Introduction
Silicone rubber compression molding is a widely utilized manufacturing method used to produce various rubber products such as gaskets, seals, O-rings, and other components. This process involves compressing uncured silicone rubber into mold cavities at high pressure and heat until it achieves the desired shape.
Finding cost-effective silicone rubber compression molding solutions in today’s highly competitive marketplace is essential to remaining profitable and offering quality products to customers at reasonable prices. Businesses must identify ways of lowering production costs while improving efficiencies to remain cost-effective while meeting customers’ demands for high-quality goods at reasonable costs.
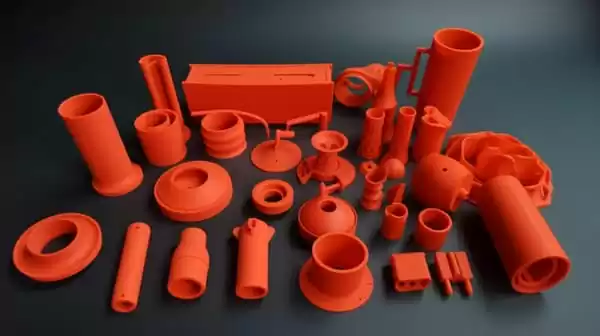
This article seeks to offer insight into cost-effective solutions for silicone rubber compression molding. In the following sections, we will explore alternative molding methods, ways to shorten production time, the costs associated with the compression molding process as well as key factors and advantages and benefits of silicone rubber compression molding manufacturing processes.
II. Compression Molding Alternatives
Compression molding is a well-established manufacturing process that has been used for many years to produce high-quality rubber products. However, there are alternative molding methods available that may be more suitable for certain applications.
One popular alternative to compression molding is injection molding. Injection molding involves injecting molten rubber material into a mold cavity under high pressure to create the desired shape. Compared to compression molding, injection molding can produce parts with greater precision and consistency.
Another alternative is transfer molding, which is similar to compression molding but involves using a plunger to force the rubber material into the mold cavity. This method can produce parts with less flash and waste, but it may not be as efficient as compression molding for high-volume production runs.
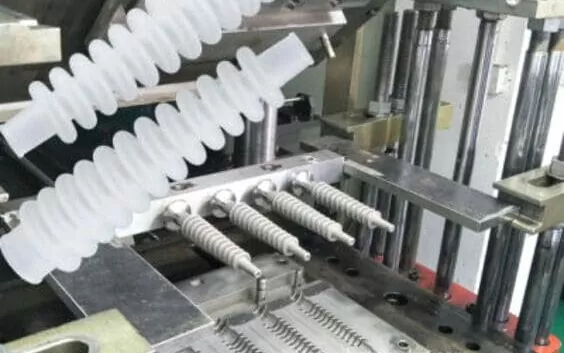
The choice between compression molding and alternative methods depends on various factors, such as the desired part geometry, volume of production, and material properties. Here are some advantages and disadvantages of alternative molding methods:
- Injection molding: Advantages:
- High precision and consistency
- Fast production cycle time
- Suitable for complex part geometries Disadvantages:
- High tooling costs
- Limited material options
- Not suitable for large parts
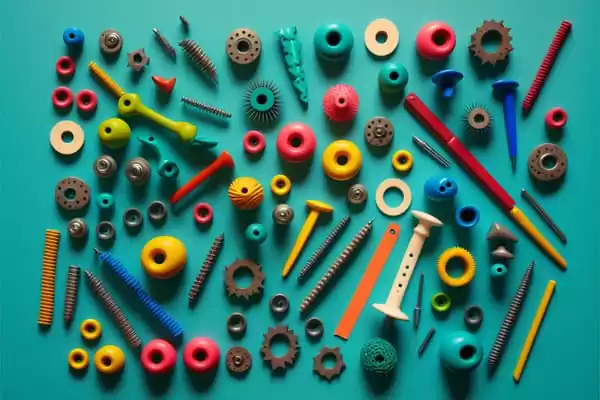
- Transfer molding: Advantages:
- Less flash and waste
- Better control over material flow
- Suitable for parts with inserts Disadvantages:
- Longer cycle time
- Limited material options
- Tooling costs can be high
Overall, it is important to consider the specific requirements of each project when choosing a molding method. Compression molding remains a viable and cost-effective option for many applications, especially those that require high-volume production runs and a wide range of material options.
Ⅲ. Ways to Reduce Production Time in Compression Molding
Production time in compression molding can play a significant role in the total cost of manufacturing silicone rubber products, impacting cost and delivery timelines significantly. By shortening production times, businesses can increase efficiency and productivity and lower manufacturing costs with faster delivery times – thus saving costs and shortening delivery times while improving profitability. Below are three methods for decreasing compression molding production time:
A. Multi-Cavity Molds:
Multi-cavity molds can help businesses boost productivity and decrease production time by creating multiple cavities in one mold to produce multiple parts per cycle, thus decreasing mold opening/closing time and improving efficiency.
