Introduction
Silicone rubber is an extremely flexible material used in various industries and applications. Being aware of its properties is key for selecting the appropriate material and meeting specifications, and we aim to demystify silicone rubber like material’s many properties, including physical and chemical characteristics, tensile properties, silicon’s effect on rubber properties, and how these can be improved; we will also discuss its many applications and their possible improvements by the end of this article. By the time you leave this read you should have an enhanced knowledge of silicone rubber compression material properties as well as their significance across industries!
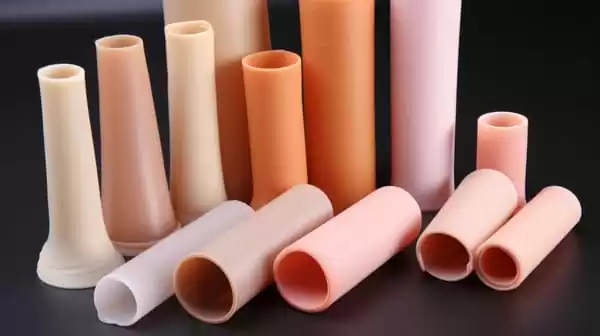
II. What are the properties of silicone rubber material?
Definition of silicone rubber
Silicone rubber is a synthetic elastomer composed of silicone polymers with organic groups attached to silicon atoms, known for its excellent thermal and electrical insulation properties, chemical attack resistance, extreme temperature tolerance, and flexibility. Highly resilient materials that maintain structural integrity across a broad temperature spectrum from very low to extremely high temperatures; its chemical structure features long polymer chains with the carbon-to-carbon backbone that gives this substance its special properties.
Physical and chemical properties of silicone rubber
Silicone rubber boasts an attractive combination of physical and chemical properties that makes it highly desirable in a range of applications. Some key physical characteristics of organic rubber include:
Silicone rubber offers excellent thermal stability, making it suitable for use in high-temperature applications.
Silicone rubber offers excellent electrical insulating properties, making it suitable for applications where electrical conductivity must be limited.
Silicone rubber offers excellent weather resistance, making it suitable for use in outdoor applications. Silicone can withstand UV rays, ozone levels and other environmental elements without degradation – an attribute which makes it perfect for use as outdoor flooring material.
Silicone rubber offers excellent flexibility and can bend and stretch without breaking, making it suitable for applications where flexibility is a must.
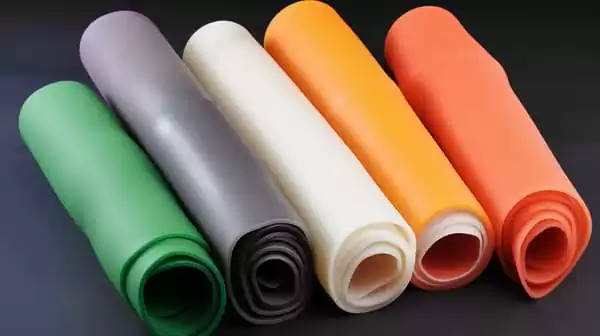
Silicone rubber boasts several key chemical and physical properties that contribute to its functionality:
Chemical Resistance: Silicone rubber has proven its resilience against chemical attack by withstanding exposure to various types of chemicals without succumbing to degradation.
Silicone rubber offers exceptional resistance to mineral oils, making it suitable for oil and gas applications.
Silicone rubber’s resistance to chlorinated hydrocarbons makes it useful in applications where these chemicals may be present, making it suitable for applications where this environment exists.
Comparison of silicone rubber to other natural rubber
Silicone rubber stands out among other elastomers such as natural rubber and nitrile rubber with its many distinct properties that set it apart.
Silicone rubber boasts an extremely broad temperature range compared to natural or nitrile rubbers, enabling it to withstand both extremely low and high temperatures without losing structural integrity.
Silicone rubber provides excellent electrical insulation properties, unlike natural and nitrile rubbers. This also makes silicone rubber suitable for applications where electrical conductivity must be reduced as much as possible.
