Introduction
Silicone rubber compression molding is a favored manufacturing technique used across numerous industries, such as automotive, medical, and electronics. This technique involves placing raw silicone material in a compression molds before heating and pressurizing it to form desired shapes – often producing high-quality parts with excellent mechanical properties.
In this article, we will compare silicone rubber compression molding with other processes such as injection and transfer molding. Additionally, we will highlight its advantages, along with different silicone compression molding and processes as well as keywords and questions relevant to this subject matter.
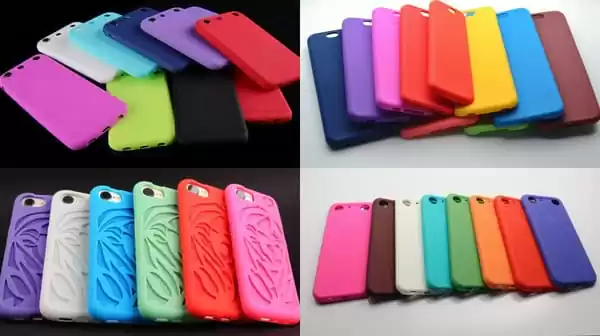
Ⅱ. Comparison of Compression Molding and Injection Molding for Silicone Rubber
Compression molding and injection molding are two popular processes used for silicone molding. Here is a comparison between them:
Compression molding:
Compression molding involves placing raw silicone material in a mold cavity and applying heat and pressure, followed by cooling to remove any excess material. Compression molding is best used for low to medium-volume production as it produces parts with excellent mechanical properties while potentially prolonging cycle times and labor costs.
Injection Molding:
For this process, raw silicone material is heated and injected directly into a mold cavity using an injection molding machine. Once the mold has cooled down, any excess material is removed employing vacuum suction and removed manually from the mold cavity. Injection molding is well suited for high-volume production as it produces parts with precise dimensions and complex shapes at lower costs than traditional methods – yet may incur higher tooling costs and require significant upfront investments to begin production.
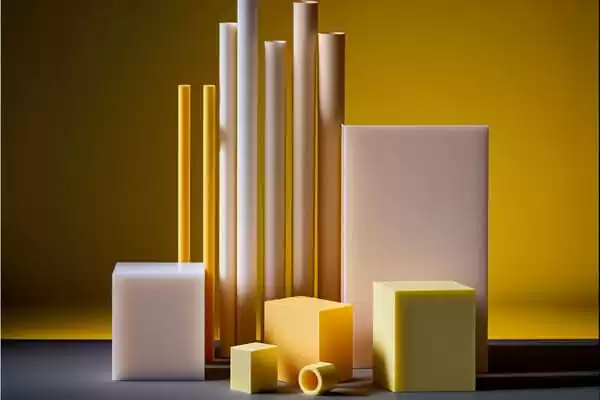
When to Use Each Process for Silicon Rubber Molding:
Compression molding is best used for low to medium-volume production where precise tolerances and mechanical properties are essential, while Injection Molding excels in high-volume environments where speed, efficiency, precision, and complex shapes are desired.
Compression molding and injection molding are both proven methods for silicone rubber molding; choosing between them depends on production requirements and volume requirements.
Ⅲ.Advantages of Silicone Rubber Molding
Silicone rubber molding offers several distinct advantages over other materials and manufacturing processes, such as printing processes. Here are a few benefits of silicone rubber molding:
Silicone rubber’s versatility makes it ideal for use across various industries – automotive, medical and electronics are among them.
Silicone rubber can withstand high temperatures, making it suitable for use in environments like automobile engines or industrial machinery.
Silicone rubber molding creates parts with an excellent surface finish, which is essential for applications like medical devices and electronic components.
Silicone rubber has proven its chemical resistance through exposure to harsh substances without degrading or corroding over time.
Silicone rubber parts possess outstanding mechanical properties, including elasticity, tear-resistance, and durability.
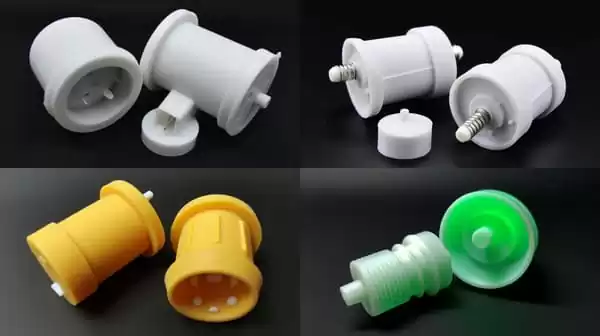
Silicone rubber molding has long been used in various industries due to its versatility, high-temperature resistance, and exceptional mechanical properties. Silicone is often employed in seals, gaskets, O-rings, wire insulation applications, medical devices, etc.
Overall, silicone rubber molding offers numerous advantages that make it a reliable and efficient manufacturing process for various industries and applications.
