Introduction
The silicone rubber compression molding process is a production method that utilizes high pressure and heat to shape liquid silicone rubber into desired products. This technique has applications across various industries such as automotive, medical, and consumer goods.
Recently, energy efficiency has become an increasingly significant factor in production processes as it not only reduces environmental impact but also lowers costs for manufacturers. Given how energy-intensive silicone rubber production can be, exploring methods to achieve energy efficiency through silicone rubber compression molding is necessary. By doing so, manufacturers can lower processing energy consumption while still producing high-quality goods efficiently. In this article, we’ll look at various approaches to achieve energy efficiency through liquid silicone rubber compression molding.
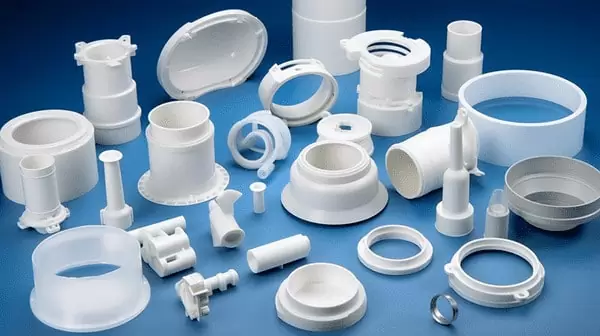
II. Achieving Energy Efficiency in Silicone Rubber Compression Molding
Silicone rubber compression molding is a popular production process used in various industries. However, this major energy consumer, resulting in high production costs and environmental impact. To address this issue, manufacturers can implement several strategies to achieve increased energy consumption and efficiency in silicone rubber compression molding.
Use of energy-saving drive systems
Advanced technology is used to control motor speed, power output, and torque, reducing energy consumption during the molding process. These systems can be programmed to operate only when necessary, reducing energy waste.
Adopt auxiliary molding technology
Additional equipment and processes can improve production efficiency and reduce energy consumption. Hot runner molds can eliminate the need for runners and gates, and in-mold welding and assembly can reduce energy consumption caused by secondary processing steps.
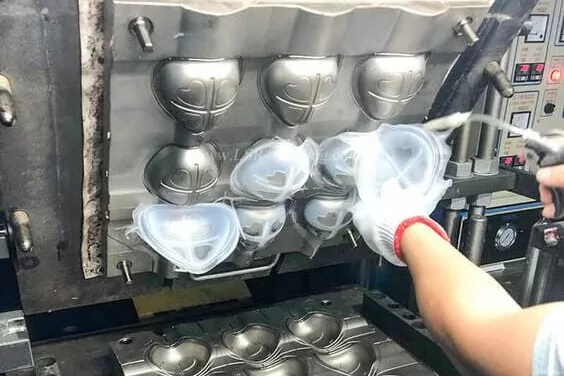
Utilization of energy regeneration systems
These systems recover and reuse waste energy generated during the molding process. For example, an energy regeneration system can recover heat from the cooling water system and reuse it to preheat the material before it enters the mold.
Improvement of heating and cooling pipes
Using advanced heating and cooling systems, such as infrared heating or high-efficiency cooling systems, can reduce energy waste and consumption during the molding process.
The selection right injection molding machine
A liquid injection molding factory should consider the capacity of the machine, the recommended injection molding process and the cooling efficiency when selecting an injection molding machine. This can minimize energy waste and reduce energy consumption.

Optimization of process parameters
Fine-tuning the process parameters, such as the melt temperature, can ensure optimal energy consumption and production efficiency.
Waste energy reduction and material waste prevention
Reducing waste and preventing material waste can minimize energy consumption and environmental impact. Mold cavity design optimization, unitized molding schemes, and other processing technologies can promote better surface quality and reduce material waste.
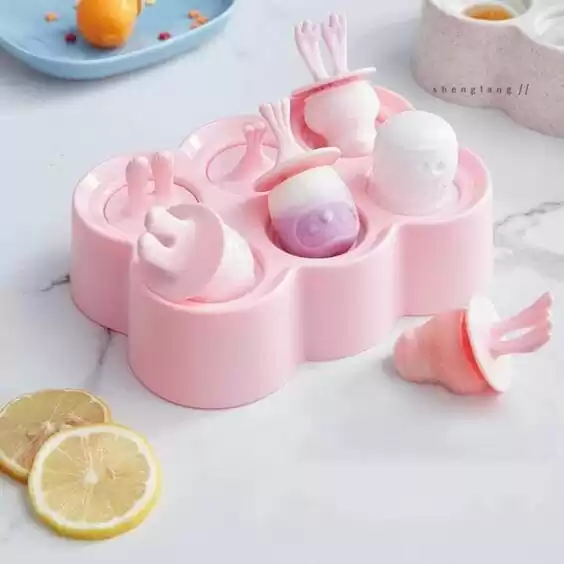
By implementing these strategies, manufacturers can achieve significant reductions in energy consumption, increase production efficiency, and minimize their environmental impact.
III. Compression Molding Versus Injection Molding Silicone?
Although silicone rubber compression molding is a widely-used production method, injection molding also has its benefits and drawbacks that should be taken into account when selecting one over the other.
