In recent years, the application of liquid silicone has become more and more widespread, and its transfer molding technology has also been developed rapidly.
Liquid silicone is a non-toxic, heat-resistant, highly recoverable flexible thermosetting material, whose rheological behavior is mainly characterized by low viscosity, rapid curing, shear thinning, and a high coefficient of thermal expansion.
Liquid silicone vulcanized products have the advantages of strong temperature adaptability, high purity, good transparency, low content of volatile substances, oil resistance and aging resistance, chemical resistance, outstanding insulation, etc.
They are widely used in automobiles, construction, the electronic industry, medical care, mechanical engineering, the food industry, and other fields. Medical care, mechanical engineering, the food industry, and other fields are widely used.
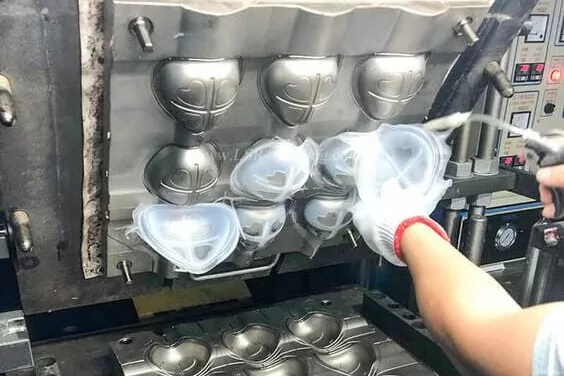
Liquid Injection Molding
Among the liquid silicone molding processes, liquid injection molding (LIM) technology was first used. Liquid injection molding is the precise measurement of A and B rubber (ingredients such as 1:1 or other ratios).
This en transported to the static mixer, mixed, and then transported to the injection device, by the injection device and then mixed and injected into the hot mold, the rubber in the mold after rapid vulcanization reaction, forms a certain strength and elasticity of silicone rubber products.
Among the components of liquid silicone, the role of catalysts and inhibitors is particularly important. Since the vulcanization reaction needs to occur in liquid silicone, catalysts are added to accelerate the vulcanization reaction.
When the temperature of liquid silica gel reaches the vulcanization temperature, it has a very high vulcanization speed (at 200°C, the vulcanization speed reaches only 3 to 5s per mm of wall thickness), and liquid silica gel cannot exist in a temperature of 40 to 50°C for a long time (at 50°C, even if the vulcanization temperature is not reached, the reaction will occur slowly within 3 to 4 minutes).
Therefore, to keep the liquid silica gel temperature from the vulcanization reaction until the vulcanization temperature is reached, it is also necessary to add inhibitors to its components. When the vulcanization temperature is reached, the inhibitor fails and the liquid silica gel reacts rapidly.
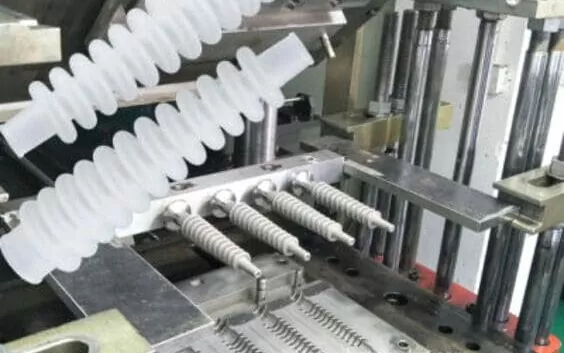
Molding characteristics
1) Compared with solid rubber injection molding, liquid silicone injection molding does not require plasticizing, mixing, performing and other operational processes, saving manpower, material, and energy, and reducing equipment investment and floor space.
2) Liquid silicone injection molding can realize the automatic processing process under fully enclosed conditions, eliminating the deviation of manual operation, reducing the influence of various variables and pollution in the process, and ensuring the dimensional accuracy and intrinsic quality of the product, which is beneficial to the application of liquid silicone in the medical field.
3) Since the viscosity of liquid silicone is very low (generally within the range of 10~1000Pas) and its fluidity and processability are good, its injection pressure is much lower than the injection molding pressure of solid rubber and plastic, generally the injection pressure is 20MPa.
In some cases, it can be lower than 1MPa, so it can produce products without flying edges, reduce material waste, and at the same time reduce the wear and tear of equipment and molds.
In addition, due to the good fluidity of liquid silicone, it is especially suitable for molding large products, products with extremely complex shapes, or ultra-thin products, such as ultra-thin products with a thickness of 0.5mm and a length of 100mm, which are difficult to mold for solid rubber.
4) The vulcanization speed of liquid silicone is very fast. The vulcanization reaction can be completed in tens of seconds to minutes under 160-220 when injecting and molding, thus its injection molding cycle is short and the production efficiency is high.
5) The back pressure required for liquid silicone in the screw metering is very small, generally less than 1.5MPa, and for some liquid silicone rubber components with very low viscosity, even no back pressure can be set, mainly because of the low viscosity silicone fluidity is very good, and the normal work of liquid silicone in the gas content is very low.
