Introduction
Compression molding is a vital manufacturing process with a profound impact on various industries. This article delves into the world of compression molding, exploring its significance, challenges, and the critical role played by simulation software in overcoming these hurdles.
Compression molding is a widely used manufacturing technique employed to craft complex components from a multitude of materials, including plastics, composites, and rubber. This process holds immense significance due to its ability to yield high-quality parts with precision, making it indispensable across industries such as automotive, aerospace, and consumer goods.
While compression molding offers numerous advantages, it is not without its complexities and challenges. Achieving optimal results in compression molding requires a delicate balance of parameters, including temperature, pressure, material properties, and compression molding fundamentals and design. The interplay of these factors can be intricate, leading to issues such as voids, warping, and inconsistent material flow. These challenges necessitate innovative solutions to enhance product quality, reduce waste, and optimize production.
This is where simulation software steps onto the stage. Simulation software has emerged as a powerful tool that empowers manufacturers to tackle the intricacies of compression molding head-on. By creating virtual models and conducting compression mold filling simulation , manufacturers can predict outcomes, optimize parameters, and identify potential defects— all without the need for costly physical prototypes. The significance of finite element simulation software in addressing the complexities of compression molding cannot be overstated, as it plays a pivotal role in driving efficiency, improving quality, and ultimately, shaping the future of manufacturing.
In the subsequent sections, we will delve deeper into the compression molding process, explore the ways in which simulation software can be leveraged effectively, and provide practical insights for optimizing compression molding results.
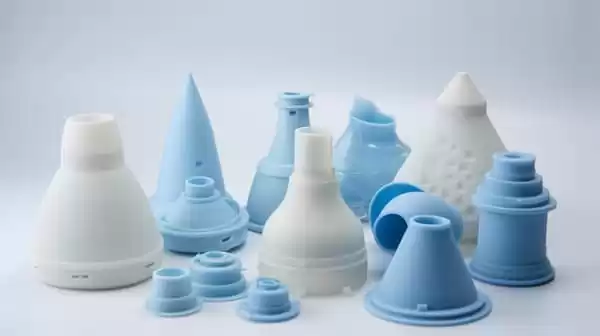
II. Understanding Compression Molding
Compression molding is a manufacturing process that involves several distinct steps and a variety of critical parameters. In this section, we will break down the basics of the compression molding process and shed light on the key parameters and variables that significantly impact the results.
The Basic Steps of Compression Molding
1. Preparation:
The compression molding process begins with the preparation of raw material, which is typically in the form of granules or preforms. This material is loaded into a mold cavity, which is a precisely designed space that determines the final shape of the product.
2. Heating:
Once the mold cavity is loaded with material, it is closed, and heat is applied to the material. The heat softens the material, making it more malleable and ready for molding.
3. Compression:
After reaching the desired temperature, pressure is applied to the material. This compression forces the material to fill the mold cavity completely, taking on the shape of the mold.
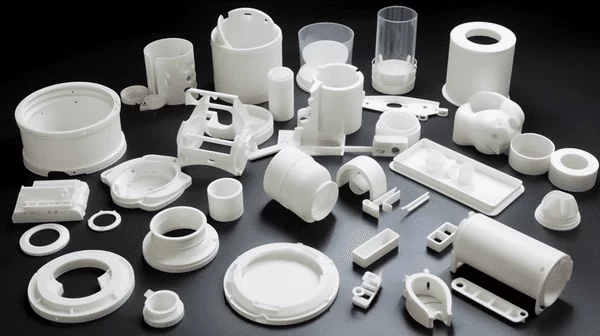
4. Cooling:
Following the compression phase, the mold is cooled to solidify the material. The cooling time is carefully controlled to ensure that the material retains its shape and structural integrity.
5. Ejection:
Once the material has sufficiently cooled and solidified, the final product is ejected from the mold. The product is then ready for further processing or use.
