Introduction
Silicone rubber compression and injection molding process is a versatile and widely used manufacturing process that holds immense significance across various industries. This method involves shaping silicone rubber into intricate forms and precise dimensions, making it a go-to choice for creating a diverse range of products. From automotive components to medical devices and consumer goods, the advantages of silicone rubber compression molding extend far and wide, shaping the modern landscape of manufacturing. Let’s delve deeper into the definition of this process and explore why it’s a pivotal player in the industrial realm.
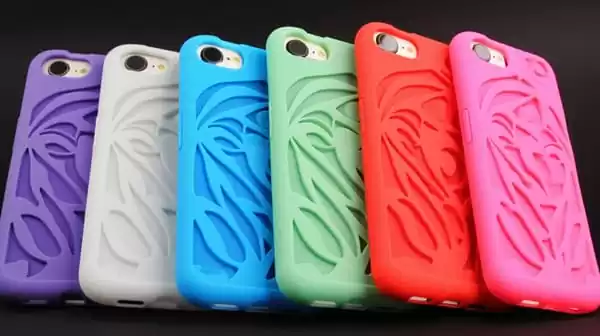
High-Quality Surface Finish
Importance of Surface Finish in Products
The surface finish of a product holds immense importance, influencing both its visual appeal and tactile experience. A flawless surface not only enhances the product’s aesthetics but also contributes to its functionality and durability. In industries where precision matters, such as electronics and medical devices, a high-quality surface finish is non-negotiable. It’s the first impression a user gets, and it can impact the overall perception of the product’s quality.
Achieving Excellent Surface Quality with Silicone Compression Molding
Silicone rubber compression molding excels in achieving exceptional surface quality, making it an ideal choice for products that demand visual and tactile finesse. The process involves meticulous attention to detail and a combination of factors that contribute to the superior surface finish:
- Mold Design: The mold used in silicone compression molding is designed with precision to ensure that the final product retains intricate details and dimensions. This level of accuracy plays a significant role in achieving a high-quality surface.
- Material Properties: Silicone rubber itself possesses inherent properties that lend well to achieving a smooth and consistent surface. Its ability to flow evenly within the mold cavity helps eliminate imperfections and irregularities.
- Pressure Control: The application of pressure during the molding process ensures that the silicone rubber material conforms precisely to the mold’s contours. This eliminates any voids or inconsistencies that could affect the surface finish.
- Temperature Management: Proper temperature control is critical in achieving a smooth surface. The curing process is carefully managed to prevent variations that might lead to surface defects.
- Mold Release Agents: Using appropriate mold release agents can prevent the material from sticking to the mold’s surface, further enhancing the quality of the finish.
In essence, silicone compression molding takes full advantage of these factors to create products with surfaces that are not only visually appealing but also free from imperfections. This meticulous attention to detail and commitment to achieving excellence in surface quality are what set silicone rubber compression molding apart in industries where precision and aesthetics are paramount.
Consistency and Precision
Role of Mold Design and Pressure Control in Achieving Consistent Dimensions
Consistency in product dimensions is a hallmark of excellence in manufacturing, and silicone rubber compression molding achieves this by leveraging meticulous mold design and precise pressure control. Here’s how these factors work in tandem:
1. Mold Design: The mold used in silicone rubber compression molding is a meticulously crafted masterpiece. It’s designed to mirror the intricate details and dimensions of the desired product. Every contour and feature is meticulously translated into the mold, ensuring that each product emerges with uniformity and accuracy.
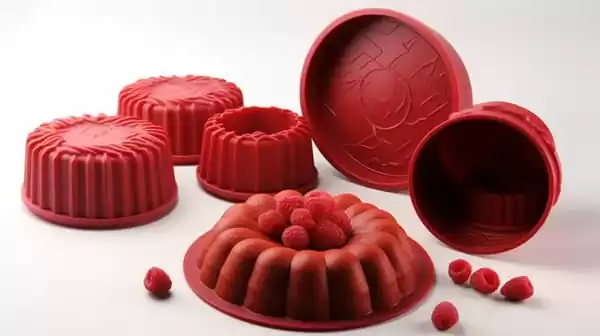
2. Pressure Control: Pressure is a guiding force in silicone compression molding process. When pressure is applied, the raw silicone material flows and fills the mold cavity according to the mold design. This controlled flow ensures that the material reaches every nook and cranny of the mold, leaving no room for variations in dimensions.
