Introduction
Compression molding is a versatile and widely utilized manufacturing process employed across a diverse range of industries. This technique involves the transformation of raw materials into desired shapes and forms through the application of pressure and heat. The process typically takes place within a mold cavity, where the materials are subjected to controlled conditions that promote their solidification and the creation of intricate components.
Industries such as automotive, aerospace, consumer goods, and electronics have embraced compression molding due to its ability to produce high-strength, durable, and precision-engineered products. One of the primary advantages of compression molding lies in its capability to create complex geometries and intricate details while ensuring consistent quality and dimensional accuracy. This makes it a favored choice for manufacturing components that demand structural integrity, such as automotive parts, electrical enclosures, and the composite structures and materials used in aerospace applications.
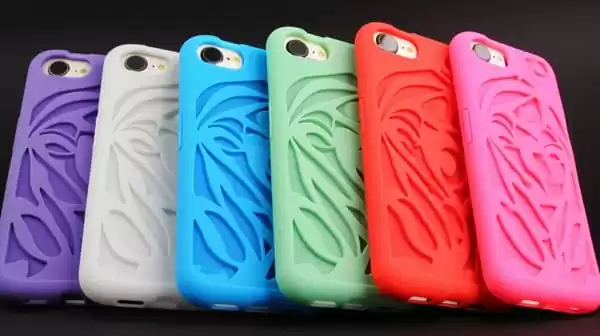
II. Understanding the Art of Compression Molding
In the realm of manufacturing, compression molding stands as a remarkable technique that marries science and craftsmanship to shape raw materials into intricately designed products. Let’s delve into the fundamentals of this process, exploring how pressure and heat collaborate to create components known for their durability, precision, and structural integrity.
Brief Overview of the Compression Molding Technique
Compression molding can be likened to a careful dance between materials and mold, orchestrated to achieve a harmonious outcome. At its core, this technique involves the strategic placement of raw materials – often in the form of powdered or pelletized substances – into a precisely designed mold cavity. Once in place, the mold is sealed shut, initiating a transformative sequence of events.
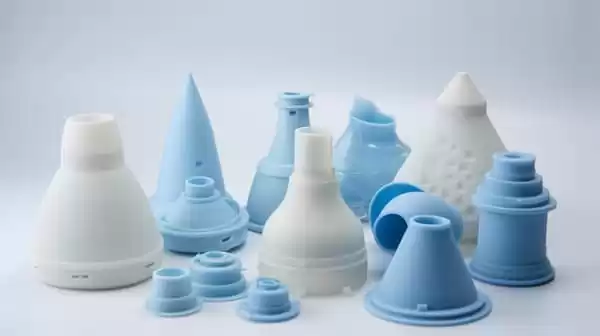
Exploring the Role of Pressure and Heat
Pressure and heat, acting as the maestros of this symphony, work in tandem to coax the raw materials into a new form. The application of pressure ensures that the materials are tightly packed within the mold cavity, while heat induces a controlled chemical reaction that triggers polymerization or cross-linking. This transformation imparts the materials with the desired strength and structure, turning them from pliable masses into resilient shapes.
Highlighting Desirable Properties Achieved Through Compression Molding
The compression molding process yields products revered for their exceptional properties, each facet contributing to their widespread appeal across industries:
Durability:
Through the strategic application of pressure and heat, compression molding imparts a robust and enduring quality to the materials. This durability ensures that the resulting components can withstand various stressors and environmental conditions.
Precision:
The inherent nature of compression molding allows for meticulous control over the final shape and dimensions of the product. This precision proves invaluable, particularly when crafting components that require strict adherence to specifications.
Structural Integrity:
The seamless fusion of materials under pressure and heat fosters a high degree of structural integrity. This property is especially crucial in applications where the components are subjected to mechanical loads or external forces.
As we delve deeper into the world of compression molding, we will unravel the remarkable influence of material additives on this intricate dance between pressure, heat, and raw materials. These additives hold the potential to elevate the properties of compression-molded products, opening avenues for innovation and customization. Join us on this exploration as we uncover the profound effects that material additives bring to the compression molding process and the resulting components.
