Giriş
Kalıp boşluğu tasarımı, çok sayıda endüstrinin geleceğini şekillendirme gücünü elinde tutan başarılı sıkıştırmalı kalıplamanın temel taşıdır. Üretimin bu kritik yönü, öneminin gerçek bir kanıtı olan yüksek kaliteli, tutarlı sonuçlar sunma kabiliyetine sahip olduğu için hafife alınmamalıdır.
İnovasyon ve hassasiyetin hüküm sürdüğü bir dünyada, basınçlı kalıplama çok yönlü ve vazgeçilmez bir üretim süreci olarak ortaya çıkmaktadır. Otomotiv, elektronik ve tüketim malları da dahil olmak üzere çok sayıda sektöre yayılan uygulamalarıyla, her gün güvendiğimiz ürünlerin şekillendirilmesinde çok önemli bir rol oynamaktadır. Performans ve dayanıklılık için tasarlanan otomotiv bileşenlerinden güvenliğimizi sağlayan elektrik yalıtım malzemelerine kadar, sıkıştırma kalıplama hayatımızın neredeyse her alanına dokunmaktadır.
Daha derinlere indikçe sıkıştırmalı kalıplama için kalıp boşluğu tasarımı'de, bu sürecin karmaşık dokusunu ortaya çıkaran bir yolculuğa çıkıyoruz. Nüanslarını keşfederek, doğru kalıp boşluğu tasarımının nasıl bir olasılıklar dünyasının kilidini açabileceğini, sadece beklentilerimizi karşılamakla kalmayıp çoğu zaman aşan ürünler üretebileceğini ortaya çıkaracağız. Kalıp boşluğu tasarımının bizi üretim mükemmelliğinin zirvesine doğru yönlendiren pusula olduğu sıkıştırmalı kalıplamanın arkasındaki sanat ve bilimin bu keşfinde bize katılın.
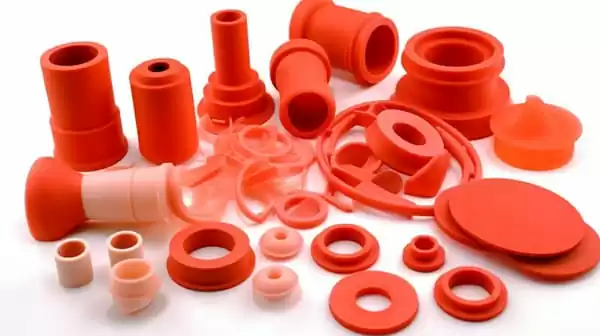
Sıkıştırmalı Kalıplama süreçlerinin anlaşılması
Sıkıştırmalı kalıplama, çeşitli sektörlerde uygulamaları olan çok yönlü ve yaygın olarak kullanılan bir üretim sürecidir. Bu tekniğin özünü kavramak için onu temel bileşenlerine ayırmak çok önemlidir.
1. Sıkıştırmalı Kalıplama Süreci:
Kalbinde, sıkıştırma kalıplama malzemelerin ısı ve basınç kullanılarak şekillendirilmesini içeren bir süreçtir. İlgili adımlar aşağıdaki gibidir:
Malzeme Hazırlama: Süreç, tipik olarak granül, pelet veya tabaka kalıplama bileşikleri (SMC) şeklinde hammaddelerin hazırlanmasıyla başlar.
Isıtma: Genellikle iki yarıdan oluşan kalıp malzemenin etrafına kapatılır. Daha sonra malzemeyi yumuşatmak veya eritmek için ısı uygulanarak esnek hale getirilir.
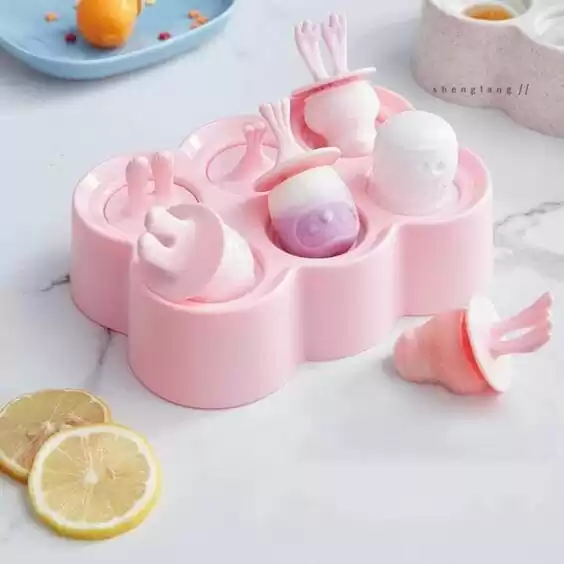
Sıkıştırma: Kalıp boşluğuna basınç uygulanarak malzemenin sıkıştırılması ve nihai ürünün istenen şekli alması sağlanır.
