Silicone rubber: the material that creates modern wonders. Electronics, as well as many other products, rely on this adaptable polymer. What makes it so impressive? Consider the following special properties: Resistance to chemical corrosion and water damage, thermodynamic stability, non corrosive, flexibility and electrical insulation capabilities.
Silicone rubber is ubiquitous in today’s electronics manufacturing, making it durable and adaptable and used in everything from cell phone casings to medical silicone sealant. But as safety, especially that of consumer product materials, comes under intense scrutiny, can silicone rubber be trusted to protect our electronic equipment or electronic systems, by extension, us from harm?
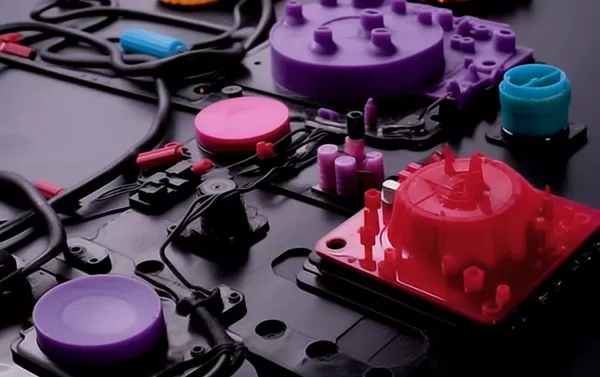
In this article, we’ll delve into the world of silicone rubber and examine its safety record in the electronics industry. We’ll consider key issues such as exposure risk and heat resistance so you have a comprehensive understanding of whether it’s safe enough for your needs.
The Basics of Silicone Rubber in Electronics
Silicone rubber, a synthetic elastomer with a long list of advantageous attributes, is a staple in the electronics industry for several reasons.
1. Heat and Cold Resistance
Silicone rubber has an amazing ability to withstand extreme temperatures, which is why it’s so useful in electronics. Unlike most materials, it doesn’t break down when high temperatures or low temperatures. Silicone materials can operate continuously from -148°F to 482°F (-100°C to 250°C), well beyond what ordinary equipment can withstand! This makes silicone not only ideal for use in insulating components inside devices that themselves generate large amounts of heat, but also for protecting circuits outdoors in the winter or even in space where there is no atmosphere at all.
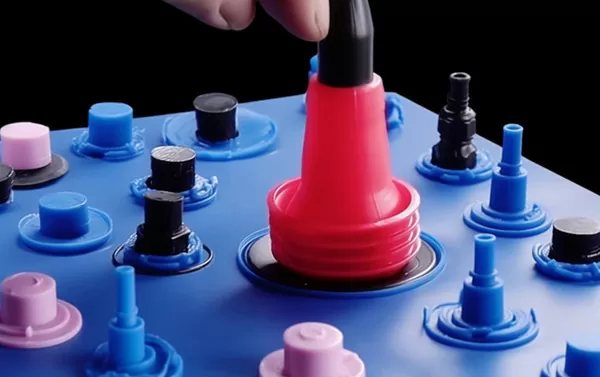
2. Chemical and Environmental Resistance
Because silicone resists chemicals well and doesn’t easily react with other substances, electronics coated or encapsulated in silicone can better withstand exposure to harsh environments or corrosive many materials. Examples include corrosive elements present in manufacturing environments or occurring naturally in the form of moisture or dust.
3. Electrical Insulation
Silicone rubber is known for its high dielectric strength, which means it effectively blocks the passage of electrical current. This makes the material an excellent insulator, useful in situations where electronics grade may become wet or may short-circuit when in contact with metals and other conductors.
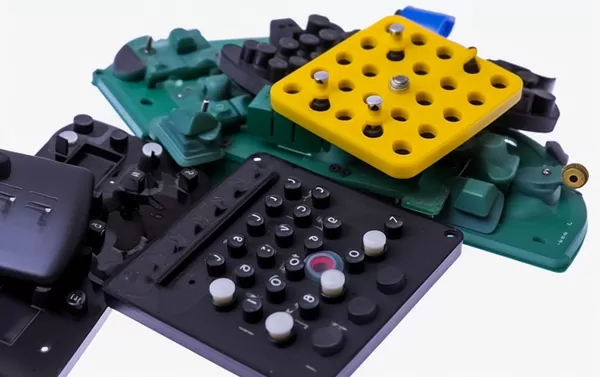
The combination of these properties makes silicone rubber the first choice for protecting sensitive electronic components as it protects them from internal and external hazards, ensuring their longevity and performance.