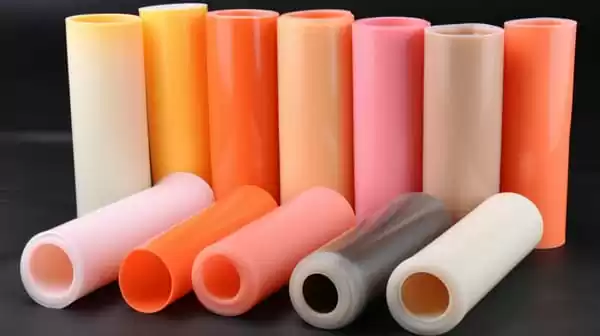
Silicone rubber offers superior chemical resistance to natural rubber and nitrile rubber. It can withstand exposure to an extensive selection of chemicals without degrading.
Silicone rubber has excellent UV, ozone, and weather exposure resistance which makes it suitable for use outdoors.
At its core, silicone rubber stands out for its wide temperature range, excellent electrical insulation properties, and resistance to chemical attacks and extreme environments.
III. Tensile properties of silicone rubber
Tensile properties of silicone rubber
Tensile properties refer to a material’s ability to withstand stretching or pulling forces without breaking, with silicone rubber boasting exceptional tensile properties that make it highly sought-after in many applications.
Silicone rubber boasts exceptional elongation at break, meaning that it can stretch to an extended extent before breaking, as well as high tensile strength that allows it to withstand stress without cracking under pressure.
Silicone polymers’ molecular structures play a crucial role in their tensile properties, particularly their high tensile strength and elongation at break. Silicone is comprised of relatively long polymer chains joined together by carbon-to-carbon backbones; these long chains give silicone rubber its distinctive strength properties such as high tensile strength and elongation at break.
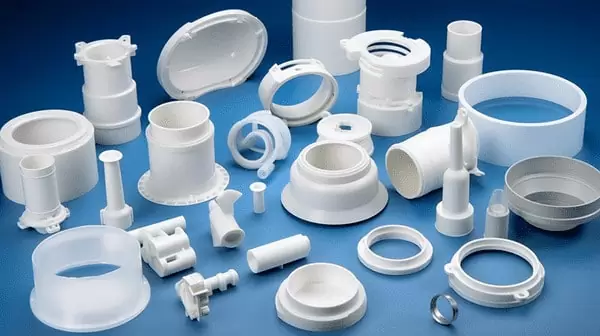
As previously discussed, silicone rubbers can be tailored to possess specific tensile properties by altering the molecular structures of polymer chains. As one example, room temperature vulcanized (RTV) silicone rubbers typically exhibit lower tensile strengths than heat-cured options.
Silicone rubber’s unique tensile properties make it an excellent material choice for applications requiring flexibility and durability, such as those found in the automotive or aerospace industries.
How the molecular structure of silicone polymers affects these properties
Silicon polymers play an important role in determining their tensile properties, with chains consisting of alternate silicon and oxygen atoms attached by organic groups to each silicon atom.
The length of polymer chains influences both elongations at break and tensile strength in silicone rubber. Longer polymer chains tend to increase material elongation at break but may reduce tensile strength; conversely, shorter chains increase strength while simultaneously decreasing its elongation at break.
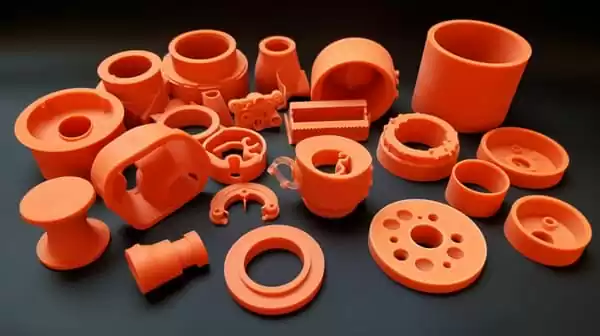
Organic groups attached to silicon atoms also influence a material’s tensile properties, altering its elongation at break and increasing the flexibility and elasticity of polymer chains; they may also decrease bonding between polymer chains, diminishing strength.
IV. Effect of silicon on rubber
Silicone rubber materials modified to enhance their properties
Silicone rubber materials can be altered to increase their properties and make them suitable for specific applications. One method for changing silicone rubber’s properties is altering its chemical composition – typically by adding fillers such as carbon black or silica to it – which will change its polymer chains’ chemical makeup, thus improving mechanical properties such as stiffness, strength and abrasion resistance.