Soğutma: Malzeme kalıbın şeklini aldıktan sonra katılaşması için soğutulur ve ısıtılan kalıp sertleşerek istenen formu korur.
Fırlatma: Son olarak, kalıplanmış parça kalıp boşluğundan çıkarılır ve daha sonraki işlemler veya kullanım için hazır hale gelir.
2. Sıkıştırma Kalıp Tasarımı:
Başarılı bir sıkıştırmalı kalıplama operasyonunun temeli kalıp boşluğunun tasarımında yatar. Sıkıştırma kalıp tasarımı birkaç önemli unsuru kapsamaktadır:
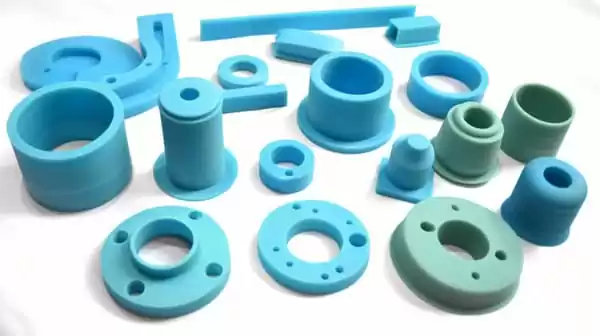
Geometri: Kalıp boşluğunun geometrisi, nihai ürünün amaçlanan şekline tam olarak uymalıdır. Bu, parça kalınlığı, çekim açıları ve alt kesimler gibi hususları içerir ve düzgün bir çıkarma sağlar.
Havalandırma: Kalıplama sırasında sıkışan hava ve gazların dışarı çıkmasını sağlamak için etkili havalandırma şarttır. Doğru havalandırma, nihai üründe hava cepleri veya boşluklar gibi kusurları önler.
Ayırma Çizgisi: Ayırma çizgisi, kalıbın kalıplanmış parçayı serbest bırakmak için ayrıldığı yeri belirler. İyi tanımlanmış olmalı ve ürünün estetiği ve işlevselliği açısından göze batmamalıdır.
Kapı Tasarımı: Kapı, erimiş malzemenin kalıp boşluğuna girdiği nokta olarak hizmet eder. Dikkatli kapak tasarımı düzgün dolum sağlar ve kusurları en aza indirir. Kapı tipleri arasında kenar kapıları, pim kapıları ve tünel kapıları bulunur.
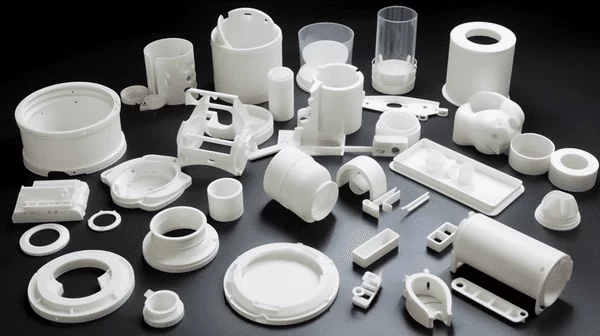
Soğutma Sistemi: Kalıp içindeki verimli soğutma kanalları, kalıplanan parçanın hızlı bir şekilde katılaşmasına yardımcı olur, bükülmeyi veya bozulmayı önler ve döngü sürelerini iyileştirir.
Yüzey İşlemi: Ürünün gereksinimlerine bağlı olarak, nihai ürünün estetiğini geliştirmek için kalıp boşluğunun yüzey kaplaması cilalanabilir, dokulandırılabilir veya kaplanabilir.
3. Sıkıştırma Kalıplamada Kullanılan Malzemeler:
Sıkıştırmalı kalıplama epoksi reçine, silikon kauçuk ve polimer reçineler gibi termoset malzemeler de dahil olmak üzere çok çeşitli malzemelerle uyumludur. Özellikle cam elyafı veya karbon elyaf kompozitler gibi elyaf takviyeli reçine malzemelerle üstünlük sağlar. Bu malzemeler mükemmel mekanik performans, sıcaklık direnci ve kimyasal direnç sunar.
