIN C45W). Para paletes de molde que precisam suportar a alta temperatura de 170 ℃ -210 ℃, eles devem ser feitos de aço pré-temperado (no.1.2312, código DIN 40 CrMn-M oS 8 6) em consideração à resistência ao impacto.
No caso de paletes de moldes com cavidades no molde, estas devem ser feitas de aço etil-ferramenta nitretado ou temperado termicamente para garantir a sua resistência a altas temperaturas.
Para os LSRs com elevada capacidade de enchimento, como os LSRs de grau resistente ao óleo, recomenda-se a utilização de materiais mais duros para o fabrico dos moldes, como o aço cromado brilhante ou o metal em pó especialmente desenvolvido para o efeito (n.º 1.2379, DINcode X 155 CrVMo121).
Ao conceber moldes de injeção para materiais de elevado desgaste, as peças sujeitas a elevado atrito devem ser concebidas para serem formadas de forma substituível, de modo a que o molde inteiro não tenha de ser substituído.
A superfície interna da cavidade do molde tem um impacto significativo no acabamento do produto. O mais óbvio é o facto de o produto moldado corresponder perfeitamente à superfície da cavidade. Moldes de injeção para produtos transparentes devem ser feitas de aço polido. O aço Chin/Níquel com tratamento de superfície é extremamente resistente ao desgaste, enquanto o PTFE/Níquel facilita a libertação do molde.
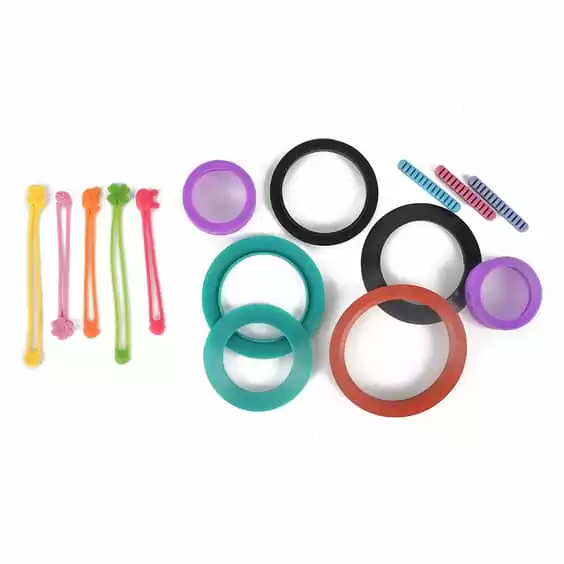
7. Controlo da temperatura
De um modo geral, é preferível que a moldagem de LSR seja aquecida por aquecimento elétrico, normalmente por aquecedores de banda, aquecedores de cartucho ou placas de aquecimento.
A chave é fazer com que o campo de temperatura seja distribuído uniformemente por todo o molde para promover a cura uniforme do LSR. Em moldes de grandes dimensões, é um método de aquecimento económico quando se utiliza o aquecimento por controlo da temperatura do óleo.
Envolver o molde com uma placa isolante ajuda a reduzir a perda de calor. A inadequação de qualquer parte do molde quente pode fazer com que este sofra grandes flutuações de temperatura entre os processos de funcionamento ou causar fugas de ar.
Se a temperatura da superfície descer demasiado, a velocidade de cura da cola será reduzida, o que muitas vezes impede que o produto seja libertado da molde de injeção e causa problemas de qualidade.
Deve ser mantida uma certa distância entre o aquecedor e a linha de separação para evitar que o molde se dobre e se deforme e forme uma rebarba de cola de transbordo no produto acabado. Se o molde for projetado com um sistema de canal frio, a extremidade quente e a extremidade fria devem estar completamente separadas uma da outra.
Podem ser utilizadas ligas especiais de aço Chin (por exemplo, 3.7165 [TiA16V4]), devido à sua condutividade térmica muito mais baixa em comparação com outros aços. Para um sistema de aquecimento integral do molde de injeção, o escudo térmico deve ser colocado entre o molde e a palete do molde para minimizar a perda de calor. O design e a conceção adequados podem garantir a moldagem por injeção de LSR, em que o molde é muito importante.
Os princípios de conceção do molde acima referidos têm como objetivo encher a cavidade do molde com borracha, encurtar o tempo de cura e obter uma qualidade superior e um elevado rendimento do produto acabado, proporcionando assim o líquido moldagem de borracha de silicone processador com bons benefícios económicos.