Rubber injection molding is a versatile process that can be used to produce a variety of parts and products, from medical devices to automotive tires.
This process can be used for high-volume production and to create custom or standard parts with complex shapes, as it allows manufacturers to choose from a variety of materials that will bond best in this type of equipment with safety features such as vibration control. To learn more about how they work, continue reading below!

How does rubber injection molding work?
Rubber injection molding is a process in which rubber is injected into a mold to make various parts and products. The thermoplastic rubber injection molding process begins by loading the rubber into the barrel of the injection molding machine.
The rubber is then melted at high temperatures, usually between 200 and 350 degrees Fahrenheit. Once the rubber is melted, it is injected into the mold under high pressure. The rubber then cools and solidifies inside the mold, forming the shape of the mold cavity.
After the rubber cools, the part or product is ejected from the mold and is then ready for use. Rubber injection molding is a versatile manufacturing process that can be used to make a wide variety of parts and products.
In rubber injection molding, the vulcanized rubber is placed in a heated barrel, the hot rubber is pressed into the mold cavity through a nozzle, where it cools and undergoes a vulcanization reaction. After some time, the mold is opened and the vulcanized rubber part is ejected.
The molds can be made from a variety of materials, including steel, aluminum, and even 3D-printed plastic. The key to successful rubber injection molding is to maintain consistent temperatures and pressures throughout the process.
Otherwise, the rubber may not cure properly or may result in a poor-quality product. In addition, it is important to use high-quality rubber designed for liquid injection molding. This will help ensure that the finished product meets the desired specifications.
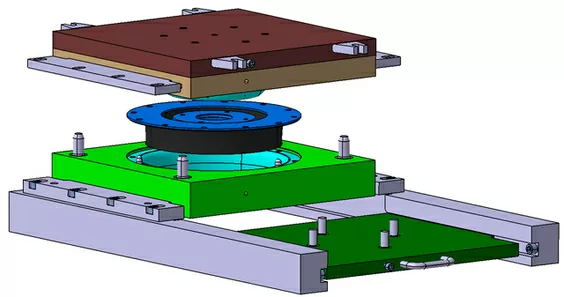
What are the benefits of rubber injection molding compared to other manufacturing processes?
The rubber injection molding process is a highly versatile manufacturing process that offers many advantages over other methods of manufacturing rubber parts and products. One of the main benefits of rubber injection molding is that it allows for very precise control of the finished dimensions.
This high degree of precision is possible because the mold cavities are created using computer-aided design (CAD) technology.
In addition, rubber injection molding can be used to produce parts with very complex designs and features that would be difficult or impossible to create using other manufacturing processes.
Another advantage of rubber injection molding is that it is a relatively fast and efficient process. In most cases, the entire manufacturing process, from creating the mold cavity to injecting the actual rubber material to cooling and curing the finished product, can be completed in a matter of minutes. This makes rubber injection molding ideal for applications that require fast turnaround times.
Finally, rubber injection molding is a cost-effective manufacturing method. Because it is a relatively fast and efficient process, it can reduce labor costs and overall production time. In addition, because the finished product is subject to very precise control, virtually no scrap is generated during the manufacturing process.
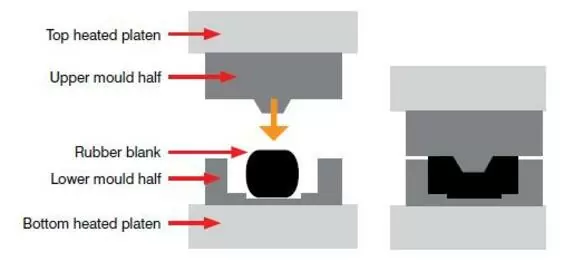
What types of rubber can be processed by this method and what is the durability of the final product?
This method can be used to process various types of rubber, including natural rubber, synthetic rubber, and recycled rubber. The durability of the end product depends on the type of rubber used and the processing conditions.
In general, this method produces a more durable product than traditional vulcanization methods. The main advantage of this method is that it does not require the use of toxic chemicals, which makes it more environmentally friendly. This method is also less likely to cause damage to the rubber during processing.
How to choose the right rubber for your project?
How to choose the right rubber for your project depends on several factors, including the intended purpose of the rubber, the intended properties of the rubber, and the compatibility of the rubber with other materials.
First, you need to determine what type of rubber you need. There are three main types of rubber: natural rubber, synthetic rubber, and recycled rubber. Natural rubber is made from latex, while synthetic rubber is made from petroleum products.
Reclaimed rubber is made from scrap tires and other post-consumer products. Each type of rubber has different properties, so it’s important to choose the right rubber for your project.
Next, you need to consider the ideal properties of the rubber. Some common properties include hardness, elasticity, abrasion resistance, and chemical resistance. Again, each property is determined by the type of rubber, so it’s important to make sure you choose the right type for your needs.
Finally, when choosing rubber for your project, you need to consider compatibility. You need to make sure that the rubber is compatible with other materials it will come into contacts with, such as metal or plastic. If you keep these factors in mind, you can be sure to choose the right rubber for your project.
