Hot vulcanized silicone rubber is a kind of organic silicon product with a large yield and wide application.
Silicone rubber has excellent high and low-temperature resistance can be used in the range of -60 ~ 250℃ for a long time and has excellent electrical insulation performance, ozone resistance, climate aging resistance, hydrophobicity, moisture-proof, and good physiological inertia.
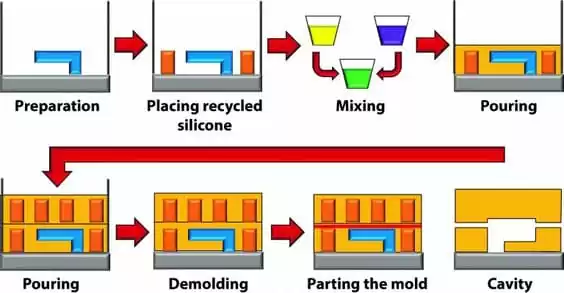
In the hot vulcanized silicone rubber add reinforcing filler, vulcanizing agent (or do not add), and other additives, by mixing is mixed rubber, can be molded, extrusion and other general rubber processing methods processed into a variety of silicone rubber products.
Mixed silicone rubber can be generally prepared in a general rubber mixer, and mass production is carried out in a kneader or closed mixing equipment.
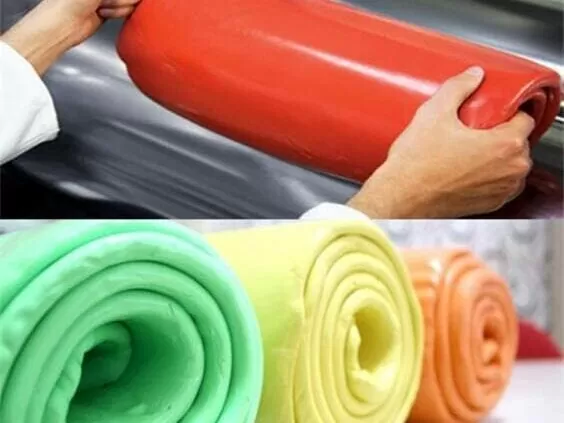
A detailed description of each process
1. Mixing
When using open mixer mixing (not commonly used), it is best to equip dust or exhaust device above the roller of the open mixer to reduce the flying of white carbon black.
In the mixing extrusion process shall not be mixed with other impurities or colloidal particles, the temperature should be controlled below 40℃, and open enough cooling water.
The mixing time of each batch of the compound is about 20 ~ 40min. The use of mixer mixing, not only can improve production efficiency, and reduce labor intensity, but also can reduce the white carbon black flying and improve the operating environment.
The operation sequence of mixer mixing (not commonly used) is similar to that of the open mixer, but the requirement of interval time is not strict.
The mixing time of each batch of silicone rubber raw material is about 8 ~ 18min, and the filling coefficient of the mixer should be controlled in the range of 0.7 ~ 0.75.
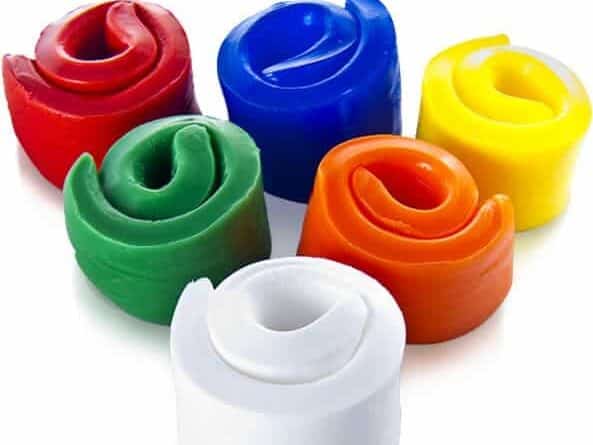
The dispensing temperature is related to the type of packing, and usually should be controlled in the range of 50℃ ~ 70℃.
Silicone sheets special kneader, vacuum extraction. Generally, 800-2000L special kneading machine is used to put raw rubber, silica black, silicone oil, mechanism control agent, and small material with special requirements into the kneading machine for mixing.
Generally, for 2-3 hours, the temperature rises to 130℃-150℃, and after half an hour of vacuum, the material is poured out of the mixer and stopped.
2. Heat treatment
When the gas phase silica without surface modification is used as a reinforcing agent, the structure control agent must be added to the compound.
Therefore, the heat treatment of the compound has become a necessary transfer molding process. The purpose of heat treatment is to further combine the structure control agent with the surface of silica (Si-OH) and eliminate the low molecular volatiles in the gum.
The general conditions of heat treatment are as follows: treatment at 160℃ ~ 200℃ for 1 ~ 1.5h under nitrogen protection or reduced pressure in the kneader.
3. The filter
Extruded products, calendered products, coated products, diaphragm products, mechanical properties impurities, and undispersed particles are one of the main factors leading to product quality problems.
Therefore, the liquid silicone rubber material used in the above silicone products must be filtered. A filter can be used to filter, and can also be used to replace the ordinary extruder.
The temperature of the barrel and screw should be controlled to the minimum, and the filter screen specifications should be 120 ~ 200 mesh.
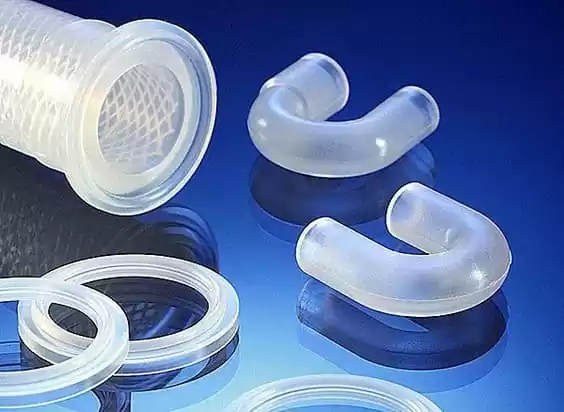
4. Return tests
After parking, the gel content increases and the plasticity decreases, so it must be reused when used.
The silicone rubbers back mixing should be enough, back mixing is insufficient, the rubber softness is poor, the surface is not smooth, And back refining is excessive, the surface of the compound will be sticky, which is not conducive to operation.