Introduction
Silicone rubber molding is a versatile manufacturing process that holds immense significance across a wide range of industries. It involves shaping and forming silicone rubber into intricate and customized components. From automotive to medical, electronics to consumer goods, silicone rubber molding has revolutionized the way products are designed and manufactured. Its ability to create complex shapes, withstand extreme temperatures, and offer excellent durability makes it an invaluable technique in modern manufacturing. In this article, we will explore the fundamentals of silicone rubber molding, its applications, advantages, and key considerations, providing a comprehensive understanding of this vital process.
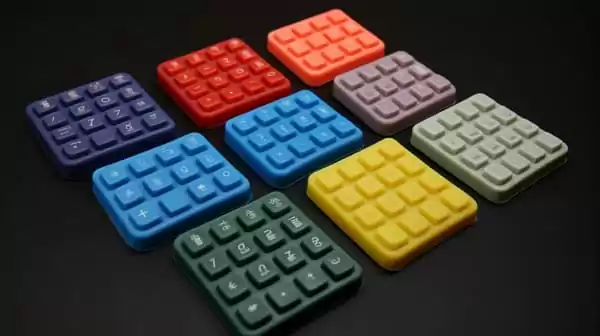
II. What is Silicone Rubber Molding?
A. Explanation of the Process:
Silicone rubber molding is a manufacturing technique that involves several key steps to shape and form silicone rubber into desired components. The process can be summarized as follows:
1.Injection Molding Process:
The silicone rubber molding process begins with the injection of liquid silicone rubber into a mold cavity. The liquid silicone rubber is injected under high pressure using specialized equipment. This high-pressure injection ensures that the material fills all the intricate details of the mold, resulting in accurate and precise component replication.
2.Liquid Silicone Rubber Materials:
Liquid silicone rubber molding (LSR) is the material used in silicone molding. It is a two-component system comprising a base forming silicone and a catalyst or curing agent. These components are mixed together before injection. LSR materials have low viscosity, allowing them to flow easily into the mold cavities and fill complex shapes and fine details.
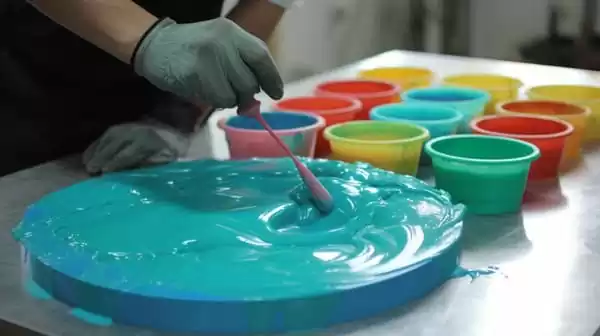
3.Mold Cavity and Mold Clamp:
The mold cavity is the hollow space within the mold where the liquid silicone rubber is injected. The mold itself is typically made of aluminum due to its excellent heat conductivity and durability. The mold cavity is carefully designed to create the desired shape and specifications of the final component. Once the mold is filled with the liquid silicone rubber, it is securely clamped together using a mold clamp to prevent leakage during the injection and curing processes.
4.Curing and Demolding:
After the liquid silicone rubber is injected into the mold cavity, it undergoes a curing process to solidify and take the shape of the mold. Curing can be achieved through heat or a chemical reaction, depending on the specific silicone rubber material and requirements. Once the silicone rubber has fully cured and solidified, the mold is opened, and the finished component is removed. This step is known as demolding. Proper demolding techniques ensure the component is safely and cleanly extracted from the mold without any damage.
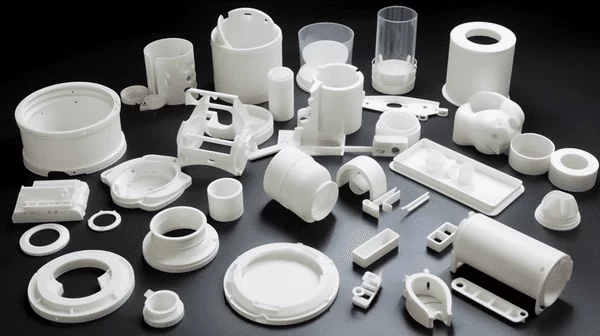
Understanding the process of silicone rubber molding provides a foundation for exploring its applications, benefits, and considerations in the manufacturing industry.
III. Applications and Advantages of Silicone Rubber Molding
A. Applications:
- Automotive: Silicone rubber molding finds extensive use in the automotive industry. It is employed in the manufacturing of various components such as gaskets, seals, O-rings, and vibration dampeners. The excellent temperature resistance of silicone rubber makes it suitable for automotive applications where exposure to high and low temperatures is common.
- Medical: In the medical field, silicone rubber molding plays a vital role in producing medical devices, implants, prosthetics, and components for healthcare equipment. Silicone rubber exhibits superior compatibility with body fluids and human tissue, making it ideal for applications requiring biocompatibility and long-term reliability.
- Electronics: Silicone rubber molding is widely utilized in the electronics industry. It is employed in the production of keyboards, connectors, and protective cases. The durability and flexibility of silicone rubber ensure reliable performance and protection for electronic devices.
- Consumer Goods: Silicone rubber molding is prevalent in the manufacturing of various consumer goods. It is used to create kitchenware, baby products, personal care items, and more. The flexibility and durability of silicone rubber make it suitable for consumer products that require safe and long-lasting materials.
