Introduction
Silicone rubber compression molding is a versatile and widely-used manufacturing process known for its ability to produce high-quality rubber products. At the heart of this process lies the mold design, a critical factor that significantly impacts the final product’s quality and efficiency.
In this comprehensive article, we will delve into the intricate world of silicone rubber compression molding mold design. We will explore the importance of mold design and its pivotal role in achieving success in this manufacturing process. Throughout the article, we will cover the key steps involved in mold design, important considerations, and address common questions to help you gain a comprehensive understanding of this fascinating and essential aspect of silicone rubber compression molding. Whether you’re a seasoned professional or just starting in the field, this guide aims to provide valuable insights that will aid you in creating top-notch molds for your silicone compression molding projects. Let’s embark on this journey through the intricacies of mold design and unlock the secrets to producing impeccable silicone rubber products.
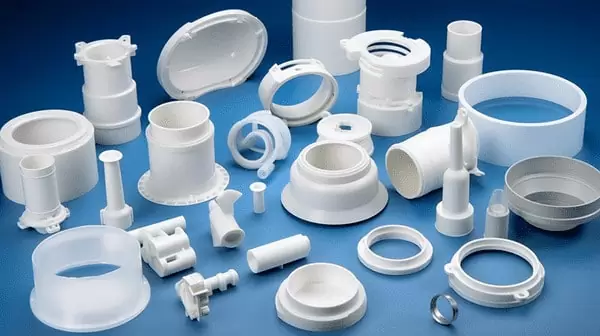
II. How Do You Design Compression Molding?
Designing a silicone rubber compression molding mold is a meticulous process that involves several crucial steps. Let’s break down each step to help you create a mold that ensures high-quality outcomes for your silicone compression molded rubber molding projects:
Step 1: Define Product Requirements
Before diving into mold design, it’s imperative to establish a clear understanding of your product’s specifications. This initial step sets the foundation for the entire process:
Material Selection: Determine the type of silicone rubber that aligns with your project requirements. Consider factors such as hardness, temperature resistance, and durability.
Product Geometry: Define the precise size, shape, and complexity of the rubber component you intend to manufacture.
Tolerances and Specifications: Specify critical dimensions, tolerances, and any other requirements essential for your product’s functionality and quality.
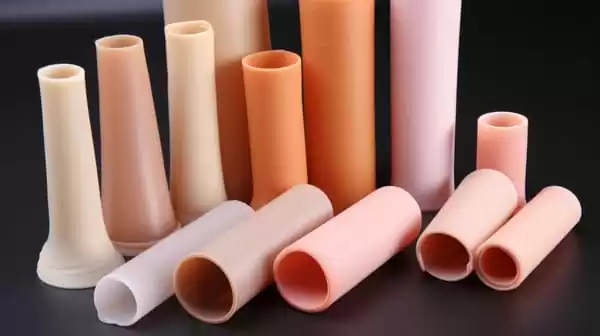
Step 2: Select the Mold Type
The choice of mold type is a pivotal decision in the mold design process. Two primary mold types are commonly used in compression molding:
Open-Top Molds: These molds comprise two flat plates and are well-suited for simpler part geometries.
Closed Molds: Closed molds, also known as cavity molds, are more complex in design and can accommodate intricate part shapes and configurations.
Carefully consider your product’s design and complexity to determine the most suitable and transfer molding and type for your project.
Step 3: Choose the Mold Material
The material used to construct the mold is a critical factor that impacts production efficiency and durability. Common mold materials for silicone rubber compression molding include:
Aluminum: Lightweight and cost-effective, making it suitable for low to medium production volumes.
Steel: Known for its durability and longevity, ideal for high-volume production.
Tooling Board: Appropriate for rapid prototyping and short-run production.
Your choice of mold material should align with your production volume, budget, and specific project requirements.
Step 4: Design Mold Cavities and Runners
Mold cavities and runners play a pivotal role in the distribution of silicone rubber within the mold. Key considerations in this step include:
Cavity Design: Ensure that the mold cavity precisely matches the product’s geometry. Consider draft angles to facilitate the removal of the molded part.
Runner Design: Develop an efficient runner system that evenly distributes the silicone rubber material into the cavities, promoting uniform molding.
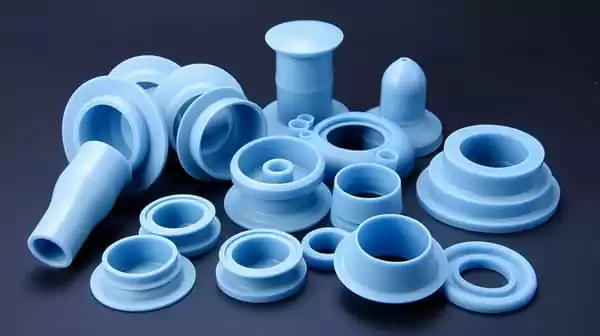
Step 5: Incorporate Venting and Vacuum
To achieve optimal results, it’s essential to address air entrapment during the compression molding process. Incorporating venting and vacuum systems is crucial:
Venting: Allows trapped air to escape from the mold cavity during compression, preventing defects in the final product.
