Introduction
Technology advances have brought about significant changes to production parts and the manufacturing industry. 3D printing and prototyping, for instance, have revolutionized how parts and products are designed and created.
3D printing is a technique that creates three-dimensional objects by layering materials on top of one another, from a digital model. Prototyping, on the other hand, involves creating an actual working model of a product to test and refine its design. Combining 3D printing and prototyping offers many advantages – particularly when producing silicone rubber parts.
Silicone rubber parts are popular in numerous industries due to their durability, flexibility, and resistance to extreme temperatures. Liquid Silicone Rubber (LSR) is one type of silicone rubber material commonly employed in automotive, aerospace, medical, and consumer goods applications.
This article will examine the use of 3D printing and prototyping for silicone rubber parts, with a special focus on producing lsr molds . We’ll look at the advantages of this method and the steps involved in prepping a 3D print for the silicone part molds. Furthermore, we’ll evaluate its various applications and compare them to traditional manufacturing processes. Finally, we’ll consider any challenges or limitations encountered while working with silicone parts, as well as potential future developments within this field.
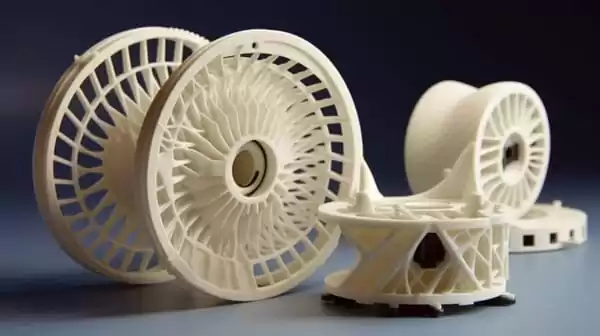
II. Advantages of Using 3D Printing for Silicone Rubber Parts
A. Rapider and Economized Production
3D printing can dramatically reduce the time and cost of producing silicone rubber parts. Traditional manufacturing requires creating molds, which is costly and time-consuming. With 3D printing, parts can be 3d printed in just hours or days without the need for lengthy mold-making processes – leading to faster turnaround times with lower production costs.

B. Expanded Design Flexibility
3D printing offers designers more design freedom when crafting silicone rubber parts. The digital nature of 3D printing enables designers to easily modify their product’s design, leading to a faster design process and superior final products.
C. Enhancing Accuracy and Precision
3D printing also provides superior accuracy and precision when fabricating silicone rubber parts. Traditional manufacturing processes may be limited by the capabilities of the machinery or tools used, but with 3D printing, parts can be created with high levels of accuracy and precision – leading to a more consistent final product.
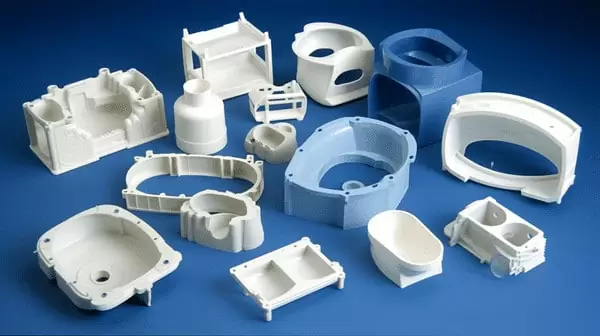
D. Enables the production of complex geometries with fine details.
3D printing allows the production of silicone rubber parts with complex geometries and fine details, something traditional manufacturing processes cannot provide. 3D printing makes this possible – especially useful for creating customized parts and prototypes.
E. Enables the production of translucent white silicone parts
Finally, 3D printing makes it possible to manufacture translucent white silicone parts, which are especially beneficial in medical and consumer applications. Transparent silicone parts themselves can be challenging to produce using traditional manufacturing processes; however, 3D printing offers greater design freedom and product customization options.
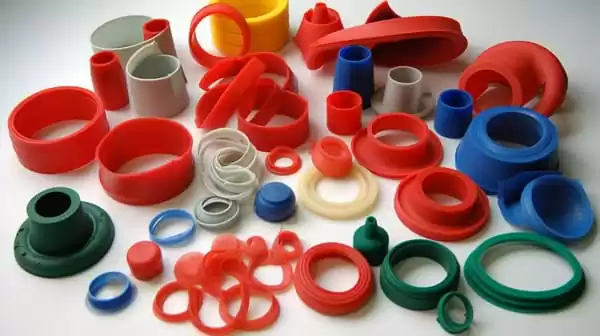
III. How to Prepare a 3D Print for Silicone Molds
A. Constructing the 3D Model
The initial step in producing a 3D print for silicone molds is creating the first 3D printed model. This can be done using specialized software or by adapting existing designs. When creating this model, take into account its end use as well as the material properties of silicone rubber that will be utilized in prototype molds.
