Introduction
Mold design plays a vital role in producing high-quality silicone rubber products. Molds used to shape and form silicone rubber directly impact its final quality, functionality, and efficiency; optimizing this mold design has become ever more crucial as silicone rubber products continue to gain popularity across numerous industries.
Silicone rubber products are highly sought-after due to their remarkable properties such as heat resistance, flexibility, and durability. Silicone rubber has found applications across numerous sectors such as automotive, electronics, medical devices, and consumer goods production – its versatility and dependability make it the go-to material for manufacturers looking to develop innovative yet high-performing products.
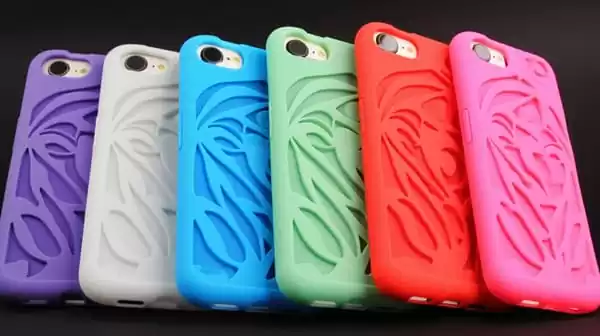
Optimized mold designs can help manufacturers unlock the full potential of silicone rubber and meet increasing consumer demands for quality products, as they ensure efficient material flow, reduce defects and ensure consistent part quality. Optimizing mold design not only ensures higher productivity but also contributes to its success and competitiveness in the market.
II. Understanding Liquid Silicone Rubber (LSR) Molding Processes
A. Definition of LSR molding as an injection molding process for silicone rubber products
LSR molding (or liquid silicone rubber molding ) is an liquid injection molding process technique used to produce silicone rubber products. The technique involves injecting liquid silicone rubber under high pressure and temperature into mold cavities, to achieve the desired shape and properties. LSR molding offers several advantages over conventional injection molding, such as high precision, excellent part quality, and the capability of producing complex geometries.
Beginning the process involves creating liquid silicone rubber material, typically consisting of two components – base silicone polymer and catalyst/crosslinker – mixed at precise proportions to obtain desired material properties and curing characteristics.
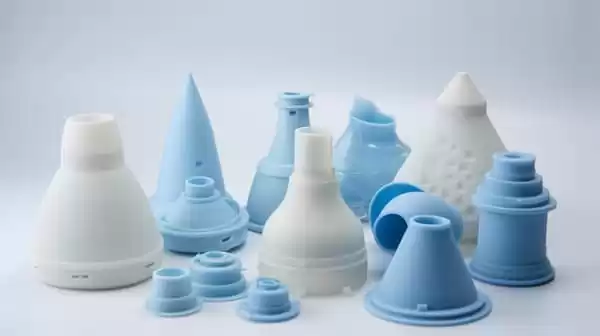
Liquid silicone rubber is fed into an injection molding machine, consisting of a heated barrel, screw or plunger mechanism for material delivery, and mold cavity. Here, the material is heated before being forced under high pressure into its desired mold shape and cavity.
Once liquid silicone rubber has been injected into a mold, it must go through a curing process in which either heating or cooling may be utilized to promote proper curing and solidification of its material. Once complete, the mold can be opened up and its solidified silicone rubber part ejected from it.
B. Overview of the injection molding machine and its role in the process
The injection molding machine is a crucial component in the LSR molding process. It consists of several key elements that facilitate the injection and shaping of liquid silicone rubber into the desired product. Here is an overview of the main components and their functions:
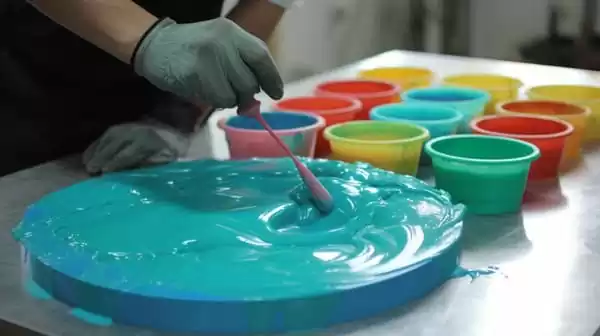
1.Barrel and Screw/Plunger Mechanism:
The barrel houses the liquid silicone rubber material and heats it to a controlled temperature. The screw or plunger mechanism then moves forward to inject the material into the mold cavity.
