Introduction
Silicone rubber is an incredibly flexible material used throughout the medical industry. Due to its temperature resistance, chemical resistance, and biocompatibility properties, silicone rubber products have found widespread application as medical devices and equipment components. When designing silicone rubber products for medical devices, however, numerous factors must be carefully considered including material properties, manufacturing methods, and design requirements – this article aims to explore why and how designing silicone rubber products for these purposes is so crucial and provide guidance for doing it effectively.
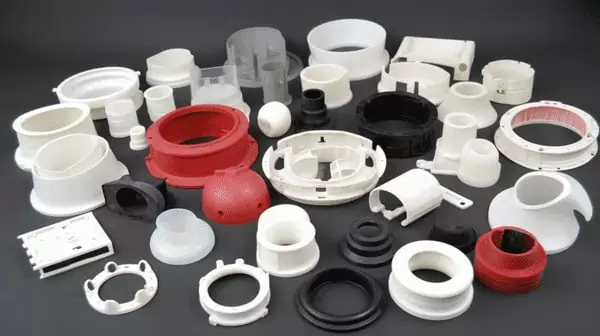
II. Manufacturing Methods for Silicone Rubber Products
A. Overview of Manufacturing Methods
There are various manufacturing methods for producing silicone rubber products, including injection molding, transfer molding, and liquid injection molding (LIM).
Injection Molding:
Injection molding involves injecting liquid silicone rubber prototypes into a mold cavity and allowing it to solidify over time, making this method perfect for high-volume production. Advantages include precise control, excellent repeatability, and fast cycle times; however, this technique may have its limitations in producing complex parts with thin wall sections or undercuts.
Transfer Molding:
Transfer molding involves using a plunger to move liquid silicone rubber from its container into the mold cavity. This method is often utilized for small to medium-sized production runs. Transfer molding offers many advantages in terms of control over molding processes as well as the ability to produce complex parts with greater ease; however, this may limit mass production due to longer cycle times.
Liquid Injection Molding (LIM):
Liquid Injection Molding is a subtype of injection molding using liquid silicone rubber material as opposed to the more common injection molding methods, including conventional plastic molding processes. LIM differs significantly from its counterpart by employing two-part liquid silicone, having lower processing temperature requirements, and offering shorter molding cycles – these features enable improved precision, reduced manufacturing costs, and shorter molding cycle times; LIM offers some other notable advantages like part size limitation or complexity limitations that may limit this method’s benefits as well.
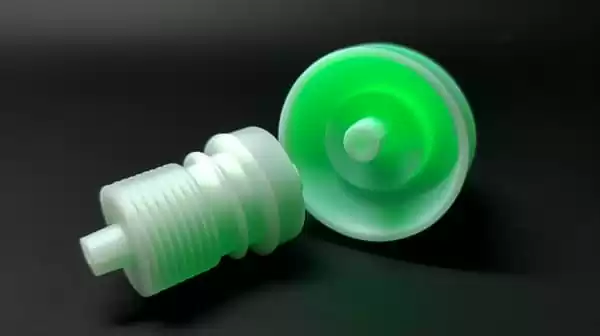
B. What Is the Difference Between Liquid Injection Molding and Conventional Injection Molding?
LIM differs from conventional injection molding by employing liquid silicone rubber as its key component. LIM injects this liquid material using a cold runner system for better control over its molding process whereas traditional injection molding uses a heated runner system to melt and inject solid silicone material into its molds.
LIM also stands out by operating at lower temperatures than traditional injection molding, reducing thermal degradation risk while simultaneously improving the material physical properties. Furthermore, its shorter molding cycle time enables faster production and increased efficiency.
In conclusion, the best manufacturing method will depend on several factors including part complexity, required quantity, and design specifications. By considering these aspects carefully, manufacturers can select the appropriate process for their silicone rubber product requirements.
III. Medical Grade Silicone Rubber Materials
Medical grade silicone rubber is a specialized variety used in medical device applications and designed to meet specific physical and chemical requirements for biocompatibility and safety in human use.
Medical grade silicone rubber must meet certain physical and chemical property criteria to be considered medical grade, such as biocompatibility, thermal stability, chemical resistance and mechanical strength. Medical-grade silicone must also go through stringent testing as well as follow strict manufacturing standards.
