Introduction
Silicone, lauded for its harmlessness and tenacity, distinguishes itself in the protective material cosmos. Its inherent pliancy endows it with the capability to quell shocks and diminish the brunt of inadvertent drops or clashes, a prevalent apprehension amongst digital apparatus aficionados. Additionally, its robust nature guarantees enduring resistance against daily erosion, rendering it an enduring shield for devices.
Beyond its defensive attributes, silicone’s allure is augmented by its non-toxic nature, ensuring its suitability for a broad spectrum of digital devices, ranging from electronic products devices to tablet computers mobile phone cases. This quality is especially pivotal in an epoch where the prominence of health and ecological mindfulness steers consumer preferences.
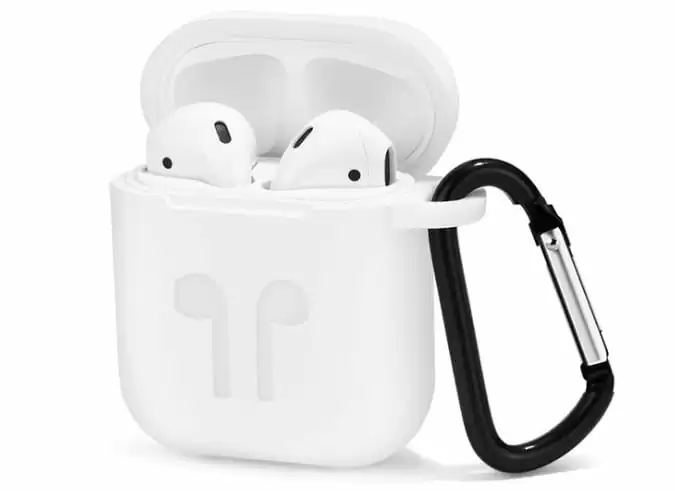
Hence, silicone protective sheaths proffer not merely a pragmatic approach to apparatus conservation but also resonate with the escalating demand for secure, resilient, and adaptable accouterments in the realm of electronic commodities.
Silicone Protective Cover Molding Process
Silicone sleeves are different from plastic silicone. They are silicone products produced using high-temperature vulcanized silicone as the main raw material through a molding and vulcanization molding process.
Step1: Rubber mixing includes mixing of raw rubber, color matching, weight calculation of raw materials, etc.;
Step 2: Vulcanization molding (called oil pressure molding)uses high-pressure vulcanization equipment to vulcanize at high temperature to make the silicone raw material into a solid state.
Step 3: Trimming The silicone covers products that come out of the custom molded will come with some useless burrs and hole chips that need to be removed; currently, in the industry, this process is completely done by hand, and some factories also use punch machines to complete it.
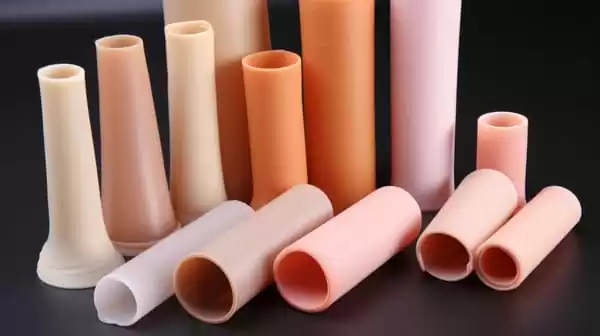
Step 4: Polishing Because the production environment is not a vacuum, the silicone protective cover will inevitably be contaminated with dust and impurities, or the startup staff will dirty some products with other materials, some of which cannot be cleaned. At this time, the protective cover can only be polished by polishing, as long as the customer accepts it. , fine polishing can reduce processing costs and waste.
Step 5: Cleaning Most silicone products need to be cleaned. Dirt is a relatively late treatment process, because the previous processes may stain the silicone protective cover. Dust and impurities can be blown off with an air gun, and then cleaned with a dust-free cloth and Tianna water to provide customers with satisfactory products.
Step 6: Spray touch oil. Most silicone protective cases need to be sprayed with touch oil. Completing this process will improve the quality of the silicone protective case products. Most ink manufacturers can provide environmentally friendly hand oil. A good protective silicone case depends first on its design and second on its feel and texture. Some use spray booths for spraying, some use ink pools for soaking, and there are various methods.
Step 7: After baking and spraying with touch oil, the protective silicone cover itself must be dried. After baking in a high-temperature oven for about 15 seconds, it can be moved aside to cool and packaged.
After the above seven steps of preparation, a perfect silicone protective cover is born.
Improve the processing efficiency of silicone protective covers
For the manufacturing industry, the efficiency and quality of factory mass production processing are the profits of the products, and customer recognition and support are the reputation of the brand. Therefore, for the processing industry, the improvement of production capacity and quality are crucial. In the silicone products industry, products Efficiency and quality are examples. The same is true for silicone cases and the current custom processing of silicone protective covers, so being able to improve efficiency and effects is the most critical. When it comes to this, it depends on the processing technology and methods of each industry.
So how to improve the efficiency of silicone products during the processing process and meet the delivery date for customers on time? Silicone protective covers are prone to bad problems during the processing and have to reduce time to improve quality, so we want efficient customized processing of protective covers. There is also a complete plan.
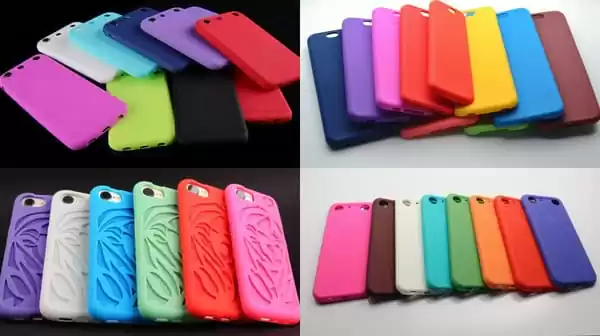
1. Appropriate release agent can be added when mixing raw materials, so that the packaged product can be quickly demoulded, which can save some pick-up time.
