Introduction
Light Emitting Diodes (LEDs) have revolutionized the lighting industry with their energy efficiency and versatility. From residential to commercial and industrial settings, LEDs have found extensive applications due to their numerous benefits over traditional lighting technologies.
With the growing demand for high-performance and reliable LED lighting solutions, the need for effective protection of LED components becomes paramount. LED encapsulation plays a crucial role in safeguarding these sensitive electronic devices from external factors that can degrade their performance and lifespan.
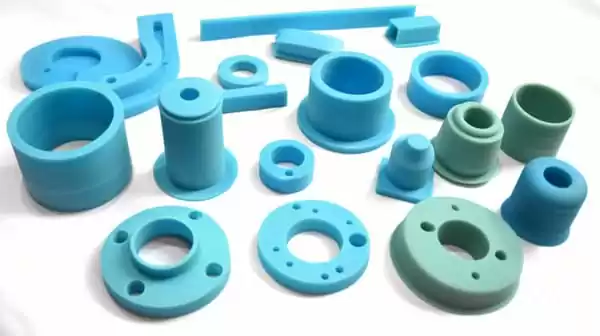
This article delves into the importance of LED encapsulation with silicone rubber and how it enhances both the protection and performance of LEDs. We will explore the unique physical properties of of silicone rubber that make it an ideal material for encapsulating LED components, ensuring their durability and efficiency in various lighting applications.
By understanding the significance of silicone rubber encapsulation, we gain valuable insights into how this technology continues to shape the future of LED lighting, providing sustainable and effective illumination solutions for a wide range of needs.
II. The Benefits of Silicone Rubber Encapsulation
A. Optical Clarity and Efficient Light Transmission
One of the key advantages of silicone rubber encapsulation for LED components is its exceptional optical clarity. Silicone materials have high light transmission properties, allowing LED light to pass through with minimal losses. This optical clarity ensures that the LED’s brightness and color accuracy are maintained, resulting in efficient and visually pleasing lighting.
When LED components are encapsulated with silicone rubber, the material forms a clear protective barrier around the delicate LED chip and other electronic elements. This barrier minimizes light scattering and absorption, allowing more light to be emitted from the LED package. As a result, silicone rubber encapsulation optimizes the efficiency and performance of LEDs, ensuring they produce maximum illumination with minimal wasted energy.
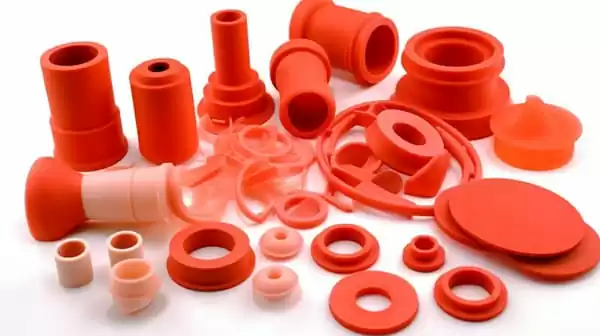
B. Durability and Resistance to Moisture, UV Radiation, and Higher Temperatures
Silicone rubber offers outstanding durability and protection for LED components, making it an excellent choice for outdoor and harsh environment applications. It provides a barrier against moisture and prevents the ingress of dust and other contaminants that could compromise the performance of LEDs.
Furthermore, silicone rubber is highly resistant to UV radiation, making it suitable for outdoor lighting applications exposed to direct sunlight. Unlike some other materials, silicone does not degrade or discolor when exposed to UV light, ensuring long-term stability and performance of LED components.
In addition to UV resistance, silicone rubber can withstand a wide range of temperatures. LEDs can generate heat during operation, especially high-power LEDs used in industrial and automotive applications. Silicone rubber’s thermal stability ensures that the encapsulated LED components can operate optimally even under elevated temperatures. This ability to handle higher temperatures contributes to the LED’s longevity and consistent performance over time.
C. Versatility in Creating Intricate Shapes for Various LED Components
Another significant benefit of silicone rubber encapsulation is its versatility in molding intricate shapes for different LED components. LED lighting often requires various optical elements, such as lenses, light guides, and light pipes, to direct and control the light output effectively.
Silicone rubber’s unique properties enable it to be molded into precise shapes, making it an ideal material for creating these optical components. Engineers and designers can customize the silicone mold to achieve the desired shape and optical properties, ensuring that the LED light is directed precisely where it is needed.
