Introduction
Compression molding is a manufacturing process used to produce rubber products using raw materials like silicone rubbers. Raw materials are placed into a heated mold cavity before compression molding compresses them to produce the final product. Compression molding offers greater control over its shape, size, and texture compared with injection molding methods like these.
One key advantage of compression molding is its capacity for customizing silicone material’s color and texture, enabling unique products to meet specific design specifications. In this article, we will look at various aspects of custom silicone rubber colors and textures used in compression molding.
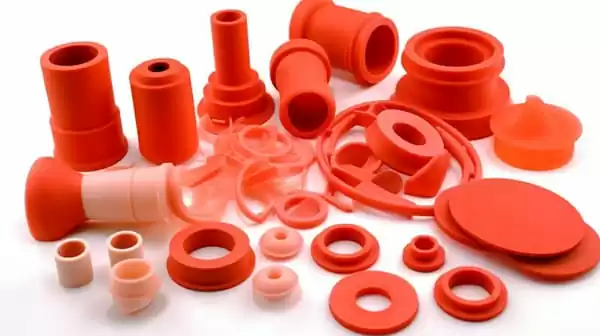
II. Materials used in compression molding
Raw materials used in molding process
Compression molding is a manufacturing process that uses raw materials such as silicone rubbers, EPDM, neoprene, and Viton rubber to produce rubber products through compression molding.
Silicone rubber is one of the most widely-used compression molding materials due to its superior properties such as strength, temperature resistance, and flame retardancy. Furthermore, it can easily be molded into complex shapes and textures for use across a range of applications.
EPDM rubber material is popularly used for compression molding applications due to its excellent weather ability, chemical resistance, and low compression set. Neoprene is another synthetic rubber that offers great weatherproofing properties against sunlight exposure, UV rays, and weathering effects.
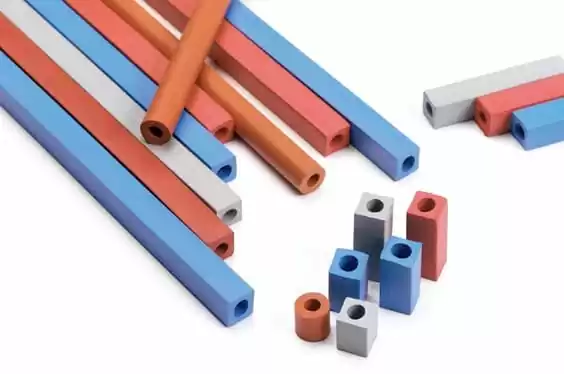
Viton rubber material is an advanced solution designed to resist harsh chemicals and extreme temperatures, protecting applications where its use would otherwise prove too problematic.
Comparison of silicone rubber and other rubber materials
Silicone rubber stands out among compression molding materials like EPDM, neoprene, and Viton in its unique properties and benefits; yet silicone outshines its peers thanks to several key advantages over these other materials.
Silicone rubber offers many advantages for applications involving high temperatures, including its ability to withstand up to 200degC temperatures, making it suitable for automotive and aerospace components. Furthermore, silicone rubber’s resistance against water, chemicals, and UV radiation makes it a durable material suitable for various uses.
Silicone rubber often stands out against EPDM due to its higher tensile strength and flexibility, while EPDM stands out due to its outstanding weather ability, chemical resistance, and low compression set properties.
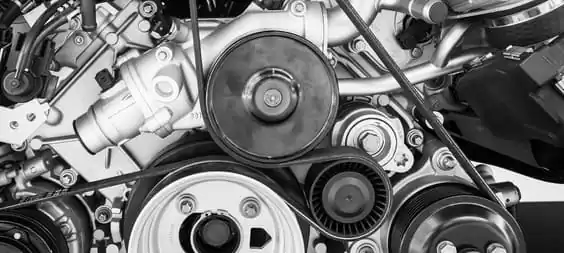
Neoprene is a synthetic rubber material with excellent resistance to ozone, sunlight, and weathering; however, its flexibility does not match that of silicone rubber. Viton rubber offers superior chemical and temperature resistance but may be more costly.
Overall, the choice of material used in compression molding will depend on your project requirements and specific goals. While silicone rubber offers some distinct advantages over other rubber materials, each material offers unique properties and benefits which make it suitable for various uses.
