Silikon kauçuk kalıplama hem bir sanat hem de bir bilimdir. Esasen bu uygulama, tasarımcıların tasarım fikirlerini veya ilhamlarını, hassas el sanatlarından endüstriyel bileşenlere kadar değişebilen gerçek ürünlere dönüştürmelerine olanak tanır. Ancak bu süreci sınırlayan şey, sertleştirilmiş, kalıplanmış silikon kauçuk ürünün kalıptan çıkarılması gibi kritik bir adımdır. Dışarıdan bakıldığında kulağa basit gelebilir, ancak bu adım kritiktir. Kalıplama sürecindeki son adımdır, bu da özellikle karmaşık ürünler veya karmaşık kalıplarla uğraşırken nihai ürünü yapabilecek veya bozabilecek kritik bir adım olduğu anlamına gelir. Bazen ince veya kırılgan bir ürün olabilir.
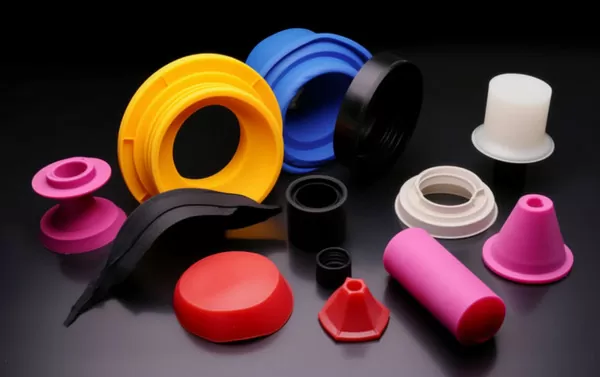
Bu blog yazısında, bu teknolojinin incelikleri hakkında size yol göstereceğiz. Yol boyunca, çabalarınızı geliştirmenize yardımcı olacak değerli tavsiyeler ve ipuçları sunacağız. silikon kauçuk ürün Daha yumuşak.
Kalıp Ayırma Süreci Neden Kritiktir?
Silikon kauçuk bir ürün üretmek için çok fazla zaman ve çaba harcadığınızı düşünün, ancak kalıptan sorunsuz bir şekilde çıkarılamadığı için kusurlu olduğunu keşfedin. Bunun, tamamen estetik sorunlardan parçanın tamamen işe yaramaz hale getirilmesine kadar uzanan bir dizi sonucu olabilir. Silikon kauçuğun kalıptan düzgün bir şekilde çıkarılması sadece yapmanız gereken önemli bir şey değil, aynı zamanda bitmiş ürününüzün bütünlüğe sahip olması için kesinlikle çok önemlidir.
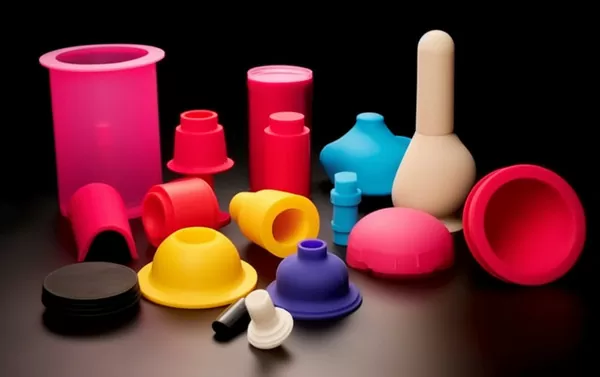
Silikon Kauçuğun Doğasını Anlamak
Kalıp ayırma tekniklerini incelemeden önce silikon kauçuğun temellerini anlamak önemlidir. Malzeme esnekliği, yüksek sıcaklıklara dayanma kabiliyeti ve genel olarak kimyasal reaktivite eksikliği nedeniyle oldukça rağbet görmektedir. Bu özellikleri nedeniyle, diğer maddelerden farklı olarak belirli şekillerde kullanılması gerekir:
1. "Yapışkan" Meydan Okuma
Silikon kauçuk, ürün kalıplama için doğal avantajlara sahip olan iyi viskozitesi ile ünlüdür, ancak kalıptan çıkarma ile ilgili sorunlar da vardır.