4. Sıkıştırmalı Kalıplamanın Avantaj ve Dezavantajları:
Avantajlar:
Uygun Maliyetli: Sıkıştırmalı kalıplamada genellikle geri dönüştürülmüş termoplastik malzemeler ve nispeten düşük erime noktasına sahip malzemeler kullanılır ve bu da üretim maliyetlerini düşürür.
Geniş Sıcaklık Aralığı: Geniş sıcaklık aralıklarına ve yüksek kimyasal direnç gereksinimlerine sahip parçalar için kalıplar oluşturabilir.
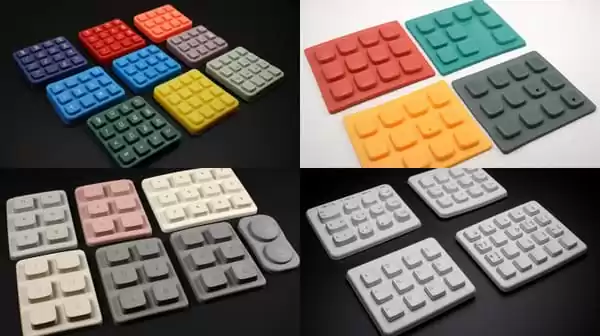
Kompozit Malzemeler: Cam elyaflar ve karbon elyaflar gibi kompozit malzemelerle çalışmak için idealdir ve yüksek mukavemetli, hafif bileşenlerin üretilmesini sağlar.
Dezavantajlar:
Karmaşık Geometriler: Son derece karmaşık geometrilere veya dar toleranslara sahip bileşenlerin üretimi için uygun olmayabilir.
Daha Yavaş Süreç: Sıkıştırmalı kalıplama, enjeksiyon kalıplama gibi diğer kalıplama süreçlerine kıyasla daha yavaş olabilir ve bu da üretim oranlarını etkileyebilir.
Özünde, sıkıştırmalı kalıplama sürecini, sıkıştırmalı kalıp tasarımının rolünü, kullanılan malzemelerin çok yönlülüğünü ve bu yöntemin artılarını ve eksilerini anlamak, çeşitli endüstrilerdeki potansiyelini kullanmak için zemin hazırlar. Hassasiyet, yaratıcılık ve mühendisliği bir araya getirerek ham maddeleri dünyamızın işlevini yerine getiren ürünlere dönüştüren bir süreçtir.
Bölüm 2: Sıkıştırmalı Kalıplama Türleri
Sıkıştırmalı kalıplama alanında, kalıp türleri sürecin sonucunu belirlemede çok önemli bir rol oynar. Kalıp seçimi ürün kalitesini, karmaşıklığını ve üretim verimliliğini önemli ölçüde etkileyebilir. Şimdi sıkıştırma kalıplama için üç ana kalıp tipini inceleyelim ve bunların özelliklerini ve uygulamalarını ortaya çıkaralım:
1. Açık Flaş Kalıp:
Özellikleri:
Flaş Yönetimi: Açık flaşlı kalıpların belirleyici özelliği, sıkıştırmalı kalıplama işlemi sırasında "flaş" olarak bilinen fazla malzemenin dışarı çıkmasına izin verilmesidir. Bu parlama daha sonra kesilerek geride istenen ürün bırakılır.
Uygulamalar:
Düşük Hassasiyetli Parçalar: Açık flaş kalıplar genellikle hassasiyetin kritik bir gereklilik olmadığı durumlarda kullanılır. Yüksek derecede boyutsal hassasiyetin gerekli olmadığı parçaların üretimi için idealdirler.
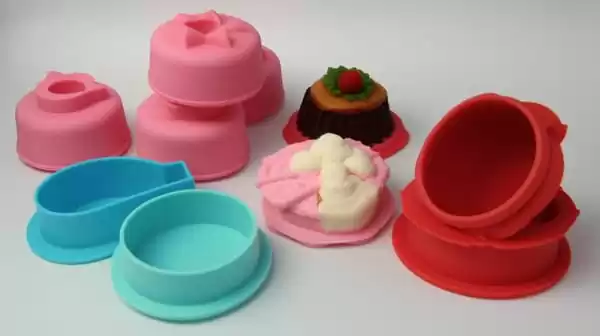
2. Kapalı Kalıp:
Özellikleri:
Hassas: Kapalı kalıplar, sıkıştırmalı kalıplama süreci boyunca yüksek derecede hassasiyeti korumak için tasarlanmıştır. Parlamayı en aza indirecek ve nihai üründe sıkı toleranslar sağlayacak şekilde tasarlanmışlardır.