Vacuum: Assists in material flow and minimizes voids, contributing to product quality.
Step 6: Implement a Cooling System
Efficient cooling is paramount for shortening cycle times and ensuring consistent part quality:
Cooling Channels: Design an effective cooling system, such as water channels or air vents, to regulate mold temperature during production.
Step 7: Consider Surface Finish
The surface finish of the mold directly impacts the quality of the final product. Depending on your product’s requirements, you may opt for:
Polished Finish: Ideal for products with smooth surfaces.
Textured Finish: Suitable for products that require texture or grip.
Matte Finish: Provides a non-reflective surface.
Step 8: Plan for Mold Maintenance
Regular mold maintenance is essential for prolonging the mold’s lifespan and ensuring consistent product quality:
Cleaning: Establish a cleaning regimen to remove residual rubber and other contaminants.
Lubrication: Apply appropriate lubricants to movable parts to prevent wear and friction.
Inspection: Regularly inspect the mold for wear, damage, or signs of fatigue.
By following these eight essential steps, you can design a silicone rubber compression molding mold that aligns with your product’s requirements and ensures efficient, high-quality production. Remember that mold design is a collaborative effort that involves mold designers, engineers, and manufacturers, all working together to achieve the best possible results for your project.
III.How Do You Make Silicone Rubber Molds?
Creating silicone rubber molds is a crucial part of the silicone rubber compression molding process. Proper molding methods part-making ensures that you can accurately replicate your desired silicone components. Here are the essential steps to create silicone rubber molds:
Step 1: Prepare a Master Pattern
Master Pattern: Start with a master pattern, which serves as a template for the final silicone component. This pattern can be made from various materials, such as metal, plastic, or other suitable materials, depending on your project’s requirements.
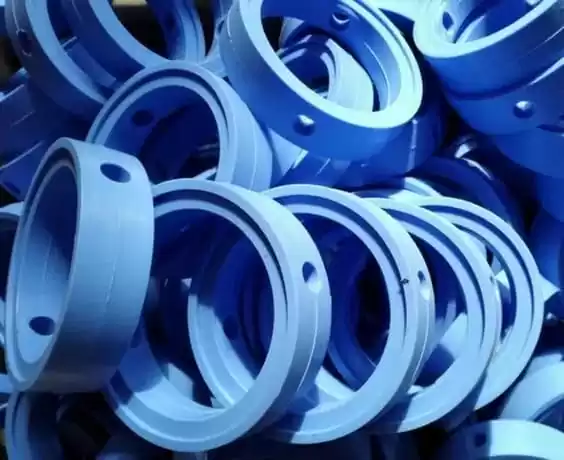
Step 2: Build a Mold Box
Mold Box: Construct a mold box or containment structure around the master pattern. The mold box contains the liquid silicone rubber (LSR) during the pouring and curing process. Ensure that the mold box is adequately sealed to prevent any leakage.
Step 3: Select Silicone Material
Silicone Material: Choose an appropriate silicone rubber material for your heated compression molding press. Consider factors like the mold’s intended use, flexibility, and durability. It’s essential to select a material compatible with the silicone compression molding process.
Step 4: Pouring and Curing
Pouring and Curing: The actual molding process involves pouring the selected silicone material into the mold box, covering the master pattern entirely. Make sure to follow the manufacturer’s instructions for mixing and pouring the silicone material accurately. After pouring, allow the silicone to cure and harden over the prescribed time, typically at room temperature or under controlled curing conditions.
Step 5: Demolding
Demolding: Once the silicone has fully cured, carefully demold the newly created silicone rubber mold. This process reveals the negative impression of the master pattern within the mold. Take care not to damage the mold during demolding, as it will be used for the silicone compression molding process.
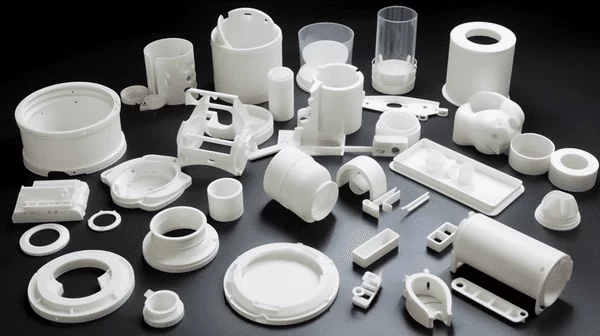
By following these five essential steps, you can create high-quality silicone rubber molds tailored to your specific project needs. These molds serve as the foundation for the silicone compression molding process, ensuring that you can consistently produce silicone components that meet your desired specifications. Proper mold-making is a critical factor in achieving successful outcomes in silicone rubber compression molding.