On the contrary, a large back pressure will lead to an increase in the density of unvulcanized silica gel and destroy the precise measurement effect of the metering device.
6) Liquid silicone does not shrink during the injection molding process, but because silicone has a high coefficient of thermal expansion.
Thus there is usually a shrinkage of 2% to 3% after demolding and cooling, the exact shrinkage data depends on the material formulation. From the processing point of view, the designer should take some factors affecting shrinkage into consideration in advance.
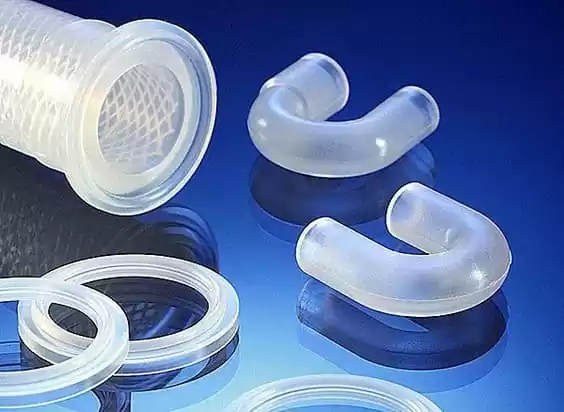
Design points
1) Adopt liquid temperature control technology to control the barrel and nozzle temperature control between 5 and 25. Cooling water is usually used as the cooling medium.
2) To prevent the liquid silicone from curing, a hydraulically driven needle valve-type sealing nozzle is used. The needle valve immediately closes the injection nozzle when the injection is finished.
3) In the injection molding process, the mixing uniformity of A and B rubber directly affects the quality of the products after vulcanization, and in the case of some products with high-quality requirements, the mixing degree of the rubber after the static mixer cannot fully meet the requirements.
The supplementary mixing effect of the screw can better meet the requirements. And because the rubber is liquid, do not need to undergo plasticization, so the screw is designed to become a non-compression or low compression and shear weak screw and does not require a large length-to-diameter ratio.
Generally should not be directly applied to the injection molding machine screw structure, because its screw structure usually has a strong shear effect, and easily causes local vulcanization, affecting the performance of the product.
So the design of the screw specifically for the liquid silicone injection machines is of great significance. If the product quality requirements are not high, you can consider using a plunger instead of a screw to complete the injection.
4) Liquid silicone viscosity is low, lower injection pressure can produce higher injection speed, and the air trapped in the mold is easily involved in the product. To make high-quality products, consider evacuating the mold before injection.
You can also use the clamping force to achieve the purpose of driving out the air, that is, when the clamping force is low, the liquid silicone filled to 90% to 95% of the cavity, and then the clamping force will be adjusted higher, so that not only can effectively exhaust, but also can avoid the liquid silicone overflow, resulting in the flying edge.
5) The viscosity of liquid silica gel is low, and it is easy to form backflow during injection, so the sealing effect of the non-return ring must be good, and it is generally not suitable for direct application of the non-return structure on the injection molding machine.
Its working process: when the screw is metering, the rubber material is pushed by the screw under the force of the screw, through the hole on the spigot ring, pushing away the non-reverse ring and entering the screw head.
6) Liquid silicone injection molding process needs to use cold runner technology, and the runner should be cold enough.
There needs to be good enough insulation between the runner and the mold to ensure that the liquid silicone does not vulcanize in the runner and clog the nozzle, which helps reduce waste generation and save costs.
7) If extremely soft and sensitive, demanding products are being molded, consider adding pneumatic brushes to clean the injection molds and using robots to eject the products.
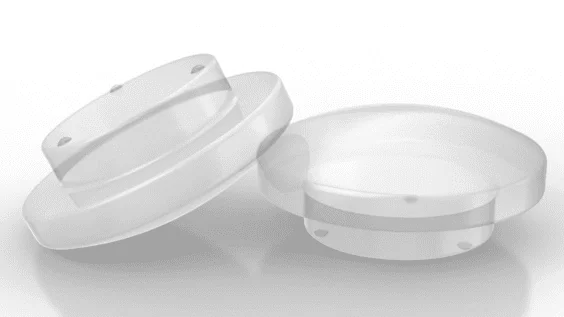
Pouring and molding
Most of the composite insulators in the power industry are molded with liquid silicone, and the volume of insulators used in high-voltage aspects is usually larger, and the mold volume for molding insulators is also larger.
When liquid silicone is used to produce insulators, the vulcanization speed is much faster than that of solid silicone, so if ordinary injection devices are used to inject the rubber, it is easy to cause the flow channel to be blocked by the vulcanized silicone before the liquid silicone fills the mold so that the performance of the injection molded products cannot meet the requirements, and even the complete products cannot be molded. Based on these problems, the injection molding process was developed based on injection molding.
