Introduction
Compression molding manufacturing process is a widely used process for creating composite materials with superior strength and durability. It involves applying intense pressure and temperature to molding material inside of a mold cavity, causing it to take on the desired shape. Materials used in compression molding can range from thermoset materials such as epoxy resin and bulk molding compound (BMC), to polymer matrix composites (PMC) and sheet molding compounds (SMC).
Material viscosity plays a significant role in compression molding, determining its resistance to flow and deformation under stress. It plays an integral role in controlling material flow during molding, impacting its mechanical properties as well as its dimensional accuracy.
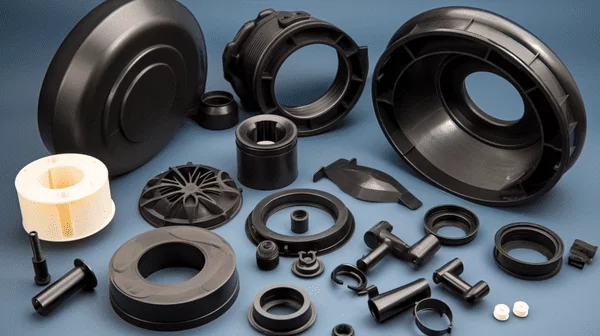
In this article, we’ll investigate the factors affecting compression molding process and materials used. Additionally, we’ll discuss key considerations during mold design such as viscosity of materials used in compression molding. Moreover, we’ll cover different compression molding processes and their mechanical properties, applications of compression molding, and potential future developments within manufacturing.
II. Factors Affecting Compression Molding Process
Compression molding is a highly-specialized manufacturing process that requires careful consideration of multiple factors. These include high pressure and temperature requirements, molding material and composition, mold design and complexity, curing process and time.
Pressure and temperature needed for compression molding differ depending on the material being molded and the complexity of the mold design. Additionally, the type and composition of molding material play a significant role in this step; you should carefully consider which material meets your application requirements before beginning this step.
The design and complexity of a mold can significantly influence how much pressure and temperature is required, as well as the final product’s dimensional accuracy. Achieving proper mold design is essential for achieving desired mechanical properties and precision in dimension.
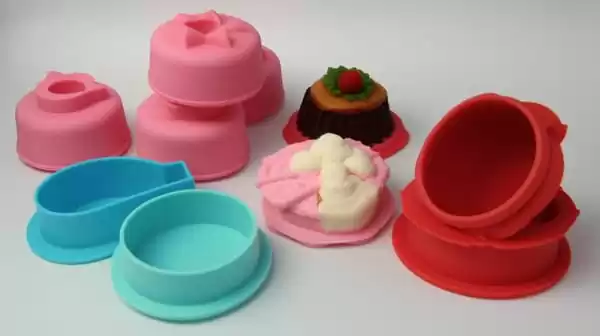
Curing process and time are vital elements in compression molding. The duration of curing depends on the material being molded, the mold design, as well as temperature and pressure applied during the procedure. Accurate control over these variables is necessary to produce desired mechanical properties and dimensional accuracy in the final product.
Overall, proper consideration of all these elements is essential for obtaining consistent and high-quality results when compression molding.
III. Materials Used in Compression Molding
Compression molding can be used with a range of materials, the most popular being thermoset materials, polymer matrix composites (PMC) and sheet molding compounds (SMC).
Thermoset materials
Thermoset materials such as epoxy resin and bulk molding compound (BMC), are widely used in compression molding due to their superior strength, stiffness, and dimensional stability. These polymers undergo a chemical reaction when heated and cured, creating an extremely strong material with excellent mechanical characteristics.
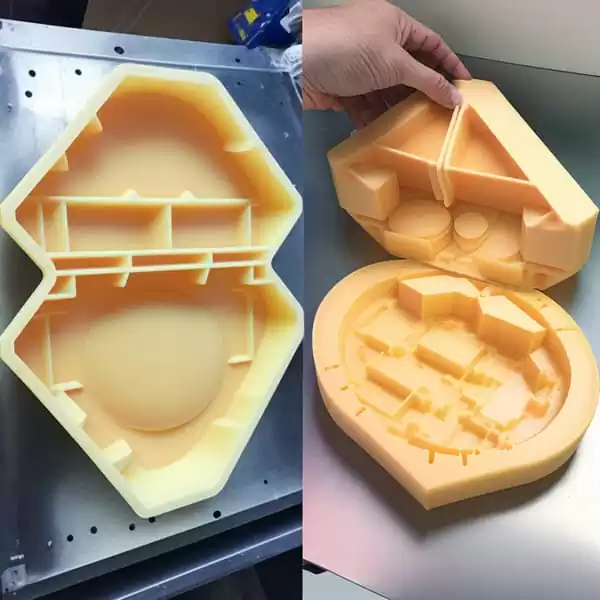
Polymer matrix composites (PMC)
Polymer matrix composite (PMC) are another material commonly used in compression molding . These composites consist of a polymer resin matrix reinforced with fibers such as glass, carbon or aramid for increased strength and stiffness. As such, PMCs have applications where high strength is necessary.