The Versatility of Silicone Rubber in Electronics
The appeal of silicone rubber in the electronic applications industry is obvious, it can withstand high and low temperatures, does not support microbial growth, and is an excellent insulator. These properties make it ideal for products such as keyboards, gaskets and O-rings that are frequently exposed or subject to severe temperature swings. It also has excellent dielectric properties, which is why cable terminations and circuit insulation are another common application area.
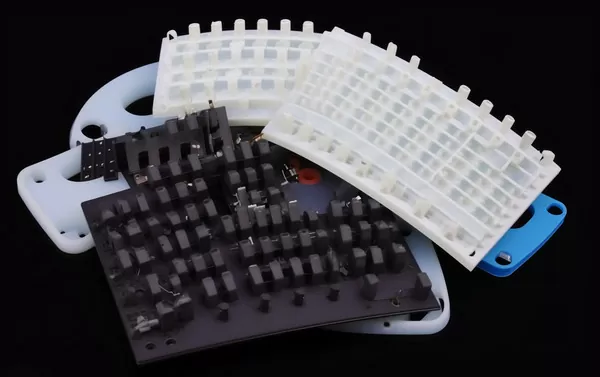
But there’s more at stake here than meets the eye, and since these materials have such a wide range of applications, we also have to consider what happens from a safety perspective, especially in products intended for consumer use.
When Can Silicone Pose a Problem?
Despite its many strengths, silicone rubber can pose potential issues in some scenarios.
1. Manufacturing Residues
There may be some residues that cannot be removed during the production process of silicone rubber products, and these residues may cause risks in the final use of the product. Safeguards such as strict quality control inspections and thorough cleaning can reduce the chance of residual contaminants after manufacturing contaminating subsequent products.
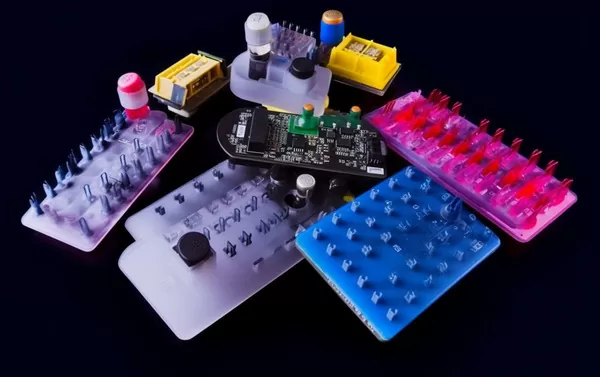
2. Compatibility with Other Materials
Designers and engineers need to be aware that silicone rubber does not bond well with other materials due to its non-adhesive properties, so this must be addressed during assembly or the product may fail later.
3. Thermal Conductivity
The thermal insulation capabilities of silicone are generally beneficial, but this feature may have a negative impact on devices that need to dissipate their own heat. Designers can overcome such issues by designing appropriate thermal interfaces into the system (or package).
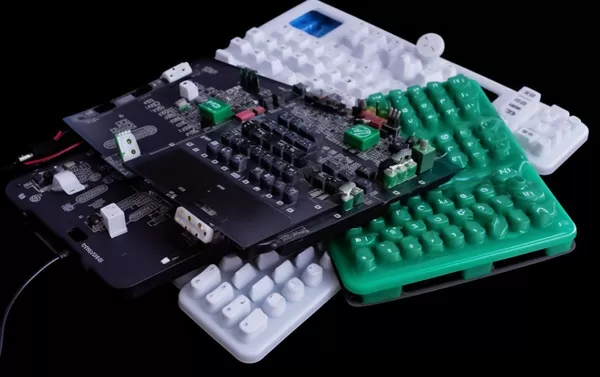
While these challenges are not inherent to silicone rubber itself, they emphasize the need for careful application and consideration of the material’s properties within the context of the specific electronic device in which it is used.