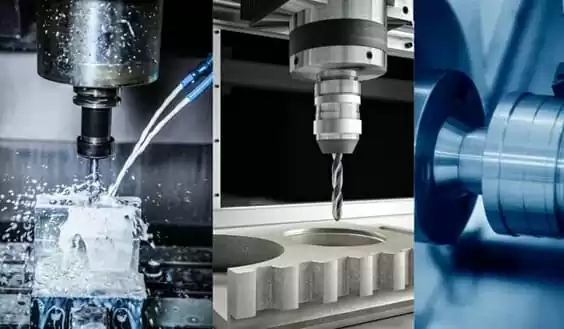
B. Printing the Prototype
After designing the 3D printed model, the next step is to print a prototype. This critical step allows designers to test the fit, form, and function of their part before it goes into mass production. Prototyping can be done using various 3D printing techniques such as Fused Deposition Modeling (FDM), Stereolithography (SLA), or Selective Laser Sintering (SLS).
C. Crafting the Silicone Mold
So, you’ve decided to create your silicone mold! Now all that remains is for you to do:
Once a prototype is 3d printed, the next step is to make a silicone mold. This involves pouring liquid silicone rubber material over smooth surface finishes the first 3d printed prototype and allowing it to cure. After curing is complete, the prototype can be removed from heated mold, leaving behind an impression of its part inside the mold which can then be used for multiple copies of that same part.
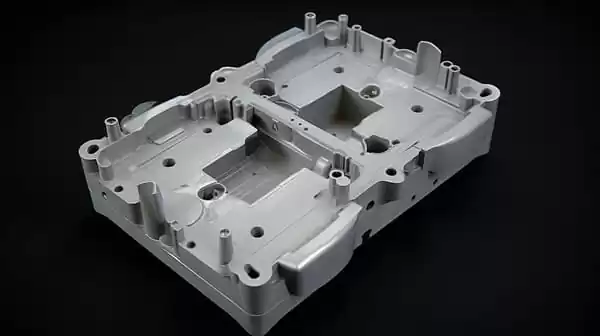
D. Pouring the Silicone Rubber Part
The next step in casting silicone rubber parts is pouring liquid silicone rubber into a mold and waiting for it to cure. Once metal mold is dry, you can carefully remove the silicone part part from its mold – this process can be repeated multiple times for multiple silicone parts in production.
E. Eliminating Support Material From 3D Prints
What are some methods for eliminating support material from the 3D printed prints?
Finally, it is essential to eliminate all support material from a used mold or 3D print before casting the silicone mold or rubber mold or part. This can be accomplished either with specialized tools or chemical treatments. Once this step has been taken, remove support material and your 3D printed silicone mold or part should be clean and ready for use as a prototype in creating a mold for your silicone mold.
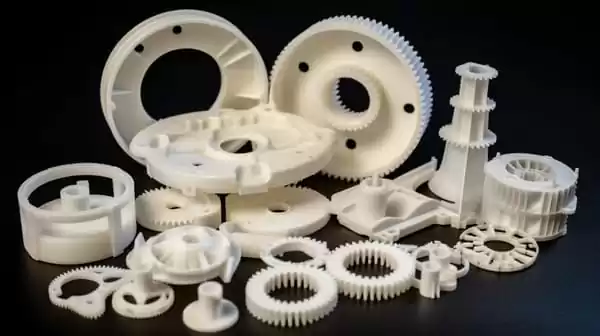
Overall, creating a 3D print for injection molded parts and silicone molds requires meticulous precision. But when done correctly, it can lead to new possibilities and an efficient production process with greater mold design, freedom and improved accuracy.
IV. Applications of 3D Printing and Prototyping for Silicone Rubber Parts
3D printing and prototyping have many applications in the production of silicone rubber parts, making it a highly valuable technology. Some of its most common uses include:
A. Medical Devices – such as hearing aids, prosthetic parts, and surgical tools. 3D printing allows the creation of customized parts that fit an individual’s anatomy perfectly. Furthermore, silicone rubber materials used in medical devices have biocompatibility and sterilization properties which make them ideal for this use.
B. Consumer Goods – such as toys, household items, and personal accessories. 3D printing and prototyping of soft materials offer designers the unique chance to create customized products tailored specifically to an individual’s preferences. Furthermore, silicone rubber materials used in consumer goods offer flexibility and durability.