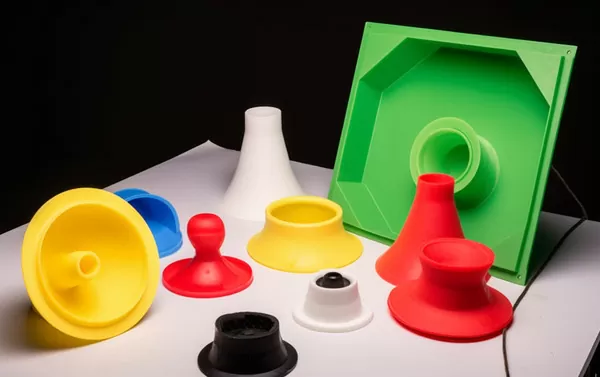
2. Yumuşaklık ve Esneklik
Silikon kauçuk malzemeler iyi bir yumuşaklığa ve esnekliğe sahiptir, bu da kalıp detayları veya karmaşık şekiller oluştururken oldukça avantajlıdır. Bununla birlikte, üretim sürecini de zorlaştırabilir ve hassas kalıplar yırtılma riski altında olabilir.
3. Termal Performans
Sıcaklık önemlidir çünkü silikon yumuşaklığını geniş bir sıcaklık aralığında koruyabilir, bu nedenle ürünlerin kalıptan düzgün bir şekilde çıkarılabilmesi için soğutulması veya ısıtılması gerekebilir.
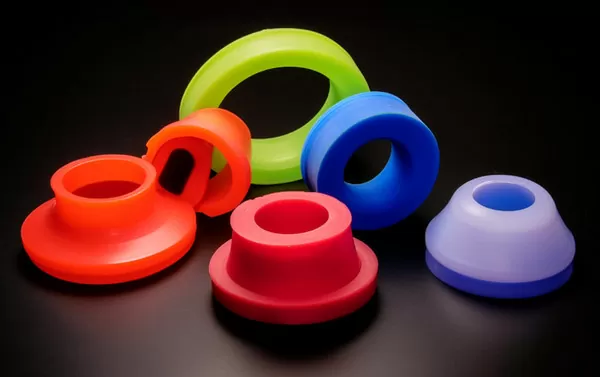
Doğru Kalıp Ayırıcı Türünü Seçme
Uygun bir kalıp ayırıcı ve silikon kalafat seçmek, başarılı bir ürün sürümü sağlamanın ilk adımıdır. İşte dikkate alınması gereken bazı faktörler:
1. Su Bazlıya Karşı Solvent Bazlı
Su bazlı ayırıcılar genellikle çoğu silikon bileşiği için iyi bir seçimdir ve çevre için de güvenlidir. Bununla birlikte, platinle sertleştirilmiş silikon kullanıyorsanız, bu aslında en iyi seçeneğiniz olmayabilir.

Bu durumda, solvent bazlı ayırıcı maddelerin kullanılması hala mümkündür (ve tavsiye edilir) - bu ürünlerin artan yanıcılık tehlikesi nedeniyle veya genel olarak daha dikkatli kullanım gerektirdikleri için belirli önlemlerin alınması gerektiğini unutmayın.
2. Ürüne Özel Tavsiyeler
Kalıp ayırıcı ürünleri kullanırken, optimum performans için her zaman üreticinin tavsiyelerine uyun.
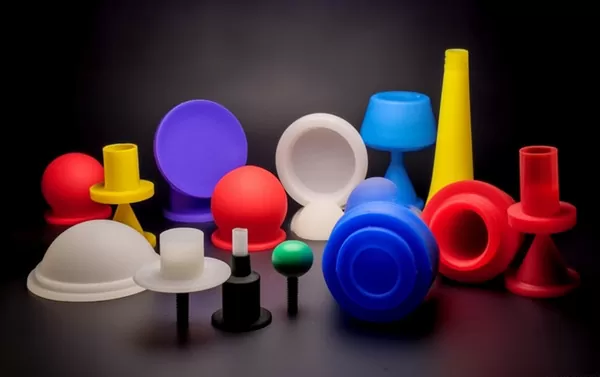
3. Sprey veya Fırça
Bu tür maddelerin uygulanması söz konusu olduğunda, dikkate alınması gereken iki seçenek vardır: yüzeye püskürtmek veya yüzeye fırçalamak.
Genel olarak konuşursak, bir ürünün püskürtülmesi daha iyi bir genel kaplama sağlar, ayrıca sonrasında herhangi bir su birikintisi kalmaz (aksi takdirde finisajı olumsuz etkileyebilir). Aynı zamanda, desenin yüzeye fırçalanması daha hassas bir etki sağlayabilir, bu da sprey desenleri için uygun olmayan daha büyük kalıplar için gerekli olabilir.

