It’s no secret that heat can damage rubber products. But did you know that there are ways to formulate rubber so that it can withstand high temperatures?
In this blog post, we’ll explore the different ways to formulate heat-resistant rubber and how they can benefit your business. We’ll also discuss some of the factors you should consider when choosing a formulation method. So if you’re looking for a way to protect your rubber products from heat, read on!
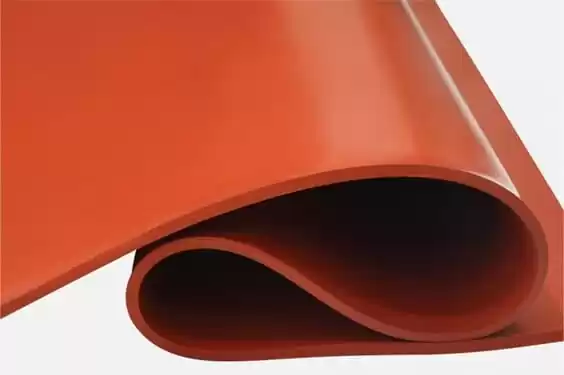
What is heat resistant rubber and why do we need it?
Heat-resistant rubber is an elastic material designed to withstand high temperatures. It is commonly used in various industrial and commercial applications such as gaskets, seals and hoses.
Heat-resistant rubber has many advantages over other types of materials. It is durable, resilient, and has excellent heat resistance.
Additionally, heat-resistant rubber is often more cost-effective than other options. As the name suggests, heat-resistant rubber is an ideal material for applications that require resistance to high temperatures.
However, it should be noted that heat-resistant rubber is not completely immune to heat damage. It will eventually degrade with prolonged exposure to heat. Despite this, heat-resistant rubbers provide excellent performance in many applications.
Heat resistance refers to the ability of rubber and its products to maintain physical and mechanical properties or performance after being subjected to long-term thermal aging. Essentially no decline of this nature.
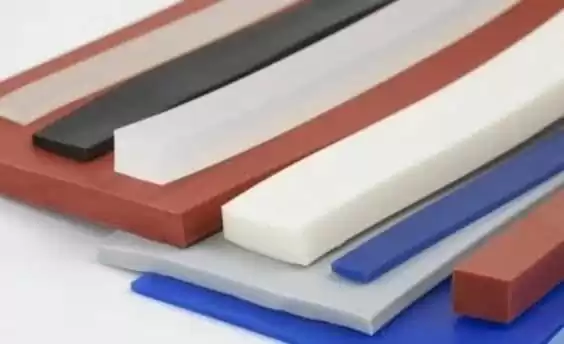
The difference between the physical and mechanical properties at high temperature and that at room temperature is small, that is, the temperature resistance is good. Indicates the variation of the physical and mechanical properties of rubber with (test) temperature.
(Heat-resistant) rubber products used at high temperatures must have good heat resistance and good temperature resistance.
There are many ways to evaluate heat resistance, such as using Martin heat resistance and Vicat heat resistance to evaluate the degree of heat resistance.
The decomposition temperature can also be found through the thermogravimetric instrument as the upper limit of the material’s service temperature, or vacuum heating for 40 to 45 minutes, the temperature at which the mass is reduced by 50% (Tn)—the half-life temperature to evaluate the heat resistance.
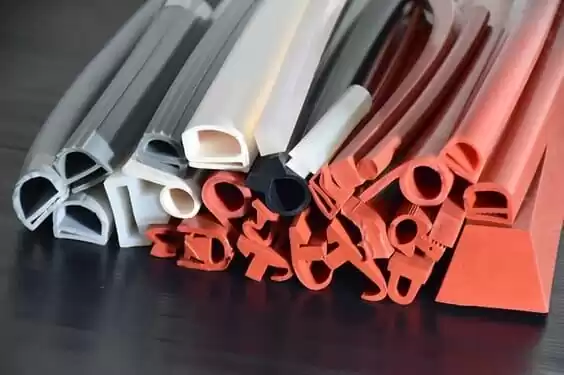
Heat-resistant rubber refers to the vulcanized rubber that can still maintain the original mechanical properties and use value under high temperature conditions for a long time.