Uygulamalar:
Kritik Hassasiyet: Kapalı kalıplar, hassasiyetin çok önemli olduğu uygulamalarda kendine yer bulur. Ürün tutarlılığının ve sıkı toleranslara bağlılığın tartışılmaz olduğu senaryolarda kullanılırlar.
3. Yarı Kapalı Kalıp:
Özellikleri:
Hibrit Yaklaşım: Yarı kapalı kalıplar hem açık hem de kapalı kalıpların unsurlarını birleştirir. Bir miktar parlamanın kaçmasına izin verirken, aynı zamanda parça boyutları üzerinde kontrol sağlarlar.
Uygulamalar:
Dengeli Gereksinimler: Yarı kapalı kalıplar, orta düzeyde hassasiyete ihtiyaç duyulduğunda ve parlama yönetiminin gerekli olduğu ancak kapalı kalıplardaki kadar kritik olmadığı durumlarda seçilir. Çok çeşitli ürün gereksinimlerine uygun dengeli bir yaklaşım sunarlar.
Esasen, sıkıştırma kalıplamada açık-flaş, kapalı ve yarı kapalı kalıplar arasındaki seçim, üretilen ürünün özel taleplerine bağlıdır. Açık flaşlı kalıplar hassasiyetin en önemli öncelik olmadığı durumlarda uygundur, kapalı kalıplar en üst düzeyde hassasiyet gerektiren uygulamalarda mükemmeldir ve yarı kapalı kalıplar bu iki uç arasında bir denge kurar. Üreticiler, uygun kalıp tipini seçerek sıkıştırmalı kalıplama süreçlerini ürünlerinin ve sektörlerinin benzersiz ihtiyaçlarını karşılayacak şekilde optimize edebilirler.
Bölüm 3: Sıkıştırma Kalıplama Malzemelerinin Türleri
Sıkıştırmalı kalıplama dünyasında, sıkıştırmalı kalıplanmış ürünler için malzeme seçimi, nihai ürünün özelliklerini ve karakteristiklerini belirlemede çok önemlidir. Bu süreçte yaygın olarak kullanılan iki malzeme Sac Kalıplama Bileşiği (SMC) ve Dökme Kalıplama Bileşiğidir (BMC). Bu malzemeleri inceleyelim ve sıkıştırma kalıplamada termoset malzemelerin kullanılmasının avantajlarına ışık tutalım:
1. Sac Kalıplama Bileşiği (SMC):
Özellikleri:
Elyaf Takviyeli: SMC, termoset reçineleri doğranmış cam elyaflarla birleştiren elyaf takviyeli bir malzemedir. Bu takviye malzemeye mükemmel güç ve sertlik kazandırır.
Levha Formu: SMC tipik olarak düz levhalar veya rulolar şeklinde tedarik edilir. Bu levhalar reçine ile önceden emprenye edilmiştir ve kalıp boşluğu içinde kolayca kesilebilir ve katmanlanabilir.
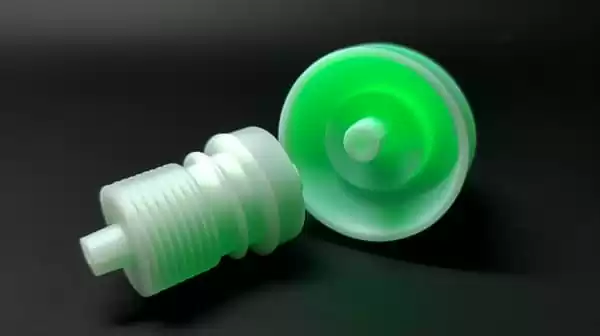
Uygulamalar:
Otomotiv Bileşenleri: SMC, yüksek mukavemeti, darbe direnci ve korozyon direnci nedeniyle otomotiv endüstrisinde gövde panelleri, kaputlar ve dış kaplama gibi bileşenlerin üretiminde yaygın olarak kullanılmaktadır.
Elektrik Muhafazaları: Elektriksel yalıtım özellikleri SMC'yi elektrik muhafazaları ve panelleri için tercih edilen bir seçenek haline getirmektedir.
2. Dökme Kalıplama Bileşiği (BMC):
Özellikleri:
Termoset Malzeme: BMC aynı zamanda termoset reçine, dolgu malzemeleri ve takviye liflerinin (tipik olarak cam) karışımından oluşan termoset bir malzemedir.