Medical grade silicone rubber can be produced through various processes, including liquid injection molding, compression molding and transfer molding. Manufacturing involves mixing high-purity silicone materials with additives like catalysts and pigments before curing the mixture to obtain a final product with desired physical and chemical properties.
Designing with medical grade silicone rubber requires following specific guidelines to ensure its product satisfies standards. These considerations include material selection, part design and manufacturing method – each factor can help ensure the final product meets physical and chemical properties required by medical device applications.
IV. Design Considerations for Silicone Rubber Products
When designing silicone rubber products for the medical industry, there are several important considerations to keep in mind. These include:
Wall thickness and rib thickness:
It is important to ensure that the wall thickness and rib thickness of the silicone rubber product are uniform and appropriate for the intended use. Thick walls can lead to longer cycle times and higher costs, while thin walls may not provide sufficient strength.
Parting lines and minimizing flash:
Parting lines and flash can occur during the molding process and may need to be minimized or eliminated to achieve a smooth, finished product.
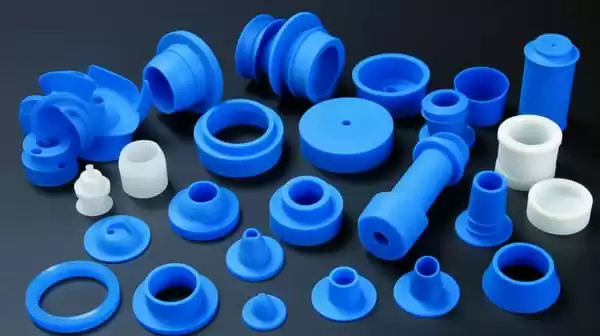
Undercuts and deep parts:
Parts with undercuts or deep features may require special tooling or additional processing steps to ensure proper molding and part injection.
Adjoining wall thickness and maximum surface area:
Adjoining wall thickness can affect the final product’s strength and durability, while maximum surface area can impact the mold’s ability to properly fill with silicone rubber.
Incorporating additional features:
Additional features such as inserts, threads, or gaskets may be required for specific medical device applications. These features must be carefully integrated into the product design to ensure proper function and performance.
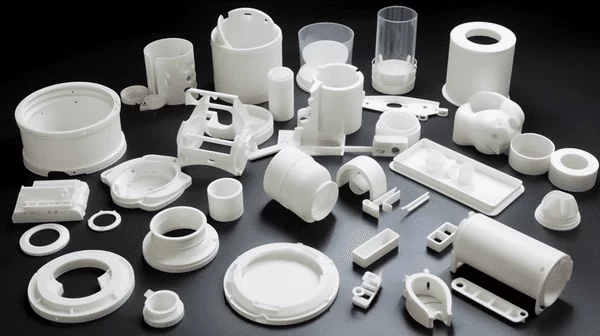
By considering these design factors, manufacturers can create silicone rubber products that meet the necessary requirements for medical device applications. Careful attention to these details can help ensure that the final product is safe, effective, and reliable.
V. Benefits of Silicone Rubber Products in Medical Applications
Silicone rubber products provide numerous advantages when applied to medical device applications, including:
Silicone rubber products provide wide temperature tolerance and resistance, making them suitable for medical devices used in extreme environments. Furthermore, they boast excellent temperature resistance that ensures they maintain their physical properties and functionality even under high-temperature circumstances.
Extreme Temperature and Chemical Resistant Products: Silicone rubber products offer exceptional temperature resistance, maintaining their physical properties in both high- and low-temperature environments. In addition, their chemical resistance makes them perfect for use in medical devices that come into contact with chemicals or harsh substances.
