Introduction
Silicone rubber products have gained immense popularity across industries due to their exceptional characteristics. Silicone rubber’s versatile properties, durability, heat, and chemical resistance make it an ideal material for many different applications. When manufacturing these products, advanced techniques like over molding and insert molding play a pivotal role, enabling innovative designs with multiple materials integrated for high-quality and functional silicone rubber products.
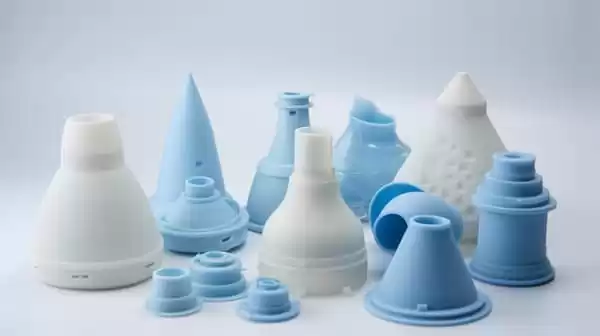
In this article, we will delve into the world of over molding and insert molding technologies used in silicone rubber product manufacturing. We’ll investigate their processes, benefits, applications, and significance within the industry – so by the time you reach the end, you will gain a complete picture of how over molding and insert molding contribute to creating superior silicone molding products.
II. Understanding Overmolding
Overmolding is an advanced manufacturing process that involves the encapsulation of an existing substrate or component with liquid silicone rubber (LSR). Let’s break down the overmolding process step by step:
A. Explanation of the Overmolding Process
1.Preparation of Substrate and Mold Cavity:
The substrate, which can be made of materials such as plastic, metal, or even another silicone rubber component, undergoes thorough preparation. This includes cleaning and, in some cases, priming the surface to ensure proper bonding with the LSR.
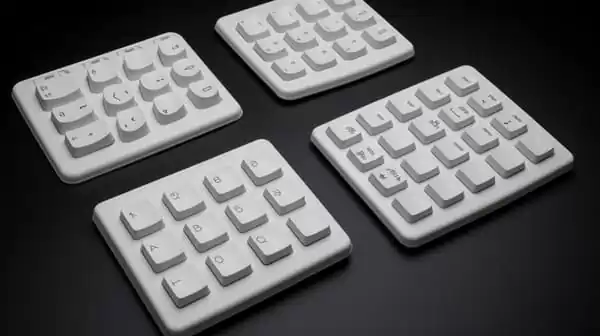
2.Insert Placement and Positioning:
The prepared substrate is placed into the mold cavity, ensuring precise alignment and positioning. This step is crucial to achieving the desired fit and functionality of the overmolded part.
3.Two shot molding or Transfer of Liquid Silicone Rubber (LSR):
Next, the LSR, in its liquid state, is injected or transferred into the mold cavity. The LSR flows around the substrate, covering it completely and taking the shape of the mold.
4.Curing and Bonding of LSR with the Substrate:
Once the LSR is injected, it undergoes a curing process. Curing can be achieved through heat, UV light, or other curing methods, depending on the specific LSR formulation. During this stage, the LSR solidifies and bonds with the substrate, creating a strong mechanical and chemical bond.
5.Ejection of the Overmolded Parts:
After the LSR has fully cured, the mold is opened, and the overmolded part is ejected. The part now consists of the substrate and the overmolded silicone rubber, forming a single integrated components.
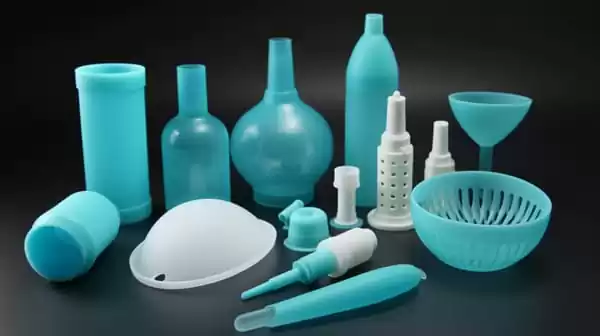
B. Benefits and Advantages of Overmolding
Overmolding offers several benefits, which contribute to its widespread use in various industries:
1.Enhanced Grip and Aesthetics: The addition of silicone rubber in the overmolding process provides a soft and tactile surface, offering enhanced grip and a comfortable user experience. Moreover, overmolding allows for the incorporation of different colors and textures, improving the aesthetics of the final product.