2.Mold Cavity:
The mold cavity is the hollow space in the mold that defines the final shape of the silicone rubber product. It is designed to accommodate the desired geometry, features, and dimensions of the part.
3.Heating and Cooling Systems:
The injection molding machine includes heating and cooling systems that regulate the temperature of the mold. Heating is necessary to facilitate material flow and curing, while cooling helps solidify the silicone rubber part for ejection.
4.Clamping Unit:
The clamping unit holds the mold halves together during the injection process, ensuring proper alignment and preventing material leakage. It exerts the necessary force to keep the mold closed during injection and opening for part ejection.
The injection molding machine provides precise control over the injection speed, pressure, temperature, and other process parameters, ensuring consistent production and high-quality silicone rubber products.
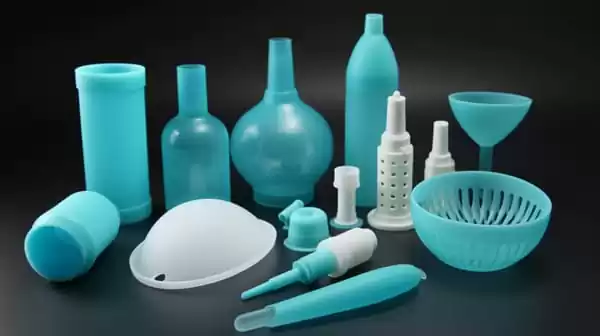
III. Key Considerations for Mold Design Optimization
A. Importance of understanding product requirements for successful mold design
To optimize mold design for silicone rubber products, it is crucial to have a comprehensive understanding of the product requirements. This includes factors such as dimensions, complexity, surface finish, and functional attributes. By understanding these requirements, manufacturers can tailor the mold design to meet specific needs, ensuring the production of high-quality silicone rubber products that align with customer expectations.
B. Design for moldability: avoiding intricate geometries, sharp corners, and undercuts
Designing silicone rubber products with moldability in mind is essential for successful mold design optimization. It is advisable to avoid complex geometries, sharp corners, and undercuts as they can pose challenges during demolding and affect part quality. Instead, incorporate smooth curves and draft angles to facilitate smooth demolding and ensure proper material flow within the mold cavity.
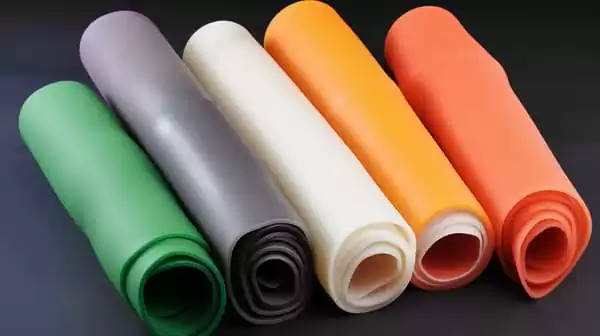
C. Wall thickness considerations and the impact on part quality and material flow
Proper wall thickness is critical for achieving optimal mold design. Maintaining a consistent and appropriate wall thickness throughout the silicone rubber product ensures consistent curing and prevents issues such as air traps or material flow restrictions. Deviations in wall thickness can lead to variations in part quality, including defects such as warping or sink marks. Careful consideration of wall thickness during the design process is essential for achieving uniform part quality and material flow.
D. Venting and degassing techniques for efficient air and gas release during curing
Effective venting and degassing are crucial in mold design optimization for silicone rubber products. Incorporating vents in the mold allows trapped air or gases to escape during the curing process. Proper venting prevents the formation of defects such as air bubbles or voids that can compromise the product’s integrity. Careful placement of vents in areas where air or gas entrapment is likely ensures efficient air evacuation and optimal curing.
