Introduction
Choosing the right silicone rubber shore durometer is of utmost importance when it comes to achieving optimal performance and durability in your application. The shore durometer is a vital measurement device used to determine the hardness of rubber materials. By selecting the appropriate durometer, you can ensure that your silicone rubber component will meet the specific requirements of your application, whether it’s in gaskets, seals, O-rings, or other molded parts.
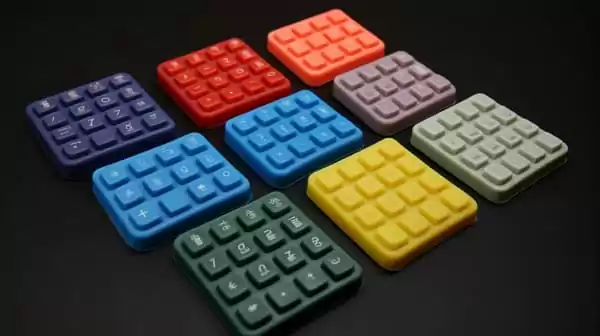
In this article, we will provide you with a comprehensive guide on how to select the right silicone rubber shore durometer for your application. We will delve into the basics of the shore durometer and its role in measuring hardness. Additionally, we will discuss the significance of choosing the correct durometer to ensure that your silicone rubber component performs optimally and has a prolonged lifespan.
Understanding the shore durometer is crucial in making an informed decision. The shore durometer scale ranges from 0 to 100 and is categorized into different scales, with higher numbers representing greater hardness. In this article, we will primarily focus on the commonly used shore A and shore OO scales for silicone rubber applications.
Our aim is to equip you with the knowledge and understanding necessary to assess your application requirements accurately. By considering factors such as functional requirements, environmental conditions, and the specific application type, you will be able to select the appropriate durometer range for your silicone rubber material. We will also address frequently asked questions and cover relevant keywords related to durometer shore hardness scale, scales, material properties, and the selection process.
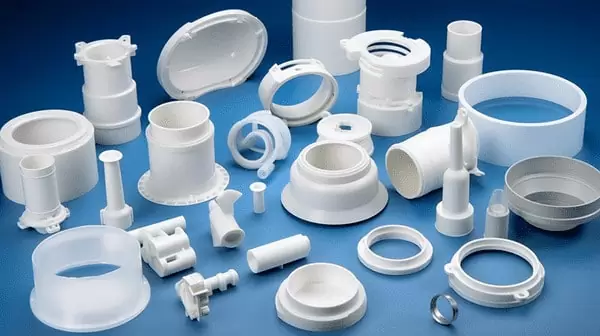
Choosing the right silicone rubber shore durometer is a critical step towards ensuring the success and longevity of your application. So, let’s dive into the world of shore durometers and embark on the journey of selecting the perfect silicone rubber shore durometer for your specific needs.
II. Understanding Shore Durometer and Shore Hardness Scales
To select the right silicone rubber main shore hardness scales and durometer for your application, it’s essential to understand the shore durometer and the various shore hardness scales. Let’s delve into the details:
A. Explanation of Shore Durometer and its Measurement Scale
The shore durometer is a device used to measure the hardness of materials, including silicone rubber. It applies a specific amount of force to create an indentation on the material’s surface and measures the depth of the indentation. The measurement measure shore hardness is then expressed on the shore durometer scale.
The shore durometer scale ranges from 0 to 100 and is categorized into different scales based on the material’s hardness. Higher values on the scale indicate greater hardness, while lower values indicate softer materials. The most commonly used shore hardness scales for silicone rubber applications are shore A, shore D, and shore OO.
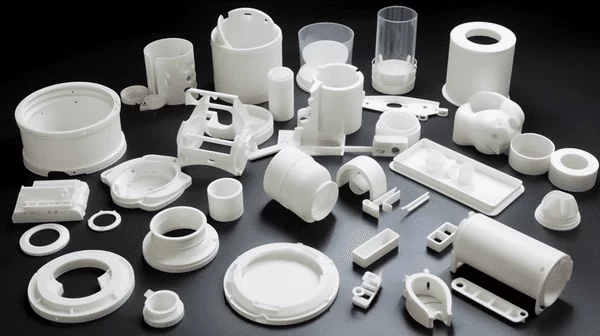
B. Introduction to Different Shore Hardness Scales
1.Shore A Scale:
The shore A scale measures the hardness of elastomeric materials, including silicone rubber. It ranges from 0 to 100, with higher numbers indicating greater hardness. The shore A scale is widely used for silicone rubber applications due to its relevance in assessing materials with varying degrees of flexibility and rigidity.
