Introduction
Silicone rubber is a versatile material that finds applications in various industries due to its unique properties. Understanding the properties of silicone rubber is crucial for utilizing its full potential in different applications. In this article, we will delve into the key properties of silicone rubber and explore its significance in different fields.
Silicone rubber is a type of elastomer, characterized by a silicon-oxygen (Si-O) bond in its molecular structure. This distinctive composition imparts exceptional properties to silicone rubber, making it an invaluable material in numerous industries. By comprehending its properties, we can harness its capabilities for diverse applications ranging from medical devices to electrical insulation.
The importance of understanding the properties of silicone rubber cannot be overstated. By knowing its characteristics, engineers and designers can make informed decisions regarding material selection, manufacturing processes, and performance optimization. Whether it’s in the medical industry, electronics, or automotive sector, a thorough understanding of silicone rubber properties is essential for creating efficient and reliable products.
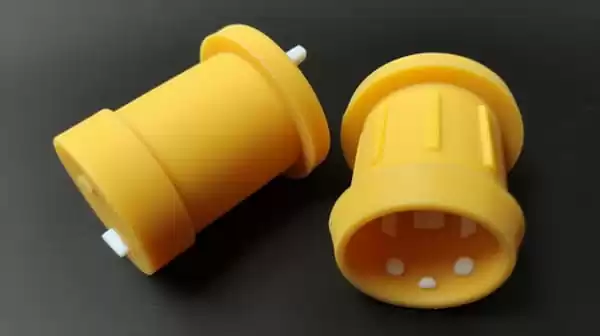
In the following sections, we will explore the physical, mechanical, electrical, and chemical properties of silicone rubber, shedding light on its capabilities and applications. By gaining insights into the properties of this highly versatile material, we can unlock its potential in various industries and drive innovation forward.
II. Properties of Silicone Rubbers
A. Physical Properties
1.Molecular structure and composition: Silicone rubber is composed of silicon atoms bonded to oxygen atoms, forming a repeating silicon-oxygen (Si-O) backbone. This unique molecular structure gives silicone rubber its distinctive properties.
2.Solid and liquid forms: Silicone rubber is available in both solid and liquid forms. Solid silicone rubber (SSR) is commonly used for molding and extrusion applications, while liquid silicone rubber (LSR) is used for injection molding processes.
3.Wide temperature range: Silicone rubber exhibits excellent thermal stability and can withstand a wide temperature range, from extreme cold to high heat. It remains flexible and retains its properties across a broad spectrum of temperatures.
4.Chemical stability: Silicone rubber displays remarkable chemical stability, making it resistant to many chemicals and solvents. It maintains its integrity and properties when exposed to various substances, contributing to its durability and longevity.
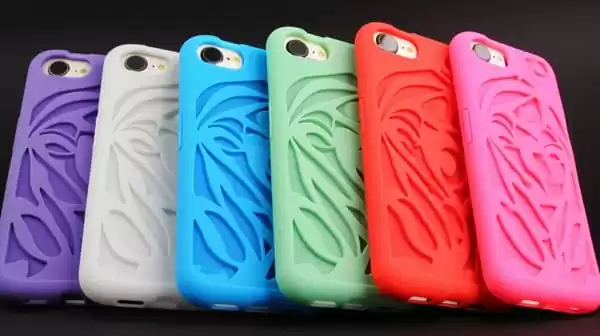
5.UV resistance: Silicone rubber possesses inherent UV resistance, which allows it to maintain its physical and mechanical properties when exposed to ultraviolet rays from the sun. This makes it suitable for outdoor applications where UV exposure is a concern.
B. Mechanical Properties
1.Strength and tear resistance: Silicone rubber exhibits excellent strength and tear resistance, allowing it to withstand mechanical stress and deformation without losing its structural integrity. It can endure stretching, compression, and repetitive movements without tearing or breaking.
2.Flexibility and elasticity: Silicone rubber is highly flexible and elastic, enabling it to recover its original shape after being stretched or compressed. This elasticity makes it suitable for applications that require repeated movement or deformation.
3.Long polymer chains and high molecular weight: Silicone rubber has relatively long polymer chains and a high molecular weight, contributing to its overall mechanical strength and durability. These characteristics enhance its resistance to wear, tear, and fatigue.