E. Cooling system design and its effect on cycle times and dimensional stability
Efficient cooling system design is essential for optimizing mold design and achieving shorter cycle times and dimensional stability in silicone rubber product manufacturing. Proper cooling helps control the curing process, reduce part shrinkage, and maintain dimensional accuracy. Strategic placement of cooling channels within the mold, along with appropriate cooling media, ensures uniform cooling and efficient heat dissipation. Well-designed cooling systems enhance productivity, minimize curing time, and contribute to consistent part quality.
By considering these key factors during the mold design optimization process, manufacturers can achieve optimal mold designs that result in high-quality silicone rubber products. These considerations, including product requirements, moldability, wall thickness, venting, and cooling, play a critical role in enhancing part quality, production efficiency, and customer satisfaction.
IV. Advanced Techniques for Mold Design Optimization
A. Insert molding and its benefits for incorporating additional components or inserts
Insert molding is an advanced technique used in mold design optimization for silicone rubber products. It involves placing additional components or inserts into the mold cavity before injecting the liquid silicone rubber. The benefits of insert molding include:
Enhanced part functionality: Insert molding allows for the integration of functional components, such as metal inserts or electrical connectors, directly into the silicone rubber product. This enhances the product’s performance and functionality.
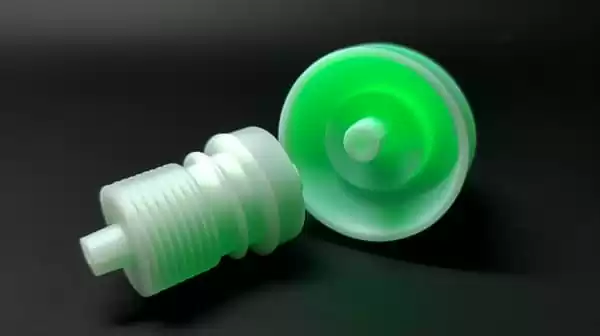
Improved part strength and stability: By securely bonding the inserts with the silicone rubber, insert molding enhances the structural integrity and stability of the final product. It eliminates the need for secondary assembly processes, reducing costs and potential points of failure.
Design flexibility: Insert molding offers design flexibility, enabling the creation of complex geometries and multi-material products. It allows for the combination of different materials with varying properties, expanding the range of applications for silicone rubber products.
B. Utilizing simulation tools and finite element analysis (FEA) for improved design accuracy
Simulation tools and finite element analysis (FEA) are powerful tools for mold design optimization. They help improve design accuracy, predict material flow, identify potential defects, and optimize process parameters. By utilizing simulation tools and FEA, manufacturers can:
Visualize and analyze the filling pattern: Simulation tools provide a visual representation of how the liquid silicone rubber flows within the mold cavity. This allows for the identification of potential flow-related issues, such as air traps, inadequate filling, or excessive material shear.
Optimize gate locations and sizes: Simulation tools help determine the optimal gate locations and sizes for injection points. This ensures proper material flow, minimizes flow-related defects, and improves part quality.
Predict part shrinkage and warpage: FEA can predict part shrinkage and warpage, allowing for design adjustments to minimize these issues. It ensures dimensional accuracy and reduces the likelihood of post-molding distortions.
C. Considerations for undercuts, parting lines, and parting surfaces
When optimizing mold design for silicone rubber products, it is essential to address considerations related to undercuts, parting lines, and parting surfaces. These factors include:
- Undercuts: Undercuts are features or indentations in the product geometry that make part removal challenging. Innovative mold design techniques, such as collapsible cores or mechanical slides, can be employed to accommodate undercuts and enable successful demolding.
- Parting lines: Parting lines are the areas where the mold halves meet, resulting in a visible line on the finished product. Careful consideration should be given to parting line placement to minimize their impact on the cosmetic appearance and functionality of the product.
- Parting surfaces: Parting surfaces refer to the mold surfaces that separate the mold halves. Ensuring smooth and precise parting surfaces helps achieve proper alignment and prevents flash formation during the silicone molding process.
