Introduction:
Silicone rubber, known for its exceptional versatility and durability, plays a pivotal role in a myriad of industries. Esteemed for its high temperature resistance, flexibility, and inert nature, silicone rubber is a cornerstone material in fields ranging from medical and automotive to culinary and construction. Its unique ability to be molded into diverse shapes and forms makes it an invaluable resource for both industrial applications and everyday products.
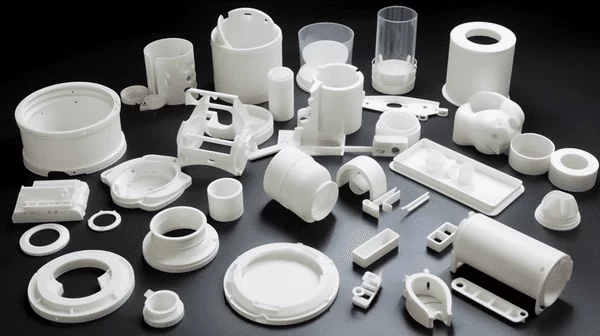
In this comprehensive guide, we aim to illuminate the path for selecting the most appropriate silicone rubber materials for molding projects. Whether you are in the business of creating intricate medical devices, crafting custom kitchenware, or producing robust automotive parts, understanding the nuances of silicone rubber will be crucial. We’ll explore the various types of silicone rubber, delve into their specific properties, and provide insights on how to choose the right material for your particular application. This article is designed to assist manufacturers, designers, and DIY enthusiasts alike in navigating the intricacies of silicone mold and rubber selection, ensuring the success of their molding endeavors.
Understanding Silicone Rubber
Types of Silicone Rubber
Liquid Silicone Rubber (LSR): LSR is renowned for its fluidity and ease of use in the injection molding process, making it a prime choice for high volume production. It’s particularly suited for creating intricate designs and complex shapes, thanks to its ability to flow into detailed molds. This attribute makes the LSR injection molding ideal for manufacturing components in the medical, automotive, and consumer electronics sectors.
High Consistency Rubber (HCR): HCR, known for its higher viscosity compared to LSR, is widely used in mold making, particularly for natural rubber products. Its stiffer consistency makes it suitable for processes like extrusion and compression molding. HCR is often preferred for creating larger, more robust items that require enhanced physical strength and durability.
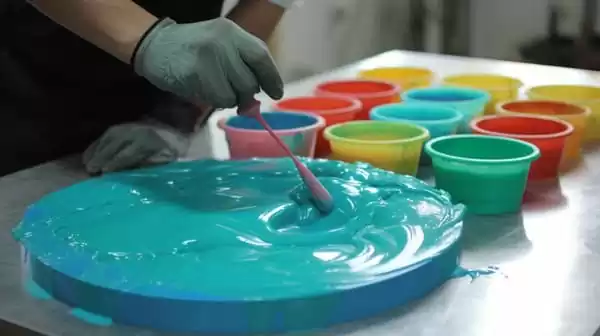
Room Temperature Vulcanizing (RTV) Silicone: RTV silicone stands out for its ease of use in smaller-scale and custom projects. This type of silicone cures at room temperature, making it ideal for DIY enthusiasts and artisans. It’s widely used for flexible molds, especially in the arts and crafts sector for casting silicone, resins, and other materials. RTV silicone’s ability to cure without additional heating equipment makes it a popular choice for quick and efficient mold creation.
Key Properties of Silicone Rubber
Temperature Resistance: One of the standout advantages of silicone rubber is its exceptional temperature resistance. Unlike many other materials, it can withstand both high and low temperature extremes without losing its integrity. This makes it an excellent choice for applications that involve exposure to varying temperatures, such as kitchenware, automotive parts, and industrial seals.
Chemical Resistance: Compared to materials like latex or certain polymers, silicone rubber exhibits superior resistance to a wide range of chemicals. This chemical inertness ensures that silicone products do not degrade easily when in contact with oils, solvents, and other harsh substances, enhancing their longevity and reliability in demanding environments.
Electrical Insulation Properties: Silicone rubber is highly valued in the electronics industry for its electrical insulation properties. It provides an effective barrier against electrical currents, making it essential for insulating wires, cables, and other electronic components. This property is crucial in ensuring the safety and functionality of a wide array of electronic devices.
