Introduction
Silicone hardware over molding, often simply referred to as over molding, is a specialized technique that brings together the versatility of silicone with the structural support of hardware components. It’s a meticulous process that encapsulates rigid hardware with silicone elastomers, resulting in products that offer the best of both worlds.
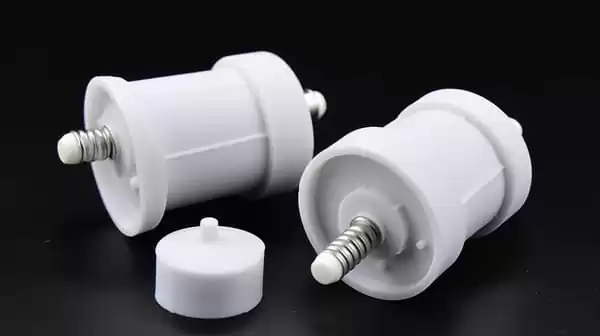
The silicone encapsulation manufacturing process refers to a method of full or partial encapsulation of silicone materials. It is divided into two types: solid silicone and liquid silicone rubber encapsulation. Solid silicone encapsulation is molded, and liquid silicone encapsulation is mostly injection molded. Silicone is placed on nylon, ABS, metal and other materials that have been coated with glue, and then placed in a mold for vulcanization or liquid silicone injection for integrated molding.
Silicone Hardware Over Molding
The silicone encapsulation process is divided into:
cleaning the substrate material – applying glue (priming agent) – silicone heat vulcanization encapsulation (molding or injection molding). The silicone encapsulation process is used in silicone coin purses, silicone kitchenware products, and silicone rubber rollers. , widely used in infant and child products.
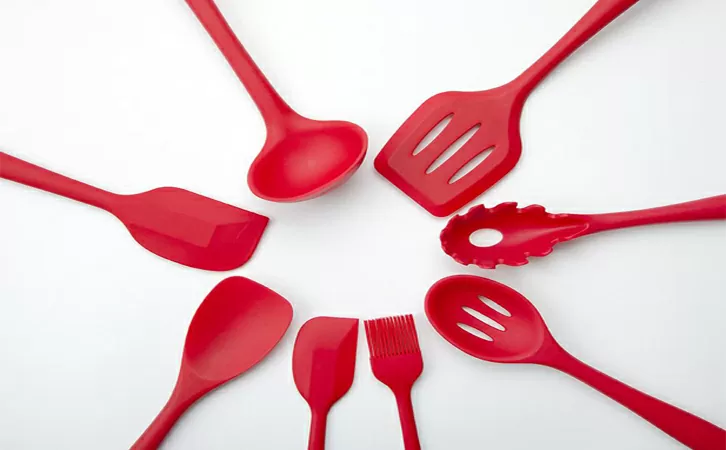
The process flow of liquid silicone rubber encapsulation:
1. Clean the hard substrate:
Before coating with liquid silicone, the nylon, ABS, metal (stainless steel, aluminum alloy) and other materials to be coated should be cleaned. The purpose of cleaning is to ensure that the surface to be coated is free of oil stains and oxide layers; oil stains It needs to be wiped clean with industrial alcohol and other solvents.
2. Apply KL-26AB silicone glue. If you need to strengthen the strength, you can apply CL-24S-3 primer treatment agent:
Generally, liquid silicone cannot self-adhere to the base material, so the corresponding glue or primer needs to be applied to the bottom silicone overmolding material. Choose different primers according to the materials. Pay attention to the coating surface being as thin and even as possible and covering all bonding points. After the glue primer dries and the film on the surface of injected material of the object is non-sticky, proceed to the next step.
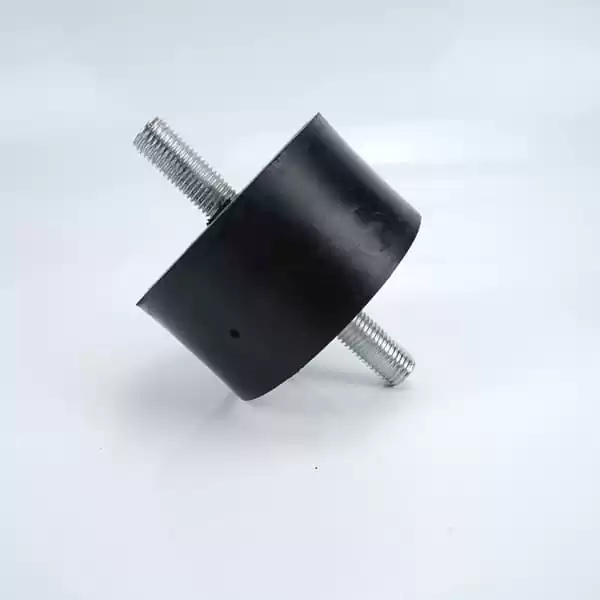
3.Liquid silicone encapsulation:
Injection molding also involves vacuuming, applying pressure, and injecting the mixed liquid silicone into the mold cavity for heating and vulcanization. After curing, liquid silicone can effectively treat the surface of nylon, ABS, metal and other materials under the action of silicone glue + primer. Pay attention to ensure that there are no bubbles during the process. Liquid silicone injection molding is an automated glue filling method.