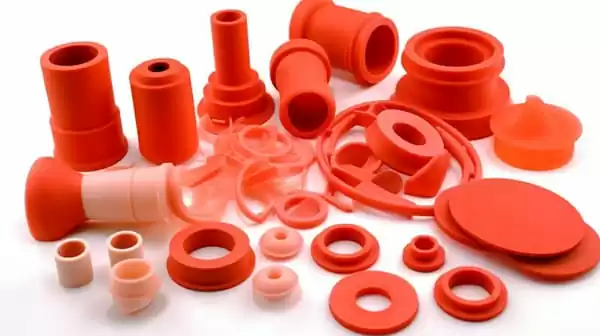
D. Optimizing mold temperature, injection pressure, and cavity pressure for consistent quality
Optimizing mold temperature, injection pressure, and cavity pressure is crucial for achieving consistent quality in silicone rubber products. Key considerations include:
- Mold temperature: Proper control of mold temperature influences material flow, curing time, and dimensional stability. Optimizing the mold temperature ensures consistent part quality and minimizes variations in mechanical properties.
- Injection pressure: Injection pressure affects material flow, filling behavior, and the replication of mold features. Optimizing injection pressure allows for complete mold cavity filling without excessive stress on the mold or part.
- Cavity pressure: Monitoring cavity pressure during the molding process helps ensure consistent part quality and dimensional accuracy. It allows for real-time adjustments to injection parameters, optimizing the production process.
By implementing these advanced techniques in mold design optimization, manufacturers can enhance the functionality, quality, and efficiency of silicone rubber products. Insert
V. Advantages of LSR Molding for Silicone Rubber Products
A. Benefits of LSR materials, including a broad range of mechanical properties
LSR molding offers several advantages for silicone rubber products, primarily due to the unique properties of liquid silicone rubber materials. These benefits include:
- Broad range of mechanical properties: LSR materials can be formulated to exhibit a wide range of mechanical properties, including varying levels of hardness, flexibility, and elasticity. This allows manufacturers to tailor the material to meet specific product requirements across different industries.
- Heat resistance and durability: LSR materials offer excellent heat resistance and durability, making them suitable for applications that involve exposure to high temperatures, harsh environments, or frequent use. They can withstand extreme temperatures without compromising their integrity.
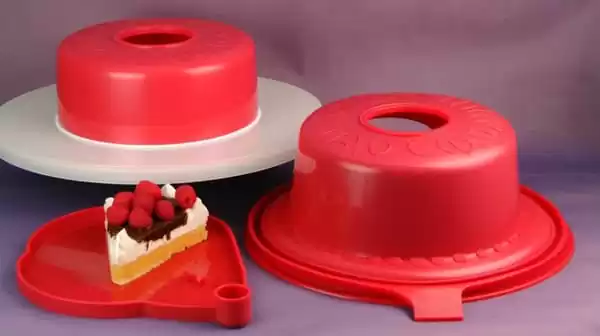
B. Enhanced cosmetic appearance and smoother surfaces compared to conventional molding
LSR molding provides superior cosmetic appearance and smoother surfaces compared to conventional molding methods. This is attributed to the unique characteristics of liquid silicone rubber, such as its low viscosity and self-leveling properties. The benefits include:
- Elimination of surface defects: LSR materials flow easily into the mold cavity, ensuring uniform distribution and minimizing the occurrence of surface defects such as sink marks, flow lines, or surface imperfections.
- Enhanced part aesthetics: LSR molding allows for the replication of intricate details and fine features with high precision, resulting in visually appealing products. The smooth surfaces achieved through LSR molding contribute to the overall cosmetic excellence of silicone rubber parts.
C. Mass production capabilities and suitability for various industries
LSR molding is highly suitable for mass production of silicone rubber products. The advantages include:
- Shorter cycle times: LSR materials cure rapidly, allowing for shorter molding cycle times compared to other rubber molding processes. This translates to increased production efficiency and higher output.