Additives are another effective way to transform silicone rubber. Additives can increase its elasticity, decrease its compression set or enhance electrical properties – for instance platinum catalysts can speed up curing times while producing uniform results.
Silicone rubber can also be modified by altering its curing process. Room temperature vulcanized (RTV) silicone rubbers, for example, are typically cured at room temperature rather than using heat curing technology; these types of RTV silicone rubbers feature lower tensile strengths than their heat-cured counterparts but boast highly flexible characteristics with excellent electrical insulation properties, making them suitable for electronics industry use.
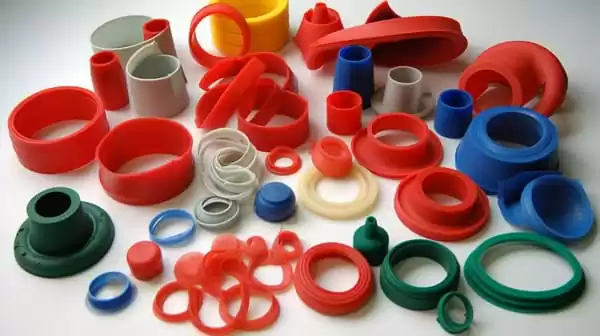
Silicone rubber materials can be altered using various other modified silicone rubber and polymers. Liquid silicone rubber (LSR), for instance, is an extremely flexible material that can be formed into complex shapes while solid silicone rubber provides higher tear strength and abrasion resistance for applications requiring high tear strength or resistance against tear or abrasion resistance.
Modifying silicone rubber materials can improve their properties and make them suitable for a range of applications, with engineers and manufacturers understanding how these modifications work to select an optimum material for specific projects.
Liquid silicone rubber and solid silicone rubber differ in terms of their properties and uses
Liquid silicone rubber (LSR) and solid silicone rubber differ significantly due to their molecular structures, with LSR having lower viscosity and being highly fluid for easy molding of complex shapes, as well as being highly resistant to heat, cold, UV light and other external influences that would normally limit outdoor usage. Solid silicone rubber on the other hand offers more rigid properties which make it suitable for applications requiring high tear strength or abrasion resistance while remaining chemical- and temperature resistant – perfect for outdoor applications!
LSR rubber is widely utilized across industries like healthcare, automotive and electronics due to its exceptional flexibility, electrical insulation properties and biocompatibility. Furthermore, food processing applications utilize this material due to its extreme temperature resistance and chemical stability properties.
Solid silicone rubber is often utilized for gaskets, seals, and O-rings due to its superior tear strength, abrasion resistance, chemical stability and tear strength. Furthermore, aerospace industry applications include engine gaskets and insulation. Due to its resistance against extreme temperatures it also finds use as engine gaskets or insulation materials.
LSR and solid silicone rubber can both be modified to improve their properties for specific applications, making them suitable for particular uses.
Curing process and how it affects the final properties of silicone products
Curing is a key step in the production of silicone rubber products. Curing involves cross-linking polymer chains into one solid mass; its rate can be affected by factors like temperature and humidity levels as well as using curing agents or catalysts.
Curing processes have an enormous effect on the final properties of silicone products. Heat-cured rubbers tend to possess greater tensile strength and rigidity compared to room temperature vulcanized (RTV) versions, which offer greater flexibility while providing excellent electrical insulation properties.
Curing processes can also have an impactful impact on the mechanical properties of silicone products. A longer curing time could result in more robust and durable product features while shorter curing times could produce a more flexible solution.
Curing agents or catalysts may also have an effect on the final properties of silicone products, for instance platinum catalysts are often used to speed up and uniformise cure times of silicone materials.
Overall, curing processes play a pivotal role in defining the final properties of silicone products. By understanding how their effects translate to product properties, manufacturers can select an optimal curing method and achieve performance and reliability goals with their products.
V. Improving the properties of silicones
Silicone rubber materials can be altered to enhance their properties and make them suitable for specific applications. One way to alter silicone rubber’s chemical composition involves changing its polymer chains; this can be accomplished by adding fillers like carbon black or silica fillers into its chemical makeup, which will increase stiffness, strength, and abrasion resistance of its mechanical properties.