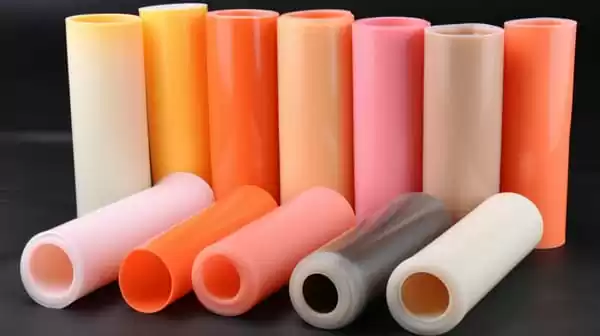
4.Reinforcing fillers: Silicone rubber can be reinforced with fillers like silica or carbon black to further enhance its mechanical properties. These fillers improve tensile strength, tear resistance, and dimensional stability, allowing silicone rubber to meet specific application requirements.
C. Electrical Properties
1.Electrical insulation: One of the notable properties of silicone rubber is its excellent electrical insulation. It acts as a reliable insulating material, effectively preventing the flow of electric current. This property makes it valuable in electrical and electronic applications where insulation is crucial for safety and performance.
2.Heat resistance and thermal conductivity: Silicone rubber exhibits remarkable heat resistance, allowing it to withstand high temperatures without significant degradation. It can maintain its electrical properties and mechanical integrity even in demanding thermal environments. Additionally, silicone rubber has relatively high thermal conductivity, facilitating heat dissipation in certain applications.
3.Voltage line insulators: Silicone rubber’s electrical insulation properties make it suitable for applications requiring voltage line insulators. It can effectively isolate electrical conductors, preventing leakage or short circuits and ensuring safe operation in various electrical systems.
4.Electrically conductive options: While silicone rubber is primarily known for its electrical insulation properties, there are electrically conductive variations available as well. Conductive silicone rubber formulations containing conductive fillers can be used in applications that require electrical conductivity, such as EMI/RFI shielding or static dissipation.
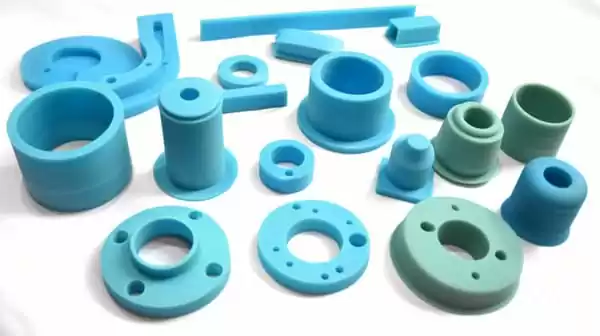
D. Chemical Properties
1.Resistance to most chemicals: Silicone rubber exhibits excellent resistance to a wide range of chemicals, including acids, bases, solvents, and oils. This chemical stability ensures that silicone rubber maintains its properties and performance even when exposed to harsh environments or corrosive substances.
2.Compatibility with organic rubbers: Silicone rubber demonstrates good compatibility with various organic rubbers, allowing for effective bonding or integration with other rubber materials. This compatibility enables the creation of composite structures with enhanced properties or the combination of different rubber materials in specific applications.
3.Flame retardancy: Silicone rubber is inherently flame retardant, meaning it has a low flammability and resists the spread of flames. It does not easily ignite and, when exposed to fire, tends to self-extinguish, making it suitable for applications where fire safety is a concern.
Understanding the electrical and chemical properties of silicone rubber is crucial for selecting the appropriate material for applications that require electrical insulation, heat resistance, chemical compatibility, or flame retardancy. In the following sections, we will explore the various types of silicone rubber and delve into its applications across different industries.
III. Types of Silicone Rubber
A. Solid Silicone Rubber (SSR):
Solid silicone rubber (SSR) is a widely used form of silicone rubber. It is a solid material that offers excellent flexibility, high tear strength, and resistance to extreme temperatures. SSR is commonly used in applications such as gaskets, seals, O-rings, and automotive components. It can be molded or extruded into various shapes to meet specific design requirements.
B. Liquid Silicone Rubber (LSR):
Liquid silicone rubber (LSR) is a two-part system consisting of a liquid base material and a catalyst. LSR is known for its exceptional flow properties, allowing it to fill intricate molds and create complex shapes with precision. It is commonly used in injection molding processes to produce items like medical devices, consumer electronics, and automotive parts. LSR offers advantages such as high purity, excellent transparency, and ease of processing.