III. Effects of Material Additives on Compression Molding
The integration of material additives into the compression molding process introduces a symphony of enhancements that enrich the characteristics of the final products. Let’s explore how these additives wield their transformative influence, elevating mechanical performance, bolstering thermal stability, refining surface finish, ensuring dimensional accuracy, and optimizing material usage.
A. Enhanced Mechanical Performance through Material Additives
1. Influence of Carbon Fibers on Mechanical Strength and Stiffness
Carbon fibers, renowned for their exceptional strength-to-weight ratio, usher in a new era of mechanical excellence in compression-molded products. When added strategically to the material matrix, carbon fiber form a reinforcement network that significantly augments both mechanical strength and stiffness. This infusion results in products capable of withstanding higher stresses and loads, making them suitable for applications demanding superior structural integrity.
2. Impact Resistance and Reinforcement with Glass Fibers
Glass fibers emerge as stalwart allies in the quest for enhanced impact resistance and reinforcement. Introducing glass fibers to the material composition fortifies the product’s ability to absorb and distribute impact energy. This added layer of defense safeguards components against external forces, making them resilient even in challenging environments.
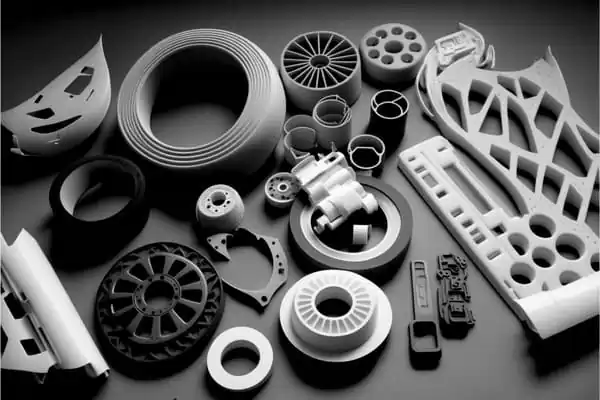
B. Improving Thermal Stability and Temperature Resistance
1. Role of Heat Stabilizers and Flame Retardants
The world of compression molding embraces the benefits of heat stabilizers and flame retardants, pivotal additives that enhance thermal stability and temperature resistance. Heat stabilizers safeguard products against the effects of prolonged exposure to elevated temperatures, ensuring that they maintain their structural integrity over time. Flame retardants, on the other hand, provide an essential layer of protection by inhibiting or slowing down the spread of flames, making compression-molded components safer in scenarios where fire risk is a concern.
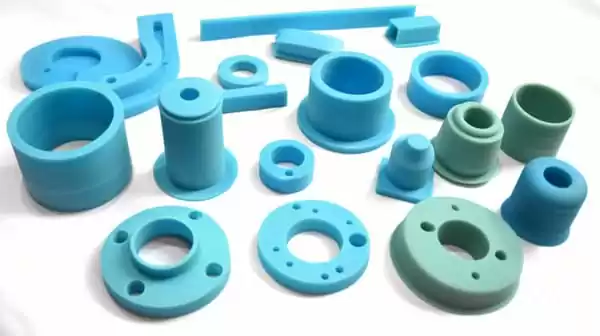
C. Customized Surface Finish and Demolding Process
1. Mold Release Agents and Their Impact on Surface Quality
Material additives extend their influence to the realm of aesthetics and ease of production. Mold release agents assume a central role in achieving a customized surface finish and facilitating the demolding process. These agents create a barrier between the material and the sheet molding compound, enabling smooth and seamless demolding while enhancing the final product’s surface quality. The result is a product with a polished appearance, ready to make its mark.
D. Achieving Dimensional Stability and Reducing Defects
1. Countering Shrinkage, Warping, and Void Formation
Dimensional stability is a cornerstone of product quality, and material additives rise to the challenge. By countering challenges such as shrinkage, warping, and void formation, these additives ensure that compression-molded products retain their intended dimensions. Through strategic formulation, manufacturers can mitigate these potential defects, contributing to the overall excellence of the end product.
