Introduction:
In the domain of self-fashioned creation and artisanal endeavors, silicone molds have arisen as a pivotal innovation. Celebrated for their pliability, resilience, and non-adhesive attributes, these molds have entrenched themselves as a cornerstone in a plethora of imaginative undertakings. Spanning from enthusiasts to seasoned craftspersons, the application of silicone molds covers a broad spectrum of uses, gaining immense acclaim in contemporary times.
The distinct advantage of silicone molds lies in their astounding adaptability. Be it for the formation of complex resin artworks, fabricating bespoke soaps, or even the culinary arts of chocolate and pastry making, these molds are adept in managing diverse tasks. Their capability to endure extreme thermal conditions and effortlessly disengage various substances positions them as an exemplary selection for both scorching and frigid casting techniques.
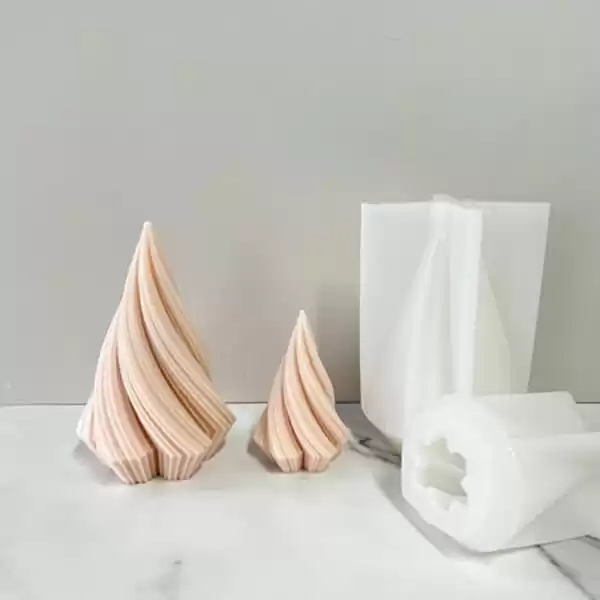
Additionally, the simplicity of this method of fabricating silicone molds domestically has unlocked a universe of creative possibilities. With a handful of components and straightforward procedures, anyone can fashion a tailor-made mold to meet the exigencies of their particular project. This adaptability paves the way for boundless ingenuity, whether it involves duplicating a vintage artifact, devising a novel piece of adornment, or crafting custom cake embellishments.
In part two part of this exposition, we shall delve into how you can exploit the potential of silicone mold for your artistic ventures, elucidating the sequential methodology of constructing your personalized silicone rubber mold. Irrespective of whether you are an experienced creator or a neophyte in the realm of silicone mold making and fabrication, this exploration promises an enlightening and thrilling experience.
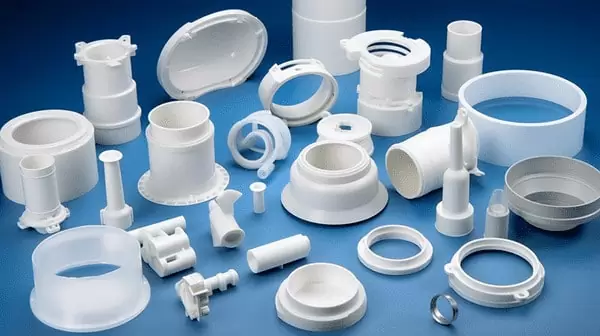
Materials Needed
To initiate your venture in fabricating a silicone rubber mold, it’s imperative to make you to amass all requisite components in advance.
Below is an exhaustive inventory to set you on course:
Bicomponent Silicone Rubber: This constitutes the mold’s primary substance, typically available in the form a dual-component mixture requiring amalgamation.
Demolding Agent: This essential compound ensures that your culminating creation can be effortlessly detached from the mold sans adherence.
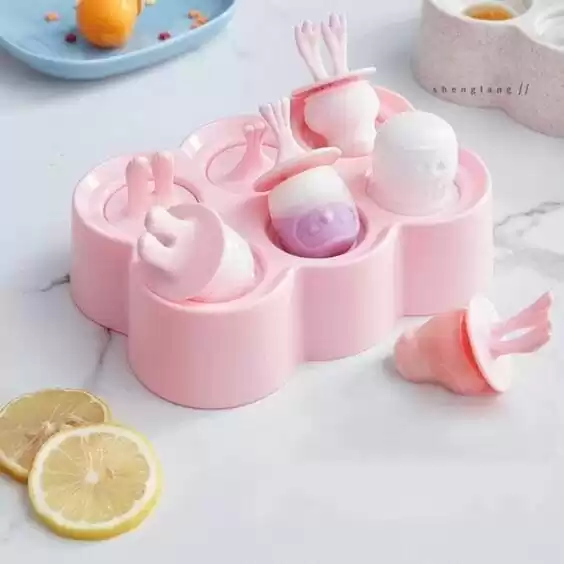
Agitation Implements: A robust blending vessel, coupled with a stirrer or spatula, is necessary for the unification of the liquid silicone rubber elements.
