Preface
Silicone rubber is a kind of synthetic rubber and semi-inorganic polymer elastic material containing a silicon-oxygen structure in the main chain of the molecule. It is formed by hydrolysis and polycondensation of bifunctional silicone monomers such as dimethyldichlorosilane. Silicone rubber looks very much like ordinary natural rubber, but silicone rubber has a high degree of thermal stability and elasticity. Maintains original characteristics within the range of -60 to 300°C. It has very little shrinkage when compressed at high temperatures, and returns to its original shape after the external force is removed. Chemical book. Silicone rubber is divided into hot vulcanization type and room temperature vulcanization type according to the vulcanization method. The latter develops faster.
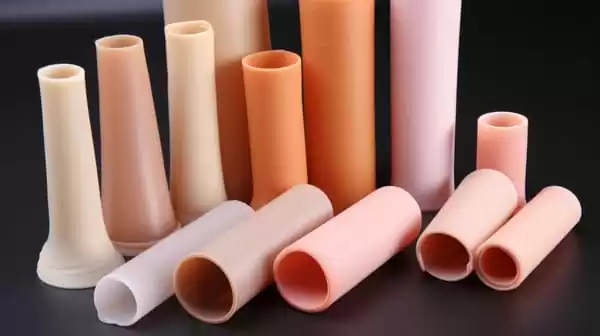
Silicone rubber layers can be used for wires, cables, protective layers of metal parts, insulation parts, gasket seals chemical raw materials, Sealing products include automobile engine crankshaft rear sealing rings, fuel pump seals, air conditioning buffer seals, potentiometer insulating bushings and potting materials, etc.Utilizing its physiological, non-toxic and non-sensitizing properties, it can be used as an ideal medical polymer material for the manufacture of artificial heart valves, artificial lungs, artificial esophagus, and plastic surgery materials. It is used to manufacture high-temperature-resistant insulation seals, medical materials, high-voltage cables, adhesives, etc. However, bubbles often appear in silicone rubber products during the production process. The appearance of bubbles and pores affects the quality of the product. Therefore, if a silicone rubber product factory wants to improve the qualification rate of its products, it can start by avoiding bubbles in its products. This article will tell you about the causes and solutions of bubbles in silicone rubber products.
II.The causes of bubbles generated
(1) The rubber material vulcanization temperature control system is too low or the vulcanization temperature is too high, which is one of the main causes of blistering in thermally conductive silicone sheets. The vulcanization temperature is an important parameter when molding silicone rubber. Usually silicone products are set at 160~200 degrees Celsius. However, sometimes the mold has not been heated by the vulcanizer for a long time due to too long out-of-mold operation or other reasons. As a result, the temperature of the silicone molding mold is low and the vulcanization temperature of the silicone is low, which will cause air bubbles in the product after the thermally conductive silicone sheet is formed. For this, we only need to increase the molding temperature, or put the empty mold into the machine and heat it for a period of time to solve the problem. If the vulcanization temperature is too high and the molding temperature is too high, it will also cause bubbles in the thermally conductive silicone sheet. Why? When the molding temperature is too high, the silicone raw material on the mold surface has begun to form during the mold closing and pressurization process. At this time, the air has been trapped inside and is difficult to discharge, so it will cause bubbles in the thermally conductive silicone sheet molding. For this reason, the molding temperature only needs to be appropriately lowered.
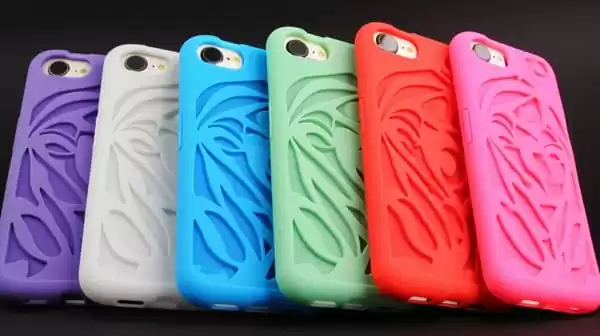
(2) The reason why silicone products have bubbles is insufficient exhaust. After the silicone rubber material is placed in the silicone mold, a lot of air will be brought in at the moment of closing the mold exhaust line. It is impossible for the air to be integrated with the silicone raw material. If these are not The air is discharged, which will cause bubbles to appear on the surface of the silicone button or mold exhaust lines after it is formed.