Granül Form: SMC'den farklı olarak BMC granül formda tedarik edilir. Bu granüler kıvam, karmaşık şekillerin hassas bir şekilde kalıplanmasına olanak tanır.
Uygulamalar:
Otomotiv Endüstrisi: BMC, otomotiv endüstrisinde valf kapakları, emme manifoldları ve kaput altı parçaları gibi karmaşık bileşenlerin üretiminde kendine yer bulur. Boyutsal kararlılığı ve kimyasallara ve ısıya karşı direnci onu ideal bir seçim haline getirir.
Elektrik ve Elektronik: BMC, mükemmel elektrik yalıtımı özellikleri ve alev direnci nedeniyle elektrik ve elektronik uygulamalarında kullanılır.
Sıkıştırmalı Kalıplamada Termoset Malzeme Kullanımının Avantajları:
SMC ve BMC'de kullanılanlar gibi termoset malzemelerin seçimi, sıkıştırmalı kalıplama sürecinde çeşitli avantajlar sunar:
Sıcaklık Dayanımı: Termoset malzemeler yüksek sıcaklıklı ortamlarda mükemmeldir. Yüksek sıcaklıklara deforme olmadan dayanabilirler, bu da onları ısıya ve termal döngüye direnç gerektiren uygulamalar için uygun hale getirir.
Kimyasal Direnç: Bu malzemeler mükemmel kimyasal direnç sergileyerek çeşitli kimyasallara maruz kalmanın beklendiği uygulamalar için idealdir.
Boyutsal Kararlılık: Termoset malzemeler basınç ve yüksek sıcaklıklar altında şekil ve boyutlarını koruyarak nihai üründe tutarlılık ve hassasiyet sağlar.
Elektrik İzolasyonu: Hem SMC hem de BMC olağanüstü elektriksel yalıtım özelliklerine sahiptir, bu da onları elektrik ve elektronik uygulamalarında vazgeçilmez kılar.
Karmaşık Şekiller: BMC'nin granül formu ve SMC'nin katmanlama kabiliyeti, karmaşık ve girift şekillerin kalıplanmasına olanak tanıyarak tasarımda çok yönlülük sağlar.
Özetle, Tabaka Kalıplama Bileşiği (SMC) ve Yığın Kalıplama Bileşiği (BMC), sıkıştırmalı kalıplamada kullanılan termoset malzemelere örnek teşkil etmektedir. Sıcaklık ve kimyasal direnç, boyutsal kararlılık ve elektrik yalıtımı özellikleri gibi doğal avantajları, onları endüstrilerdeki çeşitli ürünlerin üretiminde değerli seçenekler haline getirmektedir. Bu malzemelerin kullanımı, basınçlı kalıplamanın hassasiyeti ile birleştiğinde sıkıştırma kalıplamaözel karakteristiklere ve performansa sahip yüksek kaliteli bileşenlerle sonuçlanır.
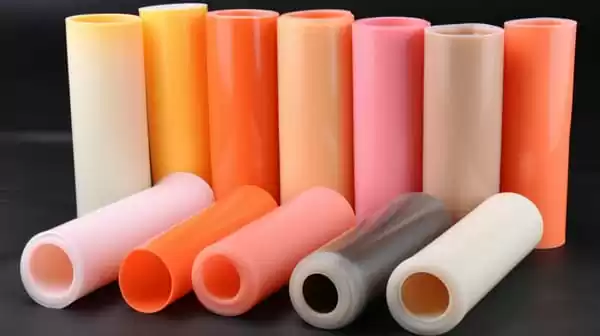
Bölüm 4: Sıkıştırmalı Kalıplama Sürecinin Kendisi
Sıkıştırmalı kalıplamanın inceliklerini gerçekten kavramak için, sürecin özüne inmek çok önemlidir. Bu bölümde, sıkıştırma kalıbının temel bileşenlerini keşfedecek, yüksek basınçlı yapısının önemini anlayacak ve kalıplanmış parçanın katılaşmasından sorumlu kürleme sürecini çözeceğiz:
1. Sıkıştırma Kalıbının Bileşenleri:
Sıkıştırma kalıbı, sıkıştırma kalıplama sürecinin kalbidir. Birkaç önemli bileşenden oluşur:
Kalıp Boşluğu: Sihrin gerçekleştiği yer burasıdır. Kalıp boşluğu nihai ürünün şeklini ve boyutlarını tanımlar. Parça kalınlığı, çekim açıları ve yüzey kalitesi gibi faktörler de dahil olmak üzere istenen geometriyi barındıracak şekilde titizlikle tasarlanmalıdır.