- Consistency and repeatability: LSR molding enables consistent and repeatable production of silicone rubber products, ensuring uniformity in part dimensions, properties, and quality. This is crucial for industries that require high-volume production with minimal variations.
- Wide applicability: LSR molding is applicable across various industries, including automotive, electronics, healthcare, and consumer goods. It accommodates diverse product requirements, ranging from medical components to industrial seals, gaskets, and consumer electronics.
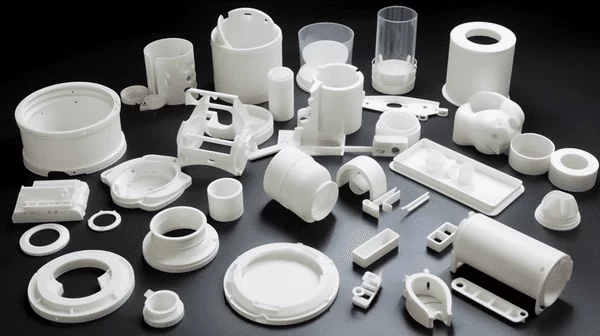
D. Impact of proper wall thickness on part integrity and cosmetic defects
Optimizing wall thickness in LSR molding has a significant impact on part integrity and cosmetic defects. Key considerations include:
- Structural integrity: Proper wall thickness ensures the structural integrity and strength of silicone rubber products. It prevents issues such as warping, distortion, or part failure due to inadequate material distribution or uneven curing.
- Cosmetic defects: Maintaining proper wall thickness throughout the product reduces the occurrence of cosmetic defects such as surface variations, sink marks, or visible flow lines. Uniform wall thickness promotes consistent curing and material flow, resulting in visually appealing parts.
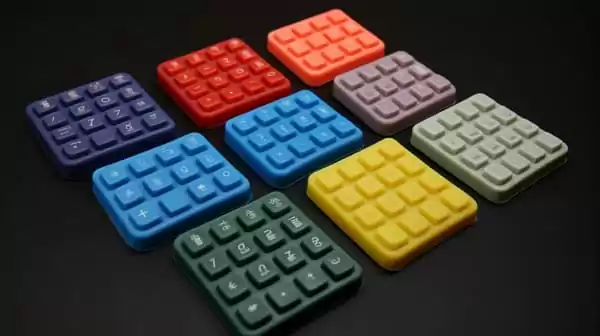
By leveraging the advantages of LSR molding, manufacturers can produce silicone rubber products with exceptional mechanical properties, enhanced cosmetic appearance, and mass production capabilities. The ability to achieve proper wall thickness ensures part integrity and minimizes cosmetic defects, contributing to the overall success and competitiveness of silicone rubber products in the market.
Conclusion
In conclusion, optimizing the lsr injection molding process and design is crucial for achieving high-quality silicone rubber products. By implementing key strategies and considerations, manufacturers can maximize the potential of the liquid silicone rubber (LSR) molding process and deliver precise, durable, and visually appealing products.
Throughout the article, we discussed the importance of understanding product requirements, designing for moldability, considering wall thickness, incorporating venting and degassing techniques, and optimizing cooling systems. These factors, among others, play a critical role in achieving optimal mold design for silicone rubber product manufacturing.
Meticulous mold design is essential for ensuring consistent part quality, minimizing defects, and enhancing productivity. By carefully considering undercuts, parting lines, and parting surfaces, manufacturers can optimize the mold design and minimize cosmetic flaws.
The advantages of LSR molding, including the broad range of mechanical properties offered by LSR materials, enhanced cosmetic appearance, and suitability for mass production, further underscore the significance of optimizing mold design. LSR molding enables the production of silicone rubber products with exceptional performance, durability, and aesthetic appeal.
In summary, by paying close attention to mold design optimization, manufacturers can unlock the full potential of the LSR molding process. This results in high-quality silicone rubber products that meet customer expectations, comply with industry standards and gain a competitive edge in the market. With meticulous mold design, manufacturers can ensure precise, durable, and visually appealing silicone rubber products that cater to a wide range of applications across various industries.