Introduction
Manufacturing industries are constantly innovating to produce high-quality parts with precision and complexity, and liquid silicone rubber molding has emerged as an innovative solution that provides highly efficient production of precision parts with complex geometries from liquid silicone rubber material. LSR molding is one such innovative manufacturing technique which has gained significant traction.
LSR molding has dramatically transformed manufacturing environments across industries like automotive, medical and electronics. Thanks to its superior capabilities conventional insulating material, this technique offers many advantages over traditional molding techniques – becoming the go-to option when producing parts with intricate designs, tight tolerances or reliable performance demands.
LSR molding stands out in its ability to meet the increasing demand for highly precise and intricately designed components, with applications across industries from medical devices and automotive parts to electronics and consumer products. LSR injection molding’s versatility makes it an appealing solution for manufacturers seeking innovative ways to achieve superior quality and functionality.
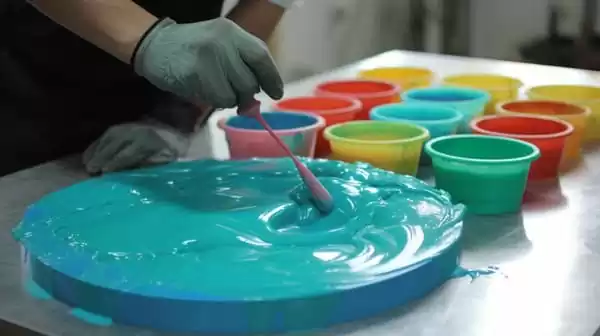
As we progress through these subsequent sections, we will dive deep into LSR molding’s details – its process, advantages, and impact across various industries. Through an in-depth knowledge of this type of manufacturing technique we can fully appreciate its transformative role within manufacturing as well as its incredible future potential for advancements.
II. What is Liquid Silicone Rubber (LSR)?
Liquid silicone rubber (LSR) is a versatile material widely used in manufacturing due to its unique properties and capabilities. It is a type of silicone rubber that exists in a liquid state before undergoing a curing process. LSR is composed of two main components: a liquid silicone base and a catalyst, often a platinum catalyst.
The process of transforming liquid silicone rubber into a solid elastomer involves cross-linking. When the liquid silicone rubber properties the base and the catalyst are mixed together, a chemical reaction is triggered, leading to the cross-linking of polymer chains within the material. This cross-linking process forms a three-dimensional network structure, transforming the LSR from a liquid to a solid elastomer.
One of the remarkable aspects of LSR is its excellent chemical resistance. It can withstand exposure to various chemicals, such as acids, bases, solvents, and oils, without experiencing significant degradation or loss of properties. This chemical resistance makes LSR suitable for applications where contact with aggressive substances is inevitable.
Additionally, LSR exhibits exceptional temperature resistance. It can endure extreme temperatures, both high and low, without compromising its mechanical and electrical properties. LSR can withstand heat without melting or deforming, making it ideal for applications exposed to elevated temperatures. Conversely, it remains flexible and resilient in cold environments, ensuring reliable performance in low-temperature conditions.
Furthermore, LSR possesses other advantageous properties, including excellent insulating properties, high tensile strength, and low compression set. Its biocompatibility and hypoallergenic nature make it suitable for medical applications, as it has demonstrated superior compatibility with human tissues and body fluids.
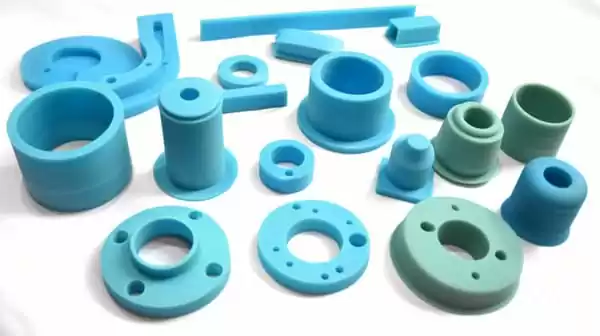
These unique properties of LSR, such as chemical resistance, temperature resistance, and biocompatibility, make it an exceptional material for a wide range of industries. From automotive components and electronics to medical devices and consumer goods, LSR offers a reliable solution for manufacturing high-quality products that can withstand demanding environments and provide long-lasting performance.
III. The LSR Molding Process and Injection Molding process
LSR molding is a highly efficient manufacturing process used to produce precision parts with complex geometries using liquid silicone rubber material. It follows the general principles of injection molding but utilizes liquid silicone rubber instead of traditional plastic materials. Let’s explore the key steps involved in the LSR molding process:
1.Injection:
The first step in the LSR molding process is the injection of liquid silicone rubber into a mold cavity. This step requires the use of specialized injection molding machines designed for LSR. The liquid silicone rubber is prepared by mixing the base material and the catalyst in precise proportions. The mixture is then fed into the injection unit of the molding machine.