The basic molding principle of plastic injection molding is: A and B are pumped into the metering system, and after metering, they enter into the static mixer, and after fully mixing in the static mixer, they directly enter into the mold; before the A and B mixed rubber enters into the mold, the mold is firstly kept at a lower temperature by using the mold temperature machine.
After the rubber is filled with the mold, it starts to heat the mold to make it reach a set temperature, then keeps warm, vulcanizes, cools, and opens the injection mold to complete the molding process.
Open the mold to complete the molding process. This kind of molding method is suitable for products with large volumes and low appearance quality requirements.
This thermoplastic injection molding method eliminates the need for injection devices, saving costs and machine space.
However, due to the lack of screw to remix and homogenize the rubber from the static mixer, and the metering and mixing system providing uneven and discontinuous pressure, the injection molding cycle is usually relatively long, so it is not suitable for high-speed, high-output, and high-quality requirements of the products.
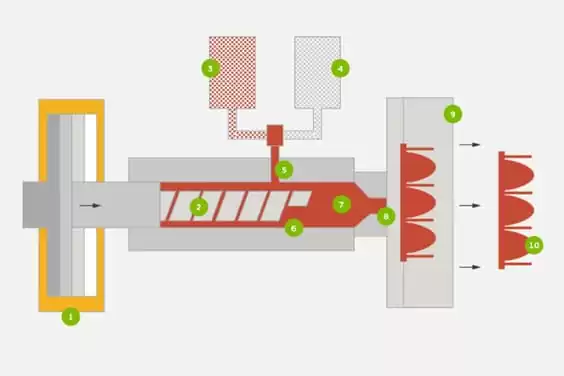
The application of liquid silica gel
1) Liquid silicone has good biological inertness and biocompatibility, very low concentration of small molecular weight components, and ideal physical properties, and can be modified at the polymer level, thus becoming the material of choice for medical devices and medical products.
Applications such as valves or seals for medical devices, medical implants, medical gloves, medical catheters and balloons, artificial organs, dental impression materials, biopics for hearing aids, etc.
Because of the medical field products, its profit margin is high and the market space is large, so the development of liquid silicone in the medical field has a broad prospect and far-reaching significance.
2) Liquid silica gel is widely used in the electric power industry to manufacture composite insulators because of its unique chemical bonding and structure, high and low-temperature resistance, water repellency, leakage resistance and corrosion resistance, electrical insulation, and many other excellent properties.
Along with the western development, power grid upgrading, large-scale construction of high-speed rail, and a series of national projects will bring a large number of insulation products demand, giving rise to a more massive market, so the development of liquid silicone in the power industry has broad market prospects.
3) Liquid silicone products also have a wide range of applications in the automotive industry. In foreign countries, liquid silicone used in the automotive industry accounts for 35% of the liquid silicone used, which is the largest application area, while in China, the proportion of its application in the automotive industry is small, which is mainly because the domestic liquid silicone molding technology is not too mature.
In the automotive industry, liquid silicone is mainly used in automotive seals, highly transparent LED lights, large and complex optical components, skin protection for spark plug connectors, switch covers, rain sensors, and diaphragm sheets for central locking systems.
4) Liquid silicone products are widely used in the manufacture of computer and remote control keys, cell phone and digital product covers, liquid silicone nipple bottles, liquid silicone waterproof eye masks and gloves, liquid silicone toys, and liquid silicone household appliances because of their soft touch, elasticity, waterproofness and resistance to high and low temperatures.
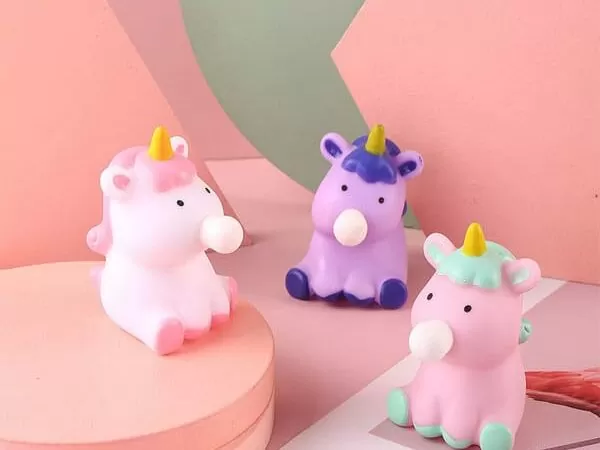
Conclusion
In addition to the liquid injection molding and casting molding processes introduced in this paper, there are also co-injection molding, binary molding, mosaic molding, extrusion molding, physical foam molding, and other processes.
Mastering and applying liquid silicone molding technology not only can produce high-quality products but also can save energy and reduce waste, so the development and application of liquid silicone molding technology are of great importance.
At present, the research of liquid silicone molding technology in foreign countries is getting deeper and deeper, and the products developed are various and the application fields are becoming more and more extensive.
While China’s liquid silicone rubber molding technology is still in its infancy, there is still a lot of research and development work to be done.
However, we believe that shortly, through the joint efforts of our colleagues, the liquid injection molding process technology will be developed rapidly in China.