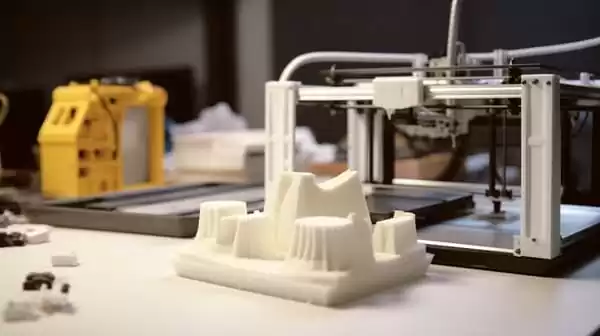
Key Parameters and Variables in Compression Molding
Achieving optimal results in compression molding hinges on a careful balance of several critical parameters and variables, including:
Temperature: The temperature at which the material is heated plays a fundamental role in its behavior during injection compression molding process. It affects the material’s flow characteristics, curing, and overall performance.
Pressure: The application of pressure is necessary to ensure that the material fills the mold cavity completely. Proper pressure control prevents defects and ensures uniformity of mold filling.
Time: The duration of each phase of the molding process, including heating, compression, and cooling, directly impacts the final product’s quality and properties.
Material Properties: Material characteristics, such as viscosity, melt flow rate, and curing behavior, are essential considerations in compression molding. The choice of material greatly influences the molding process and the quality of the end product.
Mold Design: The geometry fiber orientation of the mold cavity, as well as features like vents and runners, significantly affect material flow and the final part’s structure.
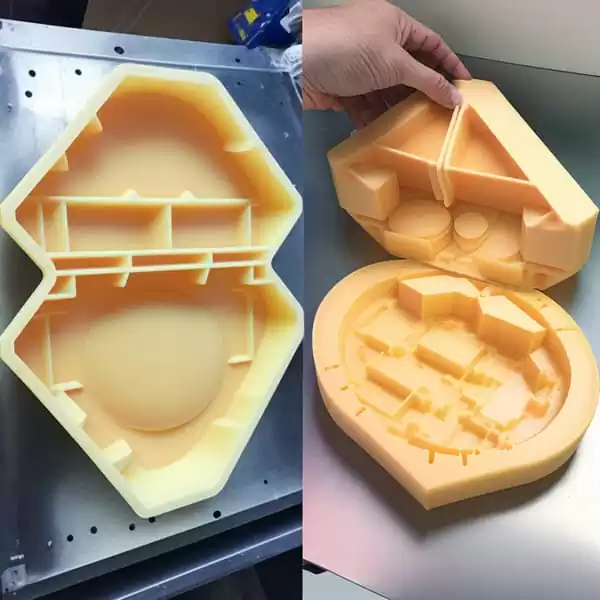
Cooling Rate: The rate at which the top sheet molding compound is cooled after compression impacts the material’s crystallization and, subsequently, its mechanical properties.
In the next section, we will explore how simulation software can be leveraged to optimize these parameters and variables, ultimately leading to improved compression molding results.
III. Role of Simulation Software
Simulation software is a game-changer in the realm of compression molding. In this section, we’ll introduce the concept of simulation software in the context of compression molding, highlighting how it serves as a powerful tool for predicting outcomes, optimizing process parameters, reducing defects, designing molds, enhancing material selection, and ultimately saving time and valuable resources.
Introducing Simulation Software
Simulation software, in the context of compression molding, refers to advanced computer-based tools that enable manufacturers to create virtual models of the entire molding process. These virtual models mimic real-world conditions, allowing engineers and manufacturers to gain valuable insights into how different parameters and variables will affect the final product. Essentially, it’s a digital sandbox where experimentation occurs without the need for physical prototypes.
Predicting Outcomes with Precision
One of the most significant advantages of simulation software in compression molding is its ability to predict outcomes with precision. Engineers can input specific parameters, such as temperature, pressure, and material properties, into the simulation. The software then calculates how these parameters will interact, providing a clear picture of what to expect during actual production. This predictive capability empowers manufacturers to fine-tune their processes for optimal results.