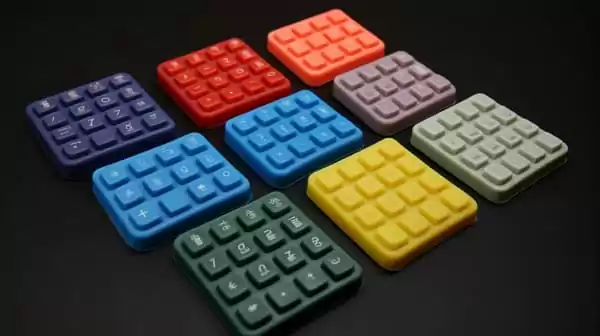
Electrical Resistance and Sterilization Compatibility: Silicone rubber products offer exceptional electrical insulation properties, making them suitable for medical devices that need electrical isolation. Furthermore, they’re compatible with various sterilization methods like steam autoclaving or e-beam irradiation for optimal use.
Silicone rubber products provide many properties that make them suitable for medical device applications, including low toxicity, biocompatibility and high tear strength – properties which make these materials highly desirable when coming in contact with human bodies.
VI.Common Medical Devices that Use Silicone Rubber
Silicone rubber is used in a wide range of many medical devices due to its unique properties and benefits. Some common medical devices that use silicone rubber include:
Surgical instruments and equipment:
Silicone rubber is used in surgical instruments and equipment due to its biocompatibility, flexibility, and resistance to extreme temperatures and chemicals. Examples of silicone rubber products used in surgical equipment include surgical tubing, catheters, and gaskets.
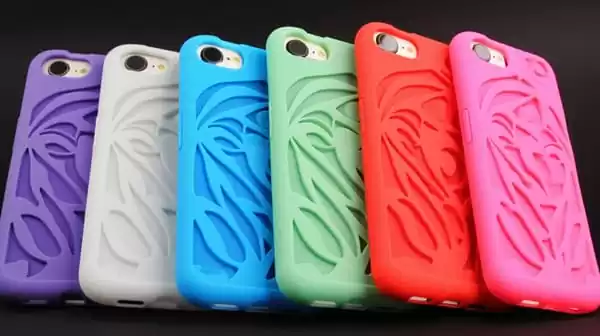
Implantable and non-implantable devices:
Silicone rubber is used in both implantable and non-implantable medical equipment due to its biocompatibility and ability to maintain physical properties over time. Examples of implantable devices that use silicone rubber include breast implants, pacemaker leads, and cochlear implants. Non-implantable devices that use silicone rubber include hearing aids, respiratory masks, and wound dressings.
Diagnostic equipment and labware:
Silicone rubber is also used in diagnostic equipment and labware due to its chemical resistance and ability to maintain its physical properties over time. Examples of silicone rubber products used in diagnostic equipment include tubing for blood analysis and syringe seals. In labware, silicone rubber is used in items such as pipette tips and vials.
In conclusion, silicone rubber is a versatile material that is widely used in the medical industry due to its unique properties and benefits. Its use in surgical equipment, implantable and non-implantable devices, and diagnostic equipment and labware highlights its versatility and importance in the medical field.
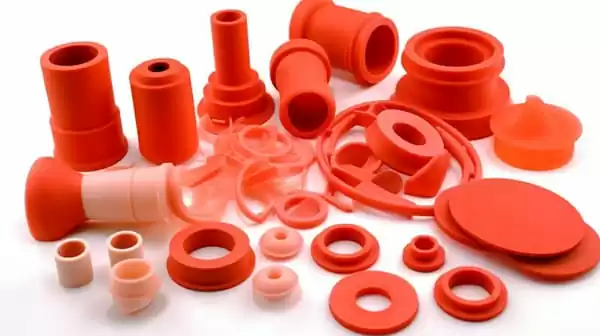
Conclusion
Silicone rubber products designed specifically for medical industry must meet stringent safety and efficacy criteria to guarantee patient health and well-being. Deliberating carefully over manufacturing methods, design aspects and material selection–such as medical-grade silicone rubber — all play key roles in producing top quality products.
Silicone rubber products provide medical applications with many advantages, including temperature resistance, chemical resistance, electrical conductivity resistance, biocompatibility and increased temperature tolerance. But there can also be challenges, such as manufacturing complexity and restrictions to part size and tool complexity when liquid injection molding.
Conclusion In summary, consideration must be given to manufacturing methods, design factors and material selection when producing silicone rubber products for medical applications. By taking such steps, manufacturers can produce high-quality medical devices that satisfy required safety and performance criteria and improve patient care and outcomes.