Kalıp Ayırıcının Doğru Uygulanmasını Sağlama
Ayırıcınızı doğru şekilde kullandığınızdan emin olmak, doğru ürünü seçmek kadar önemlidir, işte bunu nasıl yapacağınıza dair bazı yönergeler:
1. Kalıp Yüzeyini İyice Temizleyin
Tozu, olası malzeme kalıntılarını veya önceki kalıp ayırıcı maddeyi gidermek için yüzeyi kalıp temizleyici ile iyice temizleyin.
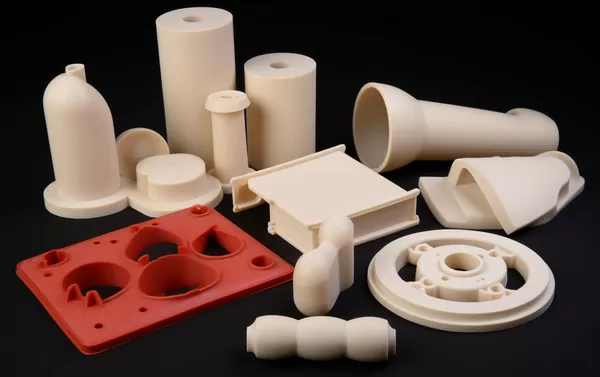
2. İnce, Eşit Bir Kat Uygulayın
İnce, eşit bir kat uygulayın. Ayırıcı maddeyi uygulamadan önce iyice çalkaladığınızdan veya karıştırdığınızdan emin olun, böylece her şey birbirine iyice karışır. Daha sonra amaç, aşırıya kaçmadan ve nesneyi doyurmadan tüm alanı eşit ancak hafif bir şekilde kaplamaktır, çünkü çok fazla kalıplama bileşiği nihai üründe birikmeye ve kusurlara neden olabilir.
3. Birden Fazla Kat Gerekebilir
Bazen, özellikle daha büyük kalıplarla veya karmaşık tasarımlı kalıplarla çalışırken tek kat yeterli olmaz; bu durumda, birden fazla ince kat uygulamak yardımcı olacaktır, sadece unutmayın, her katın başka bir kata başlamadan önce yeterli kuruma süresine ihtiyacı vardır.
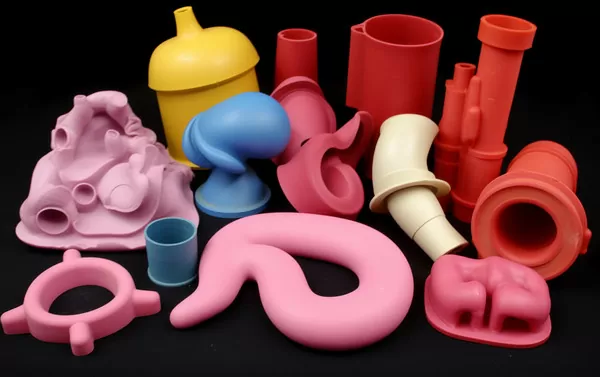
Kalıplama Sürecinize Kalıp Ayırıcı Uygulamak
Kalıplama sürecinize bir ayırıcı madde ekleyin. Ayırıcı madde eklemek, tüm kalıplama sürecinin önemli bir parçası olmalıdır. Bu yöntemler size yardımcı olabilir:
1. Tutarlılık Anahtardır
Kalıbın buna ihtiyacı olmadığını düşünseniz bile kalıptan çıkarma adımını atlamayın. Her seferinde aynı uygulama tekniği kullanılır, böylece ürün kalitesini etkileyen değişkenler minimumda tutulur.
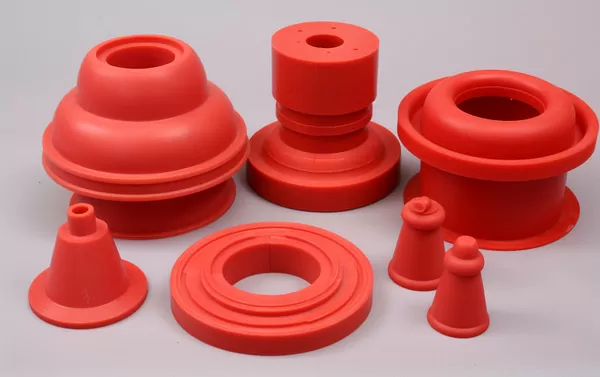
2. Hazırlık Adımları
Yoğuşma ile sertleşen silikon ile çalışırken ayırıcı maddeyi uygulamadan önce kalıbı önceden ısıtın. Ekleme kürü silikon ile çalışırken kalıbı hafifçe soğutun. Bu termal gradyan, daha sonra parçanın kalıptan daha kolay çıkarılmasına yardımcı olabilir.