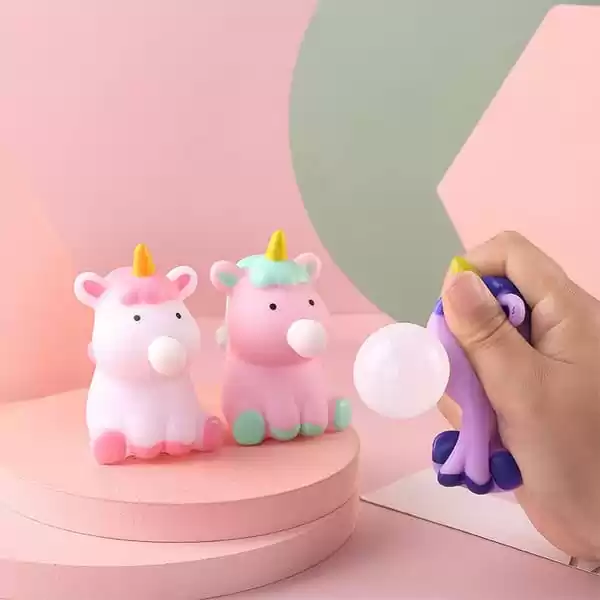
C. Industrial Manufacturing – To produce silicone parts used in machinery, equipment, and automation systems. Silicone rubber parts are popular in industrial manufacturing due to their durability, resistance to extreme temperatures, and flexibility. 3D printing and prototyping offer a faster and more cost-effective alternative than traditional manufacturing processes for producing these parts.
Overall, 3D printing and prototyping for silicone rubber parts have numerous applications that make it a valuable asset in various industries.
V. Comparing Traditional Manufacturing Processes
3D printing and prototyping offer numerous advantages when producing silicone rubber parts, but it is essential to compare this process with traditional manufacturing techniques to fully appreciate its advantages. In this comparison, we will contrast 3D printing and prototyping with two traditional silicone additive manufacturing processes: injection molding and manual casting methods.
A. Injection Molding – including Liquid Silicone Injection Molding (LSIM)
Injection molding is a technique for producing parts by injecting molten material into a mold. This technique is widely used in the production post processing of silicone rubber parts, especially during high-volume runs. Liquid Silicone Injection Molding (LSIM) is another popular injection molding option used for making silicone rubber parts; with LSIM, liquid silicone is injected into an empty mold before being heated and cured to form the final product.
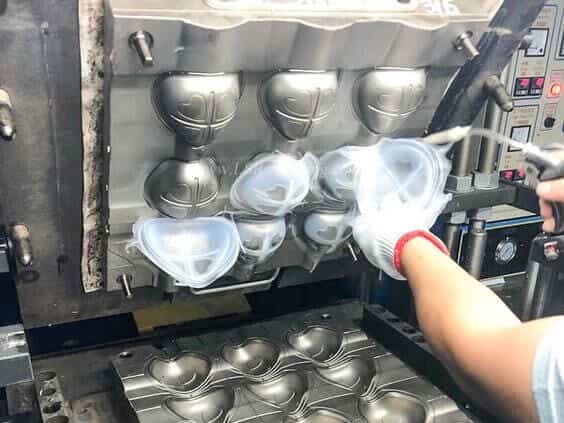
Advantages of Injection Molding
High Production Volume: Injection molding is ideal for quickly and efficiently producing large numbers of parts in low quantities.
Superior Surface Finish: Injection molding provides a smooth surface finish, which is especially essential when producing parts requiring high precision.
High Repeatability: Injection molding produces parts with excellent consistency and repeatability, making it ideal for manufacturing parts that need precise adherence to specifications.
Disadvantages of Injection Molding:
High tooling Costs: Injection molding requires the creation tens of thousands of molds for each part, making it expensive to do so for low-volume, production parts.
Limited Design Flexibility: Due to the specific mold requirement for each injection molded part, injection molding limits design freedom significantly.
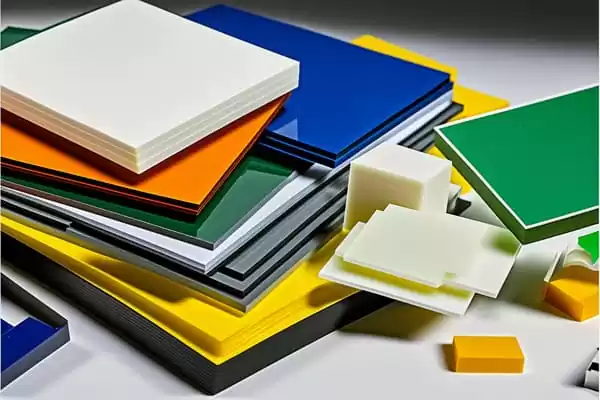
B. Manual Casting Methods
Manual casting methods involve pouring a liquid material, such as silicone rubber, into a mold and allowing it to cure. This process is commonly used for low-volume production and prototyping.