The amount of change in properties (such as hardness) and rate of change in properties (such as tensile strength, ), performance retention rate, and aging coefficient indicate the change of its mechanical properties.
In rubber sealing products, the heat resistance of vulcanized rubber in a compressed state is called heat resistance compression performance, which is often evaluated by the compression set coefficient or compression stress relaxation coefficient.
Rubber that can basically maintain its original performance and use value after long-term use above 80°C belongs to the category of “heat-resistant rubber”. The heat-resistant and high-temperature performance of silicone rubber products is the most common performance among the special properties of rubber.
The essential reason for the stable performance of rubber in this case is that it can resist the influence of factors such as oxygen, ozone, corrosive chemicals, high-energy radiation, and mechanical fatigue at high temperatures. Good performance.
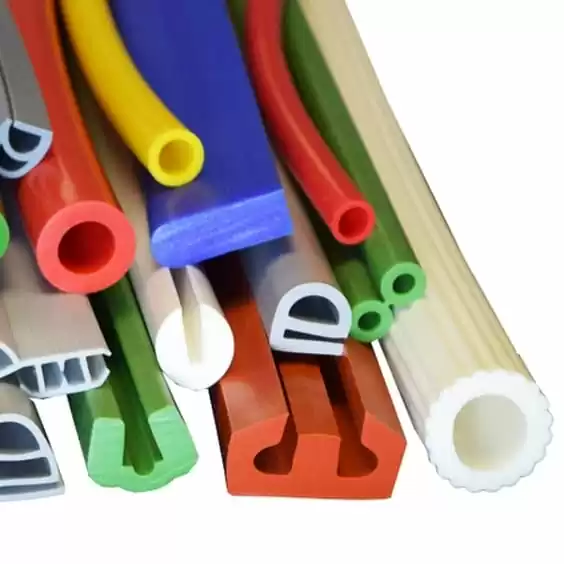
Operating temperature range/°C Applicable rubber
70~100 Natural rubber, styrene-butadiene rubber
100~130 Neoprene rubber, nitrile rubber, epichlorohydrin rubber
130~150 Butyl rubber, ethylene propylene rubber, chlorosulfonated polyethylene rubber
150~180 Acrylic rubber, hydrogenated nitrile rubber
180~200 vinyl silicone rubber, fluorine rubber
200~250 Dimethyl silicone rubber, fluorine rubber
>250 Perfluoroether rubber, fluorosilicone rubber, borosilicate rubber
The temperature resistance of national standard rubber can be divided into the following two grades and five categories
Ordinary rubber A -70~-30℃/90~120℃, such as NR, IR, BR, 237 SBR, CR.
Ordinary rubber B -40~-20℃/120~150℃, such as NBR, IIR, EPDM, CSM.
Ordinary rubber C -30~10℃/80~90℃, such as T, U.
Heat-resistant rubber A -30~-10℃/150~200℃, such as ACM, ANM, EVA, CO, ECO.
Heat-resistant rubber B -70~-20℃/250~300℃, such as MQ, MVQ, FPM, FKM.
However, in actual use, due to the influence of various internal and external factors, in order to ensure a safe service life, the general diene rubber is controlled at about 100 °C, the oil-resistant nitrile rubber is 130 °C, and the acrylate rubber is 180 °C. ℃.
The temperature of silicon and fluorine rubber is 200-250°C, and it can reach 300-350°C for short-term use. There are also 4 categories:
The heat resistance of silicone rubber products mainly depends on the type of rubber used. Therefore, when designing the formula, the choice of raw rubber should be considered first.
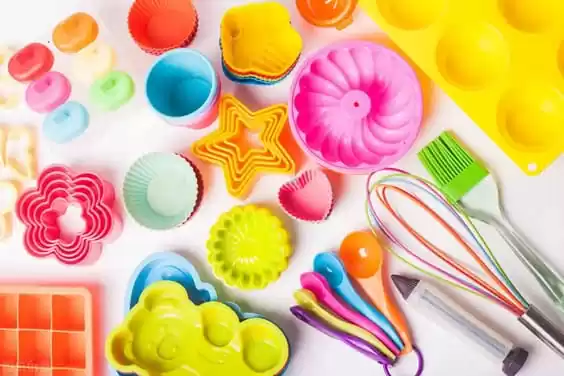
The heat resistance of rubber is manifested in the high viscous flow temperature, high thermal decomposition stability and good thermochemical stability of rubber.