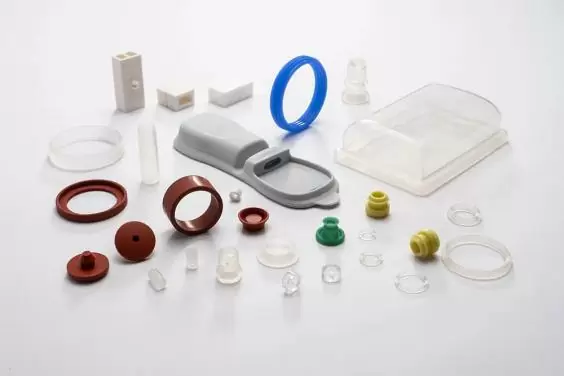
Characteristics from the rubber injection molding process
To get the most out of the rubber injection molding process, it is important to follow a few simple tips. First, be sure to choose the correct type of rubber for your project. There are many different types of rubber, each with its unique properties.
If you are unsure which type of rubber is best for your project, consult with a professional supplier. Next, it is important to properly measure the amount of rubber you will need. In most cases, it is better to have too much rather than too little.
Finally, be sure to carefully follow the instructions for your particular injection molding machine. By following these simple tips, you can ensure that your next rubber injection molding project is a success.
Successful projects using rubber injection molding
Rubber injection molding is a versatile technology that can be used to make a variety of parts and products. To demonstrate the potential of this technology, ZetarMold conducted a case study of a successful project that utilized rubber injection molding.
The project was to develop a new line of game controllers for a major video game company. These controllers had to meet stringent requirements in terms of size, weight, durability, and aesthetics.
After considering various manufacturing options, we decided that rubber injection molding was the best choice for this project. The project was a success, with the controllers receiving rave reviews from critics and gamers alike.
Using rubber injection molding allowed us to meet all the required specifications while also reducing costs. This case study demonstrates the potential of rubber injection molding and illustrates how it can be used to create high-quality products.
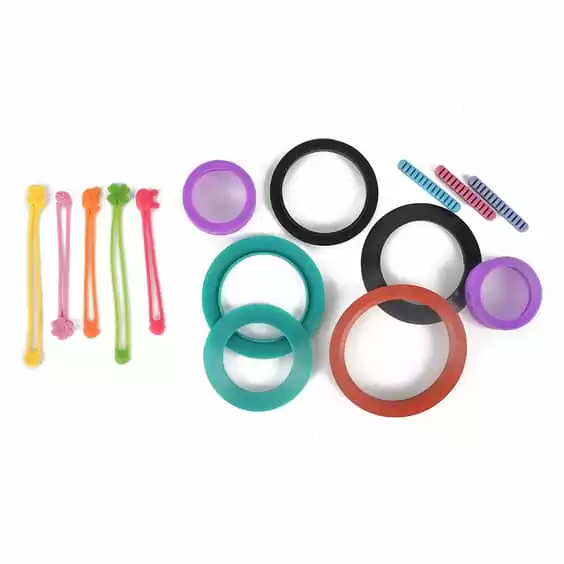
Advantages of Rubber Injection Molding
Injection rubber molding is a process that offers several advantages over other rubber molding methods.
One advantage is that it can be used to create very complex shapes. This is because the mold is injected with rubber under high pressure, which allows the rubber to flow into all nooks and crannies of the mold.
This also results in a very strong bond between the rubber and the mold, which means that the finished product will be very durable.
Another advantage of injected rubber molding is that it is relatively quick and easy to set up. This makes it ideal for companies that need to produce a large number of rubber parts in a short period.
Finally, injection rubber molding typically produces parts with a high degree of dimensional accuracy. This means that they will fit together correctly and function as intended.
Overall, the custom rubber molding process is a versatile and reliable method that offers many advantages over other types of rubber transfer molding.
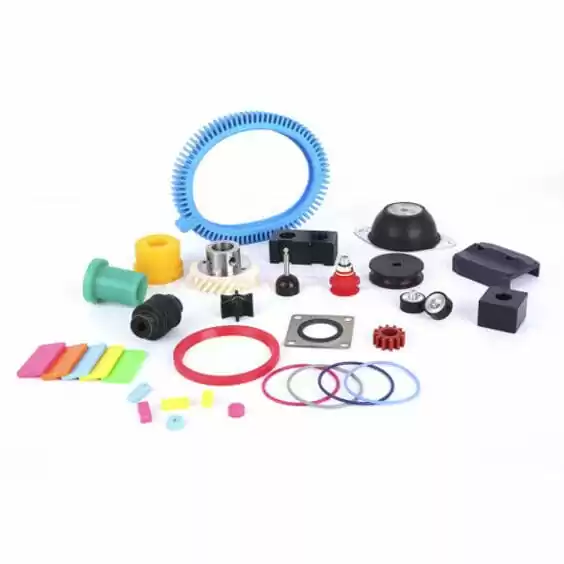
Summing up
Custom rubber injection molding is a process that has been used for many years to manufacture custom or standard parts with complex shapes.
The key to a successful rubber injection molding project is to maintain consistent temperatures and pressures throughout the process and to use high-quality rubber designed for this purpose.
If you are interested in learning more about how uncured rubber injection molding works, please contact ZetarMold today, and we would be happy to discuss your specific needs and see how we can help you get started with this versatile manufacturing process.