2. Add a rapid vulcanizing agent to the silicone material to make the product more fluid. A product that originally takes 100 seconds can reduce the time by about 30% under the same temperature and pressure.
3. Adjust the temperature and pressure of the machine. Under normal circumstances, the temperature of the machine is relatively stable, so the temperature can be gradually increased. The higher the temperature, the faster the fixed-line speed of the product, which can save unnecessary time. Prerequisite is to ensure the quality of the product
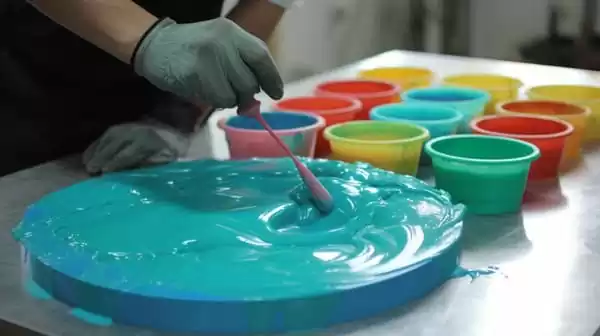
4. Change the placement method. The placement method during operation will also affect the demoulding time of the product. For example, long-shaped raw materials can be appropriately replaced into sheets to allow them to fill the mold cavity faster and increase the speed.
5. Change the number and formation of the exhaust of the vulcanization machine. During the exhaust process, the machine closes the mold up and down slowly. If the surface treatment the product is not particularly complex, the secondary exhaust can be reduced and the product can be maintained.
6. Work hard on the mold and open more discharge chutes to allow the product to keep the remaining material discharged. If the product order volume is large, the number of mold cavities can be opened as much as possible to ensure processing efficiency.
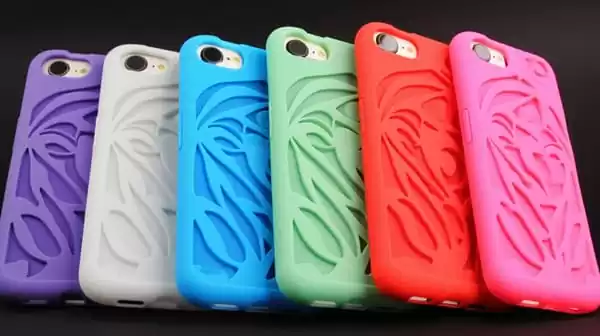
The main difference between protective covers and other products is that they need to pay attention to appearance, so they can be appropriately improved while ensuring product quality. Blind changes may lead to long-term effects. The processing of silicone products in silicone products factories is a complex process and is not any The methods and processes of a silicone are the same, and more methods of silicone product manufacturers are gradually honed.
Silicone protective cover pattern production
1. Surface treatment process:
The most common surface treatment is spraying hand oil, which can make the protective cover feel good to the touch. This is also the simplest surface treatment. Silicone products can easily absorb dust in the air under normal conditions and have a certain degree of stickiness. Spray a thin layer of feel oil on the surface of the silicone cover to prevent dust and ensure the feel.
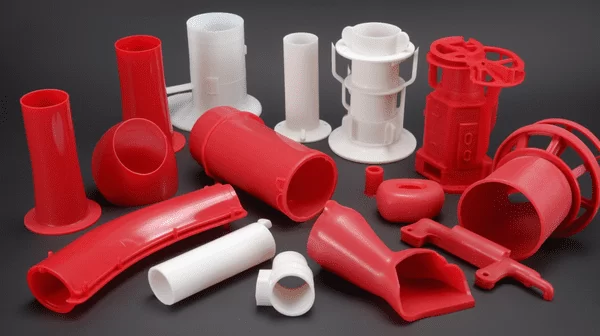
2. Oil spraying and laser engraving process:
After trimming the edges of the silicone sleeve, spray a layer of colored ink on the surface of the silicone sleeve, then laser the pattern, and then spray a layer of touch oil on the surface. This technique is quite popular at the moment.
3. Glue-dropping process:
drop colored liquid glue on the silicone sleeve that has been repaired to make a pattern.
4. Color printing process:
print any color pattern on the silicone sleeve that has been trimmed. This process can make the silicone sleeve not only beautiful but also have a strong three-dimensional effect. It feels good in hand too. It can print patterns on every side of the silicone cover, and the patterns are very smooth and natural.

Conclusion
These covers, crafted from silicone, a material celebrated for its durability, flexibility, and non-toxic nature, provide a robust shield against the everyday hazards that devices face. From absorbing the shock of drops to resisting wear and tear, silicone covers ensure that our phones, tablets, and other electronic gadgets can withstand the rigors of daily use.
Looking ahead, the future of silicone protective covers is marked by exciting possibilities. Advancements in production techniques are set to further enhance the quality and capabilities of these covers. We can anticipate a broader array of customization options, allowing consumers to tailor their device protection to their specific needs and preferences. Whether it’s integrating advanced waterproofing, improving heat insulation, or offering a wider range of aesthetic choices, the evolution of silicone cover manufacturing promises to keep pace with the ever-changing landscape of technology.
In an age where electronic devices are integral to our lives, the role of silicone protective covers is more crucial than ever. They do more than just protect; they add value, style, and personalization to our devices. As we look to the future, it’s clear that silicone covers will continue to evolve, not just as protective solutions, but as a statement of innovation and personal expression in the dynamic world of electronic accessories.