Importance of Precision in Products with Tight Tolerances
Precision isn’t just a quality; it’s a necessity in industries that demand products to perform with exactitude. Consider medical devices where a millimeter’s deviation can have critical consequences, or aerospace components that must fit together seamlessly. In such applications, tight tolerances are the norm, and silicone rubber compression molding rises to the challenge:
- Accurate Assembly: Parts produced with consistent dimensions and tight tolerances ensure they fit together perfectly during assembly. This eliminates the need for extra adjustments or modifications, streamlining the manufacturing process.
- Reliability: Precisely dimensioned components are inherently more reliable. They perform as intended without unexpected variations that could compromise their functionality or performance.
- Quality Assurance: Industries that require tight tolerances often adhere to strict quality standards. Silicone rubber compression molding’s ability to consistently meet these tolerances is a testament to its reliability and accuracy.
- Cost Efficiency: The precision achieved through silicone rubber compression molding translates to less waste, fewer rejects, and reduced need for post-processing adjustments. This, in turn, leads to cost savings over the product’s lifecycle.
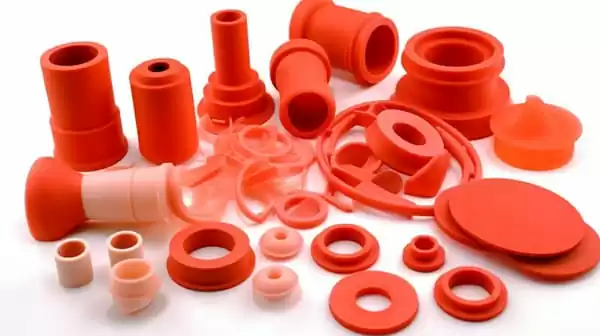
In a manufacturing landscape where precision is non-negotiable, silicone rubber compression molding stands as a reliable solution. Its ability to consistently replicate dimensions down to the minutest detail, and its dedication to precision in products with tight tolerances, make it an invaluable asset in industries where accuracy is a prerequisite for success.
Material Options and Properties
Different Silicone Rubber Formulations
Silicone rubber compression molding presents a world of possibilities through its diverse range of material formulations. These formulations, each tailored to specific applications, offer manufacturers the ability to fine-tune their products to meet exact requirements. Here’s a glimpse into some of the silicone rubber formulations available:
1. Liquid Silicone Rubber (LSR): LSR is a versatile option known for its ability to replicate intricate details. It’s often used in applications requiring precision and consistency, such as medical devices and electronics. LSR’s liquid form ensures it can fill even the most complex mold cavities, resulting in products with high accuracy.
2. Precipitated Silicone Rubber: This formulation boasts impressive tensile strength and elongation properties, making it suitable for products that require durability and flexibility. It’s often used in industries where products are subjected to frequent bending or stretching.
3. Fumed Silicone Rubber: Fumed silicone rubber offers excellent heat resistance and thermal stability, making it a preferred choice for applications involving exposure to high temperatures. Its ability to withstand extreme heat without losing its properties makes it ideal for to mold rubber parts, automotive components and industrial equipment.
Properties Offered by Different Formulations
1. Flexibility: Many silicone rubber formulations, including LSR and precipitated, silicone rubber products, offer exceptional flexibility. This property is crucial in applications where products need to bend, stretch, or endure repeated movements without compromising their integrity.
2. Heat Resistance: Fumed silicone rubber’s remarkable heat resistance enables it to function effectively even in high-temperature environments. It remains stable and maintains its properties when exposed to both extreme temperatures and heat, making it indispensable for products that operate under challenging conditions.
