Introduction
Silicone rubber molding plays a vital role in various industries, providing exceptional versatility, durability and resistance to heat and chemicals. This manufacturing process has revolutionized production of automotive parts, electronics, medical devices and consumer goods as it can create complex shapes with tight tolerances that suit various applications.
Innovation in silicone rubber molding equipment is key to meeting the ever-evolving demands of industries and remaining relevant in a competitive market. Innovations in equipment technology not only increase production efficiency and productivity but also enable the production of higher-quality silicone products with enhanced performance characteristics. By constantly innovating silicone rubber molding equipment manufacturers can open new possibilities and meet customers’ ever-evolving needs.
This article will explore the significance of silicone rubber molding across industries and examine why innovation in molding equipment is vital to keeping ahead in an increasingly dynamic market. Understanding this importance helps manufacturers realize its full potential while remaining at the cutting-edge of technology to remain at an advantage in an ever-evolving marketplace.
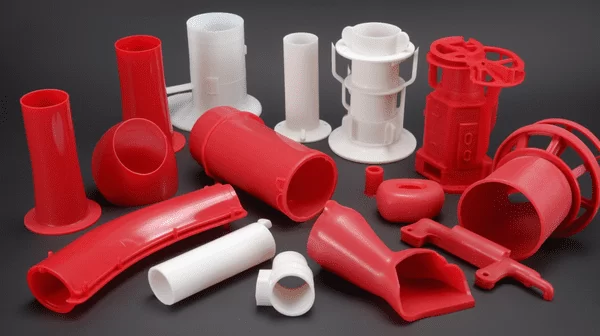
II. How do you manufacture silicone rubber?
Silicone rubber, including liquid silicone rubber (LSR), is manufactured through a precise and controlled process that involves several steps. Let’s explore the multi-step process and emphasize the significance of LSR and its two-component system.
Raw Material Preparation:
- Silicone polymer base: The silicone polymer, which provides the desired physical properties, is prepared by mixing various components such as silicone oil, reinforcing fillers, and additives. This mixture is typically in a liquid or gum form.
- Curing agent: A curing agent, also known as a cross-linker or catalyst, is added to the silicone polymer base. This agent initiates the chemical reaction responsible for curing and transforming the material into its final rubbery state
Mixing and Degassing:
- The silicone polymer base and curing agent are carefully measured and mixed together in precise ratios. This ensures the desired properties and curing characteristics of the final silicone rubber product.
- The mixture is then subjected to a degassing process to remove any trapped air or volatile components. This step is crucial for obtaining a high-quality, bubble-free material.
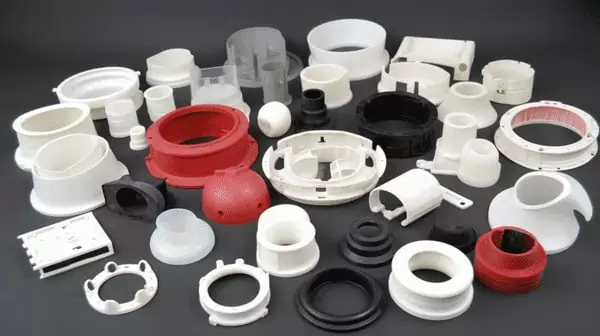
Injection Molding Process for LSR:
- LSR is commonly processed using an injection molding machine. The machine consists of an injection barrel and a plunger, where the LSR material is loaded.
- The LSR material is heated within the injection barrel to reduce its viscosity and facilitate the injection process.
- Once the material reaches the desired temperature, it is injected into a mold using high pressure.
The LSR material fills the mold cavity and takes the shape of the desired product.
Curing and Demolding:
After injection, the LSR material is allowed to cure in the mold. Curing can occur at room temperature (RTV) or under controlled heating conditions, depending on the specific requirements of the silicone rubber.
Once the curing process is complete, the mold is opened, and the cured silicone rubber product is demolded.
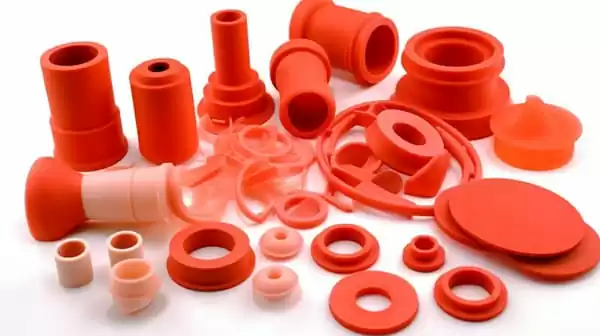
The demolded product may undergo additional post-processing steps such as trimming, inspection, and surface treatment, depending on its intended application.