Ⅳ.Alternative Processes to Compression Molding
While compression molding is a widely-used method for silicone rubber molding, there are other processes available as alternatives to compression molding: Here are three:
Transfer molding:
Transfer molding is similar to compression molding, except the material is preheated in a transfer pot before being transferred directly into the mold cavity. This method is suitable for producing intricate designs with multiple cavities; however, this process may be more expensive and may cause longer cycle times than its compression-molding counterpart.
Liquid Injection Molding (LIM):
Liquid injection molding is a process where liquid silicone rubber is injected under high pressure into a heated mold cavity and placed directly against a surface, producing parts with precise dimensions and complex geometries, but at an expense similar to compression molding.
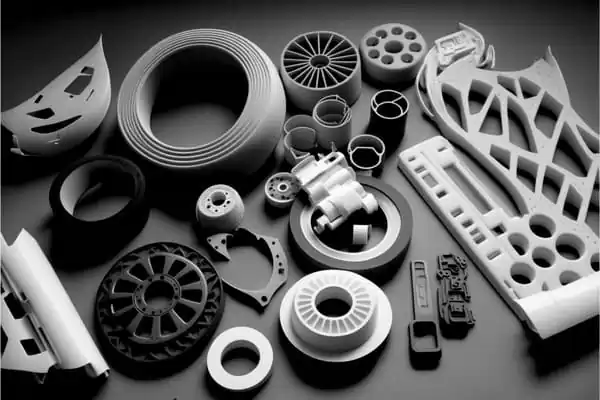
Extrusion molding:
Extrusion molding involves forcing raw material through a heated die to produce parts with consistent cross sections, such as tubing or gaskets, while this method may not be ideal for creating intricate geometries with tight tolerances or complex geometries.
Comparable to compression molding, alternative processes may offer advantages like faster cycle times and higher precision for producing complex geometries. But they may also carry with them additional tooling and material costs as well as longer lead times and more complex supply chains.
At the core, selecting an optimal molding process depends upon a consideration of application requirements and production volume needs. Before making a choice, it’s crucial that we carefully weigh up both advantages and disadvantages associated with each method before reaching our decision.
Ⅴ. Different Types of Compression Molding Processes
There are various compression molding processes used for silicone rubber molding. Here are a few of the more popular methods:
Rubber compression molding: This technique involves compressing raw rubber material into a mold cavity, heating it until curing takes place, and then extracting any surplus material from the mold cavity. Rubber compression molding can produce large parts with high precision and mechanical strength for use as engine mounts and seals.
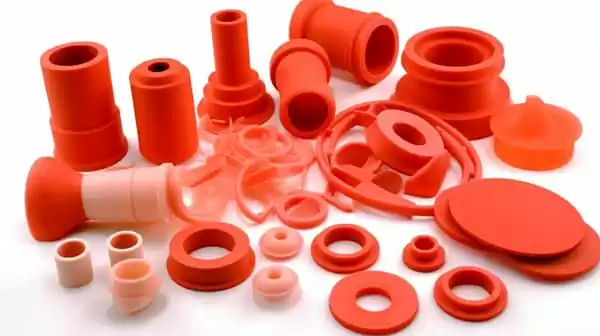
Liquid silicone rubber (LSR) injection molding: LSR injection molding is similar to liquid injection molding but uses liquid silicone rubber. The raw material is injected under high pressure and heat into a mold cavity and then cured to create the part desired. LSR molding can produce complex geometries or parts with tight tolerances such as medical devices and electronic components with ease.
High consistency rubber (HCR) compression molding: This process entails heating raw HCR material, compressing and curing it to form the final part. HCR compression molding is perfect for producing parts with high mechanical strength such as gaskets and seals.
Each type of compression molding has its own set of advantages and disadvantages. Rubber compression molding offers high mechanical strength and precision while LSR injection molding has superior precision for creating complex geometries. HCR compression molding offers an ideal balance between strength and flexibility when applying it in applications where this balance is necessary.
Selecting an optimal compression molding process for silicone rubber molding ultimately depends on application needs and desired characteristics of the final part. When selecting a molding process, factors like mechanical strength, precision, and complexity must all be taken into account.
Conclusion
silicone rubber compression molding is an efficient and reliable manufacturing process used in various industries. It offers many advantages such as versatility, temperature resistance, and superior mechanical properties; yet some drawbacks such as longer cycle times and higher labor costs than alternative processes must also be considered.
Transfer molding, liquid injection molding, and extrusion molding can provide alternatives to compression molding for silicone rubber molding applications. Each of these processes offers its own set of benefits and drawbacks that must be considered depending on specific application needs. liquid silicone injection molding
Compression molding processes come in various forms, such as rubber injection molding, compression molding, LSR injection molding, and HCR compression molding. Each has its own set of advantages and drawbacks that should be carefully considered based on what characteristics should define the final part.
Choose the optimal silicone rubber molding process depending on your application requirements for mechanical strength, precision, and complexity. Careful consideration must be made of each process’s advantages and disadvantages before making a final choice; doing this ensures manufacturers use the optimal process to produce high-quality parts efficiently with efficient production rates.