Optimizing Process Parameters
Simulation software doesn’t stop at prediction; it also excels in optimization. By running simulations with various parameter combinations, manufacturers can determine the ideal settings for their compression molding process. For example, they can identify the optimal temperature-pressure combination that results in reduced cycle times, lower production costs, and improved product quality. This optimization is a crucial step in achieving the best possible compression molding process simulation results.
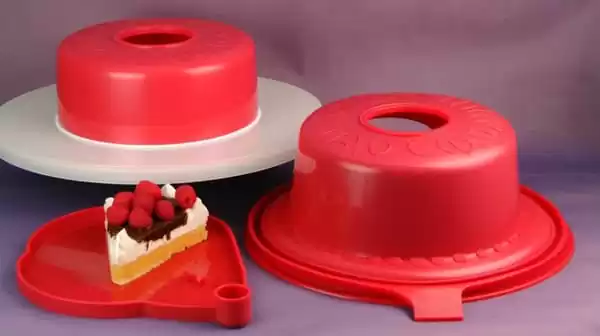
Defect Reduction and Quality Enhancement
In the quest for excellence, simulation software serves as a powerful tool for defect reduction. By simulating the molding process, manufacturers can identify potential defects such as voids, warping, or issues with material flow before they occur in real-world production. Armed with this knowledge, adjustments can be made to the process, effectively reducing defects and enhancing the overall quality of the final product.
Designing Efficient Molds
Mold design is a critical aspect of compression molding, and simulation software significantly aids in this area. Engineers can use the software to design molds with intricate geometries that are challenging to achieve through trial and error alone. The software ensures that molds are efficient and capable of producing high-quality parts consistently.
Enhancing Material Selection
Simulation software allows manufacturers to evaluate how different materials will behave during compression molding. This is particularly valuable when dealing with advanced materials such as fiber-reinforced composites. By simulating different material options, manufacturers can make informed decisions about which material is best suited for a specific application, ensuring optimal performance.
Saving Time and Resources
Perhaps one of the most compelling aspects of simulation software is its ability to save both time and resources. Traditional trial-and-error methods can be costly and time-consuming, involving multiple physical prototypes and iterations. Simulation software eliminates much of this trial-and-error by enabling engineers to refine processes digitally before committing to physical production.
In the next section, we will delve into the practical steps manufacturers can take to effectively harness the power of simulation software in the compression molding process.
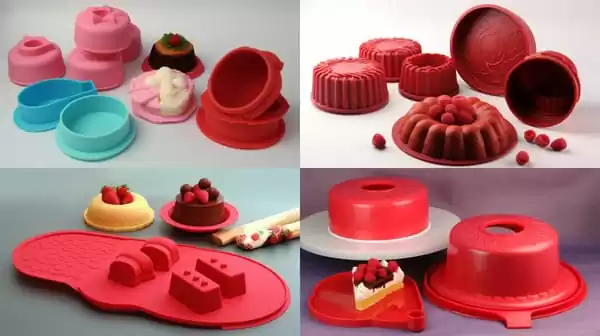
IV. Steps to Using Simulation Software Effectively
Utilizing simulation software effectively in compression molding requires a systematic approach. Manufacturers can follow a step-by-step guide to maximize the benefits of this powerful tool. Here’s a comprehensive outline of the key steps involved:
1. Data Collection
Effective simulation begins with robust data collection. Manufacturers should gather all relevant data, including:
- Material Properties: Comprehensive information about the material being used, such as its viscosity, melt flow rate, thermal conductivity, and curing behavior.
- Mold Specifications: Detailed specifications of the mold, including dimensions, geometry, and venting details.
- Process Parameters: Accurate data on process parameters such as temperature, pressure, and cycle times.
- Historical Data: Any past production data or records of defects that can inform the simulation process.