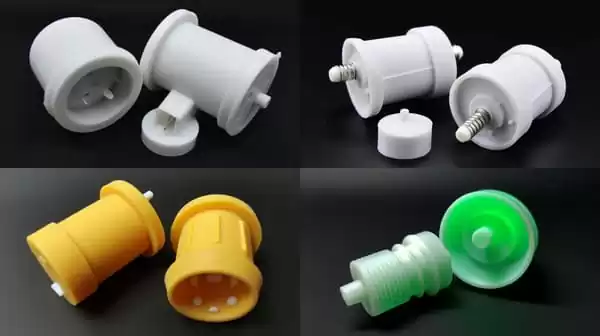
Sheet molding compounds (SMC) and glass mat thermoplastics (GMT)
Sheet molding compounds (SMC) and glass mat thermoplastics (GMT) are both employed in compression molding. SMC is composed of a thermoset resin matrix, chopped glass fibers, and mineral fillers while GMT has an acrylic resin matrix with randomly oriented glass fibers. Both materials offer excellent strength, stiffness, and dimensional stability when compressed.
When selecting material for compression molding, there are a few things to consider: mechanical properties desired, cost efficiency and production volume. A correct selection of material is key in achieving the desired outcomes in compression molding.
IV. Mould Design Considerations for Compression Molding
Are you in the market for a compression mold? Consider these design factors when creating your design.
When designing a mold for compression molding, the design of the mold is paramount to achieving success. Take into account all relevant requirements when crafting your design; here are some key aspects to keep in mind when crafting this important step:
Mold Cavity Design and Material Selection
When designing a mold cavity, the shape and size should be taken into consideration. Furthermore, ensure the material used has excellent thermal conductivity as well as resistance to wear-and-tear.
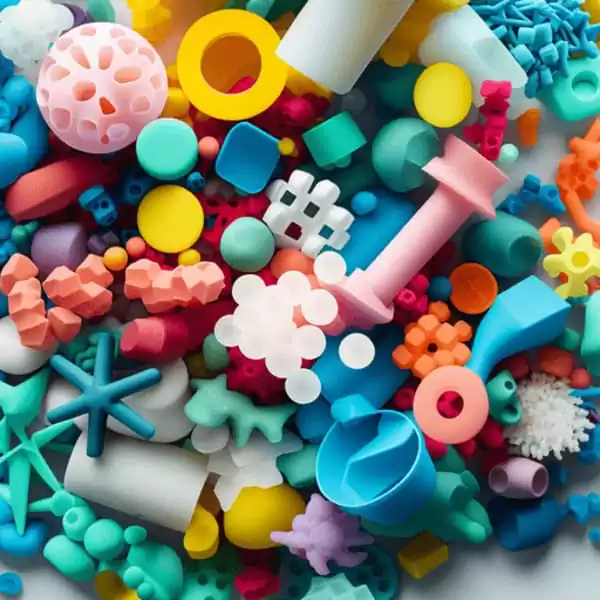
Internal Structure of the Mold
The internal structure of a mold, including its placement and distribution of vents and gates, can influence material flow during molding. A proper arrangement and distribution of vents and gates helps guarantee even material distribution throughout its cavity.
Mold Temperature and Pressure
The molding temperature and pressure should be carefully controlled depending on the material being molded and the complexity of the mold design. Both temperatures and pressure have an effect on mechanical properties as well as dimensional accuracy of the final product.
Surface Finish and Dimensional Stability
Achieving the desired aesthetics and functional requirements requires that parts have a smooth, glossy surface finish. Therefore, it is essential that the mold be designed to produce this desired surface finish. Furthermore, mold stability should also be ensured; any dimensional changes during molding should be minimized.
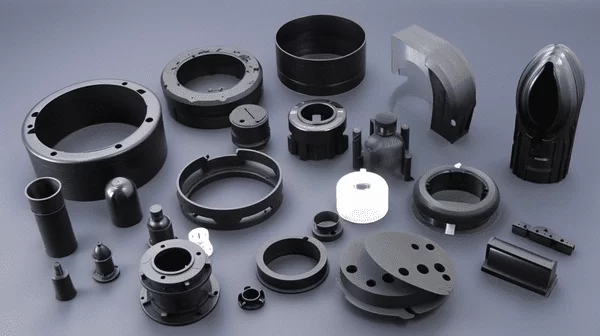
Residual Stresses in Molded Parts
Residual stresses can develop in molded parts due to cooling and curing during the production process. Therefore, mold design should be optimized to minimize these stresses, which could negatively affect mechanical properties and dimensional accuracy of the final product.