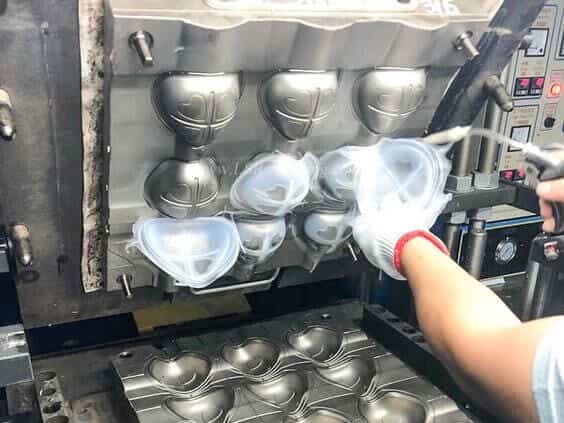
B. Heated Molds:
Heated molds can help speed up production times by shortening curing times for rubber material, leading to faster production times. By heating the mold, curing of rubber materials occurs faster and cycle time decreases accordingly – especially useful when running high-volume production runs where even minor improvements in cycle times can mean significant cost savings.
C. Transfer Molding:
Transfer molding is another molding method that can reduce production times when it comes to compression molding. Transfer molding uses a plunger to force rubber material into mold cavities quickly, giving businesses faster cycle times than compression molding due to quicker delivery by its plunger mechanism.
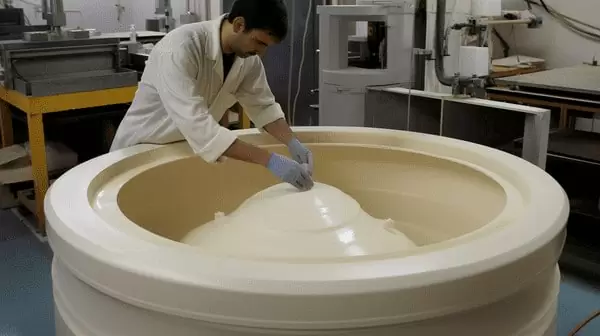
Eliminating production time is key to finding cost-effective silicone rubber compression molding solutions. By employing multi-cavity compression molds , heated molds or transfer molding techniques businesses can improve efficiency, shorten cycle times and produce quality rubber products more quickly.
Ⅳ.Cost of Compression Molding Process
Understanding what drives up the cost of silicone compression molding, can be critical for finding cost-effective silicone rubber compression molding solutions. Here are some factors affecting its cost:
Material Costs:
The costs associated with raw rubber material used in compression molding processes can differ depending on both its type and volume needed for molding purposes.
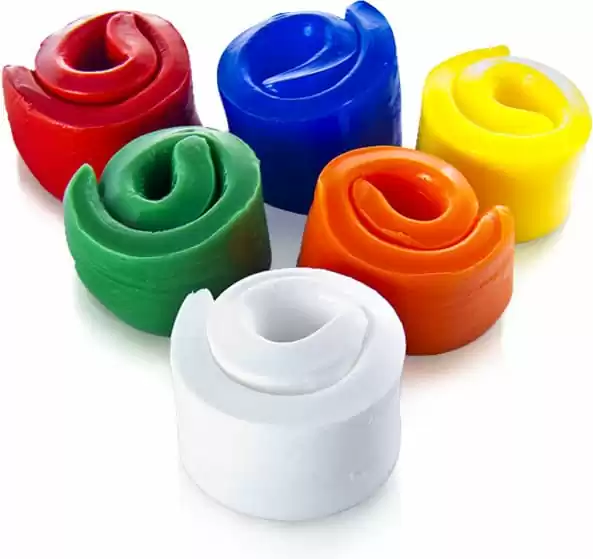
Tooling Cost:
The costs associated with creating molds used in compression molding processes may be significant for custom or complex parts.
Labor cost:
The labor costs associated with compression molding include operating costs associated with operating the molding equipment as well as the labor required to assemble and finish parts.
Overhead Costs:
Overhead expenses such as rent, utilities, and insurance policies make up part of an individual’s overhead costs.
Breaking down cost components can help businesses identify areas for cost savings. Reducing material waste or optimizing production processes could reduce labor costs while choosing suitable mold materials and designs could cut tooling expenses.