Difficulties in silicone hardware encapsulation process
For silicone products that have a special shape and require high hardness and are not easy to bend, products with silicone hardware encapsulation technology have become one of the choices for many customers. For example, our common handles are basically made of internal The outside of the metal is made of glue. This phenomenon can be called partial encapsulation and overall encapsulation. Partially encapsulated products are common products such as screwdrivers, while overall encapsulation products such as silicone spoons are full-encapsulated injection molded parts. For silicone product manufacturers, it is still relatively difficult to use the injection molding process for partially encapsulated products, so they are basically produced using the overall encapsulation effect.
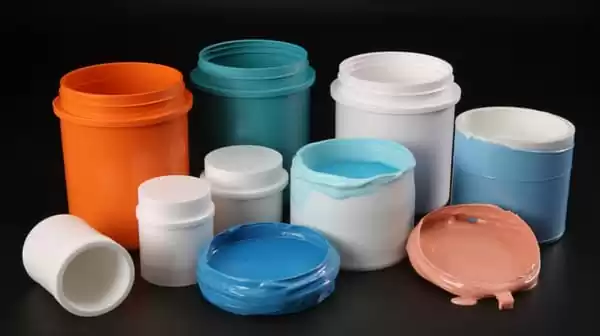
In the silicone products industry, in terms of process complexity and product accuracy, only the two-color silicone process and the silicone encapsulation process are difficult. In the production process of silicone products manufacturers, the problem of comparing manufacturers is that the silicone encapsulation process consumes labor and the defective rate is difficult to control.
However, since products with silicone hardware encapsulation technology are relatively popular in the market, and the more popular products take longer in the production and processing process, silicone encapsulation processes such as silicone spoons and silicone spatulas are not in actual production.
There will be some difficulties during the process. Let’s introduce the specific difficulties below:
1. The silicone hardware encapsulation process is difficult to position. Hardware encapsulation uses silicone rubber to completely or partially wrap the hardware and then vulcanize it at high temperature. During the entire vulcanization process, except for the silicone, the offset of other hardware components is difficult to control, so For silicone product manufacturers, positioning standards are required for products including hardware or nylon. Generally, positioning can be done in several ways.
2. If the mold structure is complex, a three-layer template can be opened. Now vulcanize the rubber material at the bottom of the silicone and the position where the hardware is placed in the middle mold to create a positioning slot for the hardware. After placing insert molding the hardware inside, remove the middle layer template. Finally, the effect of internal hardware packaging can be achieved, but this method is not feasible for most small products! This method is usually used for larger products.
3. For double-layer boards, if you do not have any requirements for appearance, you can choose to add a few positioning pins in the middle of the mold. While placing the inner rubber and overmolded material, place the hardware into the position where the last layer of rubber material and Template, there will be basically no offset in the products that come out. This method can be used better for longer or round hardware.
4. The hardware is relatively small, and the margin of the silicone part is relatively large, so you can roughly wrap the hardware manually for direct molding. This transfer molding method is better for products where the hardware is not easily offset and positioned.
