Introdução:
A moldagem por compressão é um processo de fabrico amplamente utilizado em várias indústrias, incluindo a automóvel, a aeroespacial e a de bens de consumo. Envolve a aplicação de calor e pressão para moldar materiais como os termoplásticos e os polímeros termoendurecíveis nas formas pretendidas. O processo oferece várias vantagens, incluindo a capacidade de produzir peças complexas com excelente estabilidade dimensional e propriedades mecânicas.
Em qualquer processo de fabrico, a redução do tempo de ciclo é um objetivo crítico. O tempo de ciclo refere-se ao tempo total necessário para completar um ciclo de moldagem, incluindo o carregamento do material, a compressão, o arrefecimento e a ejeção da peça. Ao minimizar o tempo de ciclo, os fabricantes podem melhorar a produtividade, aumentar a produção e otimizar a eficiência dos custos.
A importância da redução do tempo de ciclo na moldagem por compressão não pode ser exagerada. Tempos de ciclo mais curtos traduzem-se diretamente em taxas de produção mais rápidas e custos reduzidos por peça. Os fabricantes podem satisfazer as exigências dos clientes de forma mais eficiente e ganhar uma vantagem competitiva no mercado.
Além disso, a redução do tempo de ciclo em moldagem por compressão oferece benefícios que vão para além do aumento da produtividade e da eficiência de custos. Pode conduzir a uma maior eficiência energética, à diminuição do desgaste do equipamento e a uma maior sustentabilidade, reduzindo o consumo global de energia e a pegada de carbono do processo de fabrico.
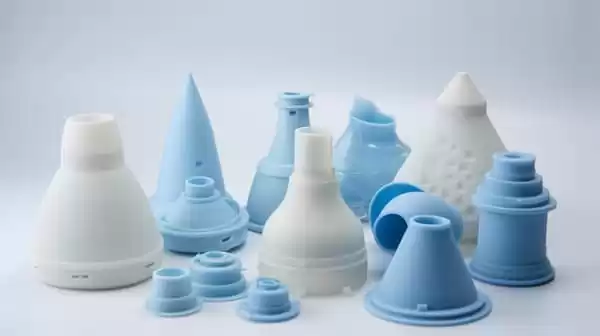
Neste artigo, iremos aprofundar estratégias eficazes para otimizar o processo de moldagem por compressão, de modo a obter reduções significativas no tempo de ciclo. Ao implementar estas estratégias, os fabricantes podem desbloquear todo o potencial da moldagem por compressão e impulsionar as suas operações para um maior sucesso.
II. Compreender o processo de moldagem por compressão
A moldagem por compressão é um processo de fabrico que envolve a utilização de calor e pressão para moldar os materiais nas formas pretendidas. É amplamente utilizado para uma variedade de aplicações, incluindo produção de componentes para automóveis, caixas eléctricas e bens de consumo.
Principais caraterísticas da moldagem por compressão:
1. aplicação de calor e pressão: A moldagem por compressão aplica calor e pressão ao material, fazendo com que este flua e se adapte à forma da cavidade do molde.
2. processo em estado sólido: Ao contrário de processos como o processo de moldagem por injeção, em que o material se encontra no estado fundido, a moldagem por compressão utiliza matérias-primas sólidas, tais como grânulos, pré-formas ou materiais em folha.
3. controlo preciso da colocação do material: O material é colocado numa quantidade pré-determinada na cavidade do molde, garantindo precisão e consistência no produto final.
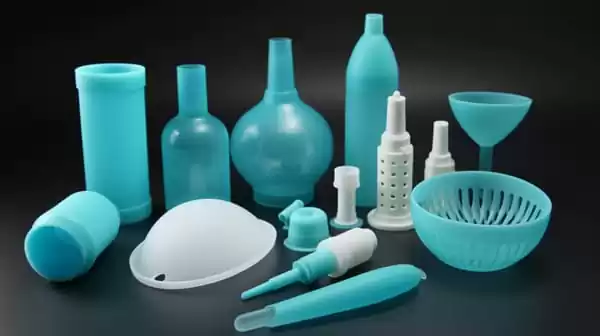
4. processo de arrefecimento lento: Em comparação com outros processos de moldagem, a moldagem por compressão tem normalmente um processo de arrefecimento mais lento devido à natureza do material em estado sólido e às secções mais espessas da peça moldada.