Liquid silicone rubber (LSR) is particularly noteworthy due to its two-component system:
- The silicone polymer base and curing agent are separate components, which are mixed in precise proportions before the injection molding process.
- This two-component system allows for better control over the curing process, resulting in consistent and reliable production of silicone rubber products.
The ability to precisely control the mixing, degassing, injection, curing, and demolding processes is crucial to manufacturing high-quality silicone rubber products. By understanding the intricate steps involved in silicone rubber manufacturing, manufacturers can optimize their processes and produce innovative products that meet the diverse needs of various industries.
III. Methods of Silicone Molding
A. Introduction to different molding methods for silicone rubber:
Silicone rubber can be molded using various techniques, each offering unique advantages. Let’s explore some of the commonly used methods:
- LSR Molding Process:
- The injection molding process for liquid silicone rubber (LSR) involves injecting the LSR material into a mold under high pressure.
- This method offers precise control over the filling process, ensuring consistent part quality and tight tolerances.
- LSR injection molding is highly efficient, allowing for high-volume production of complex silicone rubber parts with excellent dimensional accuracy and surface finish.
- Two-Shot Molding:
- Two-shot molding, also known as multi-shot or overmolding, involves using two different materials or colors in a single mold.
- In silicone rubber two-shot molding, a primary material is injected first, followed by a second material, such as LSR, to create a composite product.
- This method enables the production of parts with multiple colors, textures, or varying hardness levels in a single molding cycle, reducing assembly steps and improving product aesthetics.
- Profiled Filling:
- Profiled filling is a molding technique used to achieve specific flow patterns of silicone rubber within the mold cavity.
- By strategically designing the mold cavity and incorporating flow control elements, such as restrictor pins or valve gates, manufacturers can control the flow of silicone rubber during injection.
- Profiled filling helps optimize material distribution, minimize waste, and improve part quality, particularly for complex geometries or thin-walled parts.
- Flash Prevention Techniques:
- Flash refers to excess material that escapes between mold components during the molding process, resulting in unwanted protrusions on the final part.
- Flash prevention techniques, such as using optimized mold designs, precise machine settings, and proper clamping force, help minimize flash formation.
- By controlling the injection pressure, temperature, and mold venting, manufacturers can achieve flash-free silicone rubber parts with tight dimensional control.
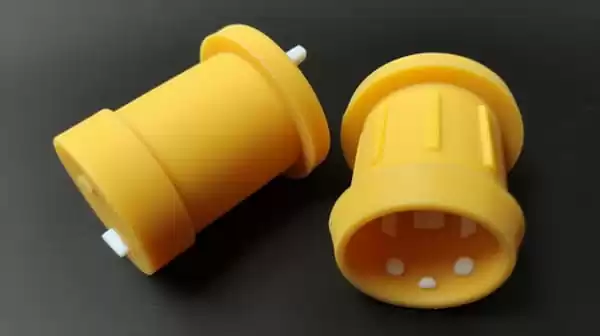
B. Brief explanation of each method and its benefits:
- Injection molding process for LSR allows for efficient, high-volume production of complex silicone rubber parts with excellent dimensional accuracy and surface finish.
- Two-shot molding enables the creation of composite parts with multiple colors, textures, or hardness levels, reducing assembly steps and enhancing product aesthetics.
- Profiled filling optimizes material distribution and minimizes waste, making it ideal for complex geometries or thin-walled parts.
- Flash prevention techniques minimize excess material and ensure tight dimensional control, resulting in high-quality silicone rubber parts.
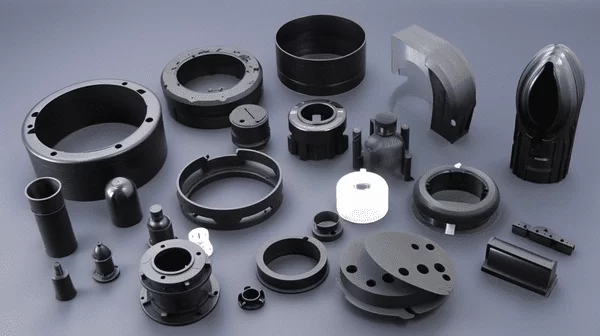
By understanding the various methods of silicone molding and their benefits, manufacturers can select the most appropriate technique for their specific product requirements. Each method offers unique advantages, contributing to the versatility and flexibility of silicone rubber molding.
IV. Innovations in Silicone Rubber Molding Equipment
A. Embracing Advanced Materials
- Introduction to advanced silicone formulations, additives, and fillers:
- Manufacturers are continually developing and utilizing advanced silicone formulations that offer enhanced properties and performance.