The viscous flow temperature of rubber depends on the polarity of the molecular structure of the rubber and the rigidity of the molecular chain. The greater the polarity and rigidity, the higher the viscous flow temperature.
The polarity of rubber molecules is determined by its polar groups and molecular structure, and the rigidity of molecular chains is also related to the regularity of polar substituents and spatial structure arrangements.
Introducing 238 cyano groups, ester groups, hydroxyl groups or chlorine atoms, fluorine atoms, etc. into rubber molecules will improve heat resistance.
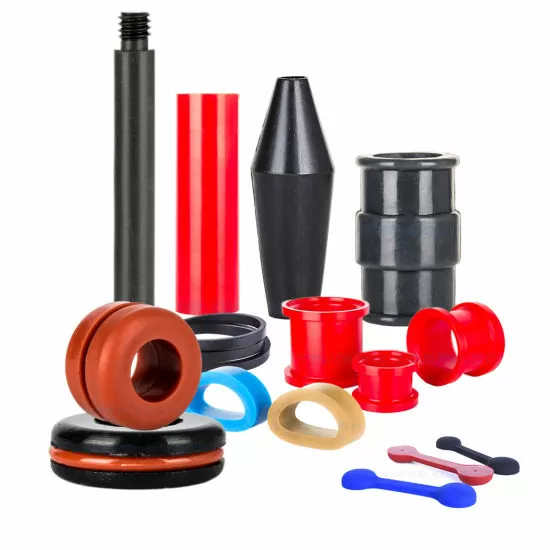
The thermal decomposition temperature of rubber depends on the chemical bond properties of the molecular structure of the rubber.
The higher the chemical bond energy, the better the heat resistance. Macromolecular chains such as borosilicate rubber, silicone rubber, and polyphenylsiloxane have high bond energy, so they have excellent heat resistance.
Generally speaking, except for fluorine-containing FPM, carbon chain rubber has low heat resistance and can be used for a long time at a temperature of 150-200°C;
The main chain does not contain carbon atoms at all, such as elemental organic polymers, such as Q type, Its heat resistance is very good, and silica gel can be used for a long time at 250°C or even 300°C.
The chemical stability of rubber is an important factor for heat resistance, because under high temperature conditions, if some chemical substances come into contact with oxygen, ozone, acid, alkali and organic solvents.
They will promote the corrosion of rubber and reduce heat resistance. Chemical stability is closely related to the molecular structure of rubber.
Butyl rubber, ethylene-propylene rubber and chlorosulfonated polyethylene with low unsaturation show excellent heat resistance.
In addition, if there is an aromatic structure connected by a single bond on the main chain, the molecular chain will also stabilize the structure by virtue of the conjugation effect.
The heat resistance of rubber is related to the degree of saturation of the rubber molecular chain, the rigidity of the molecular chain, the polarity of the molecule, and the nature of the chemical bond. Rubber with the following molecular structure has better heat resistance.
Molecular chain saturation is high, such as butyl rubber, ethylene propylene rubber, etc.; there are more inorganic chains on the rubber main chain segment, such as the main chain of silicone rubber is a silicon-oxygen structure;
The rubber molecular chain contas halogen elements, Cyano group, ester group, etc., such as fluorine rubber, acrylate rubber, chlorosulfonated polyethylene, chlorinated butyl rubber, nitrile rubber, neoprene rubber.
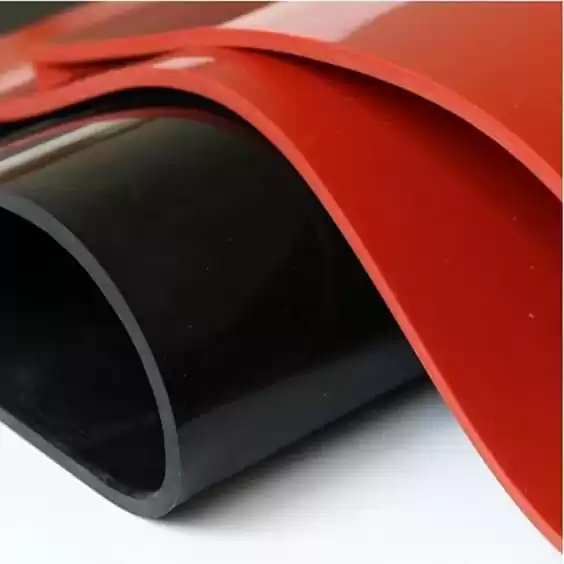
Different formulations of heat-resistant rubber
Different formulations of heat-resistant rubbers are designed to withstand different temperatures. The most common formulations are designed to withstand temperatures up to 350 degrees Fahrenheit.