2.Improved Durability and Functionality: The overmolding process creates a robust bond between the substrate and the silicone rubber, enhancing the durability and functionality of the component. The silicone rubber layer provides protection against impact, moisture, and other environmental factors, increasing the lifespan of the product.
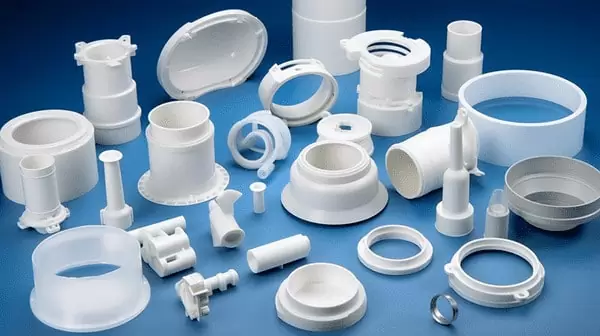
C. Application Examples of Overmolding in Different Industries
Overmolding finds wide-ranging applications across various industries, including:
Automotive: Overmolding is used to create soft-touch surfaces on steering wheels, gear shift knobs, and instrument panels, enhancing both comfort and control.
Electronics: Overmolding is employed in the production of electronic connectors, handheld devices, and remote controls to improve ergonomics and provide better grip and durability.
Consumer Goods: Overmolding is utilized in products like toothbrush handles, kitchen utensils, and tool grips to enhance user comfort, aesthetics, and overall product quality.
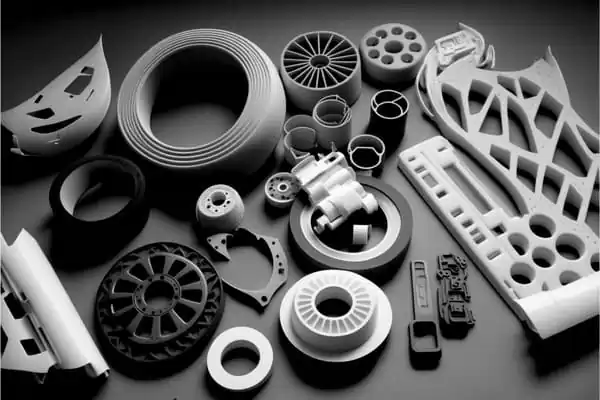
By understanding the overmolding process and its benefits, we can appreciate how it transforms silicone rubber products into highly functional and visually appealing components used in various industries.
III. Unveiling Insert Molding processes
Insert molding is another advanced injection molding process manufacturing technique used in silicone rubber product manufacturing. Let’s explore the insert molding process step by step:
A. Description of the Insert Molding Process
Placement of Preformed Inserts in the Mold: In the insert molding process, preformed inserts made of materials such as metal, plastic, or even silicone rubber itself, are strategically placed into the mold. The metal inserts are positioned to achieve the desired functionality and structural support in the final injection molded parts.
Injection or Transfer of Liquid Silicone Rubber (LSR) around the Inserts: Once the inserts are properly positioned, liquid silicone rubber (LSR) is injected or transferred into the mold cavity. The LSR flows around the inserts, completely encapsulating them and taking the shape of the mold.
Curing and Bonding of LSR with the Inserts: After the LSR is injected, it undergoes a curing process. The curing method may involve heat, UV light, or other suitable methods depending on the LSR formulation. During curing, the LSR solidifies and forms a strong bond with the inserts, creating a mechanically and chemically integrated part.
Ejection of the Insert-Molded Part: Once the LSR has fully cured and the part has reached the desired specifications, the mold is opened, and the insert-molded part is ejected. The part now consists of the inserts and the surrounding silicone rubber, forming a single component with enhanced functionality.
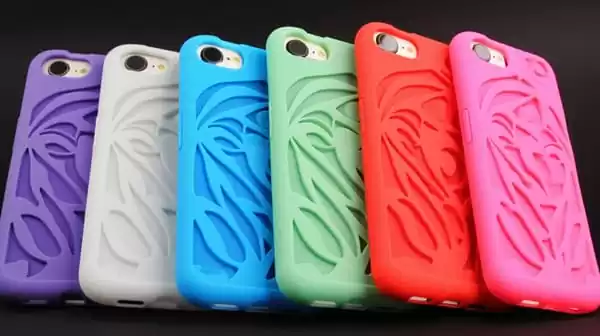
B. Advantages and Applications of Insert Molding
Insert molding offers several advantages that make it a preferred technique in silicone rubber product manufacturing:
Increased Strength and Added Functionality: By incorporating inserts into the molding process, insert molding significantly enhances the strength and functionality of the final component. Inserts made of metal or other rigid materials provide structural support, reinforcement, or specific features to the silicone rubber product.