Advantages of Manual Casting Methods:
- Low tooling costs: Manual casting methods require minimal tooling, making it a cost-effective solution for low-volume production.
- Design flexibility: Manual casting methods allow for greater design flexibility than injection molding since molds can be easily modified or created.
Disadvantages of Manual Casting Methods:
- Time-consuming: Manual casting methods can be time-consuming since each part must be cast individually, making it less feasible for high-volume production.
- Limited precision: Manual casting methods may not produce parts with the same level of precision as injection molding or 3D printing.
C. Advantages and Disadvantages of each process
Advantages of 3D printing and prototyping:
- Design flexibility: 3D printing and prototyping offer greater design flexibility than traditional manufacturing processes, allowing for easier modifications and customization.
- Low tooling costs: 3D printing and prototyping require minimal tooling, making it a cost-effective solution for low-volume production and prototyping.
- Improved accuracy and precision: 3D printing and prototyping offer a higher level of accuracy and precision compared to manual casting methods.
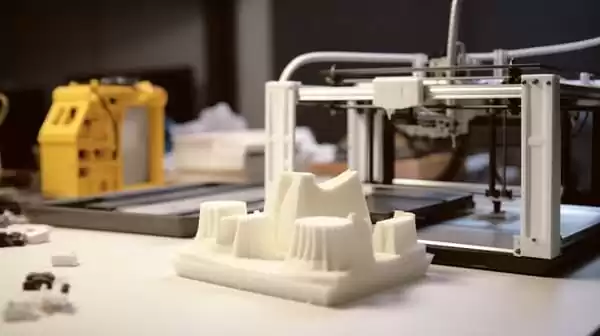
Disadvantages of 3D printing and prototyping:
- Limited production volume: 3D printing and prototyping are ideal for low-volume production but may not be as efficient for producing large quantities of parts.
- Limited material selection: The range of materials available for 3D printing and prototyping may be limited compared to traditional manufacturing processes such as injection molding.
- Surface finish: 3D printing and prototyping may not deliver the same level of surface finish as injection molding.
Overall, each manufacturing process has its own advantages and disadvantages, and the choice of manufacturing process depends on the specific requirements of the project. However, 3D printing and prototyping offer many benefits for producing silicone rubber parts, particularly for low-volume production and rapid prototyping.
VI. Silicone 3D Printing and Prototyping Materials and Techniques
Silicone is an ideal material for 3D printing, mold design and prototyping projects due to its flexibility in both mold design, material properties, ease of use, and other advantages.
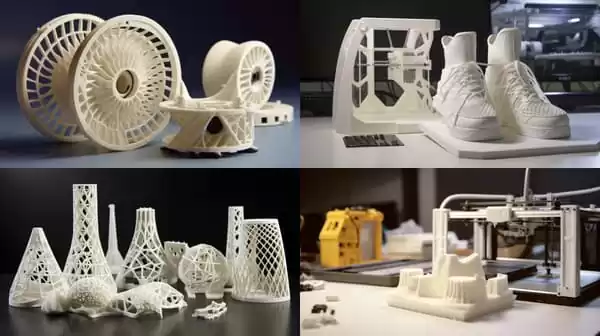
When it comes to 3D printing and prototyping with silicone, there are various materials and techniques to consider. Here we will review some of the most commonly used materials and approaches for 3D printing and prototyping with a silicone material.
A. Materials Selection
Silicone Rubber
Silicone rubber is a commonly used material in 3D printing and prototyping with silicone. Its flexibility, durability, and resistance to extreme temperatures make it ideal for producing parts that need high levels of flexibility but can withstand repeated use. Silicone rubber also lends itself well to high-temperature environments.
Liquid Silicone Rubber (LSR)
Liquid Silicone Rubber (LSR) is a type of silicone rubber commonly used for 3D printing and prototyping. As an injectable liquid material, LSR allows the production of complex geometries with thin walls. It finds applications in medical and consumer products due to its biocompatibility and flexibility.