- Industrial: In the industrial sector, silicone rubber molding is utilized for the production of seals, gaskets, and components used in machinery and equipment. Silicone rubber’s resistance to extreme temperatures and its ability to withstand harsh environments make it ideal for industrial applications.
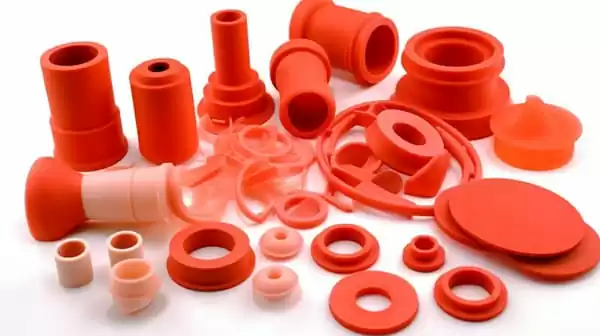
B. Advantages:
Silicone Rubber Exhibits an Outstanding Temperature Resistance: This property makes silicone rubber ideal for applications that experience fluctuating temperatures without compromise in integrity; making it the go-to material when extreme fluctuations arise.
Compatibility with Body Fluids and Human Tissue: Silicone rubber materials are biocompatible and display excellent compatibility with both human body fluids and tissue, making silicone rubber molding ideal for medical applications that involve direct contact between silicone rubber molds and the human body. This property makes silicone rubber molding especially well suited to medical uses where direct physical contact must be established with human bodies is essential.
Durability and Adaptability: Silicone rubber molding produces components that are both long-term durable and flexible enough to endure repetitive use in various environments, due to the inherent properties of silicone rubber such as good elongation and low compression set rates, contributing significantly to its resilience and adaptability.
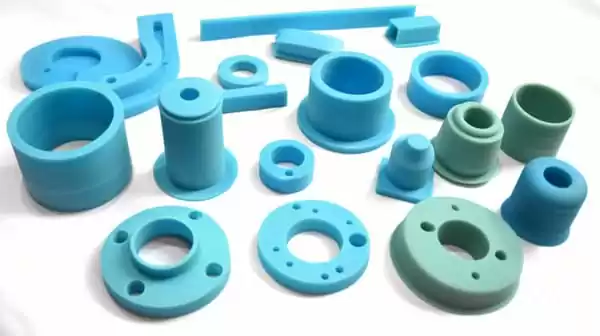
C.High-Volume Production:
Silicon rubber molding’s injection molding process offers efficient and high-volume production of consistent parts at scale, which makes it especially valuable to industries requiring large volumes in a short period.
Silicone Rubber Molding Allows for Complex Designs:
The compression molding cavity can be customized to produce components with fine details, providing manufacturers with design freedom and precision production of components.
Understanding the applications and advantages of silicone rubber molding underscores its versatility and benefits across industries, making it an invaluable manufacturing process capable of producing components with exceptional performance characteristics.
IV. How Does Liquid Silicone Rubber (LSR) Molding Work?
A. Explanation of LSR Molding Process:
Liquid Silicone Rubber (LSR) molding is a specific type of silicone rubber molding that involves the following key elements:
- Metering Section and Two-Component System: The LSR molding process begins with the preparation of the liquid silicone rubber. In a metering section, the two components of the LSR silicone material – a base forming silicone and a catalyst or curing agent – are carefully mixed together. This ensures precise control of the material ratio, which is crucial for achieving the desired properties and curing characteristics.
- Ejector Pins and Supply Drums: Once the liquid silicone rubbers material is mixed, it is ready for injection into the mold cavity. The injection process is similar to conventional silicone rubber molding, where the LSR material is injected under high pressure into the mold cavity. However, there are a couple of additional elements specific to LSR molding:
- Ejector Pins: To facilitate the removal of the molded part, ejector pins are employed. These pins push the finished part out of the mold once the silicone rubber has fully cured and solidified.
- Supply Drums: The liquid silicone rubber is stored in supply drums, which ensure a continuous and controlled flow of material during the injection process. This setup enables consistent and efficient production of LSR components.
The LSR molding process combines precise metering and controlled injection to produce high-quality silicone rubber components. The use of ejector pins and supply drums enhances the efficiency and effectiveness of the molding process, resulting in consistent and reliable production.
Understanding the intricacies of the LSR molding process provides insight into the specialized techniques employed for manufacturing components that require the unique properties and characteristics of liquid silicone rubber.
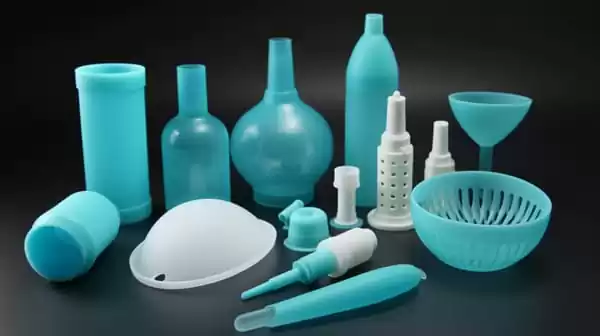
Conclusion
In conclusion, silicone rubber molding is a versatile and essential manufacturing process that offers numerous benefits for producing high-quality components. By understanding the process and considering key factors, manufacturers can achieve optimal results in their silicone rubber molding endeavors.
Silicone rubber molding allows for the creation of intricate and customized components used in various industries such as automotive, medical, electronics, consumer goods, and industrial applications. Its ability to resist extreme temperatures, compatibility with body fluids and human tissue, durability, flexibility, and design versatility make it a preferred choice for many manufacturers.