Simplified Assembly Processes: Insert molding reduces the need for additional assembly steps. Instead of separately assembling multiple components, insert molding allows for the integration of different materials in a single molding process, streamlining production and reducing assembly time and costs.
C. Examples of Insert Molding in Various Industries
Insert molding finds diverse applications across multiple industries, including:
Healthcare: Insert molding is utilized in medical device manufacturing, where silicone rubber is combined with metal or plastic inserts to create components such as catheters, syringe plunger tips, and hearing aid shells.
Electronics: Insert molding is commonly used in the production of connectors, switches, and keypads, where metal or plastic inserts are integrated into silicone rubber to achieve optimal functionality and durability.
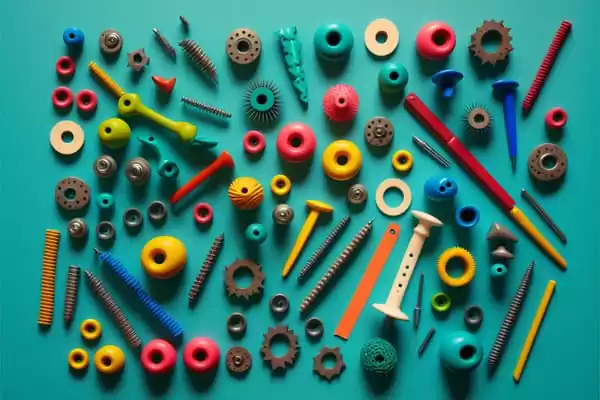
Automotive: Insert molding is employed in automotive parts manufacturing, such as sensor housings, electrical connectors, and interior components, to enhance strength, improve electrical insulation, and reduce assembly steps.
These examples highlight the versatility and value of insert molding in various industries, enabling the creation of high-performance silicone rubber products.
IV. Overmolding and Insert Molding: A Closer Look
Overmolding and insert molding are two distinct techniques used in silicone rubber product manufacturing. Let’s examine them more closely:
A. Clarification of the Differences between Overmolding and Insert Molding
Overmolding:
Overmolding involves encapsulating an existing substrate or plastic parts with liquid silicone rubber (LSR).
The substrate material can be made of materials such as plastic, metal,thermoplastic polyurethane or even another silicone rubber component.
The LSR is injected or transferred into the mold cavity, covering the substrate completely.
The curing process bonds the LSR with the substrate, resulting in a single integrated part.
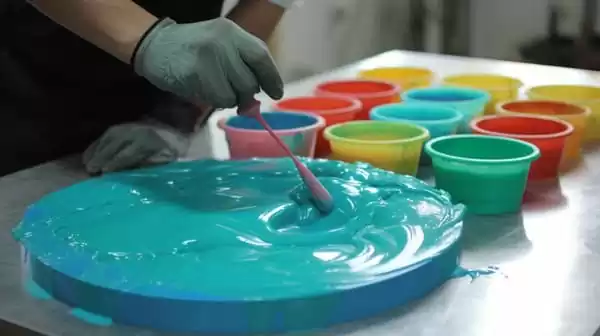
Insert Molding:
Insert molding involves placing preformed inserts, made of materials like metal or plastic, into the mold cavity.
The LSR is then injected or transferred around the inserts, encasing them completely.
During the curing process, the LSR forms a strong bond with the inserts, creating a mechanically integrated part.
The key distinction between the two techniques lies in the starting point: overmolding uses a substrate or component, while insert molding incorporates preformed inserts.
B. Key Considerations in Material Selection for Overmolding and Insert Molding
Choosing the appropriate materials is crucial for successful overmolding and insert molding processes. Some key considerations include: insert molded parts
Substrate or Insert Material Compatibility: The compatibility between the substrate or inserts and the liquid silicone rubber (LSR) must be ensured to achieve optimal bonding and performance. Factors such as thermal expansion, chemical resistance, and mechanical properties need to be taken into account.
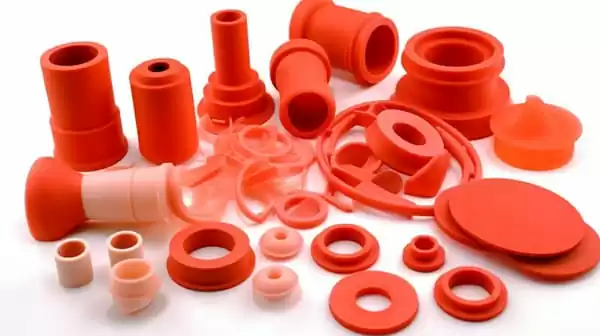
Overmold or Insert Material Properties: The properties of the overmold or insert material should align with the desired functionalities of the final component. Considerations include factors like hardness, flexibility, electrical conductivity, and cosmetic appearance.