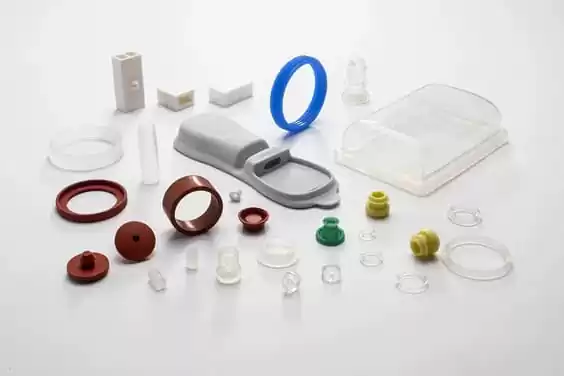
Thermoplastic Polyurethane (TPU)
TPU is a flexible rubber-like material widely used for 3D printing and prototyping. Thanks to its durability and superior abrasion resistance, TPU makes an ideal material for parts requiring high flexibility and wear resistance.
Thermoplastic Elastomers (TPEs)
TPEs are a family of materials that combine the characteristics of rubber and plastic. TPEs boast flexibility, durability, and resistance to chemicals and UV light damage, making them popular in consumer goods production as well as automotive parts production.
B. Techniques
Selective Laser Sintering (SLS)
Selective Laser Sintering (SLS) is a 3D printing technique that utilizes lasers to selectively fuse powdered material such as silicone rubber into solid objects. SLS works best when creating parts with complex geometries and fine details, making it ideal for prototyping and low-volume production runs.
PolyJet
PolyJet is a 3D printing technique that utilizes inkjet technology to deposit small droplets of liquid material, such as silicone rubber onto an open build plate. PolyJet parts boast fine detail and have an even surface finish; making them popular for prototyping or low-volume production runs.
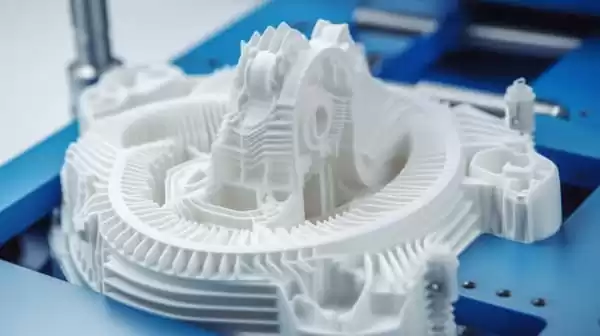
Fused Deposition Modeling (FDM)
Fused Deposition Modeling (FDM) is a 3D printing technique that utilizes a nozzle to extrude thermoplastic material, such as TPU, layer by layer onto an acrylic build plate. FDM is renowned for its strong and flexible parts produced through this process; thus it’s often employed in prototyping or low-volume production settings.
Overall, the selection of material post process and technique for 3D printing and prototyping with silicone must be tailored to the project requirements. Each material post process and technique has its advantages and drawbacks; therefore, it is essential to weigh these factors when deciding on a material or technique.
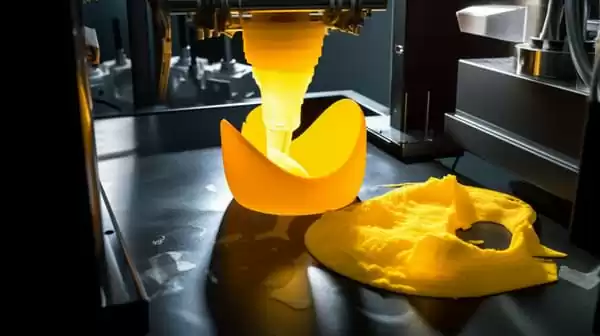
Conclusion
3D printing and prototyping offer numerous advantages for producing silicone rubber parts. These include greater design freedom, increased accuracy and precision, faster production costs, as well as limited volume production capacity and surface finish options. However, there are some drawbacks to take into account such as limited production volume or surface finish requirements.
Finally, 3D printing and prototyping of silicone rubber parts offer new opportunities in additive manufacturing, across a range of industries such as medical devices, consumer goods, and industrial production. As technology progresses, we can expect further advancements in both material ranges post processing, available for 3D printing/prototyping, along with improvements to speed and efficiency within this process.
Overall, 3D printing and prototyping may not replace traditional manufacturing processes such as injection molding, but they provide a viable, alternative method for low-volume production and prototyping. With the continued development of new materials and techniques, 3D printing and prototyping for silicone rubber parts is likely to become even more efficient and cost-effective, creating new opportunities and innovations in the manufacturing industry.