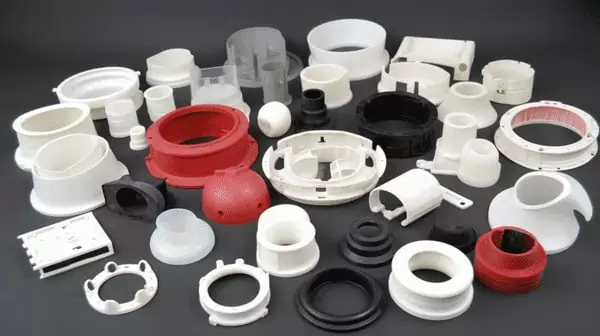
Compression molding may be more cost-effective for applications that require high-volume production runs than other molding methods such as injection and transfer molding, which may incur higher tooling costs and take longer cycle times. When choosing the most cost-effective molding technique for each project, consideration must be given to its specific requirements, and consideration of each project should also be made when making decisions regarding the molding services selection.
Overall, finding cost-effective silicone rubber compression molding solutions requires understanding all cost factors involved and recognizing opportunities for cost savings. By optimizing production processes, choosing appropriate materials and designs, and cutting wasteful production practices businesses can achieve cost-effective silicone rubber parts and product manufacturing solutions for their products.
Ⅴ.Key Factors in Silicone Rubber Compression Molding
Silicone rubber compression molding is a complex process that must be managed carefully for optimal results. Here are a few essential factors businesses must take into account when engaging in silicone rubber compression molding:
Considerations in Mold Design:
A well-designed mold design is key to producing quality silicone rubber compression molding parts, taking into account such factors as part geometry, desired surface finish, and draft angles. Venting and gating techniques for mold plates may also help ensure smooth material flow while decreasing defects risk.
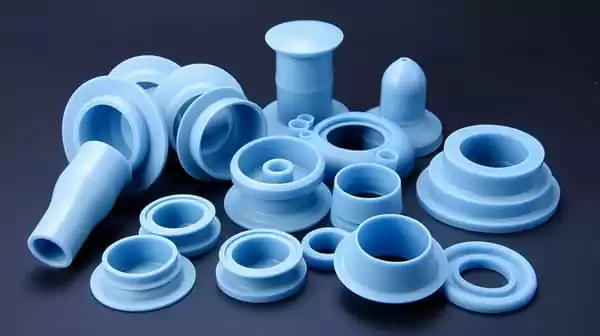
Rubber Material Options:
Selecting the ideal rubber material can have a dramatic impact on its properties and performance in the final product. Hardness, elasticity, temperature resistance, chemical resistance, and UV light resistance must all be taken into consideration when making this selection decision.
Tooling and Molding Equipment:
Selecting the appropriate tooling and molding equipment is essential to producing consistent, high-quality parts. Factors like the mold size, material and finish as well as pressure and temperature control systems all play a part in determining its final quality.
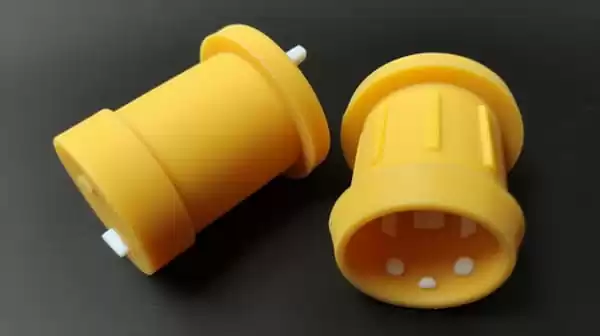
Manufacturing Process and Extrusion Techniques:
The manufacturing process and extrusion techniques utilized can greatly impact the properties, quality, and consistency of final products. Therefore, their optimization should aim at minimizing cycle times, waste production, and consistent production for maximum output.
Optimizing these key factors can help businesses achieve consistent, high-quality silicone rubber compression molding results. By working with experienced professionals and investing in quality materials and equipment, businesses can enhance their production processes to provide cost-effective solutions to their customers.
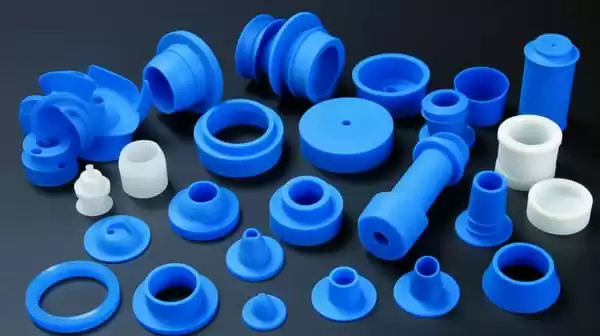
Ⅵ.Advantages and Benefits of Silicone Rubber Compression Molding
Silicone rubber compression molding offers many advantages over other molding methods, making it a top choice for many industries and products. Here are some benefits of silicone rubber compression molding:
Cost-Effective:
Compression molding is an economical method of producing high-volume runs of rubber products. Although initial tooling costs may be high, their overall costs per part tend to decrease as production volumes increase.