2.Shore D Scale:
The shore D scale is designed for harder materials, such as rigid plastics and hard rubbers. It also ranges from 0 to 100, with higher values representing greater hardness. The shore D scale is useful for measuring materials that have minimal flexibility and exhibit significant resistance to indentation.
3.Shore OO Scale:
The shore OO scale is specifically used for very soft materials. It ranges from 0 to 100, with higher values indicating greater hardness. The shore OO scale is relevant for measuring materials that possess extremely low hardness and exhibit little to no rigidity.
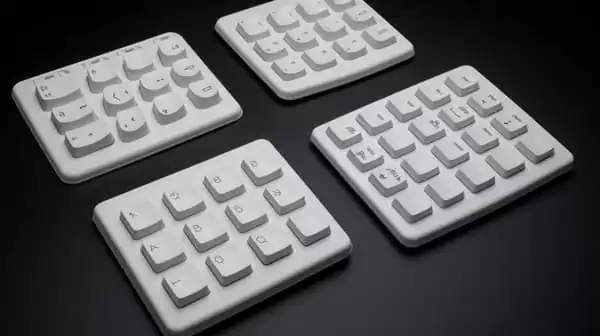
C. How Shore Hardness Scales Measure Material Hardness
Shore hardness scales provide a standardized way to measure the hardness of different materials, including silicone rubber. When using a shore durometer, the device applies a specified amount of force to the rubber mold create an indentation on the material’s surface. The depth of the indentation is then measured and converted into a numerical value on the respective shore hardness scale.
These scales enable the comparison of materials’ hardness levels and assist in selecting the appropriate silicone rubber shore durometer for a specific application. By understanding the shore hardness scales and their relevance to material hardness, you can make informed decisions about the durometer range that aligns with your desired material properties and application requirements.
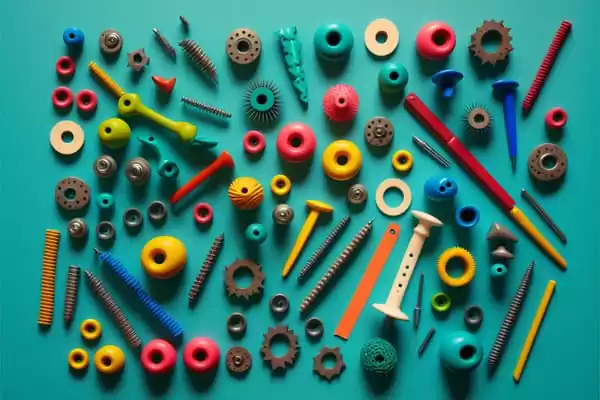
III. Assessing Application Requirements and Material Properties
Before selecting the right silicone rubber shore durometer, it’s crucial to thoroughly assess the specific requirements of your application and consider the material properties you desire. Let’s explore the key factors to evaluate:
A. Evaluating Functional Requirements of the Application
Consider the functional aspects that are essential for your application. Ask yourself the following questions:
What level of hardness is required for the silicone rubber component?Does the application demand flexibility or rigidity?
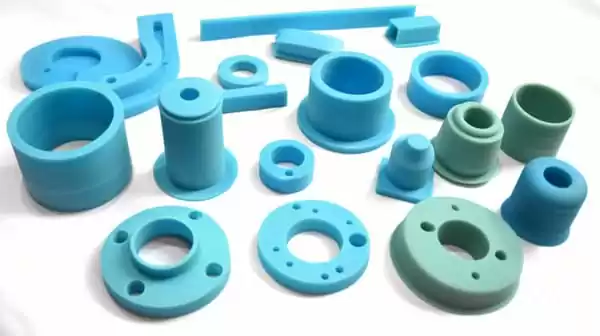
Is resistance to compression set or deformation crucial?
Are there any specific performance requirements related to load-bearing capacity or abrasion resistance?
By understanding the functional requirements, you can determine the appropriate shore durometer range that aligns with your application’s needs.
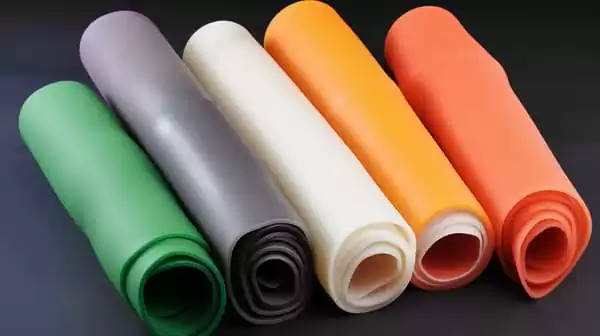
B. Considering Environmental Conditions and Their Impact on Material Selection
Environmental conditions play a significant role in material selection. Evaluate the following factors:
Temperature Variations: Will the silicone rubber be exposed to extreme temperatures? Consider the high and low temperature ranges the material will encounter during its lifecycle.