During the injection step, the liquid silicone rubber is heated and injected into the mold cavity under high pressure. The injection molding machine precisely controls the injection rate to ensure accurate delivery of the liquid silicone rubber into the mold. The flowability of the LSR allows it to fill intricate features and complex geometries, ensuring the replication of fine details.
2.Curing:
After the injection, the liquid silicone rubber undergoes a curing process. Curing is typically achieved through the application of heat or with the help of a platinum catalyst. Heat-cured LSR molding involves transferring the mold to an oven or heated chamber, where the heat activates the cross-linking reaction within the LSR. Alternatively, platinum-cured LSR utilizes a platinum-based catalyst to initiate the curing process.
The curing temperature and time are carefully controlled to achieve the desired hardness and properties of the final part. This step ensures that the liquid silicone rubber transforms into a solid elastomer, forming the shape of the mold cavity. The heating and curing process may vary depending on the specific LSR material and the requirements of the part being produced.
3.Extraction:
Once the curing process is complete, the mold is opened, and the finished LSR component is extracted. The extraction step involves carefully removing the part from the mold without causing any damage or distortion. The mold’s design may incorporate features such as ejector pins or air blasts to aid in the removal of the finished component.
The extracted LSR component retains the shape and details of the mold cavity, exhibiting high precision and tight tolerances. The combination of accurate injection and controlled curing ensures the production of quality parts with consistent dimensions and surface finish.
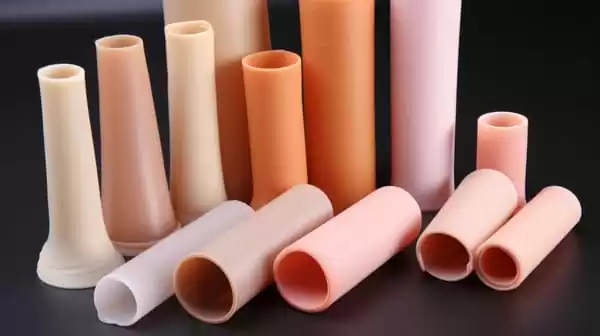
The LSR molding process, with its precise injection control and controlled curing, enables manufacturers to produce intricate parts with complex geometries. The ability to replicate fine details and maintain tight tolerances makes LSR molding a preferred choice for industries that demand high precision, such as medical devices, automotive components, and electronics.
IV. Advantages of Liquid Silicone Rubber (LSR) Molding
Liquid silicone rubber (LSR) molding offers many advantages over other molding processes, making it the go-to choice in various industries.
Let’s examine some key benefits of LSR molding:
Design Flexibility: LSR molding provides manufacturers with exceptional design flexibility, enabling them to craft parts with complex geometries and intricate details. Thanks to its low viscosity, liquid silicone rubber flows smoothly into mold cavities for accurate replication of fine details – offering manufacturers plenty of scope for innovative product designs and creating product opportunities with limitless possibilities for creativity and innovation.
Precision and Tight Tolerances:
LSR molding provides high precision with tight dimensional tolerances to guarantee consistent and reliable quality. The liquid nature of silicone rubber allows it to fill even intricate mold cavities easily, producing parts with exact dimensions and intricate features – which is key when accuracy is of utmost importance.
Chemical Resistance:
LSR materials offer exceptional chemical resistance, making them the perfect choice for applications involving exposure to chemical solutions or body fluids. LSR components remain undamaged after coming in contact with acidic, basic, solvents or oils – ensuring longevity and performance under challenging environments.
Temperature Resistance:
LSR materials provide unparalleled temperature resistance, enabling them to perform reliably even under harsh environmental conditions. At high temperatures they don’t melt, deform, or lose any mechanical and electrical properties – while maintaining flexibility and resilience at low temperatures for use in cold environments. LSR has numerous applications across various industries due to this exceptional temperature resistance.
Biocompatibility:
LSR materials are biocompatible and hypoallergenic, making them an excellent choice for medical and healthcare applications. Their compatibility with human tissues and body fluids reduces risks of adverse reactions or complications and offers safe solutions to meet healthcare industry requirements. LSR components can be utilized in medical devices, implants and drug delivery systems offering reliable healthcare solutions.
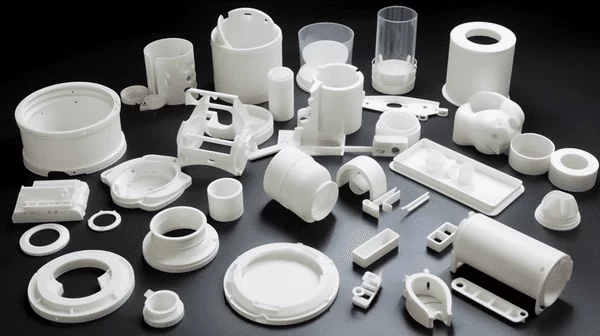
LSR molding’s combination of design flexibility, high precision, chemical resistance, temperature resistance, biocompatibility and temperature resistance make it an extremely valuable process across various industries. Automotive, electronics, consumer goods or medical applications – LSR molding offers manufacturers an innovative means of producing high-quality silicone rubber parts that satisfy stringent specifications with ease.