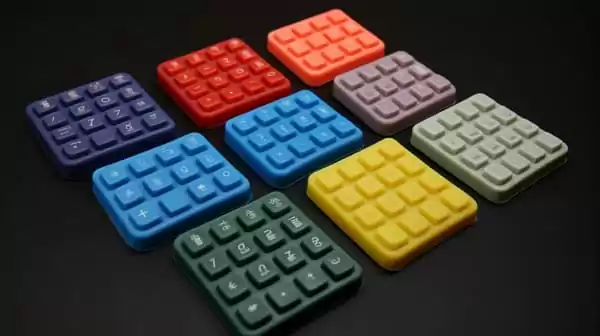
E. Cost-effectiveness and Material Optimization through Additives
The marriage of material additives with compression molding not only enhances product properties but also presents an avenue for cost-effective production. By incorporating fillers and extenders, manufacturers achieve material optimization without compromising performance. This judicious use of additives contributes to efficient manufacturing processes and economical use of resources.
As we traverse the landscape of compression molding, it becomes evident that material additives serve as catalysts of innovation, enabling the creation of products that transcend conventional limits. In the forthcoming sections, we will delve further into the intricate interplay between material additives and the compression molding process, uncovering how these additives shape the future of manufacturing.
IV. Unveiling the Effects of Material Additives on Compression Molding
The fusion of material additives with the realm of compression molding leads to a symphony of enhancements that shape the very essence of the final products. In this section, we embark on a journey to unravel the intricate tapestry of effects brought about by these additives, encompassing the elevation of mechanical performance, the fortification of thermal stability, the art of surface finish customization, the navigation of dimensional stability challenges, and the delicate balance between cost and efficiency.
A. Elevating Mechanical Performance
1. Impact of Carbon Fibers on Bolstering Mechanical Strength and Stiffness
Carbon fibers, akin to the architectural pillars of a structure, lend unparalleled strength and rigidity to compression-molded products. Their strategic incorporation within the material matrix bestows a newfound robustness, enabling the product to withstand formidable stresses and loads. The result is a component that stands tall, unfazed by the trials of its operational environment.
2. Amplifying Impact Resistance through Strategic Use of Glass Fiber Reinforcements
Glass fibers take center stage, assuming the role of guardians against impact forces. Delicately woven into the material composition, these reinforcements absorb and distribute impact energy, acting as a shield that safeguards the product from damage. The calculated inclusion of glass fibers ensures that the product retains its integrity even when faced with challenging external forces.
B. Fortifying Thermal Stability
1. Exploring the Role of Heat Stabilizers in Elevating Temperature Resistance
Heat stabilizers emerge as sentinels of durability, extending a protective embrace over compression-molded components. Their contribution lies in the enhancement of temperature resistance, allowing the product to brave the test of time and temperature fluctuations. The result is a product that remains steadfast and unwavering in the face of thermal challenges.
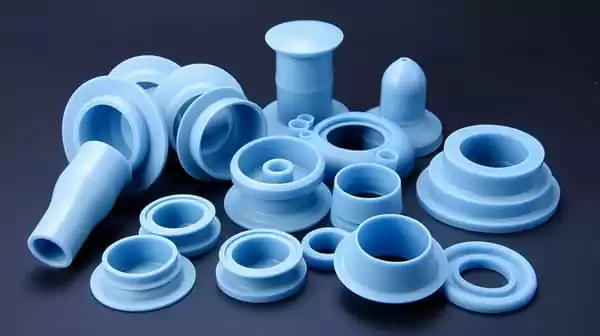
2. Flame Retardants and Their Pivotal Role in High-Risk Applications
Flame retardants join the ensemble, showcasing their prowess in applications where safety takes precedence. By inhibiting the spread of flames, these additives act as silent guardians, instilling a sense of security in high-risk scenarios. The incorporation of flame retardants transforms compression-molded components into stalwart protectors, capable of withstanding even the fiercest of challenges.
C. Mastering Surface Finish Customization
1. Understanding the Influence of Mold Release Agents on Demolding and Surface Quality
In the realm of aesthetics, mold release agents emerge as artists, crafting a polished and refined surface finish. Their presence eases the demolding process, ensuring that the product emerges seamlessly from its mold cocoon. Simultaneously, these agents leave an indelible mark on the surface quality, contributing to a final product that is both visually appealing and tactilely refined.