Adequate consideration of all these variables when designing a full sheet molding compound is essential for obtaining the desired mechanical properties, dimensional accuracy, and surface finish of the final product.
V. The Role of Material Viscosity in Compression Molding
Definition of material viscosity
Material viscosity is a critical factor in the compression molding process. Viscosity refers to a material’s resistance to flow and deformation under applied stress, and in compression molding it determines its flow behavior during compression molding.
How material viscosity affects compression molding
Viscosity of a material has an effect on how well it fills a mold cavity and distributes throughout it. High viscosities require higher pressures and temperatures for proper flow, while low viscosities flow too freely, leading to flash or distortion in the material. Viscosity also has an effect on mechanical properties as well as dimensional accuracy of the final product.
Importance of selecting the right viscosity for the material being molded
Selecting the proper viscosity for a material to mold is essential to achieve desired results. Factors like temperature, pressure and curing time can all be adjusted to achieve this balance. Achieving uniform filling of the mold cavity through proper viscosity control ensures an even and high-quality end product.
Finally, material viscosity plays a crucial role in the compression molding process. By properly managing and controlling material viscosity, one can ensure consistent and high-quality results when compression molding.
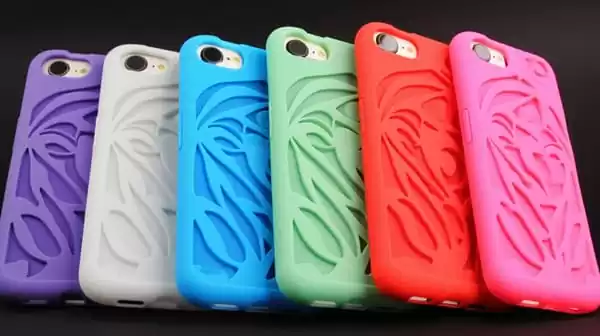
VI. Compression Molding Processes
Compression molding is a popular manufacturing technique used for creating high-strength composite materials. There are various compression molding processes, such as wet compression molding, resin transfer molding (RTM), and injection molding.
Wet compression molding
Wet compression molding involves impregnating reinforcement fibers with a liquid resin before placing them into a mold cavity. Once closed, pressure and heat are applied to cure the material – an efficient method for producing high-strength, high-performance composite parts.
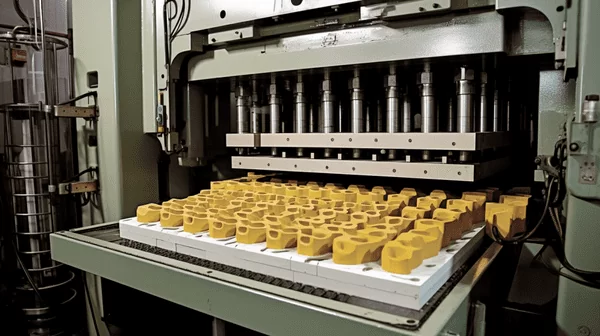
Resin Transfer Molding (RTM)
RTM is a closed-mold process that involves injecting liquid resin into a mold cavity. Reinforcements fibers are placed inside the cavity before injection of resin under pressure to imbue them with resin. Finally, heat is applied to cure the material, making RTM popular for producing large composite parts with complex shapes.
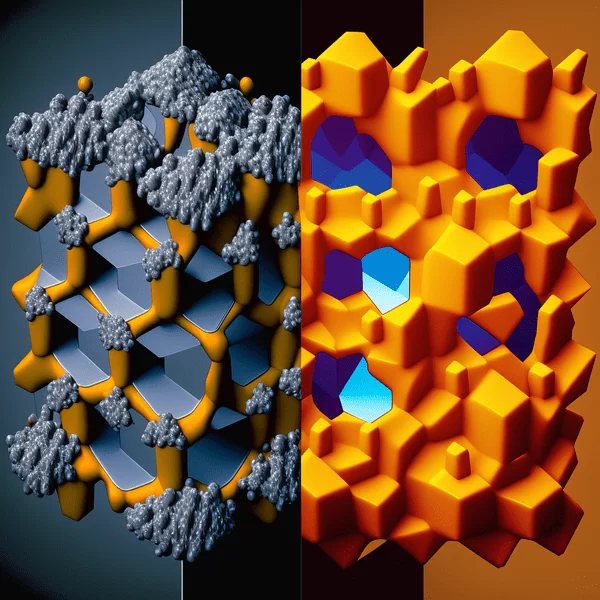
Injection Molding
Injection molding involves injecting thermoplastic material into a mold cavity. After it cools and solidifies, the part can be released. This method is ideal for producing large numbers of low-cost parts with complex geometries.