Chemical Exposure: Will the silicone rubber come into contact with chemicals, oils hard plastics, or solvents? Assess the potential chemical interactions and the material’s resistance to them.
Physical Stress: Is the component subject to high mechanical loads or stress? Consider the impact of external forces and select a shore durometer range that can withstand the anticipated stress levels.
By understanding the environmental conditions, you can choose a silicone rubber shore durometer that is suitable for the application’s operating environment.
C. Identifying the Application Type and Its Influence on Shore Durometer Choice
Different applications have varying requirements, and the type of application influences the choice of shore durometer. Consider the specific application type, such as gaskets, seals, O-rings, or molded parts. Each application may have unique characteristics that impact the choice of shore durometer, such as:
Gaskets and Seals:
Applications requiring flexibility, compression set resistance, and effective sealing of mechanical properties may benefit from a lower shore durometer range.
Molded Parts:
Applications involving complex shapes or intricate designs may require a shore durometer that balances rigidity and flexibility to ensure accurate reproduction and easy demolding.
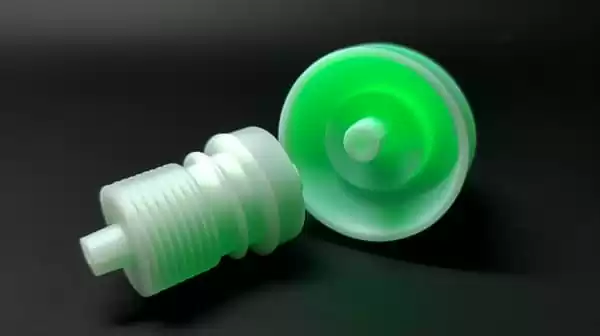
O-Rings:
Applications requiring a combination of elasticity, durability, and resistance to compression and extrusion may benefit from a specific shore durometer range.
By considering the application type and its specific requirements, you can narrow down the appropriate shore durometer range for your silicone rubber component.
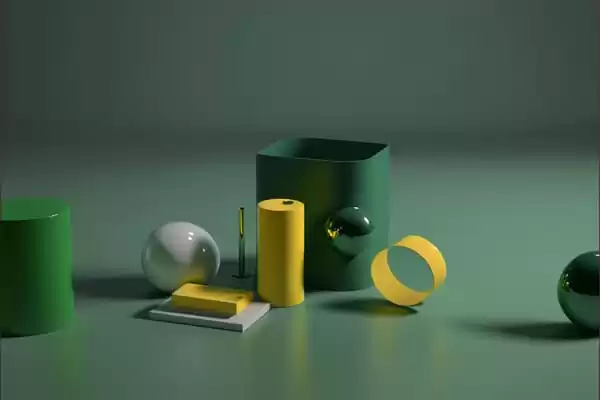
Conclusion
In conclusion, selecting the right silicone rubber with shore hardness measures and durometer is a crucial step towards achieving optimal performance and longevity in your application. By understanding the basics of shore durometer and shore hardness scales, assessing your application requirements and material properties, and considering the specific shore durometer ranges, you can make an informed decision for your silicone rubber component.
Throughout this article, we have covered the importance of choosing the right silicone rubber shore durometer and provided guidance on how to do so. Here’s a recap of the key points discussed:
- The shore durometer is a measurement device used to determine the hardness of rubber materials, including silicone rubber.
- Shore hardness scales, such as shore A, shore D, and shore OO, are used to measure the hardness of specific materials and provide a standardized way to compare material hardness.
- Evaluating the functional requirements of your application, considering environmental conditions, and identifying the application type are essential in selecting the appropriate shore durometer range.
- The shore A scale offers flexibility and durability options for various applications, while the shore D scale is used for harder materials with minimal flexibility. The shore OO scale is suitable for very soft materials with low hardness.
- Addressing frequently asked questions related to shore hardness and incorporating relevant keywords throughout the article enhances the understanding and searchability of the content.
It is vital to reinforce the significance of selecting the right silicone rubber shore durometer. The appropriate durometer range ensures that your silicone rubber component will meet the specific requirements of your application, providing optimal performance, durability, and resistance to deformation.
We encourage you to apply the guidance provided in this article to make informed decisions for your specific applications. Consider the functional requirements, environmental conditions, and the application type to narrow down the appropriate shore durometer range. Consulting with experts and conducting material testing can further aid in the selection process.
By choosing the right silicone rubber shore durometer, you can ensure that your semi rigid plastics precision mold manufacturing application operates smoothly, withstands environmental challenges, and meets the desired performance standards.