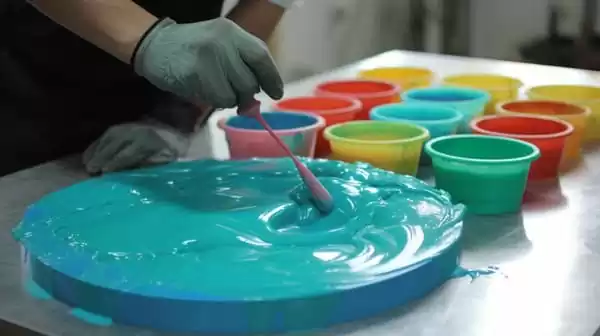
C. Room Temperature Vulcanized (RTV) Silicone:
Room Temperature Vulcanized (RTV) silicone is a type of silicone rubber that cures at room temperature without requiring high heat. It is often available in the form of a two-component system, where a base compound is mixed with a curing agent. RTV silicone is popular for its ease of use and ability to create flexible molds, sealants, and adhesives. It finds applications in areas such as arts and crafts, mold making, and construction.
D. Fluorosilicone Rubber (FSR):
Fluorosilicone rubber (FSR) is a specialized type of silicone rubber that incorporates fluorine atoms into its structure. This modification enhances the material’s resistance to fuel, oil, solvents, and other chemicals. FSR offers excellent performance in harsh environments and is commonly used in aerospace, automotive, and military applications where resistance to fluids and extreme temperatures is critical.
Understanding the different types of organic rubber enables manufacturers and designers to choose the most suitable form for their specific application requirements. Whether it’s solid silicone rubber (SSR) for durable seals, liquid silicone rubber (LSR) for intricate molded parts, room temperature vulcanized (RTV) silicone for versatile applications, or fluorosilicone rubber (FSR) for chemical resistance, each type has its unique advantages and applications.
IV. Applications of Silicone Rubbers
A. Medical Industry
Silicone rubber has long been utilized by medical device and equipment manufacturers because of its biocompatibility, flexibility, and sterilizability properties. Silicone is utilized in producing medical implants such as catheters, pacemaker leads, prosthetics as well as for applications which involve long-term skin contact such as pacemaker leads.
Respiratory Masks and Tubing: Silicone rubber is an ideal material for crafting respiratory masks and tubing due to its soft yet flexible nature, offering comfortable fits with secure seals that protect effectively. Furthermore, its chemical stability and easy of cleaning make silicone rubber suitable for medical-grade respiratory equipment.
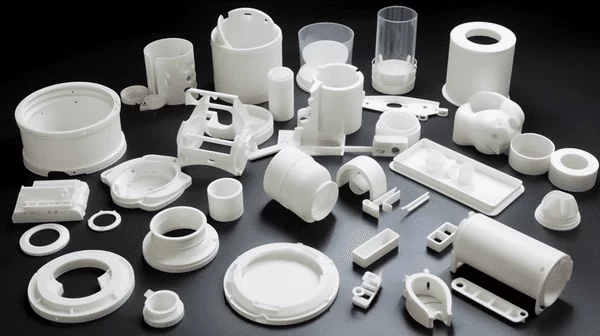
Sealing Applications: Silicone rubber’s outstanding sealing properties combined with its resistance to extreme temperatures and chemicals makes it an ideal material for sealing applications in medical fields, such as containers, valves and connectors used to ensure integrity and prevent contamination in devices and equipment.
B. Electrical and Electronics Systems
Electric motors and insulation: Silicone rubber has long been utilized as an insulation material in electric motors due to its superior dielectric strength and thermal resistance, helping prevent the transfer of electrical current between components while providing efficient and safe motor operation.
Voltage Line Insulators: Silicone rubber’s electrical insulation properties make it an excellent material to create voltage line insulators, offering safety and reliability to power distribution and transmission systems. By isolating and insulating electrical conductors effectively, silicone rubber ensures safe operations of voltage transmission lines.