Diferenças entre a moldagem por compressão e outros processos de moldagem:
1. moldagem por injeção: Na moldagem por injeção, o material é derretido e injetado no molde sob alta pressão. É adequada para produção de grandes volumes, geometrias complexas e tempos de ciclo rápidos. Em contrapartida, a moldagem por compressão é mais adequada para volumes de produção mais baixos, peças maiores e mais espessas e materiais que não podem ser facilmente fundidos.
2) Moldagem por transferência de resina (RTM): A RTM envolve a injeção de resina numa cavidade de molde fechada com materiais de reforço. É normalmente utilizada para a produção de vários materiais compósitos e peças com propriedades de elevada resistência e leveza. Moldagem por compressãoPor outro lado, não envolve a injeção de resina no molde, mas sim a aplicação de calor e pressão no material previamente colocado.
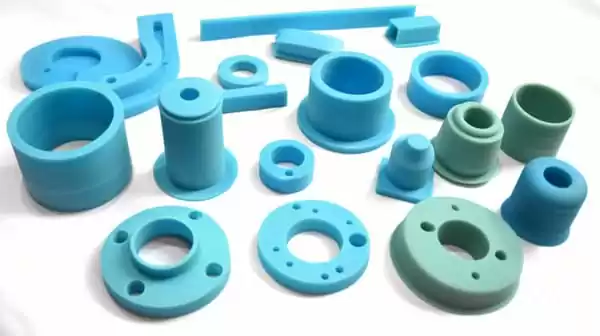
3. fluxo e distribuição de material: Na moldagem por injeção, o material fundido é forçado a fluir e a preencher as cavidades do molde, garantindo detalhes intrincados e formas complexas. Na moldagem por compressão, o fluxo e a distribuição do material ocorrem devido à pressão aplicada, resultando em geometrias de peças menos complexas.
4. tempo de ciclo: A moldagem por injeção tem geralmente tempos de ciclo mais curtos em comparação com a moldagem por compressão devido ao arrefecimento rápido do material fundido. Moldagem por compressãoO processo de arrefecimento mais lento pode exigir mais tempo por ciclo.
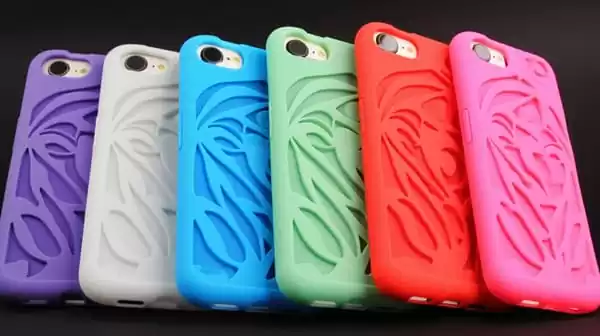
Compreender as caraterísticas e diferenças entre a moldagem por compressão e outros processos de moldagem é essencial para determinar o método mais adequado para requisitos de fabrico específicos. Ao selecionar o processo de moldagem adequado, os fabricantes podem obter resultados óptimos em termos de complexidade da peça, volume de produção e eficiência do tempo de ciclo.
III. Factores que afectam o tempo de ciclo na moldagem por compressão
O tempo de ciclo na moldagem por compressão é influenciado por vários factores que têm impacto na duração global do processo de moldagem. Compreender estes factores e os seus efeitos é crucial para otimizar o tempo de ciclo e aumentar a produtividade nas operações de moldagem por compressão. Vamos explorar os principais factores que influenciam o tempo de ciclo da moldagem por injeção e discutir o impacto da seleção do material, o design da máquina de moldagem por injeção, os parâmetros do processo e o tempo de arrefecimento:
1. seleção do material:
A escolha do material afecta significativamente o tempo de ciclo na moldagem por compressão. Os diferentes materiais têm caraterísticas de fluxo, tempos de cura e taxas de arrefecimento variáveis. Os materiais com menor viscosidade e tempos de cura mais rápidos permitem um enchimento mais rápido da cavidade do molde e tempos de ciclo mais curtos. É importante selecionar materiais que equilibrem as propriedades de fluxo com as propriedades mecânicas e térmicas desejadas para a peça moldada final.