IV.Advantages of Silicone Rubber Compression Molding
Silicone rubber compression molding offers several significant advantages that make it a preferred manufacturing method for various industries and applications. Here are the key advantages to consider:
1. Cost Savings and Suitability for Prototypes
Silicone rubber compression molding presents a cost-effective solution for both small-scale production and prototyping:
Lower Tooling Costs: Compared to injection molding, silicone compression molds typically have less costly tooling upfront. This cost-effectiveness is especially advantageous for producing prototypes or short production runs.
Cost-Efficient Material Usage: The compression molding process minimizes material wastage, ensuring that you get the most out of your silicone rubber material.
Ideal for Small Production Runs: If you require small quantities of parts or components, silicone compression molding allows for efficient and economical production.
2. High-Quality Surface Finish
One of the distinctive features of silicone rubber compression molding is its ability to produce products with exceptional surface quality:
- Smooth and Uniform Finish: Silicone compression molds are known for creating parts with smooth and consistent surface finishes. This reduces or eliminates the need for extensive post-production finishing processes, saving time and costs.
- Texture Options: If your product requires a specific texture or grip, silicone compression molding can accommodate various surface textures, ensuring your product meets the desired specifications.
- Matte or Glossy Finishes: Depending on your project’s requirements, you can achieve either matte or glossy surface finishes, enhancing the aesthetics of your final product.
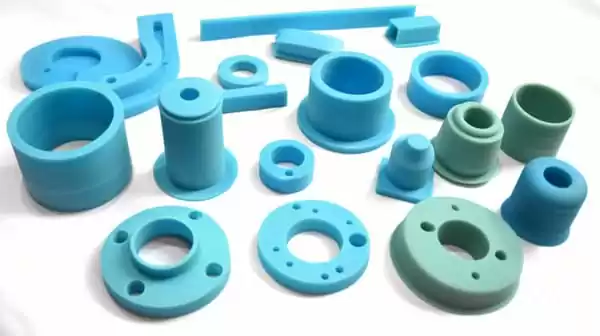
3. Temperature Resistance and Aerospace Applications
Silicone rubber’s inherent temperature resistance makes it an ideal choice for demanding applications, including those in the aerospace industry:
- Extreme Temperature Tolerance: Silicone rubber can withstand a wide range of temperatures, from very low to high extremes. This versatility allows it to excel in aerospace applications where components must function reliably under challenging conditions.
- Mechanically Demanding Environments: Components produced through silicone compression molding can handle mechanically demanding aerospace environments, offering durability and performance.
- Aerospace-Grade Components: Silicone compression molding is commonly used to produce critical aerospace components such as gaskets, seals, and insulation materials, where temperature resistance and reliability are paramount.
In conclusion, the advantages of silicone rubber compression molding extend beyond cost savings and include the production of high-quality, temperature-resistant components suitable for aerospace applications. Whether you’re aiming for efficient prototypes, aesthetically pleasing surface finishes, or robust components for aerospace, silicone compression molding is a versatile and reliable manufacturing method that meets these demands while ensuring cost-effective production.
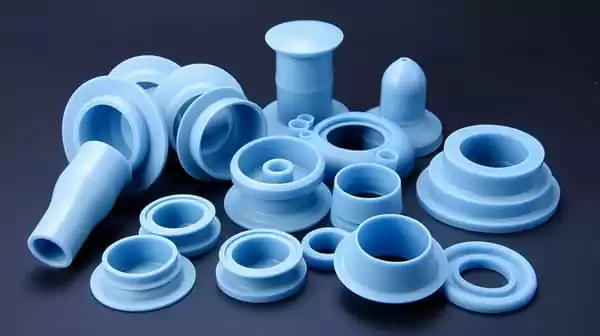
Conclusion
In this comprehensive exploration of silicone rubber compression molding mold design, we’ve journeyed through the intricacies of creating molds that play a pivotal role in the production of high-quality silicone components. To recap, let’s revisit the key takeaways from our discussion:
We began by understanding the significance of proper mold design in the silicone compression molding process, recognizing that it forms the very foundation of successful production. With meticulous attention to detail and adherence to best practices, you can design a mold that aligns with your product’s requirements, whether you’re crafting cost-effective prototypes, components for industrial applications, or aerospace-grade parts.
We then delved into the step-by-step process of mold design, where we emphasized the critical importance of defining product requirements, selecting the appropriate mold type, choosing the right mold material, and designing efficient cavities and runners. The incorporation of venting and vacuum systems, an efficient cooling system, surface finish considerations, and planned mold maintenance were also underscored as essential elements of the design process.
Furthermore, we answered common questions, addressing the use of silicone in compression molding, the creation of silicone rubber molds, and the calculation of compression molding tonnage. These insights shed light on the versatility and suitability of silicone in various applications, from consumer goods to aerospace components.
In closing, it cannot be stressed enough that proper mold design is the cornerstone of silicone rubber compression molding. It dictates the quality, efficiency, and reliability of the manufacturing process. By following the steps and considerations outlined in this article, you have the tools and knowledge to design molds that yield consistent, high-quality silicone products. Whether you’re driven by cost savings, innovative design, or precise functionality, remember that mold design is an art and a science, and mastering it can lead to remarkable achievements in the world of silicone compression molding.