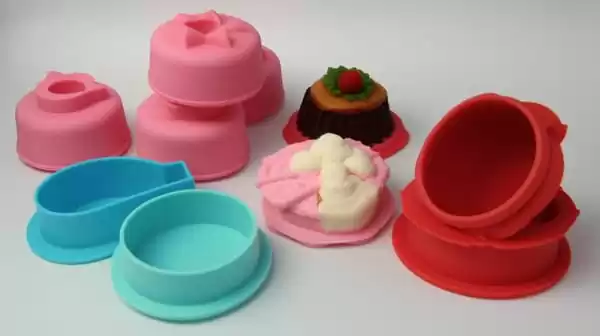
By encapsulating LED components with silicone rubber, manufacturers can create a wide range of LED lighting products with varying shapes and designs, meeting the specific requirements of different applications.
In conclusion, silicone rubber encapsulation offers numerous benefits for LED components. Its optical clarity enhances light transmission, ensuring efficient illumination, while its durability and resistance to moisture, UV radiation, and higher temperatures provide excellent protection and stability. The versatility of silicone rubber allows for the creation of intricate shapes, making it an ideal material for various LED components. By harnessing these advantages, LED manufacturers can produce high-quality, reliable, and long-lasting LED lighting solutions for a multitude of lighting applications.
III. Understanding the Molding Process
A. Compression Molding for LED Components
- Explanation of the Process and Its Advantages
Compression molding is a widely used technique for molding LED components with silicone rubber. The process begins by placing a pre-measured amount of liquid silicone rubber (LSR) into a mold cavity specifically designed to match the shape of the LED component. The mold is then closed, and pressure is applied to force the silicone material to take the exact shape of the mold.
During compression molding, the silicone rubber is subjected to heat, which initiates the curing process. The heat causes the silicone to solidify and take the desired shape of the LED component. The high pressure applied during the molding process ensures that the silicone material uniformly fills the mold cavity, resulting in precise and consistent LED components.
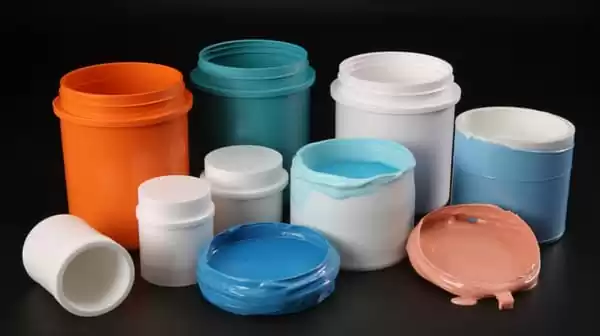
Advantages of Compression Molding for LED Components:
- Precise and Complex Shapes: Compression molding allows for the creation of intricate and custom shapes, such as lenses and optical components, which are essential for directing and controlling the light emitted by the LED. This precision is crucial for achieving optimal light distribution and efficiency.
- Enhanced Optical Clarity: The compression molding process ensures minimal air entrapment within the silicone material, leading to higher optical clarity and light transmission. This is particularly important for LEDs that require maximum brightness and uniform light distribution.
- Low Flash and Waste: Compression molding produces minimal flash (excess material) and waste, making it a cost-effective and environmentally-friendly manufacturing method. The efficient use of material contributes to reducing production costs and minimizing the impact on the environment.
B. Injection Molding for LED Encapsulation
- Description of the Process and Its Benefits for Mass Production
Injection molding is another widely adopted method for LED encapsulation, especially when high-volume production is required. In this process, the liquid silicone rubber is heated and injected into a closed mold under high pressure using an injection molding machine.
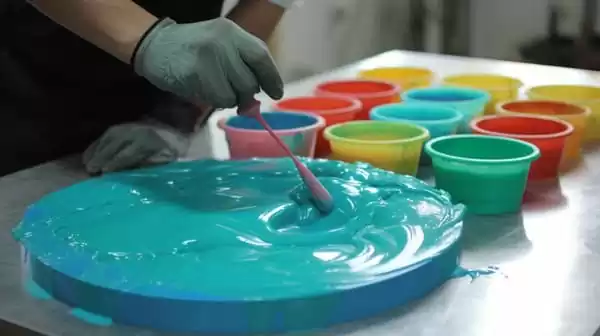
The injection molding process begins with the preparation of the silicone material, which is heated to its liquid form and then injected into the mold cavity through a nozzle. The mold is designed to accommodate multiple cavities, allowing for the production of multiple LED components simultaneously, thereby facilitating mass production.