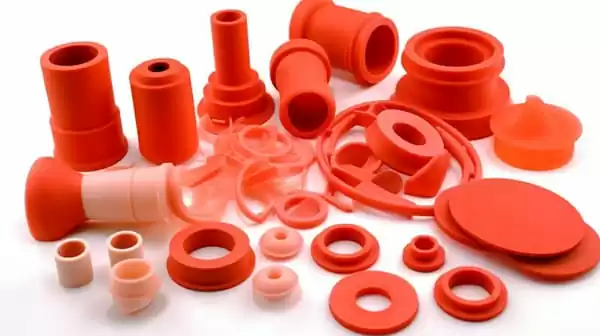
2. Model Creation
With data in hand, the next step is to create a virtual model of the compression molding process. This involves:
- Geometry Creation: Building a 3D representation of the mold and material within the simulation software.
- Parameter Input: Inputting all gathered data, including material properties and process parameters, into the simulation model.
- Boundary Conditions: Defining boundary conditions, such as initial temperatures and pressures.
3. Simulation
Once the model is prepared, simulation software is employed to run virtual compression molding processes. During this phase:
- Simulate the Process: The software conducts simulations based on the defined model, replicating the actual compression molding process.
- Monitor Behavior: Engineers can monitor how the material flows, how pressure is distributed, and how temperature changes within the virtual mold.
4. Analysis
After simulation runs are complete, it’s time for in-depth analysis:
- Defect Identification: Examine the simulation results to identify potential defects or issues in the process. This may include voids, warping, or inconsistent material flow.
- Mechanical Properties: Analyze the predicted mechanical properties of the final product, such as strength, stiffness, and resilience.
- Material Behavior: Understand how the material behaves under different conditions and pressures.
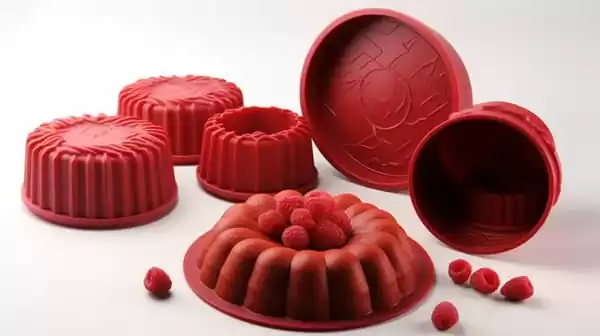
5. Optimization
With a clear understanding of the simulation outcomes and identified areas for improvement, manufacturers can proceed with optimization:
- Parameter Adjustments: Modify process parameters, such as temperature, pressure, or cycle time, to optimize the compression molding process.
- Material Selection: Based on simulation results, consider different materials or material blends that may enhance the final product’s properties.
- Mold Design: Adjust the mold design to improve material flow and minimize defects.
6. Validation
Validation is a crucial step to ensure that the simulation results align with real-world outcomes:
- Compare with Real-World Data: Validate the simulation results by comparing them with actual production data and physical prototypes.
- Iterate if Necessary: If disparities are identified, make necessary adjustments to the simulation model and run additional tests until the results match real-world performance.
7. Implementation
Finally, implement the optimized process based on the simulation findings:
- Process Adjustment: Implement the revised process parameters, mold designs, or material selections in actual production.
- Continuous Monitoring: Continuously monitor production to ensure that the improvements achieved through simulation are sustained.
- Feedback Loop: Establish a feedback loop where data from real-world production is used to further refine and improve the simulation model for future use.
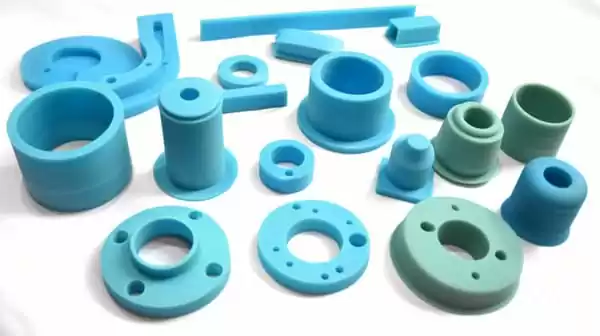
Following these steps systematically empowers manufacturers to harness the full potential of simulation software in compression molding, leading to enhanced product quality, reduced defects, and more efficient production processes.
