Overmolding of plastic parts. Usually, soft material is used as the overmolding material to form a strong bond with the hard plastic parts.
Through overmolding, to achieve certain special functions needed for plastic parts, such as soft touch, non-slip, button function, foldability, sealing, etc.
Commonly used hard plastics such as PP, ABS, PC, PE, PS, and PA; soft materials commonly used are TPE, TPR, TPU, TPV, PVC, and silicone.
However, based on the analysis of environmental protection and main application fields, the most commonly seen soft covering (adhesive covering) materials in the market are TPE/TPR and silicone.
TPE/TPR and silicone are both excellent soft rubber plastics. Both can be used for overmolding secondary molding, but the two materials still have their different characteristics to the extent that they determine their overmolding applications in different industries.

The difference between TPE software and silicone composition
1.1 Silica gel is divided into inorganic silica and organic silicone compounds
Inorganic silica gel is a highly active adsorbent material, usually made by reacting with sodium silicate and sulfuric acid, and by a series of post-treatment processes such as aging and acid bubbles.
Silica gel is an amorphous material with the chemical formula mSiO2 nH2O, insoluble in water and any solvent, non-toxic and tasteless, chemically stable, and does not react with any substance except strong alkali and hydrofluoric acid.
Silicone is a kind of organic silicon compound, refers to the Si-C bond, and at least one organic group is directly connected with the silicon atom of the compound, customary also often through the oxygen, sulfur, nitrogen, and other organic groups connected with the silicon atom of the compound is also treated as organic silicon compounds. Silicone is mainly divided into three categories: silicone rubber, silicone resin, and silicone oil.
1.2 There are many kinds of TPEs, which are usually based on styrene elastomer modification
Usually, TPE refers to styrene-based thermoplastic elastomer SBC as the basis of the blend of modified materials TPES there are many types of TPE (including TPES, TPV, TPU, TPEE, TPO, etc.). The TPE in this article mainly refers to the SBC-based modified TPES-type elastomer.
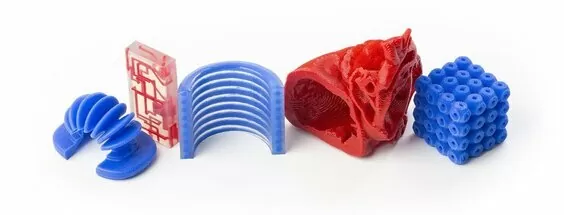
Differences in appearance
Inorganic silicone chemical formula xSio2-yH2O. transparent or milky white granular or bead-like solid.
Organic silicone has multiple different ones, containing silicone oil, silicone rubber, and silicone resin. Therefore the appearance is diverse, in a liquid, solid block, or granular available.
TPE is a blended material with no fixed composition. But the appearance is generally transparent or white granules.
Performance differences
Heat resistance
TPE is usually heat-resistant 80~100℃, silicone can usually withstand 100~150℃ high temperature.
Resilience, permanent deformability
TPE is a physical cross-linked structure, physical properties of TPE is good, but there is a certain permanent deformation; silicone usually adds a coupling agent for cross-linking, solid silicone and liquid silicone, are chemical cross-linked structure, and good resistance to permanent deformation. Or silicone has more elasticity and resistance to deformation than TPE.
Food grade characteristics
For food-grade materials, the specific test methods vary from country to country and region to region. But the current basic understanding is as follows.
A silicone composition is relatively single, most silicone through the oil solvent (such as olive oil, n-hexane, etc.) residual test, in line with the U.S. food-grade standard value FDA 21CFR 177.2600 and the German food contact materials standard LFGB.
TPE base resin and softening oil may contain residual organic small molecules, which can be easily dissolved in oily liquid.
At present, except for a few specific silicone material formulations that can comply with 21CFR 177.2600 and LFGB, most TPEs, especially low hardness TPEs, cannot pass the two food grade tests.