- Addition of additives and fillers, such as reinforcing agents or flame retardants, can further improve the characteristics of silicone rubber.
- Advanced materials impact the flow properties, curing times, and overall behavior of silicone rubber during the molding process.
- Impact on performance, flow properties, and curing times:
- Advanced materials allow for improved performance characteristics, including increased strength, flexibility, and resistance to heat or chemicals.
- Optimal flow properties of advanced materials enable better mold filling, resulting in high-quality parts with intricate details and minimal defects.
- Reduced curing times of advanced materials contribute to shorter cycle times, leading to higher productivity and cost-effectiveness in silicone rubber molding.
B. Integration of Automation and Robotics
- Benefits of automation in silicone rubber molding:
- Automation offers numerous advantages in the molding process, such as increased efficiency, productivity, and consistency.
- Automated systems can handle material preparation, injection, demolding, and post-processing tasks, reducing manual labor and human error.
- Integration of robotics enhances precision, allowing for more accurate placement of silicone rubber and reducing the risk of defects.
- Improved productivity, reduced cycle times, and enhanced precision:
- Automation and robotics enable higher productivity by optimizing process parameters and minimizing downtime between molding cycles.
- Reduced cycle times lead to faster production rates, allowing manufacturers to meet customer demands efficiently.
- Enhanced precision in silicone rubber molding equipment ensures consistent part quality and dimensional accuracy, meeting tight tolerances.
C. Real-Time Monitoring and Control
- Importance of implementing monitoring systems and data analytics:
- Real-time monitoring systems track and analyze critical process parameters, such as temperature, pressure, and curing profiles.
- Data analytics provide valuable insights to make informed decisions, optimize process parameters, and improve overall equipment performance.
- Monitoring and control systems enable proactive adjustments, ensuring consistent quality and identifying potential defects at an early stage.
- Proactive adjustments, process optimization, and defect detection:
- Real-time monitoring allows manufacturers to make timely adjustments to maintain optimal process conditions and enhance efficiency.
- Process optimization based on data analysis helps identify opportunities for improvement, leading to enhanced productivity and cost savings.
- Early detection of potential defects through monitoring and control systems minimizes waste, reduces scrap, and improves yield.
D. Enhancing Mold Design and Cooling Systems
- Exploring advanced mold designs and cooling techniques:
- Advanced mold designs, such as multi-cavity molds and hot runner systems, enable higher cavitation and increased productivity.
- Conformal cooling techniques utilize optimized cooling channels to improve heat transfer, reducing cycle times and enhancing part quality.
- Multi-cavity molds, hot runner systems, and conformal cooling:
- Multi-cavity molds allow simultaneous production of multiple parts, increasing output and efficiency.
- Hot runner systems eliminate the need for cold runners, reducing material waste and minimizing post-processing steps.
- Conformal cooling techniques optimize the cooling process by placing cooling channels closer to the part surface, ensuring uniform cooling and minimizing distortion.
E. Collaboration and Knowledge Sharing
- Encouraging partnerships with material suppliers, equipment manufacturers, and experts:
- Collaboration with material suppliers provides access to cutting-edge silicone formulations and additives.
- Partnerships with equipment manufacturers facilitate the adoption of innovative molding equipment and technologies.
- Engaging with experts in the field fosters knowledge sharing and exchange of ideas, driving continuous innovation in silicone rubber molding equipment.
- Exchange of ideas and experiences to drive innovation:
- By actively engaging in partnerships and knowledge sharing, manufacturers can stay updated with the latest industry trends and advancements.
- Collaborative efforts foster a culture of innovation, allowing for the exploration of new ideas, techniques, and approaches in silicone rubber molding equipment.
- Sharing experiences and best practices with industry peers helps identify challenges and find effective solutions, leading to continuous improvement and innovation.
By embracing advanced materials, integrating automation and robotics, implementing real-time monitoring and control systems, enhancing mold design and cooling systems, and fostering collaboration, manufacturers can drive innovation in silicone rubber molding equipment. These innovations enable improved performance, increased productivity, enhanced quality, and cost-effective production of silicone rubber parts. The pursuit of innovation in silicone rubber molding equipment is not only essential for meeting the evolving demands of various industries but also for staying competitive in a rapidly advancing market.
VI. Applications in the Medical Industry
A. Importance of silicone rubber molding in medical components and devices:
- Silicone rubber molding plays a critical role in the medical industry, providing numerous benefits for the manufacturing of medical components and devices.
