Electrical conductivity is a material used in various electronic applications. Its ability to conduct electricity makes it an ideal material for transistors, transistors, switches, and other electronic components.
Here’s how it can be tailored to meet the needs of a particular application. We’ll also discuss some of the key properties of conductive rubber that make it a career in e-commerce.
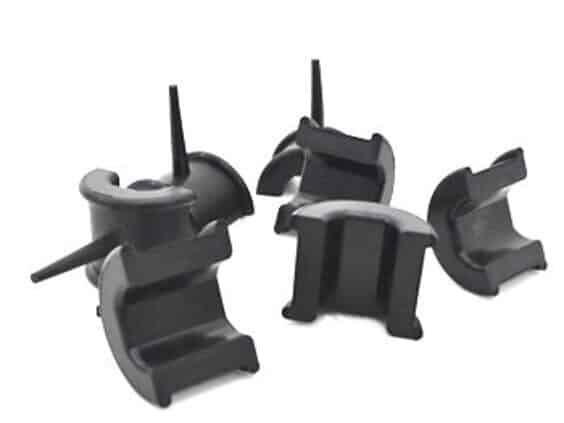
Rubber below 10^4Ω is called conductive rubber. Conductive rubber not only has a high elasticity of rubber, but is also easy to process and form, and is light in weight. Rapid development leads to the increasingly wide application of polymer materials.
When making conductive rubber products, raw rubber with a large dielectric constant is generally selected, such as silicone rubber, neoprene rubber, and nitrile rubber. Silicone rubber matrix is a better material for making conductive rubber products.
It not only has the characteristics of electrical conductivity, high and low-temperature resistance, and aging resistance, but also has good process performance, and is suitable for manufacturing conductive rubber products with complex shapes and small structures;
When used for electrical connection equipment, it can fit closely with the contact surface, is accurate and reliable, full of elasticity, and can play the role of shock absorption and sealing.
Material selection should also be made according to the conditions of use of the product. For example, conductive rubber used in an environment in contact with oil is best to use oil-resistant rubber, such as nitrile rubber, chlorohydrin rubber, and neoprene rubber.
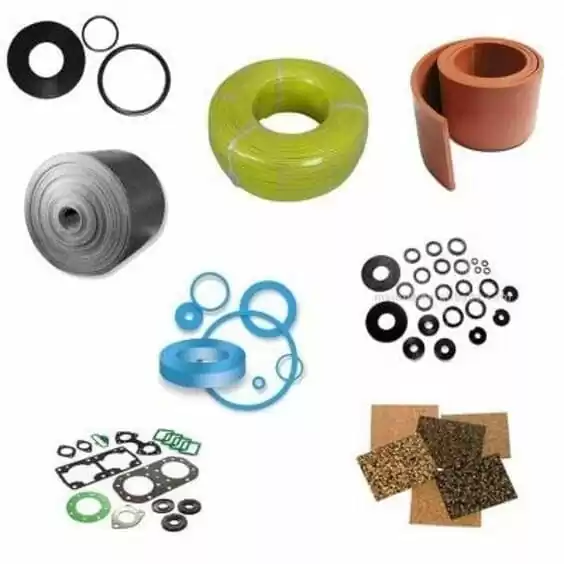
Rubber combinations or rubber/plastic can also be used to make conductive rubber. EPDM, IIR, and PE can improve insulation (such as dielectric strength), PS/EPDM, PS/PBD, NBR/EPDM, NBR/IR, NR/CR, etc. are used together, with the help of an appropriate amount of hard colloid phase to make the conductive network structure.
It is denser, or the conductive compounding agent such as carbon black is enriched in the phase interface region of the incompatible rubber pair, thereby improving the conductive performance.
Therefore, the combination of rubber and rubber and plastic can use less filler to achieve the required conductive effect, which is beneficial to the flow of the rubber during processing and also reduces the hardness of the vulcanized rubber.