Additives can also be a great way to alter silicone rubber by improving its properties, including increasing elasticity, decreasing compression set, or improving electrical properties. Platinum catalysts may even speed up curing times while creating more uniform cure times.
Liquid silicone rubber (LSR) and solid silicone rubber differ due to their various molecular structures, with LSR having lower viscosity and being highly fluid for molding complex shapes; LSR is also highly resistant to heat, cold, UV light exposure as well as outdoor elements like UV light. Conversely, solid silicone rubber offers higher tear strength, abrasion resistance as well as chemical and temperature resistance which make it suitable for outdoor applications.
Curing silicone rubber is essential to its final properties. The curing process involves cross-linking polymer chains into solid materials. Temperature, humidity, and curing agents or catalysts all affect its progress; heat-cured rubber has higher tensile strength and rigidity than RTV silicone rubbers which have excellent flexibility and electrical insulation properties.
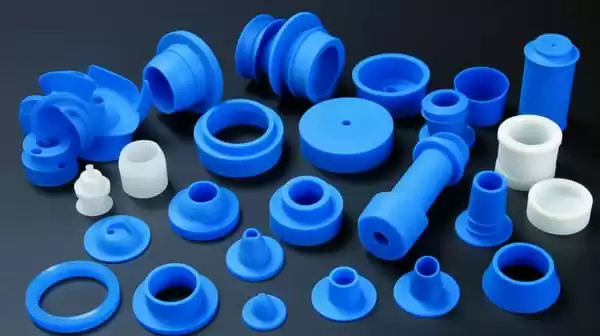
Overall, silicone rubber modification can greatly increase their properties and suit a range of applications. By understanding how silicone rubber materials can be modified, engineers and manufacturers can select the suitable material and curing process for their particular use case.
VI. Applications of silicone rubber
Silicone rubber has many applications in various industries and applications due to its unique properties. Due to its heat resistance, chemical resistance, and electrical insulation properties, silicone rubber makes an excellent material choice for use in industries like automotive, aerospace, and electrical.
Silicone rubber has long been employed in medical device production, such as catheters, seals and implants. Due to its biocompatibility and flexibility, an ideal material for such uses. Silicone rubber also finds widespread use in food processing due to its resistance to extreme temperatures and chemical stability.
Silicone rubber is widely utilized within the oil and gas industry for seals, gaskets and other applications exposed to harsh environments, due to its resistance against mineral oils and chlorinated hydrocarbons. Furthermore, this material boasts excellent electrical insulation properties which make it suitable for electric motors and other components that use this material.
Overall, silicone rubber’s properties make it an ideal material for an array of uses across industries. Its resistance to extreme temperatures, chemical attack and electrical conductivity make it highly versatile material suitable for a range of uses.
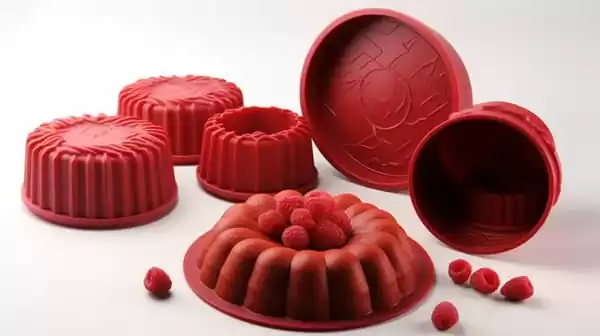
Conclusion
silicone rubber materials possess unique physical and chemical characteristics that make them highly desirable for many different applications. Their exceptional tensile strength, electrical insulation properties and resistance to chemical attack and extreme temperatures make them suitable for use across industries including automotive, aerospace and electrical.
Understanding the properties and modifications available to silicone rubber materials are vital for engineers and manufacturers, in order to increase performance and reliability in their products. By selecting appropriate material and adapting its properties accordingly, engineers can select optimal material which will result in enhanced performances for specific applications.
Exploration of silicone rubber materials and their properties to unlock their full potential across industries is highly encouraged. Understanding their properties is key in selecting the ideal material for your application and achieving desired performance and reliability.