Compression molding is a technique for shaping silicone rubber material through high pressure and heat. This method works best when creating large parts with intricate designs or parts with varied thicknesses; however, it can be slower and less efficient.
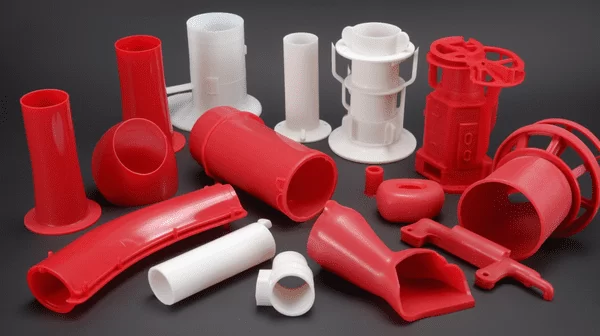
On the other hand, injection molding silicone involves injecting material into a cavity under intense pressure. This method is ideal for producing parts with excellent precision and consistency as it’s faster and more efficient than compression molding. However, it may not be ideal for large parts or those with varying thicknesses.
Compression molding offers several advantages, such as producing large parts with varying thicknesses and intricate designs. Furthermore, may be cost-effective for lower-volume production runs; however, it may not be ideal for high-volume production runs.
Injection molding silicone offers several advantages over compression moldings, such as high precision and consistency in parts, high volume production runs, and parts with complex geometries. On the downside though, injection molding silicone may be more costly and require more complex equipment than compression molding.
Finally, the decision between compression molding and injection molding silicone depends on several factors such as the size and complexity of the part being produced, desired production volume, and available equipment and resources.
IV. Enhancing Production Efficiency in Compression Molding
As efficiency is essential in silicone rubber compression molding, increasing production efficiency is equally essential for manufacturers. Here are some strategies that can be employed to boost production efficiency:
Three Ways to Reduce Production Time in Compression Molding
Manufacturers can decrease production time by using fast-curing materials, optimizing design, and using high-speed compression molding machines. These strategies help increase production rates while decreasing cycle times.
Importance of Mold Flow Analysis and the Design Process
Mold flow analysis can assist in optimizing the design of and decreasing production time. By analyzing material flow inside the mold, manufacturers can identify areas where materials may get trapped, leading to defects or slowing down production. Furthermore, optimizing mold design improves overall efficiency throughout the molding process.
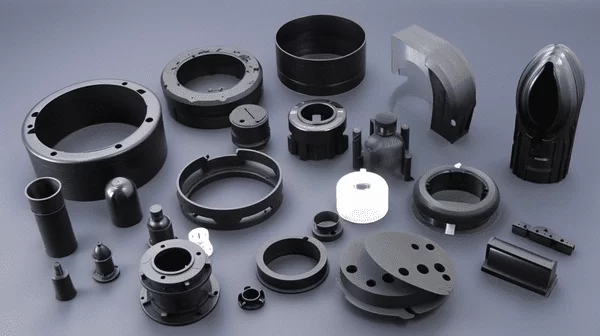
Introduction of Flexible Energy Use
Companies can adjust their energy consumption according to production demands by installing sensors and control systems that adjust based on production rate. This ensures efficient usage of resources.
Utilization of New Heating Technology
Modern heating techniques, such as electromagnetic induction heating, can more efficiently heat molds than traditional methods; this reduces energy consumption and enhances production efficiency.
Stable Production Management and Equipment Maintenance
Ensuring reliable production management and equipment maintenance can help prevent production interruptions and minimize downtime. This is accomplished by creating an appropriate maintenance schedule, monitoring the performance of the equipment, and training operators on how to identify and fix problems quickly.
These strategies can help manufacturers boost their production efficiency, shorten production times and optimize energy use.
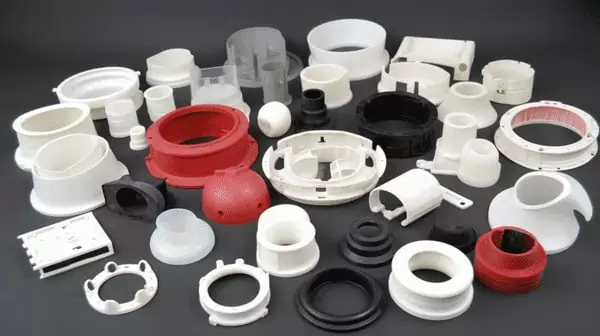
Conclusion
Finally, energy efficiency in silicone rubber compression molding is critical for manufacturers who wish to reduce costs and have a minimal environmental impact. By employing energy-saving strategies such as using energy-saving drive systems, adopting auxiliary molding technology, utilizing energy regeneration systems, and optimizing heating/cooling processes accordingly, manufacturers can significantly reduce their energy consumption and waste output.
In addition to energy efficiency, manufacturers can boost their production efficiency through strategies such as flow analysis, flexible energy use, and stable production management and equipment maintenance. Doing so allows them to produce high-quality silicone rubber products efficiently and sustainably.
Overall, the significance of energy efficiency in silicone rubber compression molding cannot be overemphasized. By adopting energy-saving strategies, manufacturers can reduce costs, minimize their environmental impact, and remain competitive in the market. With the continued advancement of new technologies and processes, achieving energy efficiency through silicone rubber compression molding will become even more essential over time.