D. Navigating Dimensional Stability Challenges
1. Addressing Concerns Related to Shrinkage, Warping, and Void Formation with Well-Chosen Additives
Dimensional stability stands as a cornerstone of quality, and additives take on the mantle of guardians against common pitfalls. Through meticulous formulation, these additives counteract challenges such as shrinkage, warping, and void formation. The outcome is a product that adheres faithfully to its intended dimensions, free from the distortions that may compromise its excellence.
E. Balancing Cost and Efficiency
1. Harnessing the Power of Fillers and Extenders to Reduce Material Costs
In the delicate equilibrium between cost and efficiency, fillers and extenders make their mark. These additives introduce a judicious approach to material usage, optimizing resources without sacrificing performance. By striking this harmonious balance, compression molding becomes a testament to economical manufacturing, where every material particle contributes to the grand symphony of efficiency.
2. Shortening Cycle Times for Improved Productivity and Energy Conservation
Efficiency takes center stage as cycle times are orchestrated with precision. Material additives step in, streamlining the compression molding process to achieve faster cycle times. The result is a harmonious dance of production, where reduced cycle times translate to enhanced productivity and energy conservation, aligning with the demands of a sustainable future.
As we unveil the myriad effects of material additives on compression molding, we peer into a world where innovation is the driving force, and customization knows no bounds. In the chapters that follow, we delve deeper into real-world applications, challenges, and the tantalizing promise of a future where material additives shape the very fabric of manufacturing excellence.
V. Real-world Applications and Intriguing Case Studies
The real-world impact of material additives on compression molding reverberates across industries, where innovation meets application in a captivating dance. In this section, we delve into intriguing case studies that showcase how material additives have redefined the boundaries of possibility, resulting in enhanced crash resistance, fortified thermal stability, and the achievement of desired aesthetics and longevity.
A. Automotive Industry: Enhancing Crash Resistance with Tailored Material Additives
In the bustling realm of the automotive industry, safety reigns supreme. Material additives have emerged as silent guardians, ushering in a new era of crash resistance. By integrating advanced additives into the compression molding process, manufacturers craft components capable of absorbing and dissipating impact energy with precision. Through the strategic inclusion of reinforcing agents like carbon fiber and glass fibers, compression-molded automotive parts stand resolute, offering a shield of protection to occupants during unforeseen collisions. These tailored material formulations epitomize the harmonious fusion of science and engineering, making the automotive landscape safer and more secure.
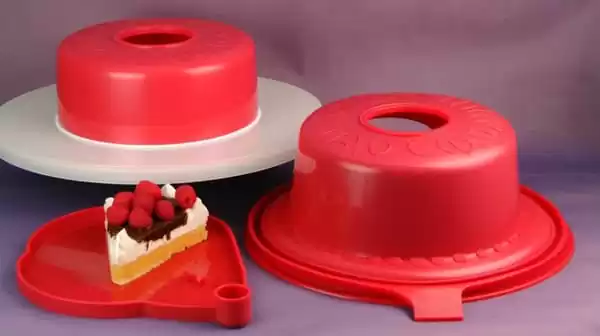
B. Aerospace Applications: Strengthening Thermal Stability for Critical Components
In the boundless expanse of aerospace, where every component must withstand the rigors of space and atmospheric conditions, material additives take center stage. The compression molding process, augmented by specialized additives, yields components that exhibit unparalleled thermal stability. Heat stabilizers, carefully incorporated into the material matrix, ensure that critical aerospace parts remain structurally sound even in the face of extreme temperatures. This fortification of thermal resilience translates to enhanced reliability and longevity, underpinning the success of missions that venture beyond our planet.
C. Consumer Goods: Achieving Desired Aesthetics and Longevity through Precise Additive Choices
The consumer goods landscape embraces the marriage of functionality and aesthetics, where material additives infuse a touch of ingenuity into everyday products. The compression molding process, guided by precise additive choices, results in items that resonate with both visual appeal and longevity. By employing sheet molding compounds and release agents, manufacturers craft consumer goods with impeccable surface quality, fostering tactile delight. Moreover, additives such as fillers and extenders optimize material usage, contributing to cost-effective production without compromising the product’s integrity. From electronics enclosures to household appliances, material additives elevate the ordinary into the extraordinary, creating products that seamlessly blend form and function.