Factors to Consider When Choosing Silicone Rubber
1: Application Requirements
Mold Complexity and Detail: When selecting silicone rubber molds, it’s crucial to consider the complexity and detail required in the mold. For molds that demand high precision and intricate details, liquid silicone rubber (LSR) is often the best choice due to its low viscosity and ability to capture fine features. In contrast, for less complex molds, high consistency rubber (HCR) might be more suitable due to its sturdier nature.
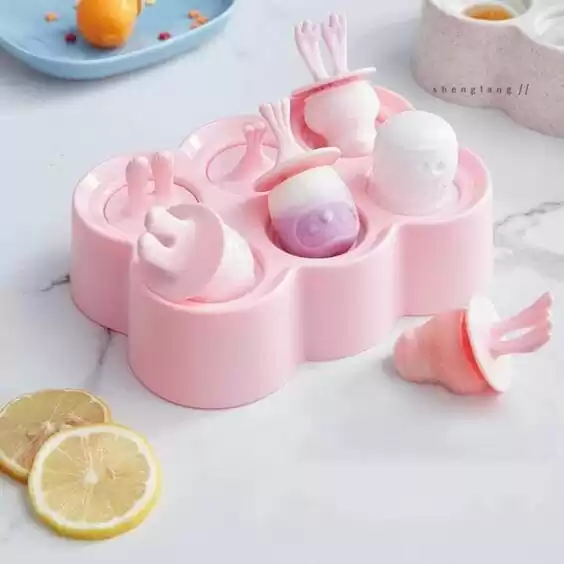
Importance of Food-Grade Silicone: For applications involving contact with food, choosing food-grade silicone is essential. This type of silicone meets specific FDA standards for safety and is non-toxic, making it ideal for kitchenware, baking molds, and other culinary tools. Food-grade silicone ensures that there is no harmful leaching of chemicals into the food, maintaining both the integrity of the silicone product and the safety of the food items.
2: Manufacturing Process
Injection Molding Process: For large-scale production, the injection molding process using liquid silicone rubber is highly efficient. This process is well-suited for producing high volumes of consistent, high-quality parts with a quick turnaround. It’s particularly beneficial for industries like medical, automotive, and consumer products where precision and scalability are key.
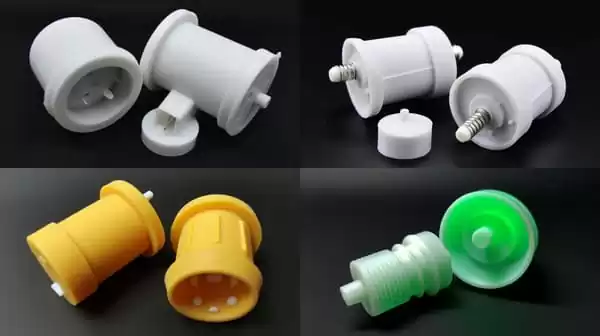
Curing Process: Heat Curing vs. Room Temperature Curing: The choice between heat curing and room temperature curing silicones (like RTV silicone) depends on the specific application and available resources. Heat-cured silicones generally offer faster curing times and stronger physical properties, making them suitable for industrial applications. In contrast, RTV silicones are ideal for smaller projects or applications where heat-curing equipment is not available.
3: Compliance and Standards
Adhering to Industry-Specific Standards and Regulations: Compliance with industry standards and regulations is a critical factor when selecting silicone rubber. Different industries have specific requirements regarding material properties, safety, and performance. For example, medical-grade silicones must meet stringent biocompatibility standards, while silicones used in aerospace or automotive industries might need to fulfill different durability and resistance criteria. Ensuring that the chosen silicone rubber aligns with these standards is crucial for both legal compliance and the success of the final product.
Tips for Beginners in Silicone Molding
1: Choosing the Right Mold Making
Evaluating the Best Material for Mold Durability and Flexibility: For beginners, selecting the right silicone material is crucial in ensuring both the durability and flexibility of the mold. If the project requires a flexible mold, with high flexibility and strength, liquid silicone rubber (LSR) is often the best choice. For projects that demand more rigidity and robustness, high consistency rubber (HCR) can be more suitable. Consider the end-use of the mold – if it’s for intricate, delicate items, opt for a softer silicone; for larger, more robust items, a firmer silicone would be preferable.