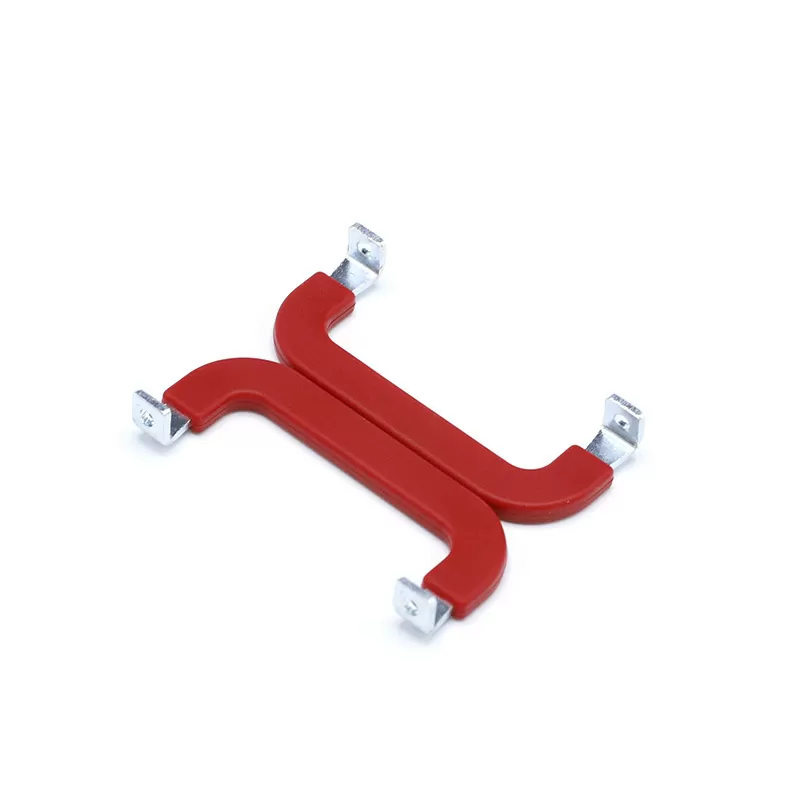
5. Deviation leads to leakage of hardware. Deviation refers to the deviation of the hardware caused by the molding process when the rubber material is placed, resulting in leakage of hardware at the head or tail. The main reason for the deviation is that excessive pressure on the machine may cause the hardware to leak. It causes the hardware to shift. Control the pressure, time and temperature of the machine to produce qualified products. This is caused by the uneven placement of the product’s rubber. The rubber needs to be placed symmetrically and evenly and attention must be paid to wrapping it during the placement process. Temperature control is very important for the edge part of the rubber material. During the placement process, try to shorten the time of entering the mold to ensure temperature and time control of exiting the two shot molding part. If it is too brittle, it may cause hardware leakage in the product.
Generally speaking, offset leakage of hardware is a difficulty for hardware encapsulation products. Generally speaking, we can solve and improve it through the above methods. Excessive pressure on the machine may cause the hardware to shift. When personnel place the rubber material, You need to focus on control! The temperature must be controlled within a certain range, etc. In short, there are many difficulties in making silicone products regardless of the process. It mainly depends on how you control it!
Precautions and maintenance tips for using silicone hardware-coated kitchenware:
Currently, the majority of silicone kitchenware is made of hardware and stainless steel, but more and more silicone hardware-coated kitchenware are used. Many people do not have a clear understanding of silicone materials and naturally lack some maintenance skills and knowledge for silicone hardware kitchenware. Purchase Finally, I don’t know how to use it correctly, so here I will introduce to you the precautions and maintenance skills of silicone hardware-coated kitchenware.
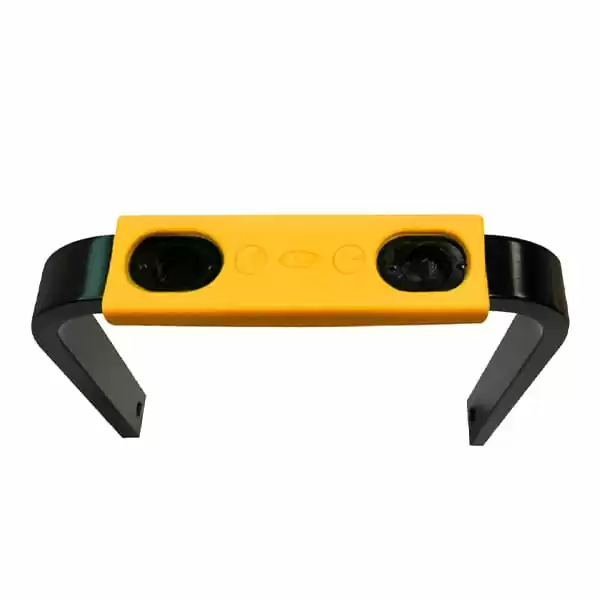
The use of kitchen utensils is a skill, and the maintenance and cleaning processes are also relatively important. At present, most of the products on the market are half-coated and half-hardware, such as silicone spatulas, silicone spoons, etc., and this kind of silicone hardware is coated with rubber. If kitchen utensils are not cleaned and maintained regularly, subsequent use functions and appearance will be affected to a certain extent.