As we delve into these real-world applications and captivating case studies, the symbiotic relationship between material additives and compression molding unfolds before us. The influence of these additives extends far beyond the manufacturing floor, touching lives and reshaping industries. Our journey continues as we navigate challenges, explore the frontiers of innovation, and envision a future where material additives continue to shape the landscape of compression molding and beyond.
VI. Navigating Challenges and Considering Trade-offs
The synergy between material additives and compression molding introduces a realm of possibilities, yet it is not without its intricacies and considerations. In this section, we embark on a journey of exploration, navigating challenges, and delving into the delicate dance of trade-offs that accompany the integration of additives. We also emphasize the vital role of testing and validation in the selection of additives to ensure that the desired results are achieved while maintaining the integrity of the final product.
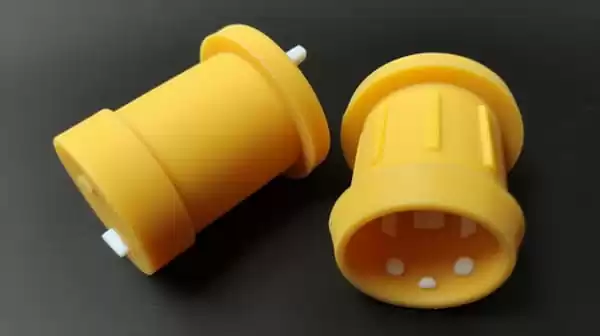
A. Achieving the Optimal Additive Balance for Targeted Results
The path to additive-enhanced perfection requires a delicate equilibrium. Manufacturers must meticulously calibrate the composition of additives to achieve the desired characteristics of the end product. Striking the right balance ensures that the product exhibits the intended enhancements without compromising other essential properties. The process demands a thorough understanding of additive interactions, as well as a keen awareness of the specific application’s requirements. Achieving this optimal additive balance becomes a harmonious endeavor, where every element contributes to the symphony of success.
B. Addressing Potential Trade-offs in Material Properties and Their Impact on Final Product Performance
The journey of additive integration comes with inherent trade-offs that warrant careful consideration. While additives enhance certain properties, they may impact others. For example, the addition of fillers or reinforcements might increase mechanical strength but could also influence factors such as weight or flexibility. Manufacturers must engage in a thoughtful evaluation, weighing the benefits against potential drawbacks. By thoroughly assessing these trade-offs, the resulting compression-molded product emerges as a well-rounded embodiment of optimized attributes.
C. Importance of Rigorous Testing and Validation in Additive Selection
The road to additive integration is paved with testing and validation, ensuring that the selected additives align with the intended goals. Rigorous testing encompasses a comprehensive examination of the interplay between additives, base materials, and the compression molding process. This phase validates the anticipated improvements and identifies any unforeseen effects. Through meticulous validation, manufacturers safeguard against undesirable outcomes and refine additive formulations to align with their vision. In this dynamic journey, testing becomes the compass guiding the way toward additive-enhanced excellence.
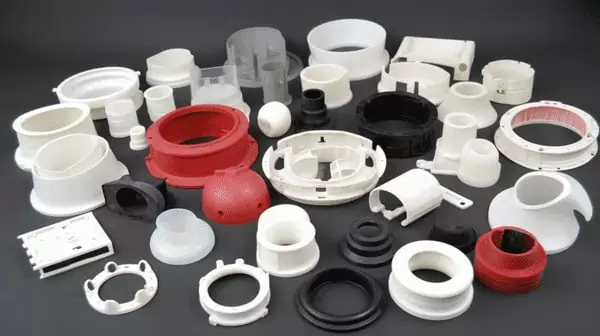
As we navigate challenges and consider the intricate dance of trade-offs, we underscore the importance of a meticulous and systematic approach. Additive integration requires a harmonious blend of expertise, innovation, and precision. By embracing the complexities, addressing potential trade-offs, and engaging in robust testing and validation, manufacturers harness the transformative potential of material additives, ushering in a new era of compression molding where every element contributes to the symphony of success.