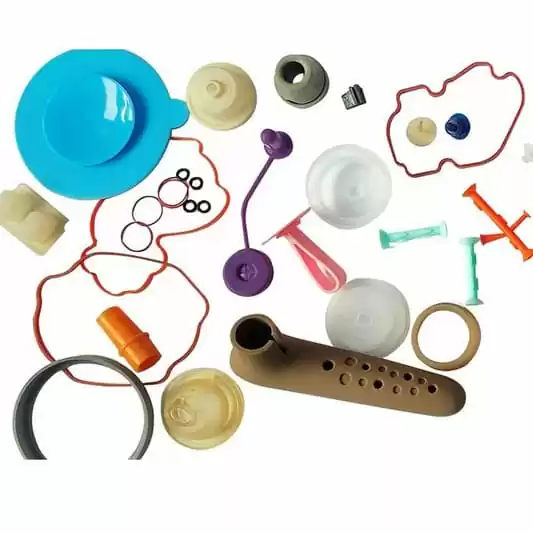
Molding Equipment
Silicone rubber is thermosetting. Most of them use a hydraulic press to mold, but some liquid silicone LSR can be molded by injection machine.
TPE is thermoplastic, mostly using an injection molding machine or extrusion machine to extrude molding.
Trim and waste recycling
TPE trimmings and scrap can be 100% recycled.
Silicone scrap is difficult to recycle.
Overmolding
TPE and most hard plastics such as PP, ABS, PC, PA, PS, PE, SAN, etc. can be well overmolded and bonded as one without the need for glue to complete.
For overmolding of silicone and hard plastics, glue is usually applied in advance, and then injection bonding is performed. However, it is said that there is modified silicone in foreign countries that can be directly over-molded and bonded without the need for glue.
Application of silicone overmolding
Silicone (solid) is usually pressed with oil, while silicone used for overmolding is usually in liquid form for fast injection molding. Examples of applications for overmolding with silicone are as follows.
Kitchenware, tableware, and other products with high requirements for environmental protection (oil resistance, high-temperature resistance direct contact with food), products with high requirements for elasticity, and resistance to permanent deformation (such as some key products that need to be pressed repeatedly).
Silicone overmolding features: when secondary injection, it is usually necessary to brush matching glue in advance to ensure excellent overmolding adhesion between silicone and hard plastic parts; usually, a higher injection mold temperature is used, and attention should be paid to the deformation of thin parts that may occur during overmolding.
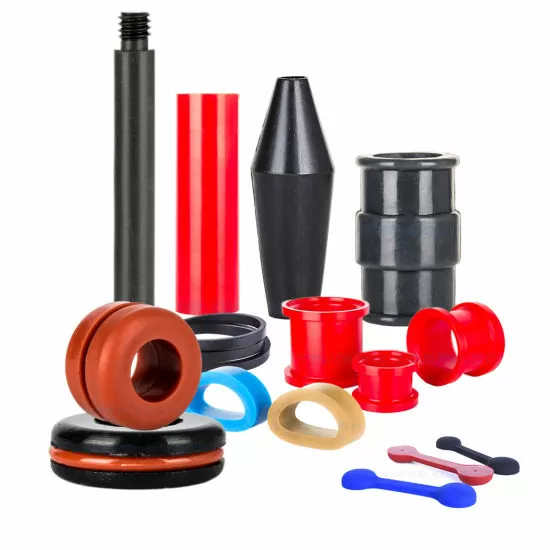
Cost comparison
Low-end solid silicone, the price is comparable to low-end TPE, about 20,000 yuan/ton or less.
Mid-to-high-end (liquid) silicone rubber, the price is close to high-end TPE, about 30,000~50,000 yuan/ton.
However, most of the TPE applications are in the middle and low-end market, while the middle and high-end silicone accounts for the mainstream of the market.
Therefore, overall, TPE price is still cheaper than silicone. If we consider production efficiency and silicone material reuse, TPE advantage will be more obvious
Identification method
Silicone: ignite, burn as a bright flame, produce white smoke, and the residue is a white powder.
TPE: lit, the flame is yellow or yellow with green at the lower end, producing either light or thick black smoke.