2.Conceção de moldes:
A conceção do molde desempenha um papel crucial na otimização do tempo de ciclo. Eficiente conceção do molde assegura um fluxo de material adequado e uma perda mínima de calor durante o processo de moldagem. Factores como o número e a complexidade das cavidades, os sistemas de ventilação e a conceção das comportas influenciam as fases de enchimento e arrefecimento, afectando, em última análise, o tempo de ciclo. Moldes bem concebidos facilitam um arrefecimento mais rápido e uniforme, resultando em tempos de ciclo mais curtos.
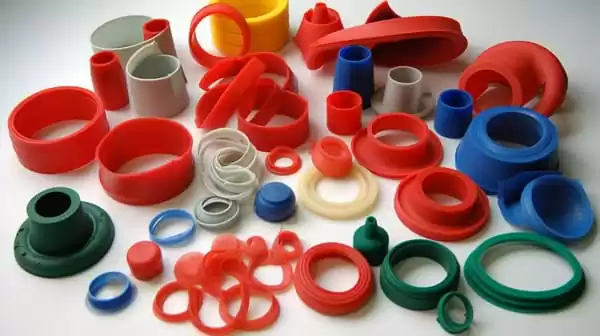
3.Parâmetros do processo:
A otimização dos parâmetros do processo tem um impacto significativo no tempo de ciclo. Parâmetros como a temperatura, a pressão e as definições de tempo influenciam diretamente o fluxo de material, a cura e as fases de arrefecimento. Ao afinar estes parâmetros, os fabricantes podem identificar a combinação ideal que minimiza o tempo de ciclo, mantendo a qualidade desejada das peças moldadas. A experimentação exaustiva e a análise do processo são essenciais para determinar os parâmetros críticos de processamento que afectam o tempo de ciclo.
4.Tempo de arrefecimento:
O tempo de arrefecimento é uma fase crítica na moldagem por compressão que afecta o tempo de ciclo. O processo de arrefecimento permite que a peça moldada solidifique e atinja as propriedades mecânicas necessárias. A espessura e a complexidade da peça, bem como a condutividade térmica do material, influenciam o tempo de arrefecimento. Técnicas de arrefecimento eficientes, como a utilização de canais de arrefecimento ou a implementação de métodos de arrefecimento rápido, podem ajudar a reduzir o tempo de arrefecimento e o tempo de ciclo global.
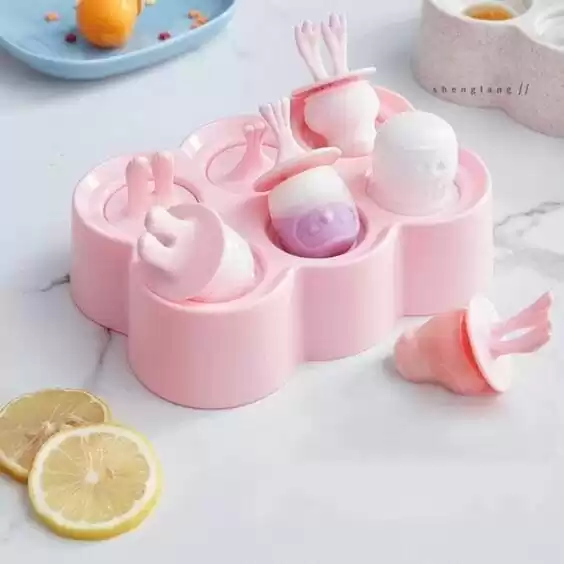
Ao considerar cuidadosamente a seleção de materiais, conceção do moldeCom a otimização dos parâmetros do processo e do tempo de arrefecimento, os fabricantes podem reduzir significativamente o tempo de ciclo na moldagem por compressão. A otimização destes factores assegura ciclos de produção mais rápidos, maior produtividade e melhor eficiência de custos. É essencial realizar uma análise minuciosa, experimentação e melhoria contínua do processo para identificar as condições ideais que minimizam o tempo de ciclo, mantendo a qualidade desejada das peças moldadas.
IV. Estratégias para otimizar o processo de moldagem por compressão
A. Seleção de materiais e otimização dos parâmetros do processo
A seleção de materiais e a otimização dos parâmetros do processo são passos cruciais para otimizar a processo de moldagem por compressão e reduzir o tempo de ciclo. Estas estratégias contribuem para melhorar a produtividade e a eficiência dos custos.
1.Destacar a importância da seleção de materiais e o seu impacto no tempo de ciclo:
Discuta a importância de escolher materiais com caraterísticas de fluxo favoráveis, tempos de cura rápidos e elevada estabilidade dimensional.