Mold Enclosure: This receptacle, which can be crafted from diverse materials like plastic or timber, houses your masterpiece and the silicone. Its composition hinges on your project’s magnitude and configuration.
Prototype Object: The entity for which you desire to replicate a mold. It can range from a statuette, an ornamental trinket, to a decorative artifact.
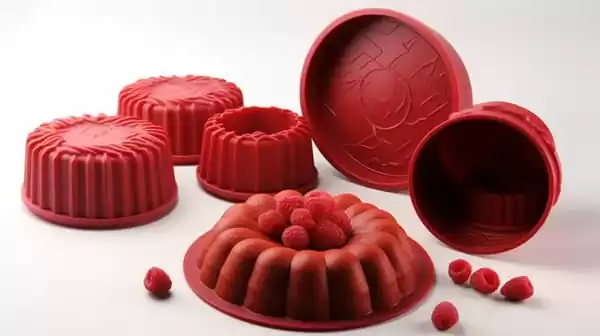
Additional elements that enhance the procedure and guarantee safety include:
Protective Gloves:
Shield your hands from the silicone, a boon particularly if your skin is prone to irritation. Silicone can be cumbersome, and gloves aid in tidying up.
Protective Sheets:
Employ paper or plastic coverings to safeguard your working area against spills and blemishes.
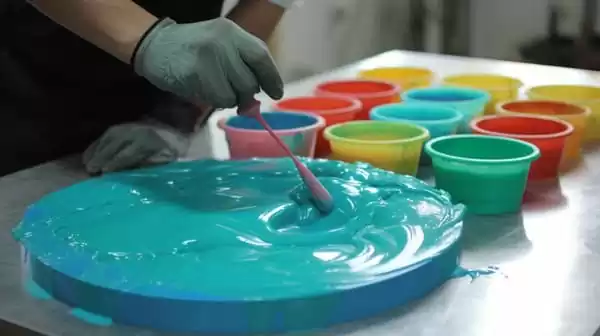
Atomizer:
A tool for evenly dispersing the demolding agent, especially beneficial for intricate or sizeable designs.
Measurement Instruments:
Mold crafting demands precision; thus, possessing exact measuring tools for the silicone constituents is vital for your mold’s excellence.
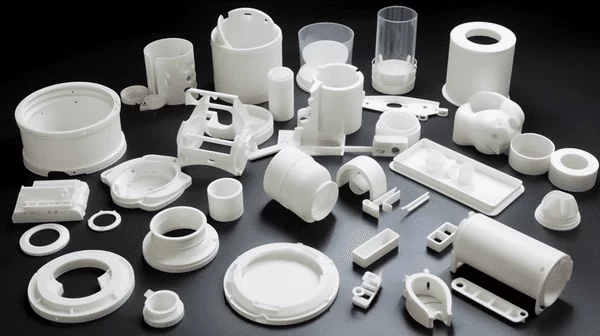
Accumulating these components prior to commencing your endeavor part silicone make will streamline the process and augment its enjoyment. Bear in mind, the caliber and precision of your materials and instruments profoundly influence your silicone mold’s outcome.
Steps for Making a Silicone Rubber Mold
Embarking on the Fabrication of a Silicone Elastomer Impression Initiation with the Principal Entity Decontamination:
Commence with an exhaustive decontamination of the principal entity to eradicate any filth or lubricants. This phase is pivotal for securing an impeccable impression.
Application of Demolding Agent:
Should the principal entity be composed of a porous substance such as terra cotta or timber, the employment of a demolding agent becomes imperative. This aids in the facile liberation of the entity post-impression solidification. Administer the agent uniformly via spraying or brushing.
Formulating the Impression Enclosure Dimensional Assessment and Edifice:
Gauge the proportions of your principal entity and fabricate an enclosure marginally more voluminous. This structure may be crafted from lumber, polymer, or even paperboard for diminutive endeavors. Ascertain the robustness and impermeability of the enclosure.