Adhesion and Bonding: The adhesion and bonding characteristics between the substrate or inserts and the LSR are critical for the overall strength and integrity of the molded part. Surface treatments or primers may be necessary to promote adhesion and improve bonding.
C. Comparison of the Benefits and Applications of Each Technique
Overmolding:
Benefits:
Enhanced grip and aesthetics
Improved durability and functionality
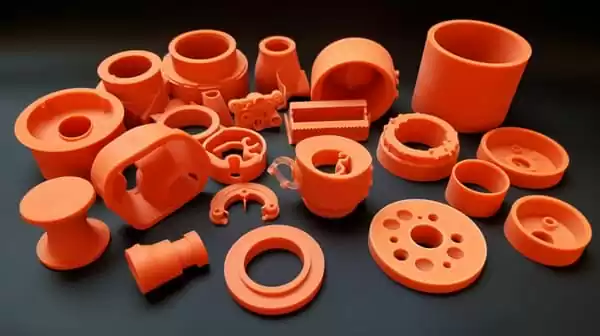
Applications:
Automotive: Soft-touch surfaces, grips, and buttons
Electronics: Sealing, protection, and ergonomic enhancements
Consumer Goods: Handles, grips, and housings
Insert Molding:
Benefits:
Increased strength and added functionality
Simplified assembly processes
Applications:
Healthcare: Medical devices, catheters, and hearing aids
Electronics: Connectors, switches, and keypads
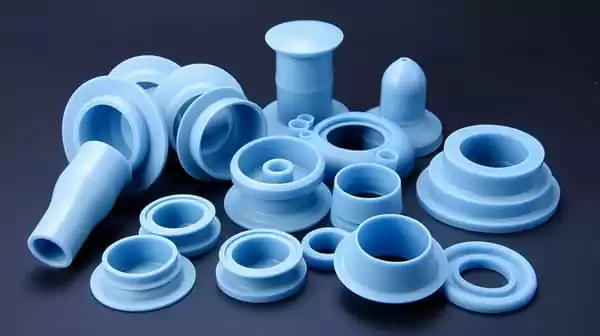
Automotive: Sensor housings, electrical connectors, and interior components
By understanding the differences between overmolding and insert molding, considering material selection, and recognizing their respective benefits and applications, manufacturers can make informed decisions to meet specific product requirements effectively.
V. Practical Examples and Use Cases
In this section, we will explore specific products that utilize overmolding and insert molding techniques in silicone rubber product manufacturing. We will highlight the benefits and advantages achieved through these techniques and discuss their impact on product performance and customer satisfaction.
A. Showcase Specific Products that Utilize Overmolding or Insert Molding
Silicone Rubber Toothbrush Handle: A toothbrush handle is an excellent example of a product that utilizes overmolding. The plastic or metal core provides structural support, while the overmolded silicone rubber layer offers a comfortable grip and enhanced aesthetics. The overmolding process ensures a strong bond between the core and the silicone rubber, resulting in a toothbrush handle that combines functionality and visual appeal.
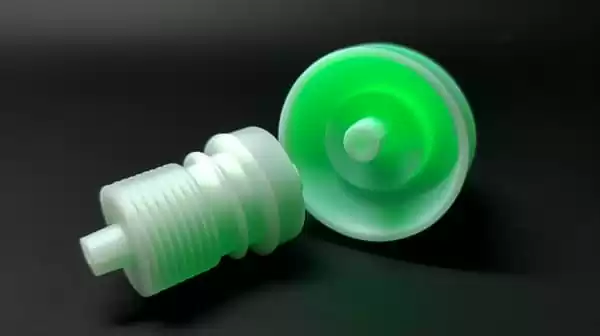
Medical Catheter: In the healthcare industry, insert molding is often employed to create medical catheters. The silicone rubber material is molded around a metal or plastic tube, providing flexibility, biocompatibility, and enhanced functionality. Insert molding allows for the integration of multiple materials, simplifying the assembly process and ensuring a secure bond between the silicone rubber and the insert.