Explicar como os materiais com menor viscosidade facilitam um enchimento mais rápido da cavidade do molde, levando a tempos de ciclo mais curtos.
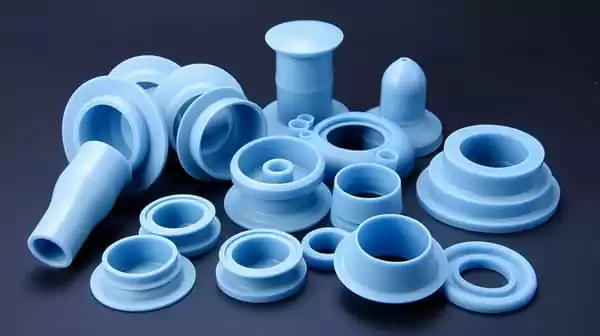
2. explicar o significado da otimização dos parâmetros do processo para reduzir o tempo de ciclo:
1. realçar o papel das definições de temperatura, pressão e tempo no processo de processo de moldagem por compressão.
2. realçar a importância de realizar experiências exaustivas para identificar a combinação óptima de parâmetros de processo que minimizem o tempo de ciclo sem comprometer a qualidade da peça.
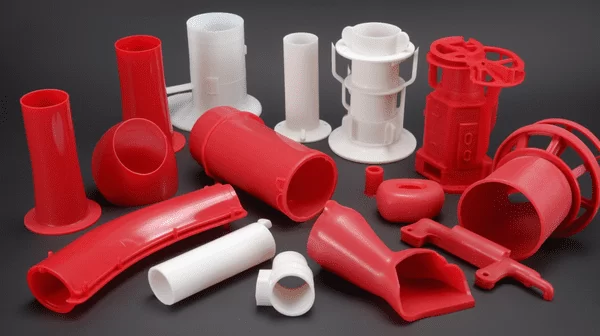
B. Conceção do molde e controlo da temperatura
A conceção do molde e o controlo da temperatura são factores críticos para conseguir tempos de ciclo mais curtos em moldagem por compressão.
1) Discutir o papel da conceção do molde na obtenção de um tempo de ciclo mais curto:
Explique como um design de molde eficiente optimiza o fluxo de material e minimiza a perda de calor durante o processo de moldagem.
Salientar a importância de uma ventilação adequada, de sistemas de fecho e da conceção da cavidade para uma evacuação rápida do ar e um enchimento fácil.
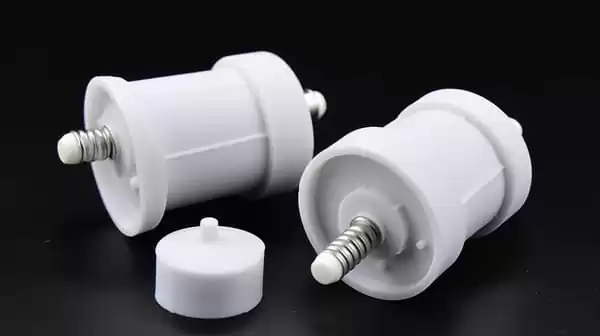
2.explicar a importância do controlo adequado da temperatura do molde e o impacto no tempo de ciclo:
Discuta como a temperatura do molde afecta o fluxo de material, a cura e as fases de arrefecimento.
Salientar a importância de manter o molde à temperatura adequada para acelerar a cura e reduzir o tempo de ciclo.
C. Automatização, ferramentas rápidas e tempo de mudança de molde
Automação, ferramentas rápidas e processos eficientes de troca de moldes contribuem para a redução do tempo de ciclo e para o aumento da produtividade na moldagem por compressão.
1) Discutir os benefícios da automatização e da robótica na moldagem por compressão:
Explicar como a automação e a robótica agilizam o carregamento de material, o fecho de moldes e a ejeção de peças, conduzindo a tempos de ciclo mais rápidos.
Salientar as vantagens da precisão e da rapidez dos sistemas automatizados em relação ao trabalho manual.