1. Before use, you need to soak it in high-temperature hot water for a period of time to completely kill the virus. Although it has been vulcanized twice, many silicone product manufacturers currently add vulcanization time for a short period of time, resulting in product substances that are not completely excessive. This must be ensured as a precaution. Antivirus process.
2. Use warm or boiling water mixed with white vinegar or cola to wipe from time to time. The effect of this method is to maintain the appearance of the product and prevent oil stains, sauces, etc. from chemical reactions with it. It can be wiped with a soft cloth, clean water, and disinfectant. Do not scrub with hard objects such as iron brushes or steel wool. This can maintain the luster and longevity of the product and keep it brand new for a long time.
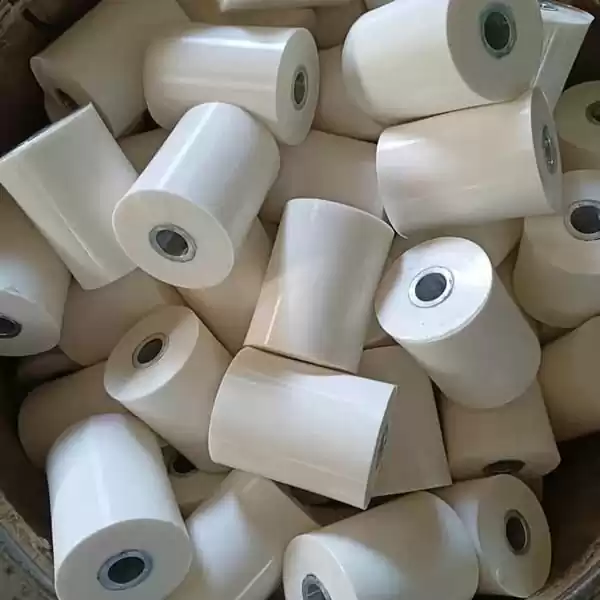
3. Silicone is combined with five-finance materials. Silicone material is a soft body, while the surface of stainless steel will undergo long-term collisions and temperature changes, leaving foreign matter on the surface treatment silicone tableware. Therefore, do not leave it alone for a long time or soak it for a long time after use. Keep it Drying can not only prevent loss of luster, but also ensure the surface is safe for use!
4. Avoid collisions. Try to avoid collision with hard objects and choose soft and gentle cleaning tools.
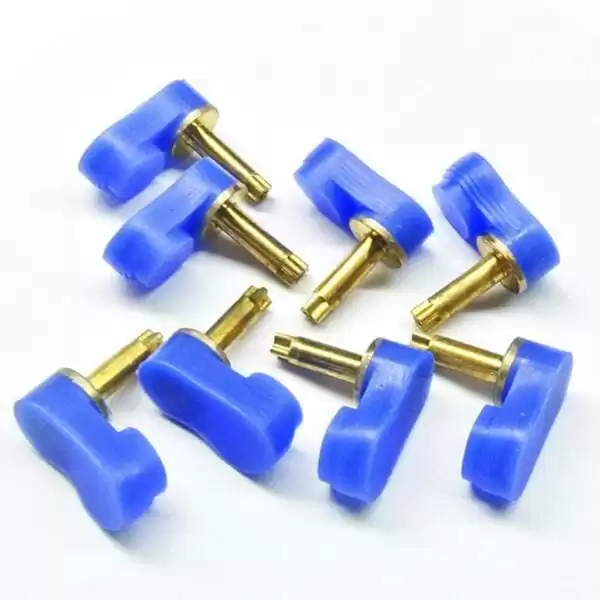
Conclusion
Significance Across Industries
The significance of silicone hardware over molding cannot be overstated. It answers the call for products that require a combination of multiple materials, and properties. Whether it’s for medical devices, consumer products, or automotive parts, this process empowers manufacturers to create products that not only meet technical specifications but also cater to user comfort and satisfaction.
The Art and Science
Silicone hardware over molding is more than just a manufacturing process; it’s an art and a science. It showcases the innovation and expertise of engineers and designers who can seamlessly blend silicone, plastic, metal, and other materials into a single, cost-effective product.
In a world where versatility and quality are paramount, silicone hardware over molding stands tall as a testament to human ingenuity. It’s a testament to our ability to meet the specific requirements of diverse applications while delivering products that enhance our daily lives. As we move forward, we can only anticipate even more exciting applications and innovations in the realm of silicone hardware over molding, making it an integral part of the industries that rely on its unique capabilities.