Liquid silicone and uncured rubber
Compression molding with liquid silicone or uncured rubber materials can also be utilized, in addition to traditional rubber materials.
Liquid silicone is a two-part material, typically mixed and then injected into mold cavities for use. Due to its highly flowable characteristics, liquid silicone fills even intricate mold designs without fail. Furthermore, its resistance to heat and cold makes liquid silicone an excellent choice in numerous industries, including healthcare and automotive applications.
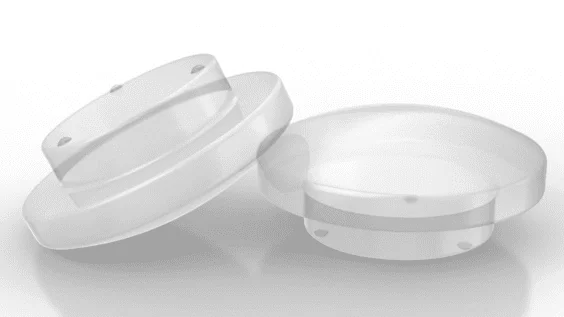
Uncured rubber is an unfinished material used for prototyping or small-scale production runs, making it an economical way of testing new product designs before committing to full-scale production runs. Furthermore, uncured rubber gives more design freedom by permitting adjustments as its material can easily be reworked or modified if changes need to be made during production runs.
Overall, choosing between liquid silicone and uncured rubber depends upon the requirements of a project. Both materials offer specific advantages that can be tailored specifically for any given endeavor.
III. Compression molding process
Compression molding is a manufacturing process in which raw materials are placed into a heated mold cavity and compressed to form the final product. The entire process includes several stages: preheating, loading, compressing, curing, and demolding.
Compression molding uses two spaces – mold cavities and tool molds – to compress raw material. Pressure is applied by pressing down on these devices so they compress raw material to its desired shape, size, and texture during compression molding.
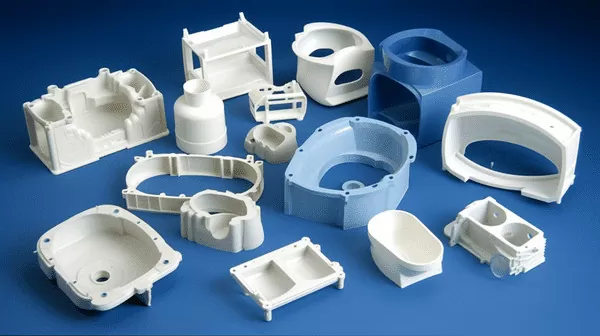
Compression molding offers several advantages over other molding methods like injection or transfer molding, including more control over texture and more material choices, along with lower production costs at low to medium-volume production runs.
Compression molding vs. other methods will depend on the specific requirements of your project, including design, size, and intended use of the final product. However, compression molding remains one of the more widely utilized processes for producing high-quality molded rubber products.
IV. Custom silicone rubber products
Custom silicone rubber products offer several benefits over standard products, including the ability to create unique designs, sizes, and textures that meet specific requirements. These products can be used in a wide range of industries, including automotive, medical, and consumer goods.
One important aspect of custom silicone rubber products is quality control. Ensuring that each product meets strict quality standards is crucial to maintaining the integrity of the final product and ensuring that it performs as intended. This involves monitoring the entire manufacturing process, from raw material selection to final product inspection.
In addition to quality control, technical support, and engineering solutions are also important for custom silicone rubber projects. These services can help customers with product design, tooling design, and material selection. With the help of an experienced engineering team, customers can ensure that their custom projects are completed on time, within budget, and to the highest quality standards.
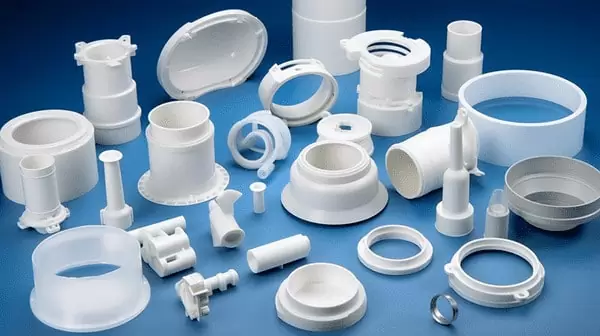
Overall, custom silicone rubber products offer several advantages over standard products, including greater design flexibility and the ability to meet specific project requirements. To ensure the success of these projects, it is important to work with a manufacturer that has a proven track record of quality, technical support, and engineering expertise.