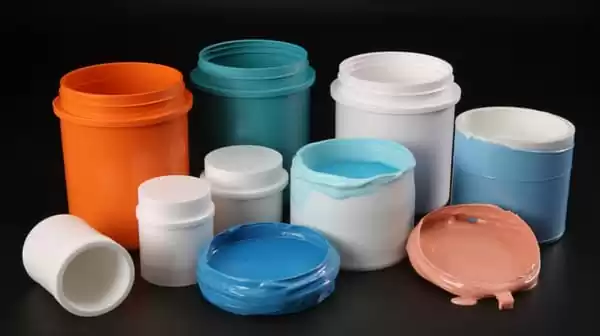
3. Electrical Insulation: Silicone rubber’s electrical insulation properties are valued in industries that require safe and reliable electrical components. Its high dielectric strength and resistance to electrical current make it an ideal material for insulating cables, connectors, and other electrical parts.
4. Biocompatibility: Certain silicone rubber formulations, particularly LSR, exhibit excellent biocompatibility. This property makes them suitable for medical devices that come into contact with the human body, as they minimize the risk of adverse reactions.
5. Weather Resistance: Silicone rubber’s resistance to weathering and UV light makes it a prime choice for outdoor applications. It can withstand exposure to harsh weather conditions, ensuring the longevity of products like outdoor signage and seals.
The ability to choose from these formulations and their associated properties empowers manufacturers to select the precise material that aligns with their application’s requirements. Silicone rubber compression molding isn’t just about creating products; it’s about tailoring them to perform optimally in their designated environments, showcasing the adaptability and customization potential of the process.
Elastomeric Properties for Functionality
Understanding the Elastomeric Nature of Silicone Rubber
Elastomeric materials possess a unique ability to stretch and return to their original shape, making them essential in applications requiring flexibility and resilience. Silicone rubber, a quintessential elastomeric material, stands out for its exceptional elastomeric properties. This characteristic allows it to deform under stress and then promptly regain its original form once the stress is removed. This inherent flexibility is at the heart of silicone rubber’s functionality in various industries.
Benefits of Elastomeric Properties: Sealing, Shock Absorption, and Vibration Isolation
1. Sealing Applications: Silicone rubber’s elastomeric nature is invaluable in sealing applications. Whether in industrial machinery, automotive engines, or household appliances, the material’s ability to conform tightly to irregular surfaces ensures effective seals that prevent leakage and contamination. This is especially crucial in environments where a secure and reliable seal can mean the difference between success and failure.
2. Shock Absorption: The elastomeric properties of silicone rubber make it an excellent shock-absorbing material. When subjected to impact or sudden force, it absorbs the energy, cushioning the blow and protecting delicate components. This is why silicone rubber is commonly found in products like phone cases, protective equipment, and even footwear, enhancing safety and user comfort.
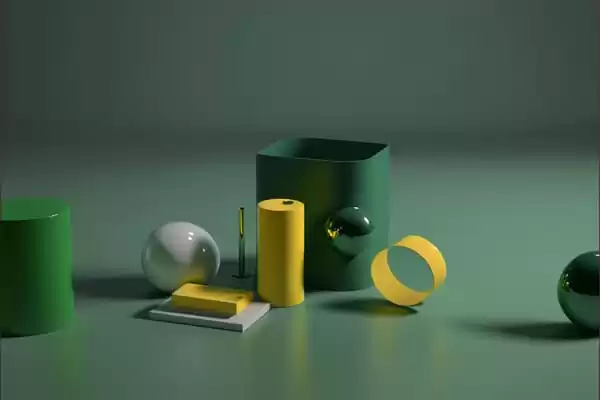
3. Vibration Isolation: In applications where vibration can cause damage or affect performance, silicone rubber’s elastomeric properties offer an effective solution. By absorbing and dampening vibrations, it prevents these disturbances from propagating to other parts of a system. This makes it invaluable in industries such as electronics, where sensitive components must be shielded from external vibrations that could compromise functionality.
The elastomeric properties of silicone rubber are the secret behind its adaptability and reliability in diverse applications. Whether it’s ensuring a tight seal, safeguarding against impact, or mitigating vibrations, silicone rubber’s ability to flex and rebound plays a pivotal role in enhancing the functionality and longevity of products across industries.
Low Waste and Environmental Benefits
How Silicone Rubber Compression Molding Generates Minimal Waste
Silicone rubber compression injection molding machine sets a remarkable precedent in minimizing waste during the manufacturing process. This eco-friendly aspect is achieved through meticulous control over materials and efficient production methods. Here’s how the process ensures minimal waste:
- Precise Material Application: The silicone rubber material is carefully measured and placed into the mold cavity, leaving little room for excess material. This precision results in a minimal amount of surplus material.