2: Mixing and Curing
Importance of Correctly Mixing Components for Effective Curing: Proper mixing of silicone components is vital for achieving the desired properties and effective curing. Beginners should pay close attention to the manufacturer’s instructions on mixing ratios to ensure the silicone cures correctly. Inconsistent or incorrect mixing can lead to a mold that is either too soft or too brittle, or one that does not cure properly.
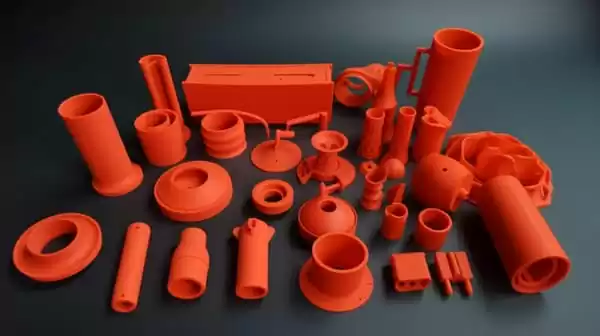
Specifics of Working with Two-Part Silicones: When working with two-part silicones like RTV silicone and silicone putty, it’s essential to mix the two components thoroughly to initiate the curing process. These types of silicones typically have a part A and part B, which need to be mixed in precise ratios. The working time (time before the silicone starts setting) can vary, so it’s important to mix quickly and efficiently, then proceed with the molding process.
3: Mold Making Considerations
Considerations of Hardness, Flexibility, and the Use of Release Agents: In mold making, understanding the hardness (shore hardness) and flexibility required for your project is key. Harder silicones are more resistant to wear and tear, while softer silicones are better for molds with intricate details. Additionally, the use of release agents is crucial in extending the life of the mold and ensuring easy demolding. Release agents prevent the silicone from sticking to the model or itself, which is particularly important when creating complex or multi-part molds.
Conclusion
In conclusion, the journey of selecting the right silicone rubber for molding projects is both an art and a science. As we have explored, silicone rubber’s versatility makes it an invaluable material across a broad spectrum of industries. From the precision required in medical devices to the durability needed in automotive parts, and from the creativity in artisan crafts to lower cost and the efficiency in high volume production, silicone rubber proves to be a material of choice.
The decision-making process involves careful consideration of mold complexity, material properties like temperature and chemical resistance, and compliance with industry standards. Whether you are handling a small-scale project or gearing up for mass production, the type of silicone rubber you choose can significantly impact the quality and success of your final product.
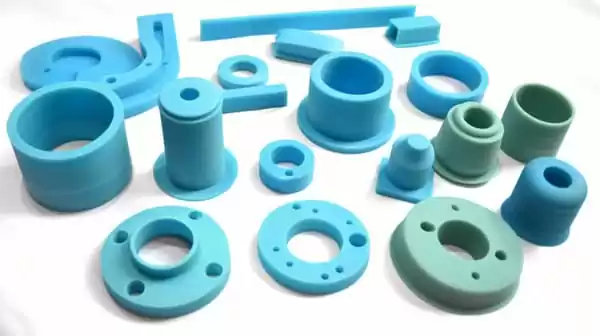
For beginners and experts alike, understanding the nuances of silicone rubber — from liquid silicone rubber (LSR) for intricate designs to high consistency rubber (HCR) for sturdier applications, and from the versatility of room-temperature vulcanizing (RTV) silicone to the precision of the injection molding process — is fundamental. Correctly mixing and curing, along with thoughtful mold design and the use of release agents, are crucial steps to master.
Silicone rubber’s role in driving innovation and quality in various sectors cannot be overstated. Its adaptability and range of properties make it an excellent choice for a myriad of applications, ensuring both practicality and creativity in molding. By making informed choices about silicone rubber materials, you can enhance the efficiency, safety, and aesthetic appeal of your projects, regardless of the scale or industry.
In essence, the journey in selecting the right silicone rubber for your molding needs is as dynamic and diverse as the material itself. Embracing this journey can lead to remarkable outcomes in both product development and creative endeavors.