Once the silicone material fills the mold cavity, it is left to cool and cure. After curing, the mold is opened, and the solidified LED components are ejected from the mold.
Benefits of Injection Molding for LED Encapsulation:
- High Production Efficiency: Injection molding is a highly efficient process that enables rapid production of large quantities of LED components. This is particularly advantageous for meeting the high demand in the LED lighting industry, where large volumes of LEDs are required for various applications.
- Consistency and Uniformity: Injection molding ensures consistent and uniform LED components, reducing variations and ensuring the same high-quality output for each piece. The reliability and uniformity of the produced LEDs are critical for maintaining product performance and customer satisfaction.
- Cost-Effectiveness: Although the initial setup costs for injection molding may be higher, the process becomes more cost-effective in mass production due to its speed and efficiency. The ability to produce a large number of LED components in a relatively short time helps manufacturers optimize production costs.
In conclusion, both compression molding and injection molding are valuable techniques for molding LED components with silicone rubber. Each method offers distinct advantages, catering to different production needs and requirements. The choice of molding process depends on factors such as the complexity of the LED component’s shape, the required production volume, and the desired level of precision. Regardless of the method chosen, silicone rubber encapsulation through molding plays a vital role in ensuring the reliability, efficiency, and performance of LED lighting solutions.
IV. Silicone Materials for LED Encapsulation
A. Properties of Silicone Rubber That Make It Suitable for LED Applications
Silicone rubber possesses a unique set of properties that make it an ideal material for LED encapsulation. These properties contribute to the protection and enhanced performance of LED components in various lighting applications.
- Optical Transparency: Silicone rubber exhibits excellent optical transparency, allowing light to pass through with minimal scattering and absorption. This property ensures efficient light transmission, maximizing the brightness and clarity of the LED output.
- Flexibility and Resilience: Silicone rubber is inherently flexible and resilient, which is crucial for protecting delicate LED components from mechanical stress and vibrations. Its ability to absorb and dissipate mechanical shocks helps enhance the LED’s durability and reliability.
- Thermal Stability: LEDs generate heat during operation, and silicone rubber can withstand a wide range of temperatures. This thermal stability ensures that the encapsulated LED components can operate optimally, even in environments with elevated temperatures.
- Resistance to Moisture and Environmental Elements: Silicone rubber is highly resistant to moisture, making it effective in preventing water ingress that could lead to corrosion or malfunction of the LED. Additionally, silicone’s resistance to environmental elements such as dust and chemicals helps protect the LED components in diverse operating conditions.
- UV Resistance: Silicone rubber is inherently resistant to UV radiation, making it suitable for outdoor LED applications exposed to direct sunlight. Unlike some other materials, silicone does not degrade or discolor when exposed to UV light, ensuring long-term stability and performance of LED components in outdoor environments.
- Low Volatile Content: High-quality silicone materials used in LED encapsulation have low volatile content, reducing the risk of outgassing that could cause performance issues or reduce optical clarity.
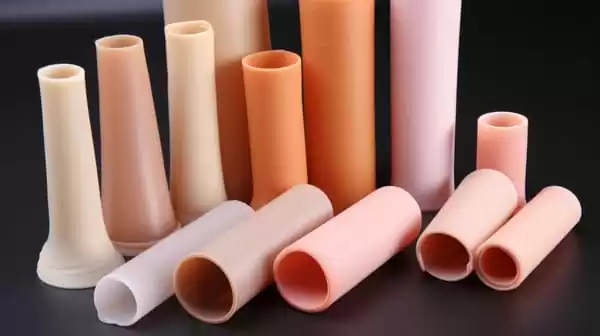
B. Role of Optical-Grade Silicones in Creating Lenses, Light Guides, and Light Pipes
Optical-grade silicones play a critical role in the manufacturing of lenses, light guides, and light pipes for LED applications. These components are essential for directing, shaping, and distributing light emitted by the LED, ensuring optimal illumination in various lighting fixtures outdoor applications.