Isıtma Sistemi: Sıkıştırma kalıpları, kalıp boşluğu içindeki sıcaklığı yükselten bir ısıtma sistemi ile donatılmıştır. Bu ısıtma, ham maddeyi yumuşatmak veya eriterek esnek ve kalıplanmaya uygun hale getirmek için gereklidir.
Soğutma Sistemi: Verimli soğutma kanalları veya sistemleri, kalıplanan parçayı şekillendirdikten sonra hızla soğutmak ve katılaştırmak için kalıp boyunca ilerler. Doğru soğutma, istenen formun korunmasını sağlar ve bükülme veya bozulmayı önler.
Basınç Mekanizması: Sıkıştırmalı kalıplama yüksek basınçlı doğasıyla bilinir. Kalıp, kalıp boşluğuna önemli ölçüde basınç uygulamak için bir mekanizma içerir. Bu basınç, malzemenin sıkıştırılmasından, kalıbın her köşesini doldurmasını sağlamaktan ve nihayetinde parçanın yoğunluğunu ve yapısal bütünlüğünü tanımlamaktan sorumludur.
2. Sıkıştırmalı Kalıplamanın Yüksek Basınçlı Doğası:
Sıkıştırmalı kalıplama, nihai ürünün şekillendirilmesinde çok önemli bir rol oynayan yüksek basınçlı doğası ile karakterize edilir. Bu yüksek basınçlı ortamın önemi birkaç açıdan yatmaktadır:
Malzeme Sıkıştırma: Sıkıştırmalı kalıplama sırasında uygulanan yüksek basınç, malzemeyi kalıp boşluğu içinde sıkıştırır. Bu sıkıştırma, malzemenin kalıbın geometrisine tam olarak uymasını sağlayarak mükemmel parça üretimi ve boyutsal doğruluk sağlar.
Yoğunluk Kontrolü: Basınç, nihai ürünün yoğunluğunu belirler. Üreticiler basıncı dikkatli bir şekilde kontrol ederek, parçanın mekanik özelliklerini ve performansını etkileyen belirli malzeme yoğunlukları elde edebilirler.
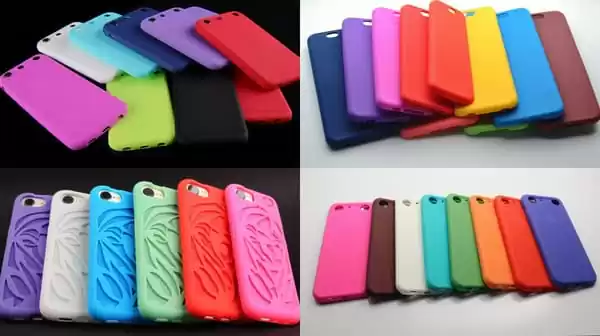
Tek Tip Dolgu: Yüksek basınç, kalıp boşluğunun eşit şekilde doldurulmasına yardımcı olur. Bu da nihai üründe boşluk, hava cebi veya diğer kusurların oluşma riskini en aza indirerek kaliteye katkıda bulunur.
3. Kürleme Süreci:
Malzeme kalıp boşluğu içinde istenen şekli aldıktan sonra kürleme işlemi devreye girer. Kürleme, kalıplanmış parçanın katılaştırılmasından ve nihai yapısal bütünlüğünün sağlanmasından sorumlu adımdır. İşte nasıl çalıştığı:
Isı ve Basınç: Uygulanan basınçla birlikte kalıp içindeki yüksek sıcaklık, termoset malzemede kimyasal bir reaksiyonu tetikler. Bu reaksiyon malzemenin sertleşmesine ve şeklini almasına neden olur.
Soğutma: Kürleme işlemi tamamlandığında, sıcaklığı hızla düşürmek için kalıbın soğutma sistemi etkinleştirilir. Bu soğutma aşaması, parçanın katılaşmasına yardımcı olarak onu sertleştirir ve kalıptan çıkarılmaya hazır hale getirir.
Sonuç olarak, sıkıştırma kalıbının bileşenlerini, yüksek basınçlı ortamın önemini ve kürleme sürecini anlamak, sıkıştırma kalıplama mekaniği hakkında değerli bilgiler sağlar. Isı, basınç ve hassas mühendisliğin bu karmaşık etkileşimi, aşağıdaki ürünlerin üretimini mümkün kılmaktadır yüksek kaliteli bileşenler İstenilen şekil, yoğunluk ve mekanik özelliklere sahip. Üretim mükemmelliğinin somutlaşmış halidir ve en yüksek performans ve güvenilirlik standartlarını karşılayan ürünler sunar.