Standards and Compliance in Silicone Rubber Production
Manufacturers of silicone rubber compounds are acutely aware of how stringent the material requirements for electronics are. If a substance is to be considered suitable for use in electrical applications, it absolutely must meet very strict specifications set by two organizations: the International Electrotechnical Commission (IEC) and Underwriters Laboratories (UL).
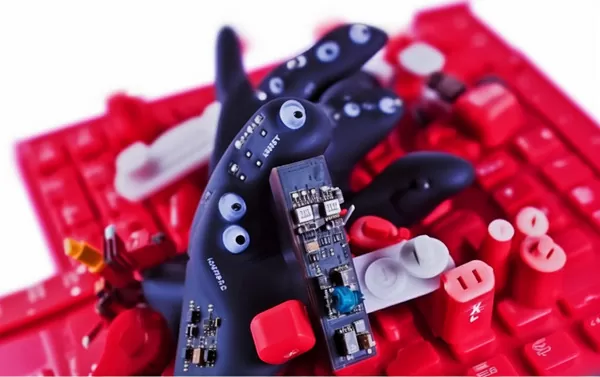
There is no room for negotiation in meeting these standards, as doing so is directly related to the reliability and safety of the final product. Such strict supervision and control also means people can be confident in the safe use of silicone rubber electronics.
Concerns and Controversy
Although silicone rubber meets industry standards, some consumer groups are still concerned. One area of focus is silicones, which are byproducts of silicone manufacturing and have attracted attention because of their potential endocrine-disrupting properties.
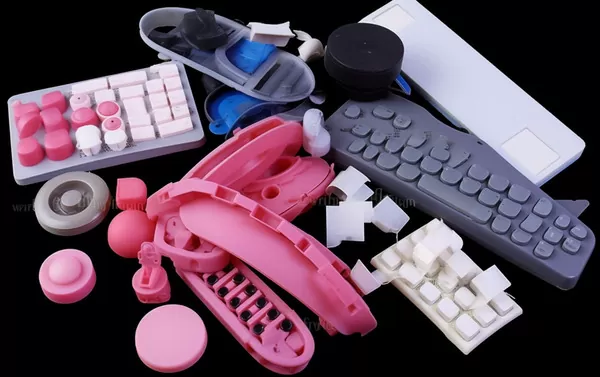
The debate stems from ongoing research into silicone products, which suggests these substances may mimic estrogen and may have health effects, particularly as they may break down from the product during use. Some tests have shown this Situations may happen.
A New Generation of Materials
There are growing concerns about certain properties of silicone rubber, which has caught the attention of the industry. This has sparked a movement among professionals in the field who hope to find new substances that are similar enough to replace everything existing substances do while being better for people and the planet. One such material that is currently gaining popularity are bio-based elastomeric materials, which have the potential to replace various uses in which we currently rely heavily on silicones. If successful, it could provide an opportunity for electronics manufacturers to not only reduce waste, but even address safety issues that electronics manufacturers often consider.
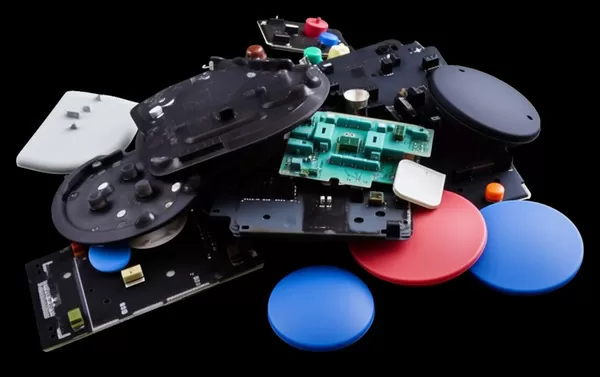
Silicone Rubber Safety Tips for Consumers
When it comes to the safety of silicone rubber, most concerns focus on consumer products such as cookware or baby products. Fortunately, there are ways to reduce the risks that may come with using these products:
From Reputable Manufacturers: Stick to trusted brands that use safe materials to build their products.
Use as Intended: Always follow the directions or instructions for a product carefully so that nothing bad happens because someone doesn’t understand the usage scenario. Extreme temperatures, microwave use and daily wear and tear can cause material degradation and potential leaching.