(3) The structure of the mold is unreasonable. Unreasonable design of the silicone molding mold cavity indoor humidity will also cause bubbles in silicone molding. For example, the arrangement of the exhaust line hole distribution products in the mold, the partitioning method, the mold parting method, the design of the mold size, etc. will all cause poor bubbles. , but the cost of opening a set of molds is very high, and it is not easy to modify.
(4) The vulcanization time is too short. Like the vulcanization temperature, the vulcanization time is also one of the important parameters for the molding of the thermally conductive silicone sheet. The length of the vulcanization time determines whether the thermally conductive silicone sheet can be completely vulcanized. If the vulcanization time is too short, not only will the thermally conductive silicone sheet become soft after molding, but it will also easily cause bubbles to form on the surface of the thermally conductive silicone sheet. If such defects occur, the vulcanization time of the silicone can be appropriately extended.
(5) The production process is also crucial: the anti-aging agent RD is prone to bubbles during the mixing operation of the open mill. This is mainly caused by the melting point of the anti-aging agent RD and secondly by the lower operating temperature of the open mill. Regarding the mixing rubber, Special attention should be paid to the dispersion of zinc oxide during mixing. Its uniform dispersion will also cause foaming of the silicone sheets, so the rubber mixing process is also a very important stage.
(6) The moisture content of the raw materials used in the formula and the adequacy of drying during the mixing operation and after the product is extruded and cooled with water are mainly caused by the power of the moisture during the addition of vulcanization.
III. Solution Measures for Bubble Prevention
1. Adjust Silica Gel Particle Proportion
One source of silicone bubbles lies with excessive silica gel amounts in products; to counter this issue you should adjust this ratio appropriately to reduce their generation and avoid bubbles altogether. Testing and experimental verification may be required prior to any final decisions on this strategy being implemented.
2. Employ Vacuum Extraction Equipment
When producing silicone products, using vacuum evacuation equipment can help expel gases contained within them and effectively reduce any bubbles present within it. In order to address the bubble issue during production processes, vacuum evacuation should definitely be used as part of their solution plan.
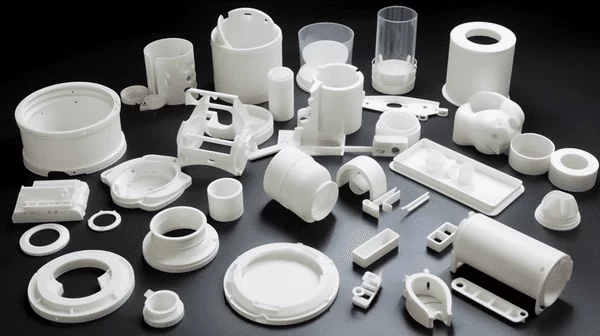
3. Set Production Temperature
Temperature plays an essential part in manufacturing silicone products, as choosing an incorrect one could cause bubbles to form within them. Therefore, during production the temperature needs to be properly set so as to limit bubbles formation as much as possible and maintain reasonable control depending on current situations to minimize bubbles production.
4. Add Surfactant
Silicon products often experience bubble issues during production. By encouraging silica gel molecules to adsorb one another more efficiently and reduce bubble formation, surfactants may help increase quality while improving production processes.
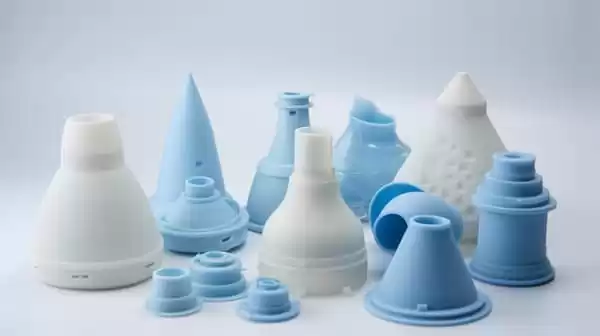
Conclusion
The generation of bubbles is often not caused by one factor, but by a combination of many reasons. When solving the bubble problem, it is difficult to follow general rules, and specific problems should be analyzed in detail. First determine the root cause of the bubbles, and find ideas and methods to solve the problem based on the cause. There is often more than one solution, and it is best to use a multi-pronged approach. It is best to prevent the generation of bubbles. On the one hand, adequate exhaust settings should be made when designing the mold; on the other hand, pre-baking the rubber blank and other materials before vulcanization can effectively eliminate the volatilization inside the rubber material. It is an effective means to prevent bubbles in products.