V. Advantages of compression molding
Compression molding offers several distinct advantages over other molding methods, including significant cost savings and the potential for mass production. Due to lower tooling costs and shorter lead times, compression molding may often be more cost-effective for low to medium-volume production runs.
Compression molding’s other advantage lies in the high-temperature resistance and flame retardancy properties of silicone rubber products, making them perfect for use in applications requiring high heat resistance such as automobile and aerospace industries, and also applications requiring flame retardancy like electrical components.
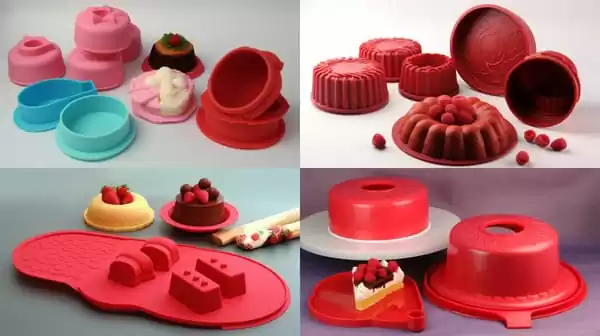
Compression molding allows for the creation of complex silicone rubber products with complex shapes and textures due to its ability to control material flow during the compression stage of the process, giving greater design freedom and customization options.
Overall, compression molding offers several distinct advantages over other molding methods, including cost savings, high-temperature resistance, flame retardancy, and design flexibility. As such, this technique has become popular for applications across various fields including automotive, aerospace, medical, and consumer goods manufacturing.
VI. Applications of custom silicone rubber products
Custom silicone rubber products have many uses in numerous industries, from medical devices and seals to O-rings and rubber sheets. Medical applications of custom silicone rubber products often involve surgical implants, catheters, and other medical devices due to their biocompatibility as well as resistance against heat, chemicals, and high temperatures.
silicone rubber molding products have long been utilized within the automotive industry to provide gaskets, seals, and other components with their high-temperature resistance and durability. Furthermore, they’re widely utilized within aerospace for applications that require flame retardancy as well as extreme temperature resistance.
Custom silicone rubber products can also be utilized for custom packaging and screen printing applications, including protecting delicate electronic devices during transport; branding/product identification purposes can also be accomplished with silicone rubber product printing. For instance, custom screen-printed sleeves can protect delicate devices during shipping while custom screen-printed stickers provide visual identification purposes for branding/product identification purposes.
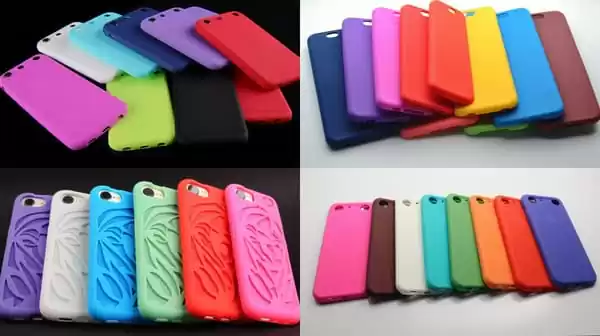
silicone rubber products have long been an appealing solution for diverse industries and applications, such as medical devices, automotive components, or custom packaging. Their flexibility has made them popular choices across various fields. Custom silicone rubber products can even be tailored specifically to each industry or application’s specific needs.
Conclusion
Custom silicone rubber colors and textures in compression molding offer numerous advantages over standard products. By accommodating specific design specifications and meeting individual customer requirements, custom silicone product can be utilized across a wide array of industries and applications.
Custom silicone products provide numerous advantages, including cost savings, temperature resistance, flame retardancy, and design flexibility. Quality control, technical support, and engineering solutions are also crucial elements to the success of custom silicone rubber projects.
To achieve optimal results, it’s vital to collaborate with an experienced custom silicone rubber manufacturing team. They will be able to offer quality products, engineering support, and technical solutions tailored specifically for each project – working with trusted manufacturers ensures their projects will be completed on time, within budget, and to the highest quality standards.