3. Serbest Bırakma Sonrası Temizlik
Sonra SİLİKON ÜRÜN kalıptan çıkarıldığında, bu kimyasallar temizlenmesi gereken bir miktar artık malzeme bırakabilir.
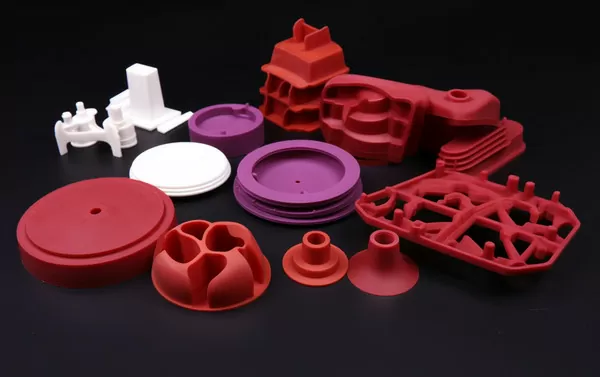
Sürüm Sorunlarını Giderme
İyi uygulanmış bir ayırıcı madde ile bile sorunlar ortaya çıkabilir. Sık karşılaşılan sorunların nasıl ele alınacağı aşağıda açıklanmıştır:
1. Yapışma veya Yırtılma
Hala yapışma sorunları yaşıyorsanız, ayırıcı maddenin eşit şekilde uygulandığını ve kalıbın kullanılan ayırıcı madde türü için doğru sıcaklıkta olduğunu iki kez kontrol edin.
Malzeme çıkarılırken yırtılırsa, farklı türde bir ayırıcı madde kullanmayı deneyin. Genellikle daha yapışkan olan belirli kalıplama malzemeleriyle bir ayırıcı madde kullanmayı veya ürünü uygularken kalıbın sıcaklığını değiştirmeyi düşünün.
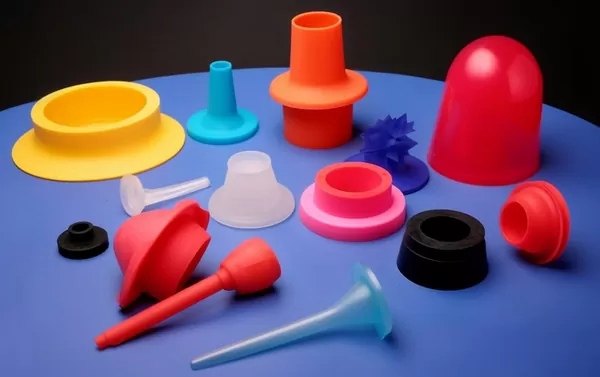
2. Kusurlu Yüzey İşlemi
Yağlı veya pürüzlü bir yüzey genellikle çok fazla ayırıcı madde kullanılmasından kaynaklanabilir. Çalışırken ince bir tabakayı eşit şekilde uyguladığınızdan emin olmanız gerekir.
3. Kalıp Kirlenmesi
Bu, kalıp içinde çok fazla ayırıcı madde biriktiğinde meydana gelir ve bu da bitmiş yüzeyde kabarcıklar veya başka izler oluşturabilir. Düzenli temizlik ve doğru kullanım bunun olmasını önlemeye yardımcı olacaktır.
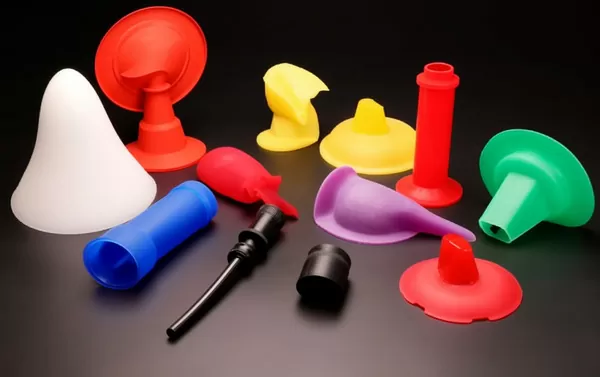
Kalıp Ayırma için İleri Teknikler
Süreçlerine ince ayar yapmak isteyen deneyimli kalıpçılar için, işte birkaç gelişmiş yöntem:
1. Hava Destekli Serbest Bırakma Sistemleri
Bu tür bir sistem, parçanın kalıptan çıkarılmasına yardımcı olmak için kontrollü bir hava üflemesi kullanır. Ön maliyet pahalı olsa da, bu sistemler özellikle karmaşık veya kırılgan parçalar için etkilidir.