The conductivity of conductive rubber depends largely on the type and amount of conductive fillers. The type and amount of fillers are crucial to the conductivity of rubber products.
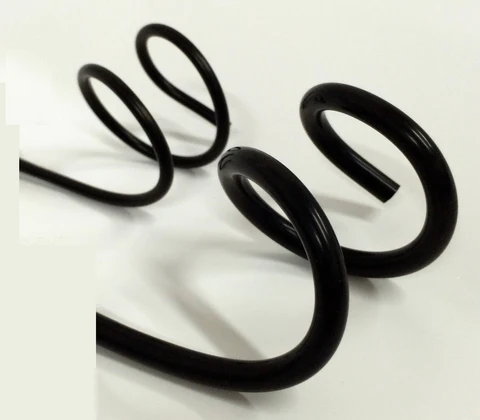
Commonly used conductive rubber fillers are granular carbon black, carbon fiber fillers, and metal conductive fillers such as gold, platinum, silver, copper, nickel, and other fine powders and flakes, foils, or processed into metal fibers, etc.
These conductive fillers can provide electrical conductivity, improve the mechanical strength, fatigue resistance, and aging resistance of vulcanizates, etc. When the conductive filler particles reach a certain value, the conductivity will jump and increase sharply by several or ten orders of magnitude.
After the conductive filler reaches or exceeds a certain critical value, the rubber filled with the conductive filler becomes conductive rubber. This critical value corresponds to the critical value at which the conductive filler particles in the composite material start to form conductive pathways.
1. What is conductive rubber and what are its properties?
Conductive rubber is a conductive polymer material widely used in applications involving the transmission and dissipation of electrical current. It mainly consists of elastic rubber and carbon black, which acts as a conductive agent in the rubber matrix. One of its most important properties is its flexibility, allowing it to adapt to any given shape or surface modification.
In addition, due to the soft nature of rubber, it insulates well against shocks, prevents abrasion and vibration, and has superior weather resistance and durability compared to conventional materials.
Additionally, its ability to form into any shape allows it to comfortably conform to the hand mounted on electrical equipment, eliminating the risk of electric shock from exposed metal edges. Overall, conductive rubber is an ideal solution for a variety of applications where conductivity and protection from physical damage are required.
2. Different types of conductive rubber
Conductive rubber is an important material used in many different industries because it can easily absorb and transport electrical charges. There are many different types of conductive rubber available, depending on the application.
Both silicone and neoprene have impressive thermal properties and provide effective insulation, making them excellent choices for electronic applications.
EPDM rubber has excellent weather resistance and chemical stability, making it suitable for outdoor applications where harsh conditions may exist. The natural rubber has great tensile strength and elasticity, which means it can handle heavy loads without compromising its structural integrity.
Finally, nitrile rubber is extremely resistant to oil and abrasion, so it is often used in seals and hoses that need to withstand the pressure of liquids or debris. Each type of conductive rubber offers specific benefits based on application needs. With so many options, finding the right one is easy!