Bölüm 5: Kalıp Boşluğunun Tasarlanması
Kalıp boşluğu, sıkıştırma kalıplama sürecinin tam kalbinde yer alır. Bu bölümde kalıp boşluğu tasarımının kritik rolünü inceleyecek, sıkıştırma kalıbı tasarımını tanımlayacak ve sıkıştırma kalıplamada çok önemli bir faktör olan tonaj hesaplamasına değineceğiz:
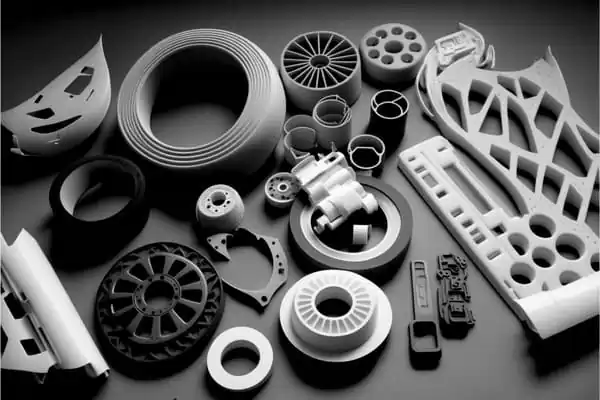
1. Kalıp Boşluğu Tasarımının Önemi:
Kalıp boşluğunun tasarımı, sıkıştırmalı kalıplama sürecinin başarısını sağlamada çok önemlidir. İşte bu yüzden büyük önem taşıyor:
Hassasiyet ve Tutarlılık: Kalıp boşluğu, ürünün nihai şeklini ve boyutlarını tanımlar. İyi tasarlanmış bir boşluk, kalıplanan her parçada hassasiyet ve tutarlılık sağlayarak en yüksek kalite standartlarını karşılar.
Malzeme Akışı: Kalıp boşluğunun geometrisi malzemenin nasıl akacağını ve kalıbı nasıl dolduracağını belirler. Uygun olmayan bir tasarım, eşit olmayan malzeme dağılımına yol açarak nihai üründe kusurlara veya tutarsızlıklara neden olabilir.
Havalandırma ve Soğutma: Kalıp boşluğundaki etkili havalandırma kanalları veya oluklar, sıkışan hava ve gazların dışarı çıkmasına izin vererek hava cepleri gibi kusurları önler. Boşluk içindeki soğutma sistemi, parçanın hızlı bir şekilde katılaşmasına yardımcı olarak döngü sürelerini azaltır.
Yüzey İşlemi: Kalıp boşluğu tasarımı, kalıplanmış parça üzerinde istenen yüzey kalitesinin elde edilmesinde de rol oynar. Belirli estetik ve işlevsel gereksinimleri karşılamak için cilalanabilir, dokulandırılabilir veya kaplanabilir.
2. Sıkıştırma Kalıp Tasarımı Nedir?
Sıkıştırma kalıp tasarımı sıkıştırmalı kalıplamanın doğasında bulunan yüksek basınçlara ve sıcaklıklara dayanabilecek bir kalıp boşluğunun titizlikle oluşturulması sürecidir. Birkaç kritik hususu kapsar:
Geometri: Kalıp boşluğu, nihai ürünün amaçlanan şekline tam olarak uymalıdır. Bu, parça kalınlığını, çekme açılarını ve düzgün çıkarma için alt kesimleri dikkate almayı içerir.
Havalandırma: Uygun havalandırma kanalları veya oluklar, kalıplama sırasında sıkışan hava ve gazların dışarı çıkmasını sağlayarak nihai üründe hava cepleri veya boşluklar gibi kusurları önler.
Ayrılık cümlesi: Ayırma çizgisi, kalıbın kalıplanmış parçayı serbest bırakmak için ayrıldığı yeri belirler. İyi tanımlanmış olmalı ve ürünün estetiği ve işlevselliği açısından göze batmamalıdır.