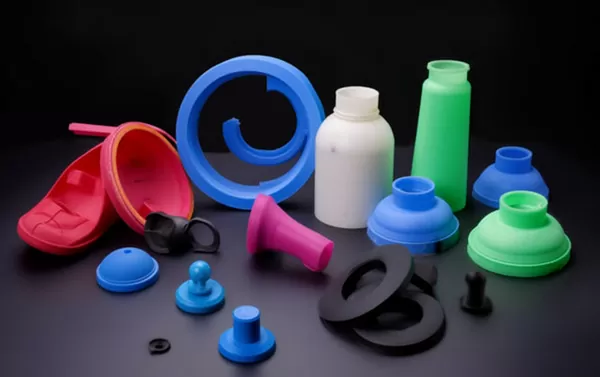
2. Darbe ve Titreşim
Özel kalıp malzemesi veya derin alt kesimleri veya çok ince detayları olan kalıplarla çalışırken, kalıptan çıkarma aşamasında kontrollü şok veya titreşim, kalıbın diğer parçalarına zarar vermeden sıkışmış parçaların serbest kalmasına yardımcı olabilir.
3. Özelleştirilmiş Salım Ajanları
Bazen standart kalıp ayırıcılar belirli işler için yeterli değildir; uygulama için gereken belirli özelliklerden (yüksek sıcaklık direnci gibi) yoksundurlar. Bu durumda, üreticiler zor kalıp ayırma durumlarının üstesinden gelmek için özel olarak uyarlanmış formülasyonlar geliştirmeyi seçebilirler.
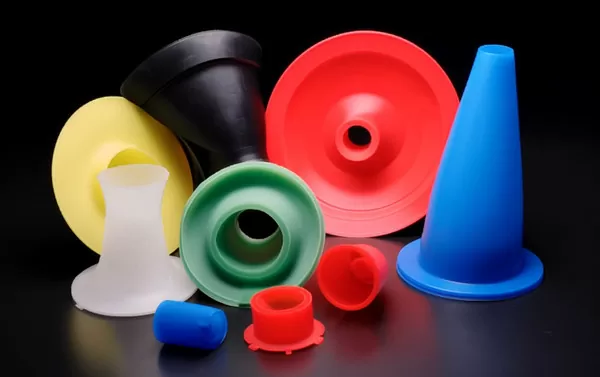
Kalıp ve Ürün Tasarımının Rolü
Bir ürünün ilk tasarımı, ürünün üretim süreci üzerinde büyük bir etkiye sahip olacaktır. Çekim açısı ve ayırma çizgisi gibi faktörler kalıptan çıkarmayı kalıp ve ürün için daha kolay veya daha zor hale getirebilir. İşte tasarımın nasıl yardımcı olabileceği:
1. Çekim Açılarının Dahil Edilmesi
Taslak açısının tasarımda önceden dikkate alınması, parçanın şekillendirildikten sonra kalıptan çıkmasını kolaylaştıracaktır.
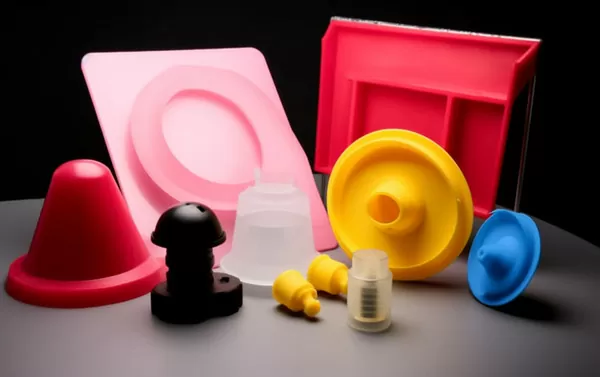
2. Akıllı Ayırma Çizgileri
Stratejik olarak yerleştirilmiş ayırma çizgileri, ürünlerin kalıptan sorunsuz bir şekilde çıkmasına ve kalıptan çıkarmayı zorlaştırabilecek alt kesiklerin önlenmesine yardımcı olabilir.