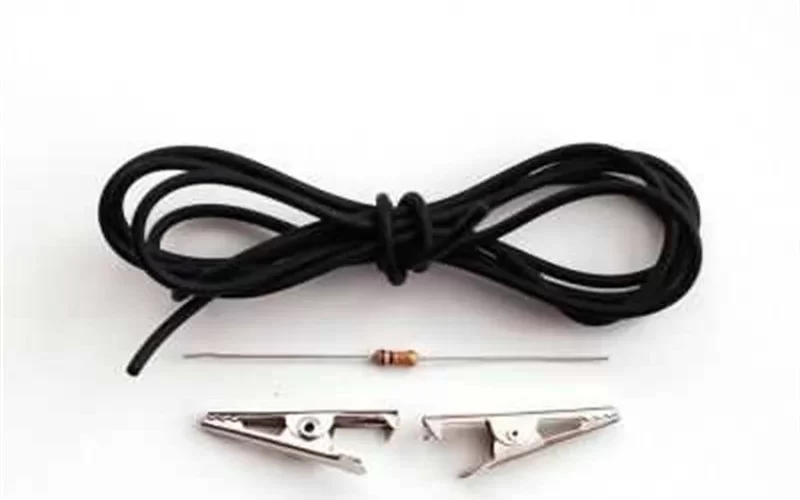
3. How to choose the right type of conductive rubber to meet your needs?
Knowing how to choose the right type of conductive rubber for your needs can be tricky. When choosing a material, consider how much insulation is required and how the material will be used in its intended application. In addition to resistance considerations, it is important to consider thickness, flex life, and temperature range.
Thickness and curvature are important components as they determine whether a product will fit your machine and also last a long time. Additionally, the temperature range affects the lifespan and integrity of the material—some rubbers are only suitable for low temperatures, while others may last at higher temperatures.
Finally, since there are many types of conductive rubber on the market, take some time to research each type so you can make an informed decision when choosing the one that meets your needs.
By carefully assessing your needs and researching materials before purchasing, you’ll have a better chance of finding the type of conductive rubber that perfectly suits your requirements.
4. Tips for formula design of conductive rubber
When it comes to formulating conductive rubber, there are a few key tips that should be taken into consideration. First, the rubber in the rubber formulation should be highly conductive while also being strong enough to withstand harsh environmental conditions. To achieve this balance, it may be beneficial to add a small amount of carbon black or another type of conductive agent.
Once you have added the desired amount of agent, you will need to test the electrical properties of the rubber to ensure it meets your quality standards. Also, since rubber is a highly malleable material, you might want to consider testing its flexibility and durability. Finally, keep a close eye on your formulation process and note any changes in color or smell so you can make adjustments as needed before finalizing your product.
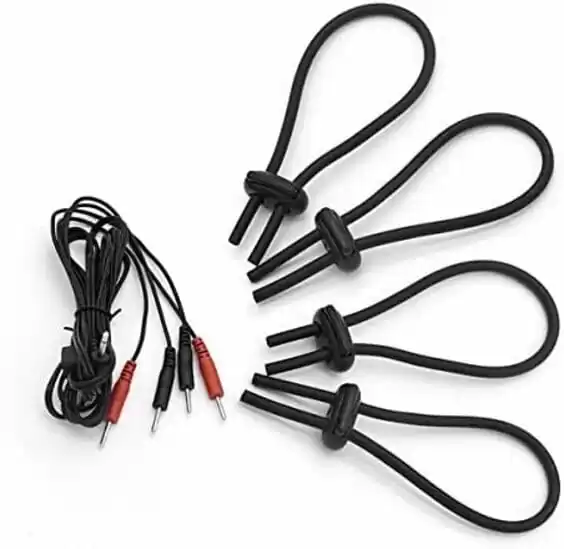
5. Examples of how to use conductive rubber in products?
Conductive rubber-also known as conductive elastomers or silicone elastomers — is a material commonly used in manufacturing because of its excellent combination of electrical and superior mechanical properties, as well as its ability to resist extreme temperatures and environmental stresses.
There are many ways conductive rubber can be incorporated into products, whether it is medical devices, protective covers, automotive components, or any other type of application that requires durability and continued thermal conductivity.
A popular way to use conductive rubber is to encapsulate a product’s printed circuit boards (PCBs) to protect them from dust and moisture while still allowing reliable signal transmission. Conductive rubber is also used as a noise-suppression tool for home appliance motors. Other beneficial uses include adding flexible antennas to cell phones or RFID tags;
Insulation for high-voltage equipment; impact protection for laptops; housings for pressure switches; sealing for camera lenses; shock absorbers for vehicles; and more. The possibilities are endless. Through the correct application of conductive rubber, manufacturers can produce innovative products that are both safe and effective.
Source: https://www.youtube.com/@mikezetarmold-com