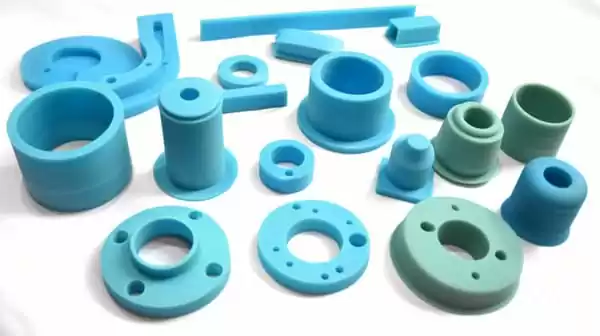
Kapı Tasarımı: Kapı, erimiş malzemenin kalıp boşluğuna girdiği nokta olarak hizmet eder. Dikkatli kapak tasarımı düzgün dolum sağlar ve kusurları en aza indirir. Kapı tipleri arasında kenar kapıları, pim kapıları ve tünel kapıları bulunur.
Soğutma Sistemi: Kalıp içindeki verimli soğutma kanalları, kalıplanan parçanın hızlı bir şekilde katılaşmasına yardımcı olur, bükülmeyi veya bozulmayı önler ve döngü sürelerini iyileştirir.
Yüzey İşlemi: Ürünün gereksinimlerine bağlı olarak, nihai ürünün estetiğini geliştirmek için kalıp boşluğunun yüzey kaplaması cilalanabilir, dokulandırılabilir veya kaplanabilir.
3. Sıkıştırmalı Kalıplama için Tonaj Nasıl Hesaplanır?
Tonaj olarak sıkıştırma kalıplama Malzemeyi kalıp boşluğu içinde sıkıştırmak için gereken kuvveti ifade eder. Uygun malzeme sıkıştırma ve parça yoğunluğu elde etmede çok önemli bir faktördür. Tonajı hesaplamak için aşağıdaki formülü kullanabilirsiniz:
Tonaj = Basınç × Alan
Basınç: Basınç tipik olarak PSI (Pounds per Square Inch) cinsinden ölçülür.
Bölge: Alan, kalıplanan parçanın öngörülen alanını temsil eder.
Üreticiler, gerekli tonajı hesaplayarak, sıkıştırmalı kalıplama işleminde kullanılan presin, kalıp boşluğu içindeki malzemenin istenen sıkıştırma ve yoğunluğunu elde etmek için gerekli kuvveti uyguladığından emin olabilirler.
Özünde, kalıp boşluğu tasarımı başarılı sıkıştırma kalıplamanın temel taşıdır. Ürün kalitesini, hassasiyetini ve tutarlılığını belirler. Sıkıştırma kalıbı tasarımı geometriyi, havalandırmayı, ayırma hatlarını, kapı tasarımını, soğutma sistemlerini ve yüzey kaplamasını kapsar; hepsi de istenen parçanın özel gereksinimlerini karşılamak üzere uyarlanmıştır. Tonajın anlaşılması ve hesaplanması, sıkıştırmalı kalıplama sürecinin en iyi şekilde çalışmasını ve endüstri standartlarını karşılayan veya aşan yüksek kaliteli bileşenler üretilmesini sağlar.
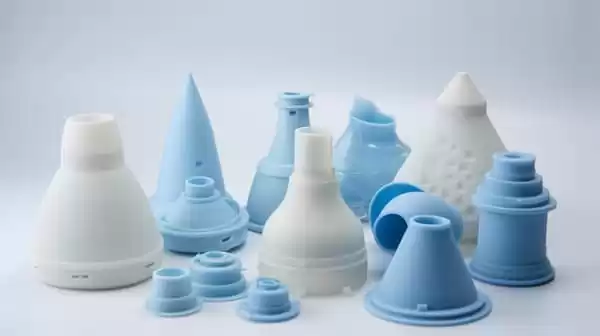
Sonuç
Sıkıştırmalı kalıplama ve kalıp boşluğu tasarımına ilişkin bu kapsamlı araştırmada, çok sayıda sektörde silinmez bir iz bırakan bir üretim sürecinin karmaşık dünyasını ortaya çıkardık.
Araştırmamızı sonlandırırken, okuyucularımızı üretim ihtiyaçları için sıkıştırma kalıplamayı düşünmeye teşvik ediyoruz. Hassasiyeti, çok yönlülüğü ve yüksek kaliteli bileşenler sunma kabiliyeti, onu çok çeşitli uygulamalar için keşfedilmeye değer bir süreç haline getirmektedir. Üreticiler, sıkıştırma kalıplamayı benimseyerek ve uygun kalıp boşluğu tasarımının gücünden yararlanarak, üretimde en yüksek mükemmellik standartlarını karşılamakla kalmayıp aşan ürünler üreterek bir olasılıklar dünyasının kilidini açabilirler.