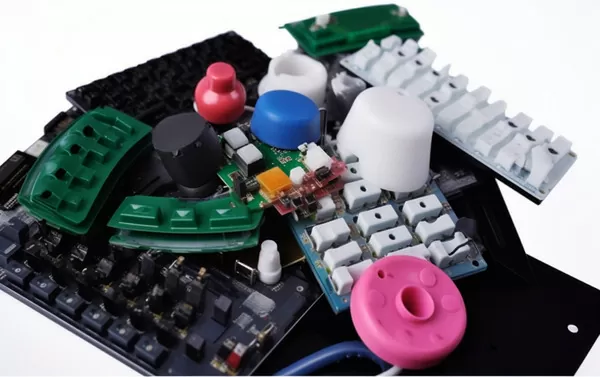
Regular Inspections: Regularly inspect the silicone parts of electronic devices and cables for any signs of accidental damage or wear.
The Balanced Perspective on Silicone Safety
In order to properly evaluate the safety of silicone rubber (or any substance), it is important to maintain an objective and balanced perspective. Silicone rubber does meet strict safety and compliance requirements as long as it is used as intended. However, there are subtle issues worth considering when we decide how best to use and oversee this remarkable substance.
Electronics manufacturers must keep up with the latest research to understand the potential risks involved and be prepared to move to new materials if concerns escalate. For consumers, it requires informed use and consideration of safe and sustainable alternatives.
Conclusion
Today we explore the safety of silicone rubber in electronic applications, focusing on various types such as neutral cure silicones, neatral cure silicones, RTV silicone, and oxime cure, and their potential interaction with substances like acetic acid.
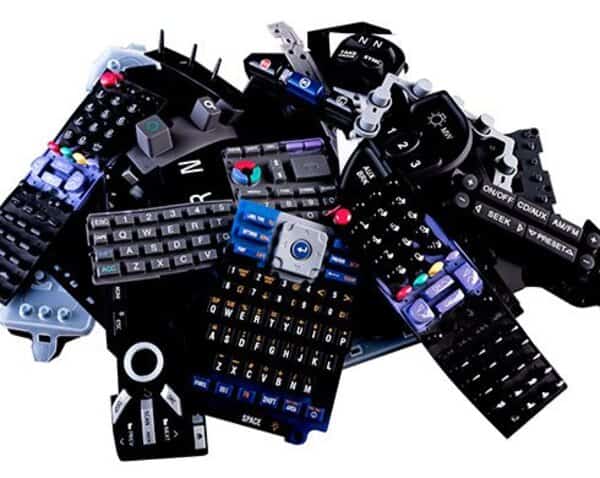
Silicone rubber is safe if used correctly and subject to valid quality testing and certification. Materials scientists, regulators, manufacturers and consumers must work together to manage risks. As long as we are careful, we can safely use silicone rubber in electronic products and enjoy its superior properties.
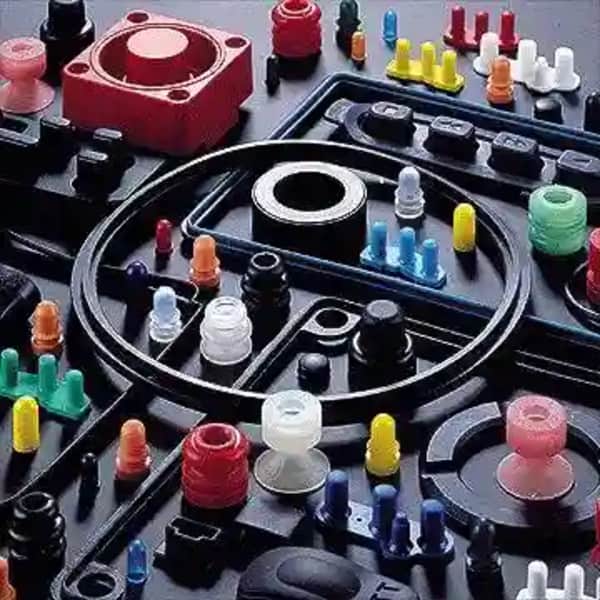
Overall, what matters is not the substance itself, but how little we know about it, and how often the rules are broken or precautions ignored, and this applies to products from silicone to anything. With silicones, as with many other materials, it depends on responsible use and a commitment to ongoing safety evaluations as we learn more about the materials we use.