This formulation is typically used in applications where the rubber will be exposed to intermittent high heat, such as gaskets and seals.
There are also higher-temperature formulations that can withstand temperatures up to 600 degrees Fahrenheit. These formulations are typically used in applications where the rubber will be continuously exposed to high heat, such as boiler gaskets or oven seals.
Higher temperature formulations are available for special applications, such as aerospace applications where the rubber must be able to withstand extreme temperatures. Different formulations of heat-resistant rubber are available to meet the needs of various applications.
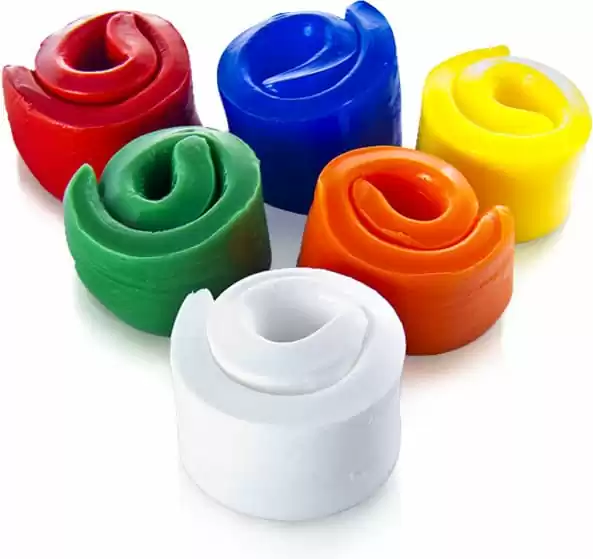
Proper use of heat-resistant rubber tips
If you are looking for a reliable, high quality, durable material that can withstand high temperatures then look no further than Heat Resistant Rubber.
This type of rubber is ideal for applications where there is a possibility of exposure to high temperatures, such as in gaskets and seals. However, it is important to note that heat resistant rubber is not indestructible and needs to be used correctly for best results. Here are 5 tips for getting heat-resistant rubber right.
1). Use the correct grade of heat resistant rubber for your application. There are different grades available, which are designed to withstand different temperature ranges. Make sure you choose the one that suits your needs.
2). Heat-resistant rubber will harden and become brittle over time when exposed to high temperatures. This could cause it to crack or break. To avoid this, make sure you check your heat-resistant rubber products regularly and replace them if necessary.
3). When installing heat-resistant rubber products, be careful not to damage them. Any cuts or tears weaken the product, making it more prone to failure.
4). Always follow the manufacturer’s instructions when using heat-resistant rubber products. Information on storage, installation and maintenance can be found on the product packaging or in the owner’s manual.
5). If you have any questions about using heat-resistant rubber, please consult a professional who has experience in working with this type of material. They will be able to advise you on the best way to use it in your particular application.
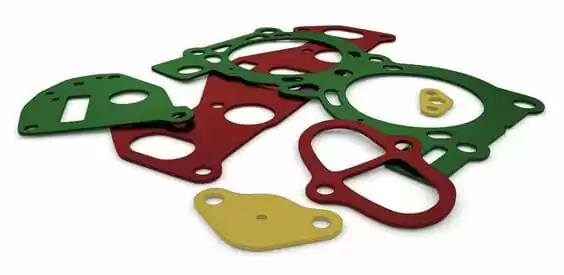
Conclusion
The formulation design of heat-resistant rubber is still an open problem. However, researchers have proposed a series of solutions to improve the thermal stability and mechanical properties of heat-resistant rubbers. We hope that this review article can provide some useful enlightenment for future research on formulation design of heat-resistant rubber.