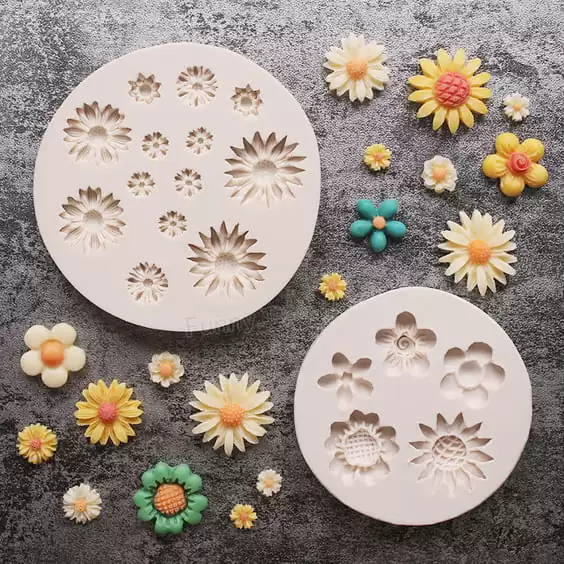
Amalgamating the Silicone Elastomer Adherence to Kit Directives:
Blend the bifurcated components of the silicone elastomer following the directives provided in your kit. Precision in proportions is crucial for the impression’s quality. Stir diligently until a uniform amalgamation is achieved.
Administering the Silicone Methodology:
Introduce the silicone into the enclosure, initiating from one vertex and gradually circumnavigating the entity. Disperse from an elevated position to minimize bubble formation and secure to create a more even surface.
Maturation of the Silicone Duration and Procedure:
Permit the silicone to mature following the manufacturer’s recommendations. The maturation duration can fluctuate, thus consulting the product directives is vital. Refrain from disturbing the impression during this period.
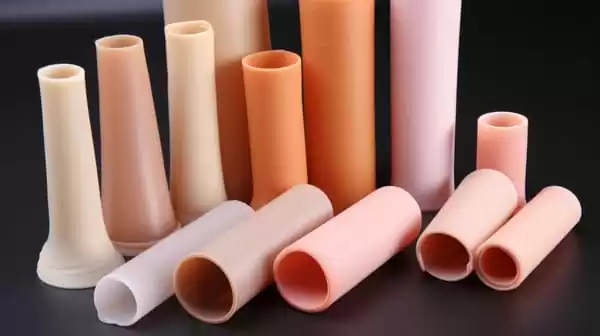
Extraction Ejecting the Silicone Impression:
Subsequent to the full maturation of the silicone, gingerly detach the impression from the enclosure. Thereafter, cautiously extricate the principal entity from the silicone impression.
Refinement Examination and Refinement: Scrutinize the impression’s surface for any flaws. Utilize a precise instrument for modifications or to smoothen the surface, achieving a refined finish.
Utilizations and Recommendations Multifaceted Applications:
Silicone impressions are adaptable for an array of projects, spanning from resin and wax castings to soap creation. They offer versatility and are amenable to repeated usage.
Stratified Techniques:
For intricate impressions, consider a tiered pouring approach. Allow each tier to reach a semi-matured state prior to appending the subsequent, enabling multi-level or chromatic effects.
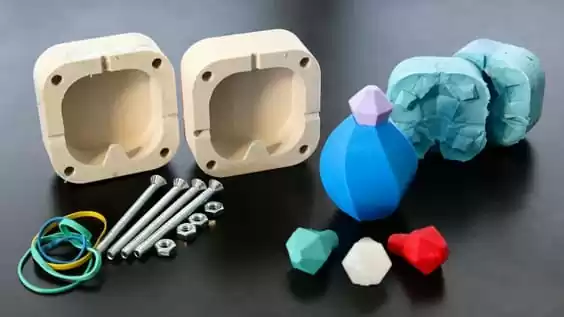
Conclusion
Embarking on the endeavor of fabricating your silicone rubber mold melds artistic flair with technical savoir-faire, unlocking a plethora of avenues in the realms of handiwork and DIY ventures. We’ve delineated the pivotal phases of mold release: priming your archetype, erecting a casting frame, amalgamating and instilling the silicone compound, awaiting its solidification, and ultimately unveiling your brainchild. Each juncture is crucial, shaping the superior caliber of your mold.
Contemplate the allure of crafting silicone casts: their adaptability shines in diverse domains such as clay and resin sculpture, candle fabrication, soap design, or even gastronomic experiments. These molds boast resilience and pliability, vital in actualizing your concepts. Initially, the procedure might appear formidable, yet with each mold you craft, you want to make your prowess and assurance flourish.
We champion your commencement in mold making and fabrication. Delve into varied forms and substances, and embrace errors – they often emerge as paramount educators. Circulate your masterpieces and tales; the artisan community stands as a splendid bastion for encouragement and ingenuity.
Therefore, marshal your resources, gird yourself, and submerge into the silicone molding cosmos. Here, creativity is your sole boundary!