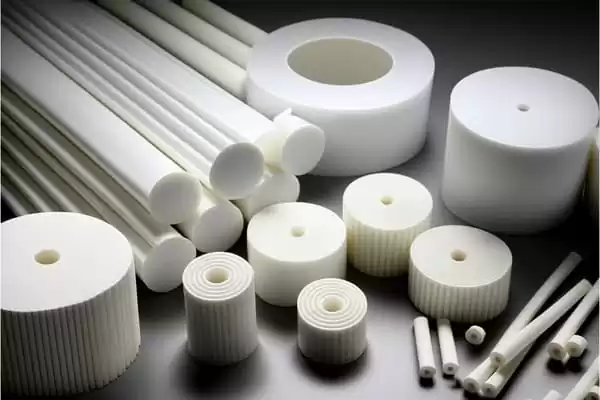
Differences between compression molding and other molding techniques
Compression molding shares some similarities with other molding techniques, such as injection molding. However, there are key distinctions between them. For instance, compression molding utilizes higher pressure and temperature which results in materials with greater strength and stiffness. Furthermore, compression molding permits the use of reinforcement fibers which further boost material properties.
Overall, compression molding offers distinct advantages over other molding processes, making it a popular choice for creating high-strength composite materials.
VII. Mechanical Properties of Compression Molded Parts
Compression molding parts have the mechanical properties expected from them, as their construction requires no reinforcement whatsoever.
Compression-molded parts must meet certain mechanical specifications depending on their material composition and fiber reinforcement used.
Polymer composites are often employed in compression molding, composed of a polymer resin matrix reinforced with fibers such as glass, carbon or aramid. The fiber reinforcement increases the strength and stiffness of the material, making it ideal for applications requiring high mechanical performance.
Compression molding processes use various reinforcement fibers, with the type and amount having an important influence on the mechanical properties of the final product. Carbon fibers for example can produce materials with superior strength and stiffness while glass fibers offer higher stiffness but lower strength levels.
In addition to fiber reinforcement, high density polyethylene (HDPE) in compression molding can also improve the thermal properties of the material. HDPE’s excellent thermal conductivity helps dissipate heat more effectively, producing materials with improved thermal stability.
Overall, the mechanical properties of compression molded parts are determined by several factors, such as material composition, type and amount of reinforcement fibers used, and additives like HDPE. Achieving desired mechanical performance from these factors requires careful selection.
VIII.Compression Molding Applications
Compression molding is an excellent tool for creating various products by applying pressure on them.
Compression molding is an innovative manufacturing process with numerous uses in various industries and applications. Common examples of compression molding include:
Automotive Industry
Compression molding is widely used in the automotive industry to fabricate engine components and other complex geometries. Due to its high strength and stiffness, materials produced through compression molding make them ideal for applications where performance and durability are essential factors.
Aerospace Applications
Compression molding is often employed in the aerospace industry to fabricate high-strength, lightweight composite parts. The cost advantages and swift production processes associated with compression molding make it a desirable option for aerospace manufacturers.
Medical Industry
Compression molding is widely used in the medical industry to manufacture components like syringe stoppers. With its superior precision and dimensional accuracy, compression molding provides the ideal solution for crafting parts with tight tolerances.
Finally, compression molding is a widely-used manufacturing process used in various industries and applications. Its capacity to manufacture high-strength materials with complex geometries and tight tolerances make it ideal for industries where performance and durability are essential factors.
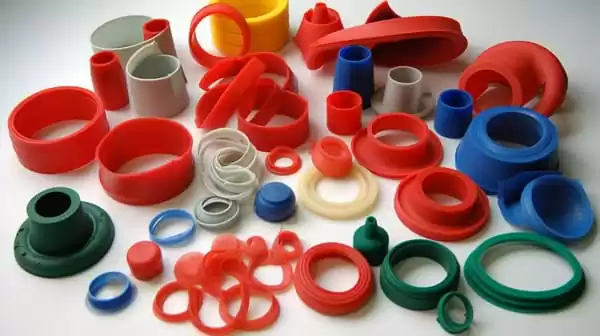
Conclusion
Compression molding is an extensive manufacturing process used in many industries and applications. It utilizes high pressure and temperature to produce strong composite materials with complex geometries and tight tolerances.
Material viscosity plays a significant role in compression molding, as it directly influences the flow behavior and mechanical properties of the final product. Achieving consistent, high-quality results requires proper control over material viscosity during compression molding.
Future developments in compression molding will involve the use of advanced materials like nanocomposites and bio-based materials, as well as new manufacturing methods like additive manufacturing. These innovations are expected to enhance performance, efficiency, and sustainability within the compression molding process.
Overall, compression molding is a dependable and cost-effective manufacturing process with numerous advantages, such as high strength and stiffness, complex geometries, and tight tolerances. By properly taking into account all factors involved in compression molding – including material viscosity – one can ensure the desired result and meet specific requirements for various applications.