VII. Peering into the Future: Innovations and Beyond
The horizon of possibilities stretches before us, beckoning with the promise of remarkable advancements in additive manufacturing compression molding, through the lens of material additives. In this section, we cast our gaze forward, shedding light on emerging additives that hold the potential to reshape the landscape and exploring the dynamic evolution of additive manufacturing techniques for a future characterized by unprecedented customization and innovation.
A. Spotlight on Emerging Material Additives and Their Potential Game-changing Effects
As technology propels us forward, emerging material additives take center stage, poised to usher in a new era of compression molding excellence. Imagine the fusion of novel nanomaterials that promise unmatched strength at a microscopic scale or the integration of bio-based additives that contribute to a more sustainable manufacturing landscape. These innovative additives have the potential to revolutionize compression molding by bestowing previously unattainable properties upon products. From enhanced biodegradability to tailored electrical conductivity, these additives are catalysts for transformation, opening pathways to uncharted territory where imagination and innovation collide.
B. Exploring the Evolving Landscape of Additive Manufacturing Techniques for Further Customization
In the ever-evolving world of large scale additive manufacturing, customization emerges as a guiding principle. The marriage of additive techniques with compression molding expands the realm of possibilities, enabling the creation of products that cater precisely to individual needs. Techniques such as 3D printing and additive layer manufacturing synergize with compression and molding processes, granting manufacturers the power to craft products with intricate geometries, optimized material distribution, and tailored mechanical properties. This fusion engenders a future where each product is a masterpiece of personalization, blurring the boundaries between creativity and manufacturing prowess.
As we peer into the future, the symphony of material additives and compression molding resonates with endless potential. The evolution of additives and the seamless integration of additive manufacturing techniques hold the promise of a manufacturing landscape where innovation knows no bounds. It is a future where compression molding transcends its current limitations, where materials become canvases of creativity, and where each product is a testament to the harmonious convergence of human ingenuity and technological progress. Our journey through material additives and their effects on compression molding culminates in this tantalizing vista, an invitation to a future that is limited only by the horizons of our imagination.
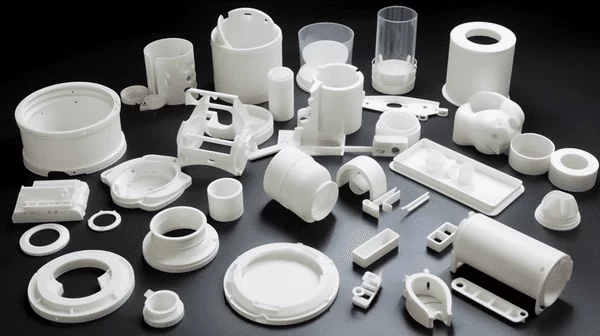
Conclusion
In the intricate dance between material additives and compression molding, we have traversed a landscape of innovation, customization, and boundless potential. As we draw the curtain on this exploration, it becomes clear that material additives are not merely ingredients; they are the architects of transformation, molding the very essence of the products they touch.
Throughout this journey, we have witnessed the multifaceted effects of material additives on compression molding. We’ve seen how carbon fiber reinforced polymers and glass fibers bolster mechanical strength and impact resistance, how heat stabilizers and flame retardants fortify thermal stability, and how mold release agents weave a tapestry of surface finish customization. We’ve navigated the challenges of dimensional stability and trade-offs, recognizing the pivotal role of rigorous testing and validation in additive selection.
Material additives stand as catalysts that shape the very course of modern manufacturing. They bridge the gap between art and science, enabling compression molding to yield products that defy convention. From the automotive industry’s crash-resistant components to aerospace marvels that withstand the extremes of space, material additives forge a legacy of innovation that echoes across industries.
As we bid farewell to this exploration, we reinforce the central role of material additives in the manufacturing landscape. They are the silent heroes that elevate mechanical performance, invigorate thermal stability, refine aesthetics, and steer products toward excellence. They are the conduits through which compression molding transcends its limits, sculpting a future where ingenuity and technology intertwine in harmonious symphony.
In the grand tapestry of modern manufacturing, material additives are the brushstrokes of progress, painting a portrait of a world where every product is a testament to human creativity and engineering acumen. As we step forward into this ever-evolving journey, let us remember the profound influence of material additives on compression molding, forever shaping the art of creation and innovation.