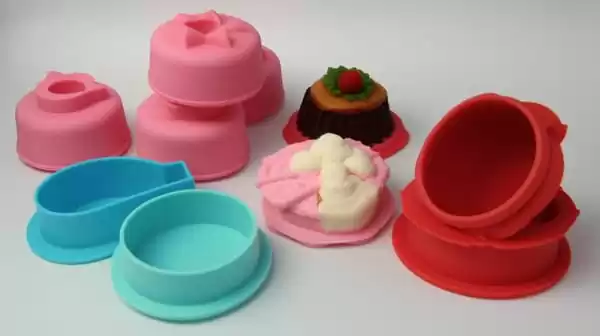
Silicone Rubber Compression Molding Offers Multiple Material Options:
Silicone rubber compression molding offers businesses a range of materials for compression molding – including liquid silicone rubber, synthetic rubber, and other custom rubber compounds – to choose from to meet their particular requirements and applications. This allows businesses to select one which best matches them.
Reliable Parts:
Compression molding has proven its ability to produce consistently high-quality parts with tight tolerances and excellent surface finishes, making it especially suitable for applications requiring precision and reliability.
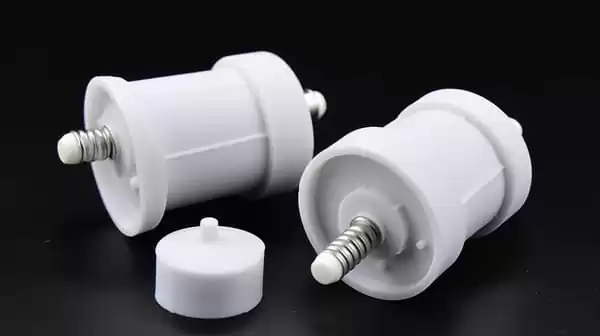
Compression Molding Is Suited for Multiple Industries and Products:
Compression molding can be used across numerous industries and products, from automotive to aerospace, medical, and consumer goods – making it a versatile option that many businesses choose for themselves.
Compression molding offers several advantages over other molding techniques like injection and transfer molding, such as injection and transfer molding. While injection molding produces high-precision parts with relatively lower initial tooling costs, transfer molding is less efficient for high-volume runs than compression molding.
Silicone rubber compression molding is used extensively across numerous industries for creating gaskets, seals, O-rings, rubber grommets, and other components such as seals. Additionally, this technique can produce parts with inserts, complex geometries, or different durometers.
Silicone rubber compression molding offers many advantages and benefits that make it an appealing option for many applications. By optimizing production processes and selecting cost-effective materials and designs, businesses can produce high-quality rubber products at reduced costs.
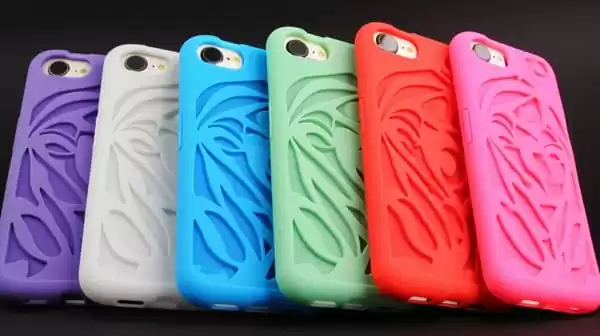
Conclusion
In summary, cost-effective silicone rubber compression molding solutions require careful consideration of several factors, including mold design, rubber material options, tooling and molding equipment, and manufacturing processes. By optimizing these factors businesses can achieve high-quality, consistent results while simultaneously increasing efficiency and productivity.
Compression molding offers many advantages over other molding methods, including cost-effectiveness, material availability, and high-quality parts that meet specific industry and product needs. Businesses should take into account alternative molding solutions when identifying the most cost-effective solution for their specific requirements.
Compression molding is an efficient manufacturing method for producing high-quality rubber products, using multi-cavity molds, heated molds and transfer molding techniques to significantly cut production times.
The cost of silicone compression mold-ing will depend on various factors, including material, tooling, labor costs, and overhead expenses. Mold design, rubber material choices, tooling/molding equipment options, and manufacturing processes are key elements in silicone rubber compression molding.
Compression molding offers several distinct advantages over other molding methods, including cost-efficiency, material flexibility, and high-quality parts production suited for multiple industries and products.
By understanding and implementing cost-effective solutions in silicone rubber compression molding, businesses can achieve optimal results while remaining competitive in today’s market.