3. Keskin Köşelerden ve Kenarlardan Kaçınma
Bu özellikler ürünün kalıptan çıkarılırken sıkışmasına neden olabilir. Bunun yerine, mümkünse köşeleri yuvarlatılmış bir tasarım seçin, çünkü bunların sıkışması keskin köşeli tasarımlara göre daha az olasıdır.
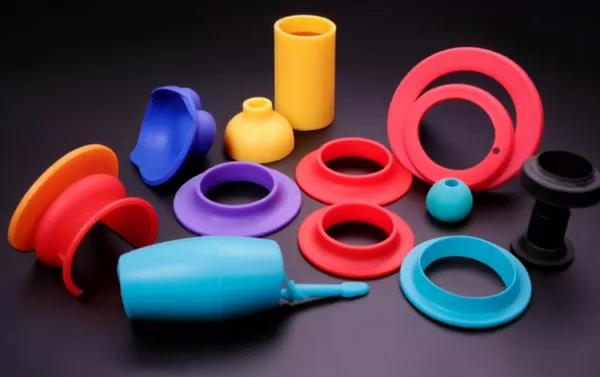
Sonuç
Kalıp sökme işlemi, üretimin önemli bir parçasıdır. silikon kauçuk kalıplama süreci. Bunu iyi yapmak için silikon kauçuğun nasıl çalıştığını anlamanız ve doğru ayırıcı maddeyi seçmeniz gerekir. Ayrıca doğru şekilde uygulamanız ve projede devam eden diğer şeylerle nasıl uyum sağladığını göz önünde bulundurmanız gerekir. Tüm bunları iyi yapabilirseniz, sadece üretiminizin hızlanması değil, aynı zamanda ürününüzün kalitesinin de artması ihtimali yüksektir.
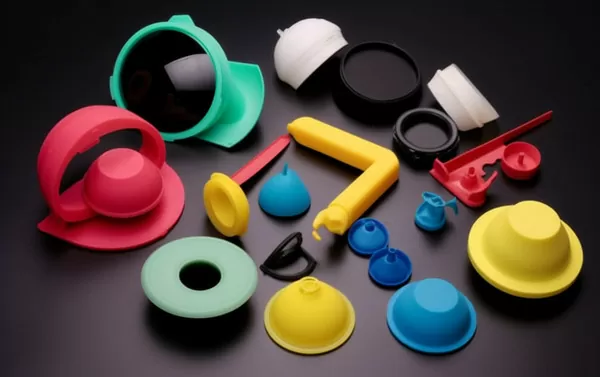
Silikon kauçuk ürünleri kalıplardan etkili bir şekilde çıkarmak için çeşitli yöntemler ve maddeler kullanılabilir. Bunlar arasında örneğin silikon kalafat, vazelin veya mineral ispirtolar olabileceği gibi kalıp kutuları, vakum odası ve keskin bıçak gibi ekipmanlar da yer alabilir! Bununla birlikte, bu teknikleri kullanırken çok dikkatli olun, böylece sadece potansiyel yüzey detay hasarlarından kaçınmakla kalmaz, aynı zamanda dökümdeki hava kabarcıklarını gidermek gibi yaygın sorunlarla da başa çıkabilirsiniz, ister eski silikonu çıkarırken ister kalıp yapım işlemi sırasında yeni silikon uygularken kabarcıklar üretecektir.
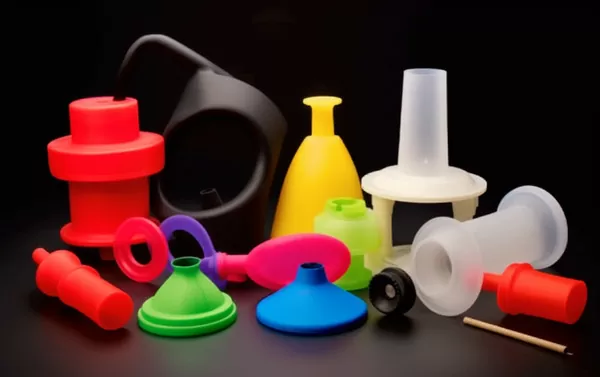
Tüm üretim süreçlerinin en küçük yönlerine dikkat ederek, silikon kauçuk ürünlerinizin silikon kalıptan çıktıklarında mükemmel görüneceğini garanti edebileceksiniz. Silikon kauçuk kalıplama, hassasiyet, sabır ve her sürümden bir şeyler öğrenme isteği gerektiren bir süreçtir.