Electronic Connector: Electronic connectors frequently utilize overmolding to enhance functionality and durability. The plastic or metal connector pins are encapsulated with silicone rubber, offering excellent electrical insulation, moisture resistance, and improved grip. Overmolding ensures a seamless and secure bond between the connector pins and the silicone rubber, resulting in a reliable and long-lasting electronic component.
B. Highlight the Benefits and Advantages Achieved through These Techniques
The utilization of overmolding and insert molding techniques in silicone rubber product manufacturing brings forth numerous benefits:
Enhanced Functionality:
Overmolding and insert molding allow for the integration of different materials, providing added functionality and improved performance to the final product.
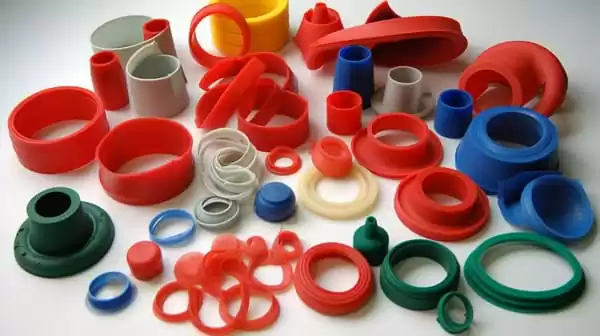
Improved Aesthetics:
These techniques offer the ability to create visually appealing products with smooth and seamless surfaces, enhancing the overall aesthetics and market appeal.
Durability and Reliability:
Overmolding and insert molding result in a strong mechanical bond between materials, increasing the durability and reliability of the molded parts.
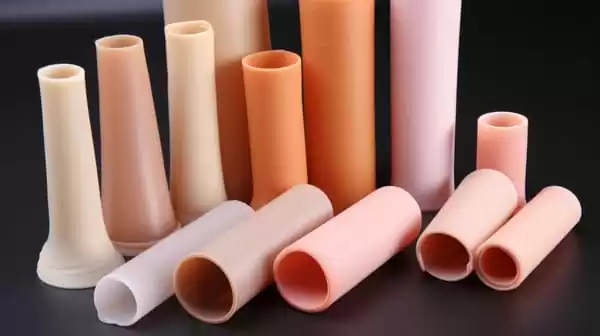
Simplified Assembly:
These techniques streamline the assembly process by combining multiple components into a single molding process, reducing manufacturing time and costs.
C. Discuss the Impact on Product Performance and Customer Satisfaction
The application of overmolding and insert molding has a significant impact on product performance and customer satisfaction. The enhanced functionality, improved aesthetics, and durability achieved through these techniques contribute to high-quality products that meet the evolving needs of consumers. By providing products with better grip, ergonomic design, and reliable performance, overmolding and insert molding techniques enhance customer satisfaction and elevate the overall user experience.
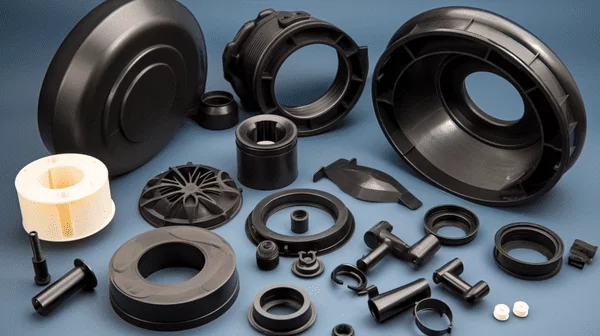
Conclusion
Overmolding and insert molding techniques play a vital role in silicone rubber product manufacturing, providing numerous advantages while broadening their appeal. By integrating multiple materials, overmolding and insert molding can produce components with enhanced functionality, aesthetics and durability that meet customer requirements.
Overmolding and insert molding cannot be understated in terms of importance to manufacturers. By employing these processes, they are able to produce silicone rubber products with outstanding performance, aesthetics, and functionality. By combining various materials through overmolding or insert molding techniques, manufacturers have more opportunities for designing innovative products.
Looking towards the future, overmolding and insert molding techniques should continue their rapid advancement through research and development efforts. We anticipate further enhancements to materials, processes and tooling which will open up opportunities to create even more sophisticated silicone rubber products with quality.
As technology progresses, overmolding and insert molding in silicone rubber product manufacturing will become ever more versatile and widely applied – becoming essential methods of meeting consumer demands across various industries.
Overmolding and insert molding are critical technologies for producing superior silicone rubber products, helping manufacturers create functional yet aesthetically appealing components to drive customer satisfaction and innovation. Their future potential holds great promise as these techniques continue to shape the landscape of silicone rubber product manufacturing.