- Efficient Mold Design: The design of the mold plays a crucial role in optimizing material usage. By creating molds that match the exact dimensions of the desired product, silicone rubber compression molding ensures that no material goes to waste.
- Consistent Production: The process’s ability to replicate products with consistent dimensions means that there’s no need to discard parts due to variations or defects. This further reduces wastage.
Cost and Environmental Advantages of Reduced Material Wastage
The cost and environmental benefits of reduced material wastage in silicone rubber compression molding are substantial:
- Cost Savings: Less material wastage directly translates to cost savings. Manufacturers spend less on acquiring raw materials, which can be a significant expense, particularly in larger production runs.
- Energy Efficiency: With less material to process, the overall energy consumption during production decreases. This aligns with sustainable practices and reduces the carbon footprint associated with manufacturing.
- Eco-Friendly Reputation: As environmental concerns take center stage, adopting processes that generate less waste enhances a company’s reputation as an environmentally conscious entity.
- Regulatory Compliance: Many industries are subject to regulations that govern waste disposal. By minimizing waste, manufacturers ensure compliance with these regulations and avoid potential penalties.
- Resource Conservation: The conservation of raw materials through reduced wastage contributes to the sustainable use of resources, preserving them for future generations.
By prioritizing minimal waste generation, silicone rubber compression molding not only benefits the bottom line but also aligns with the growing global emphasis on sustainability. It exemplifies how innovation in manufacturing techniques can lead to significant positive impacts on both economic and environmental fronts.
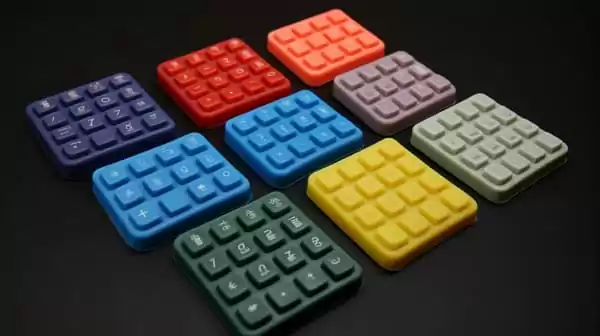
Conclusion
In the realm of manufacturing, few processes stand as versatile and advantageous as silicone rubber compression molding. From its ability to create intricate designs with precision to its contribution to various industries, the advantages of this method are undeniable. Let’s recap the key takeaways that highlight why silicone rubber compression molding remains a cornerstone in modern manufacturing:
Versatility Across Industries: Silicone rubber compression molding defies limitations, catering to industries as diverse as automotive, electronics, medical devices, and consumer goods. Its adaptability to various applications underscores its role as a manufacturing powerhouse.
High-Quality Surface Finish: The meticulous attention to surface quality is a testament to the process’s commitment to aesthetics and precision. Products born from silicone rubber compression molding boast exceptional surface finishes that captivate both the eye and the touch.
Consistency and Precision: This process champions consistent dimensions and precise details through mold design and pressure control. This level of accuracy is pivotal in industries that demand products with tight tolerances and exact specifications.
Material Options and Properties: The array of silicone rubber formulations available, each with its distinct properties, empowers manufacturers to select materials tailored to their product’s requirements. Flexibility, heat resistance, electrical insulation, and more are at their disposal.
Elastomeric Properties for Functionality: Silicone rubber’s elastomeric nature opens doors to sealing, shock absorption, and vibration isolation. Its ability to flex and rebound enhances the functionality of products across industries.
Low Waste and Environmental Benefits: Minimized material wastage highlights the process’s commitment to cost efficiency and environmental responsibility. The reduced carbon footprint and efficient resource usage are undeniable advantages.
Emphasizing its role as a versatile, efficient, and customizable manufacturing process, silicone rubber compression molding paves the way for innovation. It enables the creation of products that not only meet but exceed expectations, infusing quality, precision, and functionality into every facet. As industries evolve and demand more from manufacturing methods, silicone rubber compression molding stands as an exemplar of adaptability and excellence, shaping the products that shape our world.