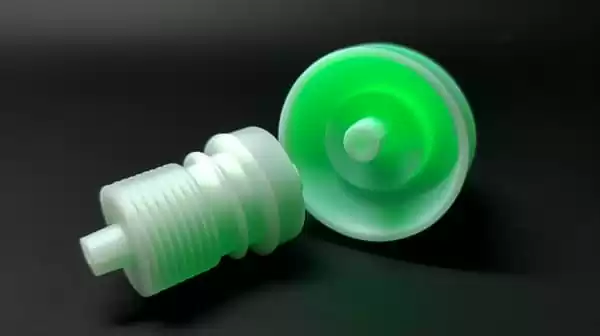
Silicone rubber’s heat resistance and thermal conductivity properties make it an excellent solution for thermal management applications, including heat sinks, thermal pads and the encapsulation of electronic components to efficiently dissipate heat while achieving ideal operating temperatures.
C. Industrial and Automotive applications
Silicone rubber’s resilience, flexibility and resistance to extreme temperatures make it an excellent material choice for gaskets and seals in industrial and automotive settings. Silicone seals prevent leakage of fluids, gases and contaminants, providing reliable sealing solutions with long-term reliability and durability.
O-rings and Connectors: O-rings made of silicone rubber are widely utilized across industries, from automotive to manufacturing, for their sealing capabilities in both dynamic and static applications such as hydraulic systems, fuel systems and connectors.
Silicone Rubber Components for Automobiles: Silicone rubber has become increasingly important in automotive components due to its resistance to high temperatures and compatibility with fluids used for fluid management systems, including gaskets, seals, hoses, spark plug boots and other vital engine and exhaust system parts.
Silicone rubber’s versatile properties make it an excellent material for use across numerous fields and applications, from the medical industry for devices and seals, electrical and electronics, and thermal management, industrial/automotive applications requiring gaskets/components or seals/gaskets – to providing reliable performance with long-term durability.
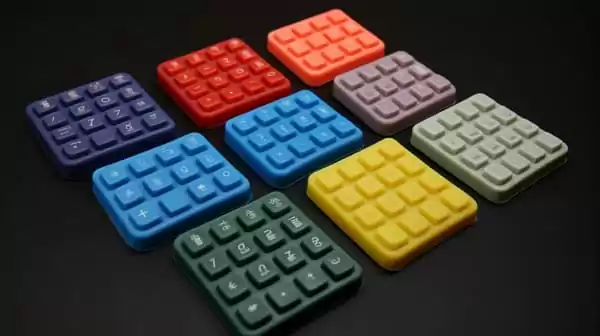
Conclusion
Silicone rubber is a highly versatile material with a wide range of properties that make it indispensable in various industries. Throughout this article, we have explored the physical, mechanical, electrical, and chemical properties of silicone rubber, highlighting its exceptional characteristics.
Silicone rubber’s molecular structure and composition, availability in solid and liquid forms, wide temperature range, chemical stability, and UV resistance contribute to its unique properties. Its strength, tear resistance, flexibility, and long polymer chains make it a durable and resilient material. Additionally, its electrical insulation, heat resistance, and compatibility with organic rubbers further enhance its usability.
The importance of understanding the properties of silicone rubber cannot be overstated. Engineers, designers, and manufacturers can leverage this knowledge to select the appropriate form of silicone rubber for specific applications. Whether it’s solid silicone rubber (SSR) for gaskets and seals, liquid silicone rubber (LSR) for precise molding, or room temperature vulcanized (RTV) silicone for versatile applications, silicone rubber offers a highly reliable and safe material solution.
Silicone rubber finds extensive applications across various industries. In the medical field, it is crucial for medical devices, respiratory masks, and sealing applications, ensuring patient safety and comfort. In the electrical and electronics industry, silicone rubber is used for electric motors, insulation, voltage line insulators, and thermal management solutions, enabling efficient and reliable performance. In the industrial and automotive sectors, silicone rubber is essential for gaskets, seals, O-rings, and automotive components, providing durability and functionality in demanding environments.
Looking towards the future, advancements and developments in silicone rubber technology are anticipated. Researchers and manufacturers continue to explore new formulations, processing methods, and applications to further expand the capabilities of silicone rubber. These advancements may include improved electrical conductivity, enhanced resistance to extreme temperatures, and the development of new silicone rubber products to meet evolving industry needs.
In conclusion, silicone rubber stands as a highly versatile and reliable material with a broad range of properties. Its importance in various industries cannot be overstated, as it plays a vital role in enabling innovative solutions, ensuring safety, and enhancing performance. With ongoing advancements, silicone rubber will continue to shape the future of industries and drive progress in diverse applications.