V. Applications of Liquid Silicone Rubber (LSR) Molding
Liquid silicone rubber (LSR) molding finds extensive application across various industries, thanks to its unique properties and advantages. Let’s explore some industries and products that benefit from LSR molding:
1.Medical Devices:
LSR molding is widely utilized in the medical industry for the production of critical medical devices. It is used to manufacture components such as surgical implants, catheters, respiratory masks, syringe components, and valves. The biocompatibility and hypoallergenic nature of LSR make it ideal for applications involving direct contact with human tissues and body fluids. The high precision and tight tolerances achieved through LSR molding ensure the accuracy and reliability required in medical applications.
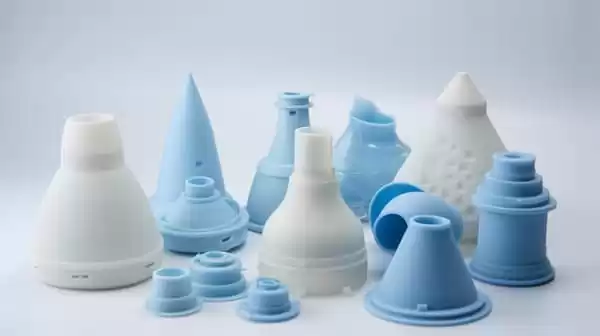
2.Automotive Industry:
LSR molding plays a crucial role in the automotive industry, where precision, durability, and reliability are paramount. It is used for manufacturing components such as gaskets, seals, connectors, keypads, and vibration dampeners. The chemical resistance, temperature resistance, and excellent sealing properties of LSR make it an ideal choice for automotive applications, ensuring longevity and performance in challenging environments.
3.Electronics and Electrical Industry:
LSR molding is employed in the electronics and electrical industry for the production of keypads, insulators, connectors, and seals. The excellent insulating properties of LSR make it suitable for electrical applications where insulation and protection are essential. LSR’s resistance to heat and cold temperatures, as well as its chemical resistance, ensure the reliability and longevity of electronic and electrical components.
4.Consumer Goods:
LSR molding finds application in the manufacturing of consumer goods, including products such as kitchenware, baby products, toys, and wearable devices. The design flexibility of LSR allows for the creation of unique and intricate product designs. LSR’s durability, resistance to chemicals, and temperature resistance contribute to the longevity and functionality of consumer goods.
LSR molding is particularly beneficial for applications that require precise specifications and reliability. Industries such as aerospace, telecommunications, and industrial equipment often rely on LSR molding for critical components that demand strict adherence to specifications and consistent performance over time. LSR’s high precision, tight tolerances, and consistent quality make it a reliable choice for such demanding applications.
In summary, LSR molding finds application in diverse industries and a wide range of products, including medical devices, automotive components, seals, electronics, consumer goods, and more. Its unique properties and advantages make it a preferred choice for applications that demand precision, reliability, and performance under challenging conditions. The versatility and reliability of LSR molding continue to drive innovation and advancements across various industries.
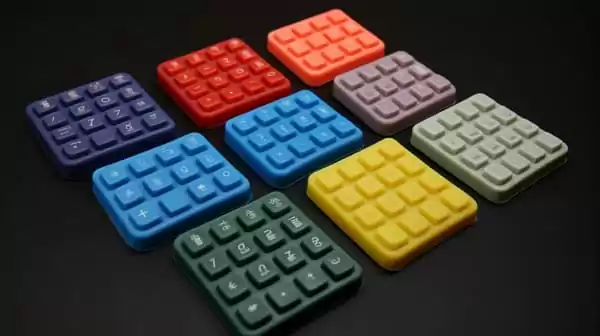
Conclusion
Liquid silicone rubber (LSR) molding is an efficient manufacturing process, enabling precision parts with complex geometries to be molded from liquid silicone rubber material. We have discussed its key aspects and advantages throughout this article, letting us summarize all these points:
LSR is liquid injection molding process that employs liquid silicone rubber material to produce parts with tight tolerances and precise precision. The process entails injecting the liquid silicone rubber into a mold cavity before curing and extracting of the finished part from its final mold cavity.
LSR injection molding has applications across various industries, from medical devices and automotive components to consumer goods and electronics. It’s especially suitable for applications requiring precise specifications and reliable performance, such as medical devices.
LSR molding is an efficient manufacturing process with numerous advantages that should not be underestimated in its role within the manufacturing industry. Thanks to its unique properties and capabilities, LSR molding allows manufacturers to produce high-quality parts that fulfill demanding specifications with ease. As this technology progresses we can expect exciting advancements as this technique grows further.