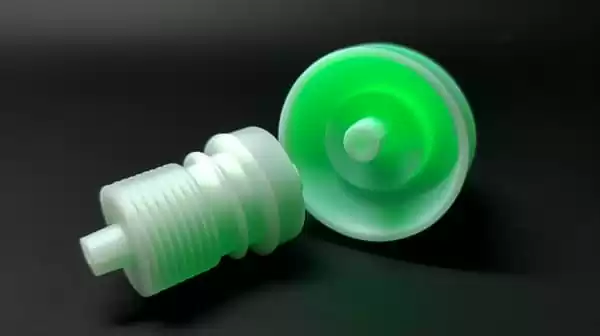
2. realçar a importância das técnicas de fabrico rápido de ferramentas e dos processos eficientes de mudança de molde:
Explicar como as técnicas de ferramentas rápidas minimizam o tempo de troca de moldes, permitindo transições mais rápidas entre diferentes moldes.
Discuta os benefícios de uma coordenação eficiente entre equipas, procedimentos de ferramentas simplificados e mudanças de molde bem planeadas.
D. Tempo de arrefecimento e otimização
A redução do tempo de arrefecimento é um aspeto crucial da otimização do tempo de ciclo em moldagem por compressão.
1. explicar a importância de reduzir o tempo de arrefecimento na moldagem por compressão:
Destacar a forma como o tempo de arrefecimento afecta o tempo total do ciclo e a eficiência da produção.
Discuta como um arrefecimento mais rápido leva a tempos de ciclo mais curtos e a uma maior produtividade.
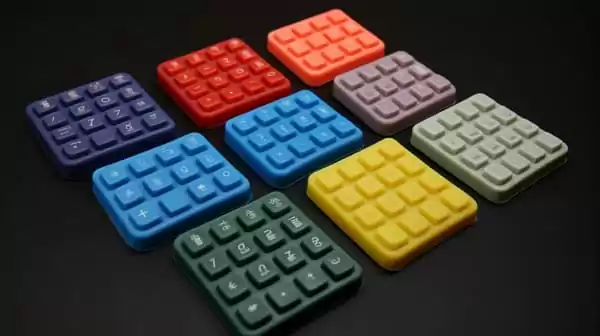
2.Discutir diferentes técnicas de arrefecimento e o seu impacto no tempo de ciclo:
Explore métodos como o arrefecimento a água ou a ar que aceleram a solidificação de peças moldadas, destacando as vantagens e considerações de cada técnica de arrefecimento em termos de redução do tempo de ciclo.
E. Melhoria contínua dos processos e análise de dados
A melhoria contínua do processo e a análise de dados são essenciais para otimizar o processo de moldagem por compressão e reduzir o tempo de ciclo.
1. realçar a importância da melhoria contínua na redução do tempo de ciclo:
Discuta os benefícios de uma abordagem proactiva para identificar e implementar melhorias nos processos.
Salientar a importância de monitorizar e analisar regularmente o desempenho do processo.
2 - Discutir o papel da análise de dados e da otimização do processo na obtenção de parâmetros óptimos de moldagem por compressão:
Explicar como é que a tomada de decisões baseada em dados melhora o tempo de ciclo e a eficiência global do processo.
Discutir a utilização de métodos de controlo estatístico de processos e técnicas de análise de dados para identificar tendências e otimizar parâmetros críticos de processamento.
Ao implementar estas estratégias para otimizar o processo de moldagem por compressãoCom o processo de moldagem por compressão, os fabricantes podem obter reduções significativas no tempo de ciclo, aumentar a produtividade e obter eficiência de custos. A melhoria contínua, a análise de dados e a integração de técnicas de automatização e de ferramentas rápidas são elementos-chave para alcançar os parâmetros ideais de moldagem por compressão e a eficiência global do processo
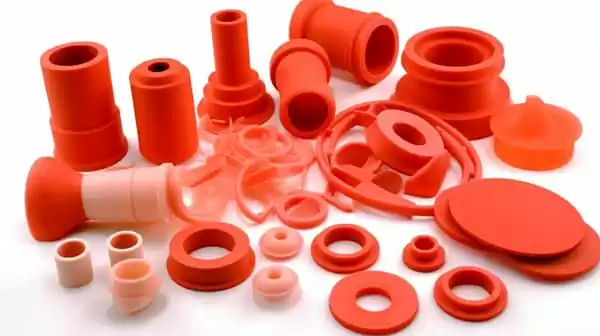
Conclusão
Neste artigo, explorámos estratégias para otimizar o processo de moldagem por compressão para reduzir o tempo de ciclo, aumentando a produtividade e a eficiência de custos. Discutimos os principais factores que influenciam o tempo de ciclo, incluindo a seleção do material, a conceção do molde, os parâmetros do processo e o tempo de arrefecimento. Ao abordar estes factores, os fabricantes podem melhorar significativamente as suas operações de moldagem por compressão.
