FDA, on behalf of the Food and Drug Administration, is a U.S. regulatory agency responsible for the safety management of food, dietary supplements, drugs, vaccines, and other biological agents, medical devices, radiological electronics, cosmetics, veterinary products, and tobacco products sold or manufactured in the U.S.
The export of these FDA rubber products must do FDA registration to successfully export to the U.S. The FDA also inspects and enforces regulations related to these industries, and those that do not meet the requirements will be detained by the FDA.
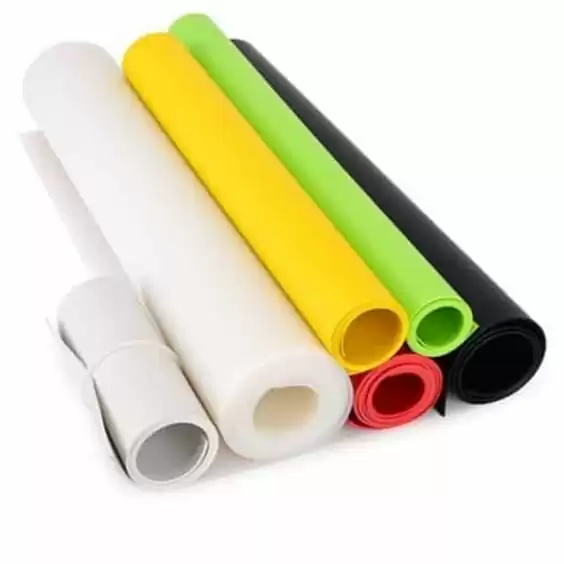
What is rubber FDA grade?
Because the FDA has strict standards for the types of materials that may come into contact with consumables, materials used to make food-grade rubber must be officially approved by the FDA.
All FDA-manufactured products are handled and packaged in certified cleanroom environments and rigorously tested to meet the needs of the most challenging food processing industry and beverage applications, and these rubber materials are typical.
1. Used for food, beverage, meat, milk, or any food-compliant chemical
2. Odorless, tasteless, and naturally resistant to bacterial growth
3. Provide reliable service over a wide temperature range
4. Non-toxic, non-marking, and non-allergenic materials
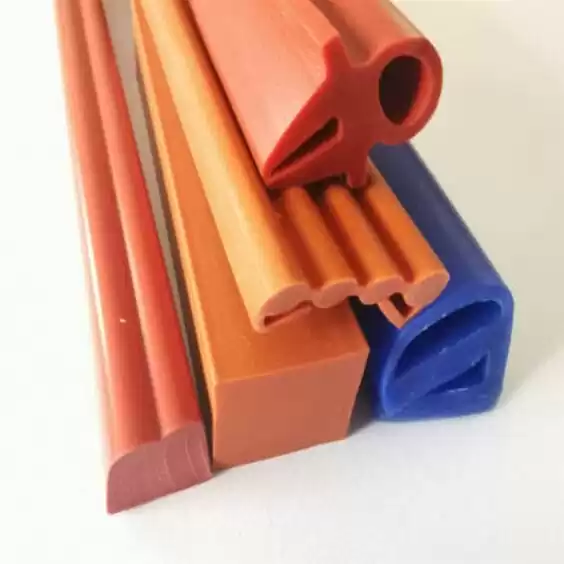
The rubber FDA certification regulations
The FDA specification for the use of FDA-approved rubber states, “Rubber products intended for reuse may be safely used in the production, manufacture, packaging, processing, preparation, handling, packing, transportation, or preservation of food products, subject to this section.”
FDA rubber, for short, complies with FDA regulations under federal regulations (FDA 21 CFR 177.2600) covering materials used with consumables such as food and beverages; however, food-safe silicones can also be used in the cosmetic and pharmaceutical industries.
It should be noted that FDA-approved rubber should not be confused with commercial-grade or medical and pharmaceutical-grade rubber, which are made to less or more stringent specifications.
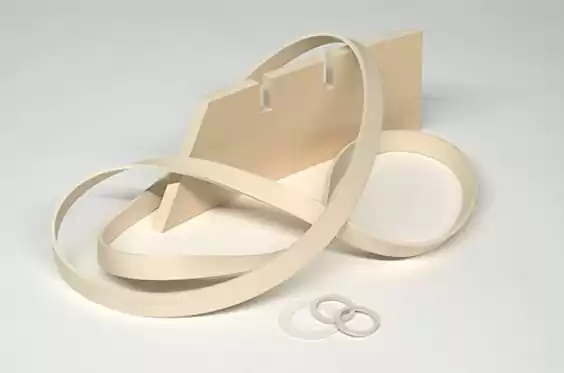
Rubber FDA food contact material testing
Food-grade rubber is a specially certified grade of rubber approved for food production and packaging using silicone, natural rubber, nitrile rubber, neoprene, and polyurethane rubber to make food-grade rubber products that can be used in the production of liquids and pharmaceuticals, in addition to food.
FDA rubber is typically used in applications involving the production, packaging, processing, preparation, or preservation of food, beverages, or consumables to maintain the quality of these products and prevent them from contamination due to exposure to foreign elements, and FDA silicone rubber does not allow harmful contaminants to collect on it.
FDA rubber certified to (FDA 21 CFR 177.2600) must be used in these applications because the risk of product contamination is significantly increased when such rubber is not used.
Frequent contact with certain foods or liquids can lead to the production of acids and chemicals that can affect the quality of food and can lead to food poisoning, and because FDA-approved rubber is considered non-toxic and a non-marking material, it is the perfect elastomer for food-related applications.
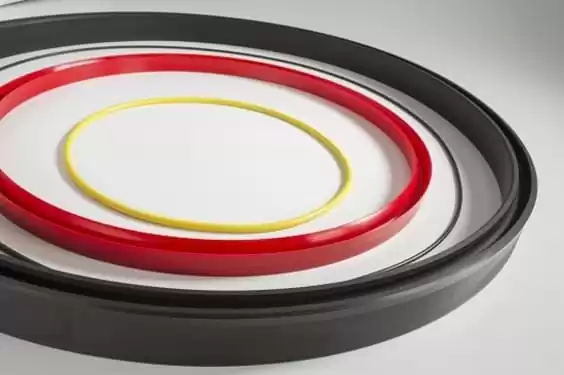
The food FDA certification process
The food and FDA-approved materials certification process is as follows:
1. Consultation: the applicant provides product information pictures or a description of the products and materials required to apply for the FDA.
2. Quotation: Based on the information provided by the applicant, the technical engineer will make an assessment, determine the items to be tested, and provide a quotation to the applicant.
3. The applicant confirms the quotation and fills in the test application form and test samples.
4. Sample testing will be conducted by the applicable FDA standards.
5. Provide an FDA certification report after the test is completed.

For food-grade rubber
1. EPDM
EPDM rubber is used in cases where the rubber needs to resist environmental degradation and ozone exposure.
2. Natural rubber
Natural rubber is suitable for products exposed to dry and wet organic acids and alcohols and chemicals of medium pH.
3. Neoprene
Neoprene is suitable for exposure to high abrasion and wears chemicals that leave residues such as grease.
4. Nitrile rubber
Nitrile rubber is a synthetic rubber, suitable for direct mixing with grease products.
5. Silicone rubber
Heat-resistant, open flame, and electrical insulation, widely used rubber for the manufacture of food and pharmaceuticals.