IV. What Is Moldflow Simulation?
In the intricate world of the plastics industry, Moldflow simulation emerges as a specialized and indispensable tool. This section will define and explain Moldflow simulation, shedding light on its role in comprehending material flow and distribution within molds.
Defining Moldflow Simulation
Moldflow simulation is a highly specialized software tool employed within the plastics industry. Its primary function is to create virtual representations of the entire injection molding process, enabling manufacturers to gain a profound understanding of how molten plastic material flows and distributes within molds. This tool serves as a virtual laboratory, providing insights into the complex behavior of materials during the molding process.
Understanding Material Flow and Distribution
Moldflow simulation excels in its ability to simulate and analyze material flow and distribution with a high degree of precision. Here’s how it achieves this:
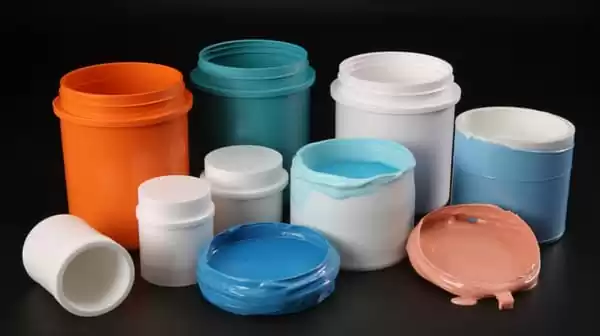
- Material Behavior: Moldflow simulation begins by considering the properties of the plastic material being used. This includes aspects such as melt viscosity, temperature-dependent behavior, and rheological characteristics.
- Geometry Analysis: The software then takes into account the geometry of the mold cavity, including its intricate features, gates, runners, and cooling channels. This analysis is crucial in understanding how material will flow within the mold.
- Injection Simulation: The heart of Moldflow simulation lies in its ability to simulate the injection phase. It predicts how the molten plastic material will enter the mold, how it will fill every nook and cranny, and how pressure will be distributed.
- Flow Visualization: Through the simulation, Moldflow generates visual representations of the material flow. This can include flow fronts, pressure profiles, and temperature gradients, offering engineers and manufacturers a clear picture of what transpires inside the mold.
- Defect Identification: Moldflow simulation is also proficient in identifying potential defects that may occur during the injection molding process. This includes issues like air traps, weld lines, sink marks, and incomplete filling.
Role in Mold Design and Optimization
Moldflow simulation isn’t just about understanding the material flow; it’s also instrumental in designing and optimizing molds. Here’s how:
- Mold Design: Engineers can use Moldflow simulation to fine-tune mold designs, ensuring that material flow is uniform and that defects are minimized. This can involve modifying gate locations, adjusting runner systems, and optimizing cooling strategies.
- Material Selection: The simulation allows for the evaluation of different materials and their behavior within the mold. Manufacturers can choose the most suitable material based on simulation results.
- Optimization: Moldflow simulation aids in optimizing process parameters, such as injection speed, melt temperature, and cooling rate, to achieve the best possible molding results.
In summary, Moldflow simulation is a specialized software tool designed for the plastics industry. It plays a pivotal role in understanding how molten plastic material flows and distributes within molds during the injection molding process. By simulating material behavior, mold geometry, and the injection phase, Moldflow provides invaluable insights into the complex world of plastics molding. It not only aids in defect identification but also guides mold design and process optimization, ultimately leading to more efficient and higher-quality plastic components.