- Optical Clarity and Light Transmission: Optical-grade silicones offer exceptional optical clarity, enabling maximum light transmission through the components. This high light transmittance ensures efficient utilization of the LED’s output and reduces energy wastage.
- Design Flexibility: Optical-grade silicones can be easily molded into intricate shapes, allowing for the design of custom lenses and light guides tailored to specific lighting requirements. Their versatility in shaping the light path ensures precise light control and distribution.
- Efficient Light Distribution: Light guides and light pipes made from optical-grade silicones efficiently distribute light from the LED to desired locations, ensuring uniform illumination and avoiding hotspots or dark areas.
- Durability and Longevity: The use of optical-grade silicones in lenses, light guides, and light pipes enhances their durability and resistance to environmental factors, such as UV exposure and moisture. This durability extends the lifespan of the LED lighting fixture.
- Optimum Color Accuracy: Optical-grade silicones exhibit minimal color distortion, preserving the LED’s color accuracy and ensuring consistent lighting across different applications.
In conclusion, silicone rubber, especially the optical-grade variety, offers a range of properties that make it well-suited for LED encapsulation and the creation of optical components. Its optical transparency, flexibility, thermal and optical stability throughout, and resistance to moisture and UV radiation contribute to the protection and reliable performance of LED components. Additionally, optical-grade silicones’ ability to shape and control light distribution enhances the efficiency and visual appeal of LED lighting fixtures, making them an indispensable part of modern lighting technology.
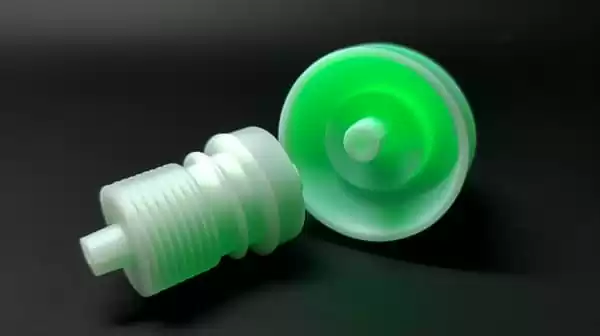
Conclusion
In conclusion, silicone rubber encapsulation plays a crucial role in ensuring the longevity, efficiency, and reliability of LED components. The unique properties of silicone make it an ideal material for LED encapsulation, providing a protective barrier that safeguards LED chips, wire bonds, and other electronic elements from environmental stresses and contaminants.
The optical clarity of silicone rubber enables efficient light transmission, maximizing the brightness and clarity of LED output. This property is particularly essential for LEDs used in various lighting applications, where optimal illumination is of paramount importance.
Silicone rubber’s flexibility and resilience protect LED components from mechanical stress and vibrations, enhancing their durability and reliability in diverse operating conditions. Its thermal stability ensures that the encapsulated LEDs can operate optimally, even in environments with elevated temperatures, contributing to their long lifespan and consistent performance.
Furthermore, silicone rubber’s resistance to moisture, UV radiation, and environmental elements ensures that LED components remain protected and functional in outdoor and harsh environment applications. The low volatile content of high-quality silicone materials minimizes the risk of outgassing, enhancing the LED’s performance and optical clarity over time.
The role of optical-grade silicones in creating optical lenses and, light guides, and light pipes cannot be understated. These components are instrumental in directing and distributing light effectively, achieving optimal light control and uniform illumination. The use of optical-grade silicones ensures high light transmittance, efficient light distribution, and optimum color accuracy, making LED lighting fixtures not only energy-efficient but also visually appealing.
In shaping the future of LED lighting, silicone rubber will continue to be a driving force behind innovation and advancements in LED technology. As the demand for energy-efficient and sustainable lighting solutions grows, silicone encapsulation will remain a critical enabler for producing high-performance LED components suitable for diverse applications.
With ongoing research and development, silicone materials are expected to evolve, providing even more advanced solutions for LED encapsulation. Engineers and designers will have the flexibility to create increasingly intricate and custom shapes, further optimizing LED lighting performance.
In conclusion, silicone rubber encapsulation and the use of optical-grade silicones are indispensable in achieving efficient, reliable, and visually appealing LED lighting solutions. As technology continues to advance, silicone’s role in the LED industry will remain pivotal, contributing to a brighter and more sustainable future for lighting applications worldwide.