A otimização da seleção de materiais e dos parâmetros do processo é crucial para a redução do tempo de ciclo. A escolha de materiais com caraterísticas de fluxo favoráveis e a otimização dos parâmetros de processamento ideais, como as definições de temperatura, pressão e tempo, contribuem para fases mais rápidas de enchimento, cura e arrefecimento, levando a tempos de ciclo mais curtos sem comprometer a qualidade da peça.
A conceção do molde e o controlo da temperatura desempenham um papel fundamental na obtenção de tempos de ciclo mais curtos. A conceção de moldes eficientes optimiza o fluxo de material, minimiza a perda de calor e assegura um arrefecimento uniforme. O controlo adequado da temperatura do molde acelera a cura e o arrefecimento, reduzindo ainda mais o tempo de ciclo.
Automação, ferramentas rápidas e processos eficientes de troca de moldes simplificam a operação de moldagem, minimizando o trabalho manual e o tempo de inatividade. A integração da automação e da robótica aumenta a produtividade e assegura operações precisas e rápidas. As técnicas de ferramentas rápidas e as mudanças de molde bem planeadas permitem transições mais rápidas entre moldes, maximizando o tempo de produção.
A redução do tempo de arrefecimento é um aspeto crítico do tempo de ciclo e do próprio processo de otimização. A implementação de técnicas de arrefecimento eficientes e a utilização de métodos de arrefecimento avançados, como os canais de arrefecimento conformes, aceleram a solidificação e melhoram a qualidade das peças, reduzindo simultaneamente o tempo de ciclo.
A melhoria contínua do processo e a análise de dados são essenciais para otimizar a moldagem por compressão. Ao monitorizar e analisar regularmente o desempenho do processo, os fabricantes podem identificar áreas de melhoria e tomar decisões baseadas em dados para atingir os parâmetros ideais de moldagem por compressão.
Em conclusão, a otimização do processo de moldagem por compressão para reduzir o tempo de ciclo é essencial para melhorar a produtividade e a eficiência de custos. Ao implementar estratégias como a otimização da seleção de materiais, vários parâmetros de moldagem por injeção, melhorias de design, automatização e melhoria contínua do processo, os fabricantes podem obter reduções significativas no tempo de ciclo, aumentar a produção e melhorar a competitividade global no mercado. Ao adotar estas estratégias, os fabricantes podem libertar todo o potencial da moldagem por compressão e posicionar-se para o sucesso nas suas respectivas indústrias.
Em conclusão, a otimização do processo de moldagem por compressão para reduzir o tempo de ciclo é essencial para uma maior produtividade e eficiência de custos. Ao implementar estratégias como a otimização da seleção de materiais, melhorias no design do molde, automatização e melhoria contínua do processo, os fabricantes podem obter reduções significativas no tempo de ciclo, aumentar a produção e melhorar a competitividade global no mercado. Ao adotar estas estratégias, os fabricantes podem libertar todo o potencial da moldagem por compressão e posicionar-se para o sucesso nas suas respectivas indústrias.
Em conclusão, a otimização do processo de moldagem por compressão para reduzir o tempo de ciclo é essencial para uma maior produtividade e eficiência de custos. Ao implementar estratégias como a otimização da seleção de materiais, melhorias no design do molde, automatização e melhoria contínua do processo, os fabricantes podem obter reduções significativas no tempo de ciclo, aumentar a produção e melhorar a competitividade global no mercado. Ao adotar estas estratégias, os fabricantes podem libertar todo o potencial da moldagem por compressão e posicionar-se para o sucesso nas suas respectivas indústrias.
Em conclusão, a otimização do processo de moldagem por compressão para reduzir o tempo de ciclo é essencial para uma maior produtividade e eficiência de custos. Ao implementar estratégias como a otimização da seleção de materiais, melhorias no design do molde, automatização e melhoria contínua do processo, os fabricantes podem obter reduções significativas no tempo de ciclo, aumentar a produção e melhorar a competitividade global no mercado. Ao adotar estas estratégias, os fabricantes podem libertar todo o potencial da moldagem por compressão e posicionar-se para o sucesso nas suas respectivas indústrias.