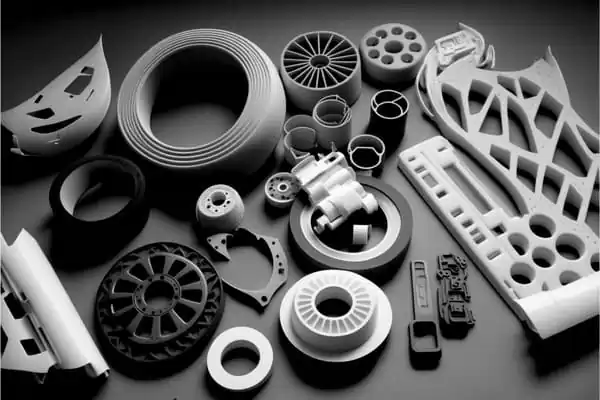
V. Controlling Parameters in Compression Molding Process
The success of the compression molding process hinges on careful control of various parameters and variables. In this section, we will list and explain the controlling parameters that play a pivotal role in achieving optimal compression molding results:
1. Temperature:
- Explanation: Temperature control is fundamental in compression molding. It influences material behavior by affecting its viscosity, melt flow, and curing properties. The precise temperature profile during the heating and cooling phases is critical for product quality.
2. Pressure:
- Explanation: Pressure is another key parameter in compression molding. Properly controlled pressure ensures uniform material distribution, minimizes defects like voids or warping, and compacts the material into the desired shape within the mold cavity.
3. Time:
- Explanation: Time is a critical parameter that governs the duration of each phase of the compression molding process. Careful timing is essential to achieve the desired material cure, cooling, and overall process efficiency.
4. Material Properties:
- Explanation: The properties of the material being molded significantly impact the compression molding process. These properties include viscosity, melt flow rate, thermal conductivity, curing behavior, and even the material’s rheological characteristics. Understanding and optimizing these material properties are essential for successful molding.
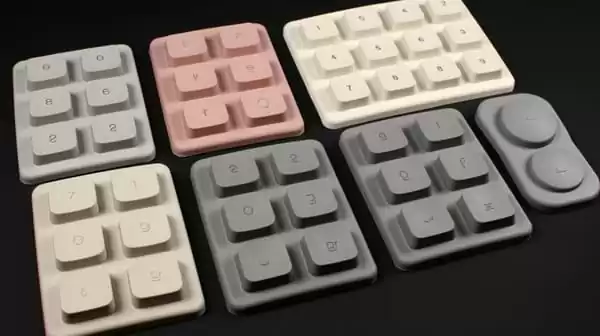
5. Mold Design:
- Explanation: The geometry of the mold cavity and other features like vents, runners, and cooling channels have a profound impact on material flow, distribution, and final part quality. A well-designed mold ensures efficient material compaction and minimizes defects.
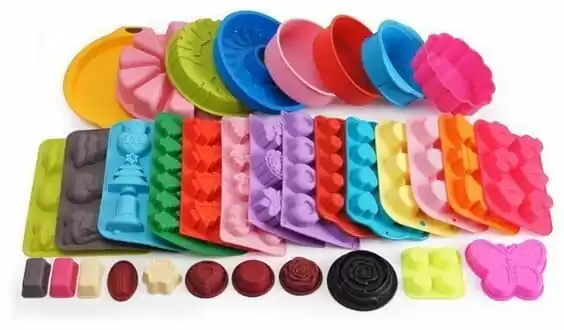
6. Pressure Distribution:
- Explanation: Not only is the overall pressure crucial, but also the distribution of pressure across the mold surface. Even pressure distribution ensures consistent material compaction and minimizes defects like uneven thickness or voids in the final product.
7. Cooling Rate:
- Explanation: The rate at which the mold is cooled after compression significantly affects the material’s crystallization and, consequently, its mechanical properties. Precise cooling rate control is essential for achieving the desired part properties.
8. Mold Surface Temperature:
- Explanation: Controlling the temperature of the mold surface is vital to ensure proper material cure and release from the mold. Mold surface temperature impacts the material’s behavior during both the heating and cooling phases.
9. Material Flow Analysis:
- Explanation: Understanding how material flows within the mold is essential for controlling parameters like pressure and temperature. Analyzing material flow can help identify areas of concern and optimize the molding process.