- The unique properties of silicone rubber, such as biocompatibility, flexibility, and chemical resistance, make it an ideal material for medical applications.
- Molding equipment innovations enable the production of complex geometries, tight tolerances, and precise customization required for medical devices.
B. Examples of medical applications and the benefits of silicone rubber:
Medical Components: Silicone rubber is used in various medical components like seals, gaskets, O-rings, diaphragms, and connectors. It provides reliable sealing, flexibility, and resistance to chemicals and high temperatures, ensuring the integrity of medical devices.
Medical Devices: Silicone rubber is widely used in medical devices such as catheters, surgical instruments, respiratory masks, and implants. It offers exceptional biocompatibility, softness, and hypoallergenic properties, reducing the risk of adverse reactions and improving patient comfort.
Drug Delivery Devices: Silicone rubber is utilized in drug delivery devices like syringe plungers, infusion pump components, and inhalers. Its excellent adhesion and chemical resistance ensure precise drug dosage, while its flexibility enables smooth operation and ease of use.
Dental Applications: Silicone rubber is commonly used in dental applications, including impression materials, orthodontic appliances, and prosthetic components. Its accuracy in capturing dental impressions and biocompatibility make it an ideal choice for dental professionals and patients.
Wound Care Products: Silicone rubber is utilized in wound care products such as dressings and scar management sheets. Its non-adherent properties, breathability, and flexibility facilitate optimal wound healing and patient comfort.
The benefits of silicone rubber molding in the medical industry include:
Biocompatibility: Silicone rubber is well-tolerated by the human body, making it suitable for medical devices that come into contact with patients’ skin or internal tissues.
Chemical Resistance: Silicone rubber demonstrates excellent resistance to chemicals, disinfectants, and body fluids, ensuring the integrity and longevity of medical components.
Durability: Silicone rubber exhibits exceptional durability and can withstand repeated sterilization cycles, maintaining its performance over time.
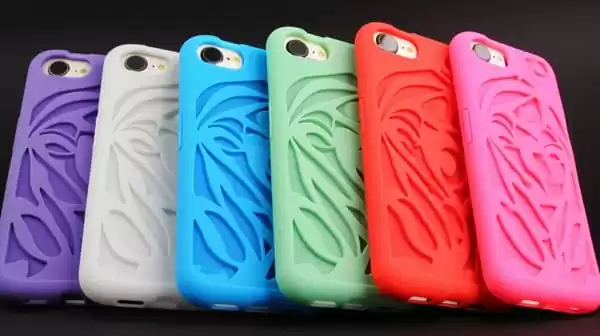
Tight Tolerances: Innovations in silicone rubber molding equipment allow for precise control over dimensions and tolerances, ensuring the accuracy and reliability of medical devices.
Customization: Silicone rubber can be molded into various shapes and sizes, allowing for customization to meet the specific needs of medical applications.
The use of silicone rubber molding in the medical industry continues to expand, driven by its unmatched properties and the ongoing innovations in molding equipment. These advancements enable the production of safe, reliable, and high-quality medical devices that contribute to improved patient care and outcomes.
Conclusion
Innovation in silicone rubber molding equipment is of paramount importance in today’s ever-evolving manufacturing landscape. The versatility, durability, and unique properties of silicone rubber make it a preferred choice in various industries, including automotive, electronics, consumer goods, and especially the medical industry. By embracing innovation in silicone rubber molding equipment, manufacturers can unlock new possibilities, enhance efficiency, and stay competitive in the market.
The potential for growth and advancements in the silicone rubber molding industry is vast. Continual developments in advanced materials, integration of automation and robotics, implementation of real-time monitoring and control systems, and enhancements in mold design and cooling techniques enable manufacturers to achieve higher productivity, superior product quality, and cost-effectiveness. These innovations empower manufacturers to meet the evolving demands of their customers and stay ahead of the competition.
In this dynamic industry, manufacturers are encouraged to embrace innovation as a means to gain a competitive edge. By actively seeking collaborations, engaging in knowledge sharing, and staying updated with the latest advancements, manufacturers can harness the full potential of silicone rubber molding equipment. Embracing innovation not only enhances productivity and profitability but also enables manufacturers to deliver exceptional quality silicone products that cater to the diverse needs of various industries.
As the demand for high-quality silicone products continues to grow, the pursuit of innovation in silicone rubber molding equipment remains critical. By continuously striving for advancements and improvements, manufacturers can position themselves at the forefront of the industry, driving growth, and delivering cutting-edge solutions to meet the challenges of the future. Embracing innovation is the key to unlocking the vast potential of silicone rubber molding machines and maintaining a competitive advantage in the ever-changing manufacturing landscape.