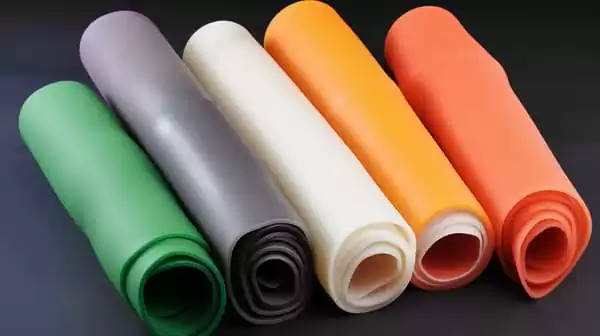
10. Venting and Air Evacuation:
- Explanation: Proper venting and air evacuation are necessary to prevent the entrapment of air or gas within the mold. Effective venting ensures complete material compaction and minimizes defects.
These controlling parameters collectively define the conditions under which compression molding takes place. The precise management of these parameters is critical to achieving consistent, high-quality results and ensuring the efficient production of molded components. Manufacturers must carefully consider and optimize each parameter to meet their specific product requirements and quality standards.
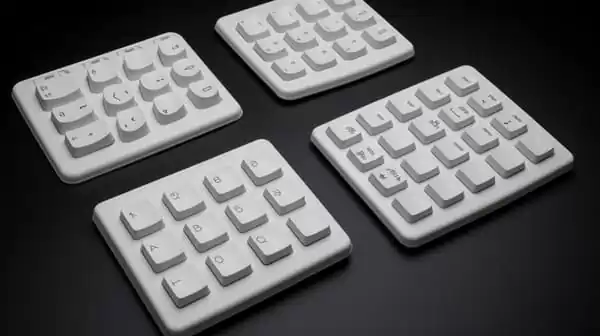
Conclusion
In conclusion, this article has explored the realm of compression molding, highlighting its significance and the intricacies involved in achieving optimal results. We have emphasized the pivotal role of simulation software in addressing these challenges and optimizing the compression molding process. Here are the key takeaways:
- Significance of Compression Molding: Compression molding is a crucial manufacturing process used across industries, enabling the creation of complex components with precision and efficiency.
- Challenges in Compression Molding: Achieving optimal compression molding results requires precise control of parameters such as temperature, pressure, time, material properties, and mold design. Complexities in material behavior and mold design can lead to defects and inefficiencies.
- The Power of Simulation Software: Simulation software is a game-changer in compression molding. It allows manufacturers to create virtual models of the process, predict outcomes, optimize parameters, and reduce defects before physical production begins.
- Steps to Effective Simulation Use: Manufacturers can follow a structured approach, including data collection, model creation, simulation, analysis, optimization, validation, and implementation, to effectively utilize simulation software.
- Moldflow Simulation: Moldflow simulation, a specialized tool for the plastics industry, plays a crucial role in understanding material flow and distribution within molds. It aids in defect identification, mold design, material selection, and process optimization.
- Controlling Parameters: Key controlling parameters in compression molding include temperature, pressure, time, material properties, mold design, pressure distribution, cooling rate, mold surface temperature, material flow analysis, and venting. Precise control of these parameters is essential for consistent and high-quality results.
- The Future of Molding Simulation: The article concludes by underlining the significance of simulation software in achieving consistent and superior compression molding results. It is through the digital realm of simulation that manufacturers can innovate, optimize, and adapt to the evolving landscape of mechanical engineering and polymer processing. As technology advances, we can expect simulation tools to become even more integral in shaping the future of manufacturing.
In the ever-evolving world of mechanical engineering and polymer processing, simulation software is the compass guiding us towards greater efficiency, innovation, and excellence in compression molding. With each simulation, we inch closer to perfecting the art of crafting precision components while saving valuable time and resources. As we look ahead, we anticipate simulation software to continue its transformative role in pushing the boundaries of what is possible in manufacturing, ensuring that compression molding remains a cornerstone of modern production.